Five-step OEE implementation strategy
Properly navigating the implementation of Overall Equipment Effectiveness (OEE) solutions and practices is crucial for boosting productivity and sustainability.
This lesson gives youa practical strategy to help you implement OEE solutions for sustained manufacturing excellence and profitability.
The framework used in this lesson is called the Highway Solution, a methodical, five-step OEE implementation strategy that streamlines the deployment of production monitoring systems like Factbird. It’s spearheaded by Mikkel Rauff Simonsen, Senior Manager of Plant Optimization at Danish Crown, who has first-hand experience in rolling out Factbird across over 50 sites.
Let’s dive in!
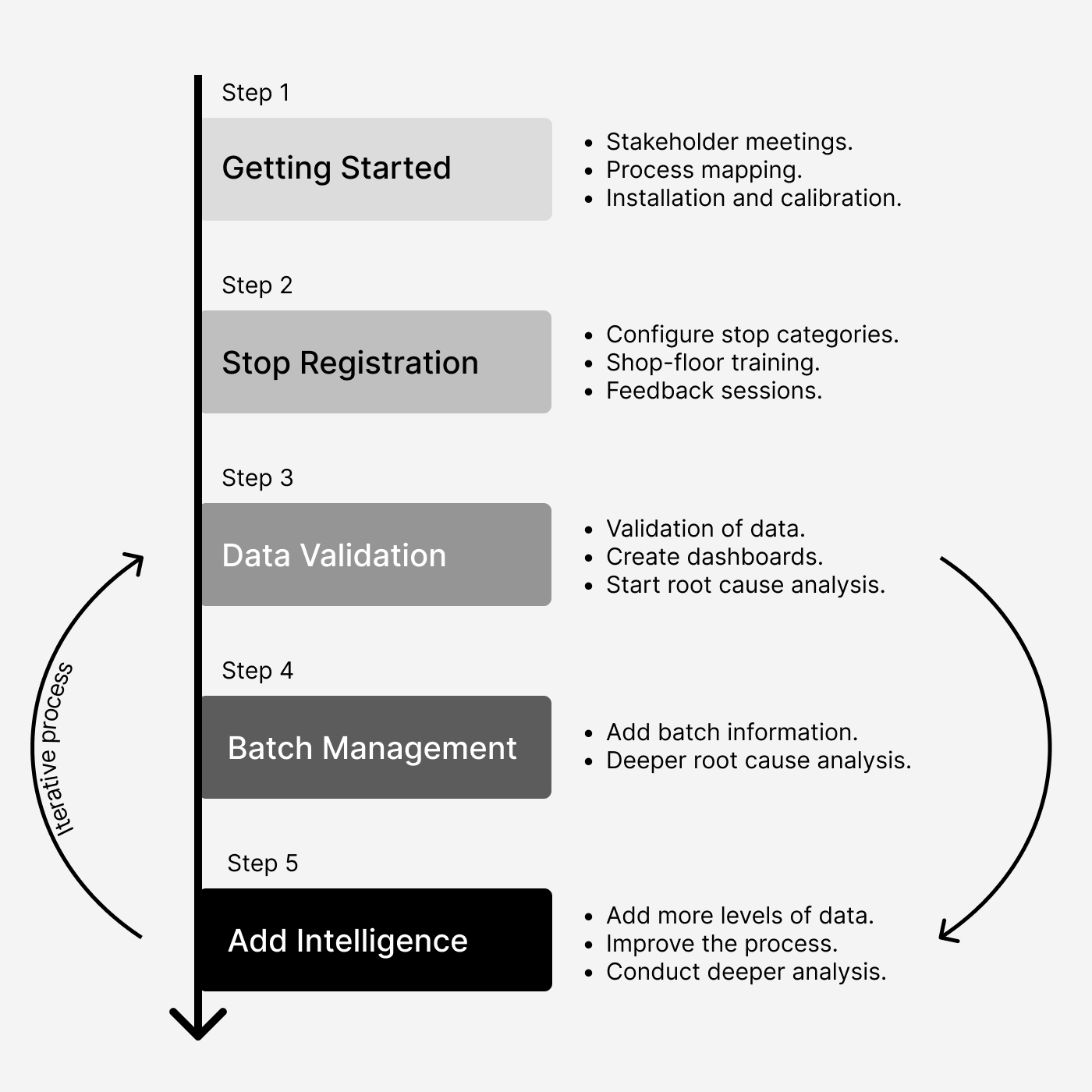
Step 1: Getting started
The initial phase involves setting the foundation for successful OEE implementation.
Here, you focus on the fundamentals, start seeing data, and start using the system.
This includes configuring and calibrating sensors and establishing baseline data capture protocols on production lines.
First meetings with the OEE solution vendor
You’ll want to begin with getting a good introduction to your new OEE solution and holding meetings with stakeholders to get buy-in.
This meeting is not a one-time event; be aware of information overload and the need to recap and allow time for questions.
Management:
- The focus with management is to create a structured plan.
- Introduce the solution, discuss needs and possibilities, and discuss sensor placement.
- This is critical because it ensures a strong start for the new solution and future establishment.
Technicians:
- The focus here is ensuring successful data collection.
- Technicians’ expertise is critical because they have the know-how to install hardware and ensure reliable signals.
Operators:
- The focus here is to use their experience to map stop causes.
- It’s critical to involve operators and utilize their daily experience with your equipment, while also empowering them with ownership for the future success of your improvement efforts.
Other key activities with your solution vendor
Other than the vital task of getting stakeholder buy-in, you'll want to lean on customer success experts from your solution vendor to help with setup. This will include tasks like:
- Deciding on sensor placement. Here is where you decide what you want to measure.
- Creating stop categories and stop types. We recommend getting input from your OEE solution vendor on the typical categorization of stops for your industry.
Configuration activities
Other important steps in the getting started phase involve the setup of your new solution and checking that data is being collected.
- Name lines based on a standardized naming scheme, e.g. organisation_country_site_department_line.
- Retrofit plug-and-play IIoT devices and sensors and/or integrate with existing production data (Scada, Kepware, etc.) where possible.
- Check your getting signals to your OEE cloud software.
- Set stop duration targets, add shift schedules, and set sensor standards.
Here’s an example of standard operating procedures regarding sensors at Danish Crown:
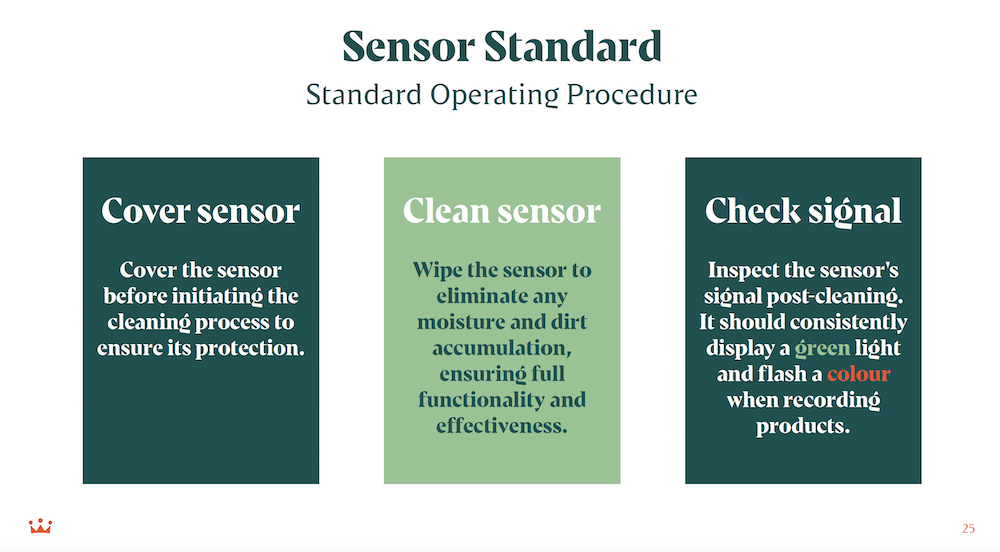
Formulating and practicing simple tasks like these will help improve the reliability of your solution in the long run.
Step 2: Stop registration
A vital aspect of implementing OEE is defining and registering stop categories and stop causes.
These categories represent the events that lead to downtime in your manufacturing process, while the causes pinpoint the specific reasons behind these events.
Here's how we typically define stop categories at Factbird:
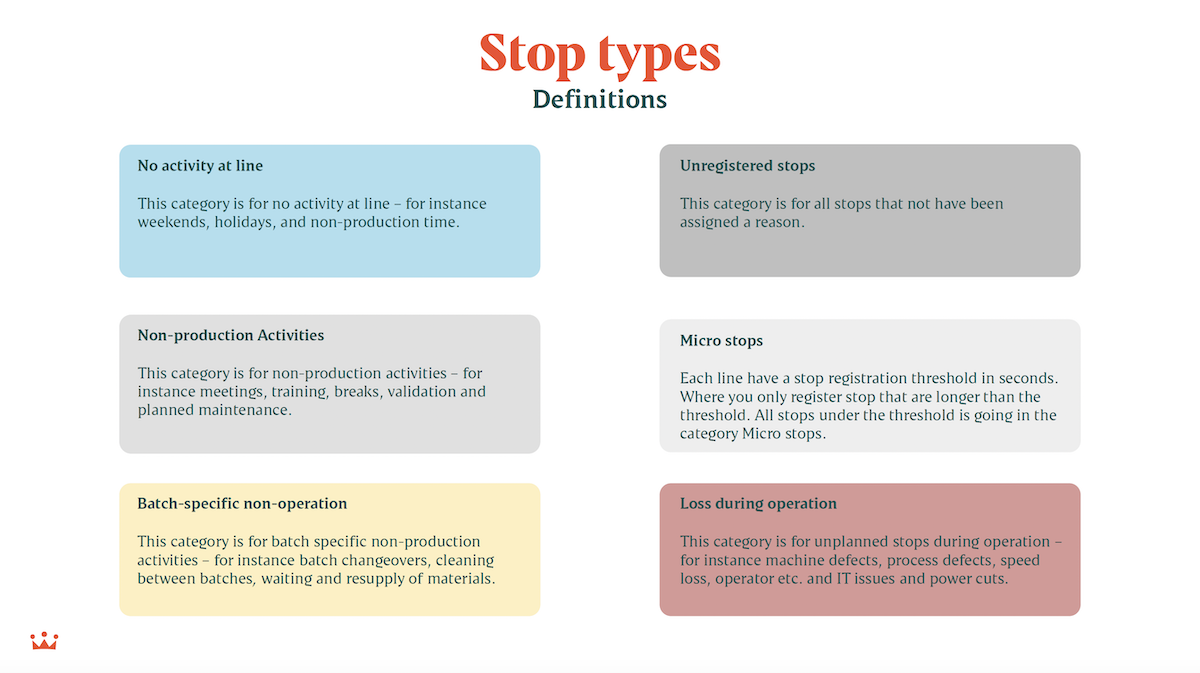
By carefully defining, categorizing, and standardizing stops across sites, you can gain actionable insights to drive OEE improvements effectively.
Here’s an example of a good process for kicking off stop registration in production:
- Training of super users who act as contact persons for fixing local issues in your OEE tracking solutions and out in production.
- Configuring input devices such as tablets with stop categories and causes.
- Going live to ensure a quick ROI on your OEE tracking investment.
- On-the-floor training and starting the registration of stops.
- Training and feedback sessions with operators to improve the accuracy of data entry.
- Training and feedback sessions with managers to make sure data is utilized correctly.
- Perform ongoing follow-ups to deepen usage of your OEE tracking solution.
At Factbird, we suggest starting with a maximum of 20 main stop causes. By starting with basic categories like "material jam," you keep operators engaged, don’t disturb their work, build good habits, and record useful information.
You can download our stop causes template here to get started: Download the OEE Stop Causes Excel Template (direct download).
As your organization gains experience and accumulates data, you can refine your stop causes by breaking down the initial high-level categories into more specific causes. For instance, you can further delve into "material jam" subcategories such as "label jammed on roll," "cardboard jammed in folder," or "product stuck in extruder."
This level of granularity allows for a more precise understanding of the root causes behind stoppages.
Step 3: Data validation and visualization
Ensuring the integrity of the data that you gather is crucial. The activities in this stage focus on validating and then making sense of the data.
Validate data quality
It’s important to regularly check data to ensure accuracy. This can be done at a frequency of every 2nd and 4th hour, for example. You’ll want to check things like all stops are registered, the stop causes are correct.
It’s critical that operators continue to register stops correctly, as you need valid data to be able to make improvements.
Continue setup with vendor
Once you’ve collected data for around a month, it’s a good time to analyze unregistered stops, OEE scores, and the top five downtime categories with your solution vendor.
Then decide on what needs to be improved going forward and figure out what data could further help your teams.
Build dashboards
Now it’s time to build and introduce dashboards that display relevant data for your teams.
Be selective in the data you show to executives, managers, technicians, and operators so you don’t overwhelm them. It’s best to start with simple visualizations and improve them as your teams become more mature.
Once built, monitor usage of your dashboards as users begin to conduct root cause analysis and check that they understand them and are utilizing them correctly.
Step 4: Batch management
Not every product is the same, and manufacturers nowadays work with hundreds or thousands of SKUs per plant.
Managing and analyzing production batches at the SKU or item number level allows for more detailed OEE analysis. You will get a proper view of your OEE when you are able to distinguish between products that vary in speeds, say 200 pcs/m vs. 300 pcs/m.
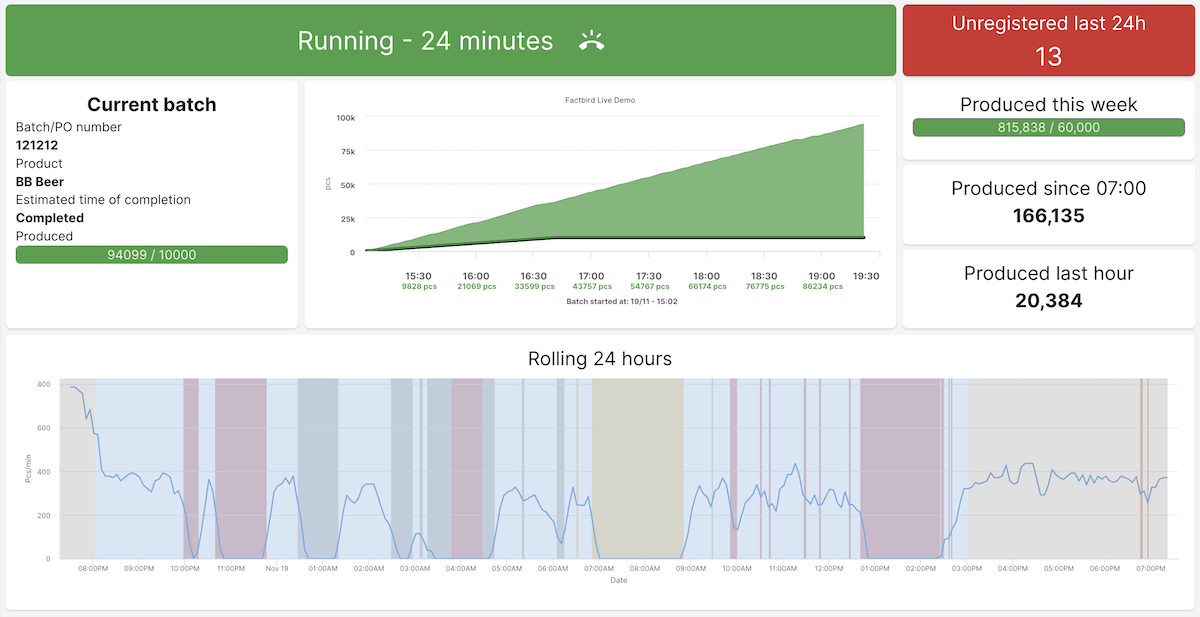
To get batch management working right in your OEE tracking system, you’ll first want to make sure you have a structured plan for batches in your ERP system.
Then, where possible, it’s best to integrate your ERP system with your OEE software rather than relying on manual input of batch information. Automated data flow helps improve reliability and visibility while also saving time.
Once integrated, it’s a good idea to conduct a time study by measuring how long it takes to produce a certain number of units within a batch. A time study can help verify that your OEE system is correctly tracking production rates and performance.
In Factbird, it is possible to automatically detect batches based on their speed. This only requires a signal that sends the item number of the product, 100 for 100 pcs/m, for example, and a signal that changes whenever the first signal changes to signify a new batch.
Now you can track performance variations across batches and identify more optimization opportunities.
Step 5: Adding intelligence
When rolling out solutions, it's generally best to start simple and gradually add complexity. This is the stage where you can introduce that complexity after mastering the fundamentals.
Key here is to keep looking for needs that aren’t being fulfilled and new opportunities. Then decide on what is feasible, implementing and monitoring the solutions, and facilitating the sharing of knowledge across the organization.
Adding intelligence to your OEE system and processes could involve the following solutions:
- Introducing predictive maintenance to reduce equipment downtime.
- Introduce video monitoring of lines to find the root cause of equipment malfunctions quicker.
- Incorporating an AI co-pilot into your OEE software to streamline analysis.
In essence, this final step is about continuously refining and improving processes related to the use of OEE solutions, ensuring that progress never stagnates.
And that’s it!
I hope you got some useful ideas and strategies out of this thorough lesson on implementing OEE analysis into your organization. Join me in the next module where we dive into some examples of OEE in practice.