Manual to Automated: SIP Manufacturing's Production Monitoring Leap with Factbird
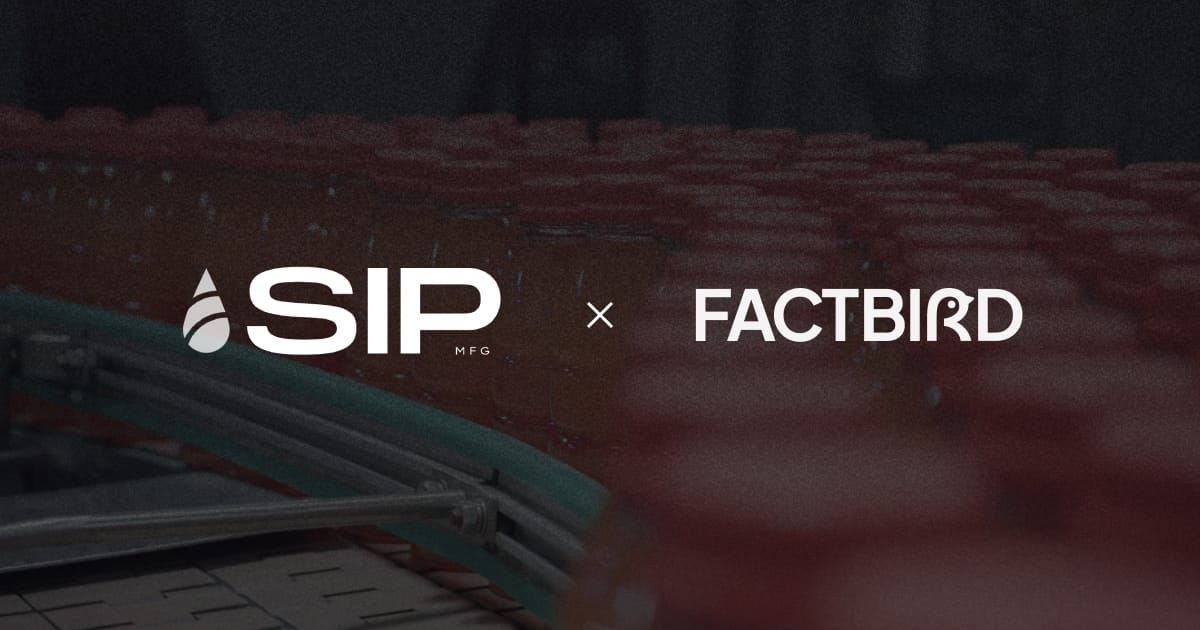
Meet SIP
SIP Manufacturing are experts in beverage formulation, packaging, and fulfillment and have cemented their place as leaders in their industry from their base in Lake Elsinore, California.
We wanted to learn how they adeptly manage the production of a wide range of beverages. So we spoke with Johnnie Green, Vice President of Operations at SIP Manufacturing, about how Factbird's Manufacturing Intelligence solutions have been integrated into their operations.
The challenge
The challenges that SIP Manufacturing faced that sparked the hunt for a manufacturing intelligence solution will be quite familiar to people in the manufacturing industry.
Manual production monitoring
In Johnnie’s words, “We've got some pretty big customers, but everything was manual. So operators were capturing data on the lines, such as downtime, start times, and how many bottles, cans, or units were produced.
“No automation was really in place at all. Everything was transcribed from paper and tabulated.”
Johnnie Green, VP of Operations at SIP Manufacturing
“We were using a lot of Excel spreadsheets for the metrics. That was a lot of time, a lot of energy, and a lot of redundancies. We actually had a full-time person handling all of that.”
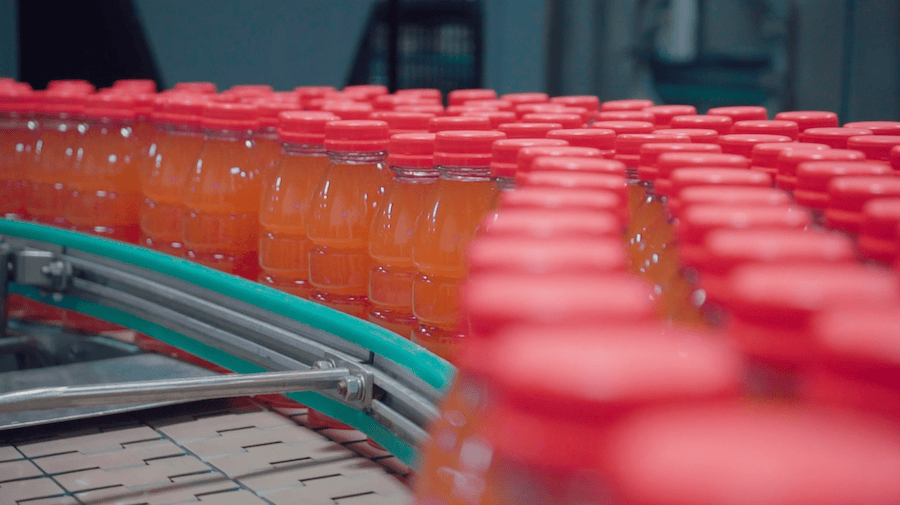
Increase throughput
A major KPI for SIP Manufacturing is throughput, or first-time quality, but they were seeing a big dip in units between the fillers and the end of the line.
In Johnnie’s words, “There was a big delta in the product that was run through the filler versus the product that was actually shipped and sold. So obviously, we want to be able to maximize throughput and actually be able to sell, you know, the most number of units that we can actually produce.”
The solution
After some searching, SIP started using Factbird in 2022 and has been full steam ahead with improving efficiency since. Here’s how.
Automatic, real-time production monitoring
SIP Manufacturing is using Factbird sensors and IoT gateways to capture bottles per minute, cans per minute, and units per minute coming out of their fillers.
“We're able to measure bottles per minute, output, throughput, and stops in real time.”
Johnnie Green, VP of Operations at SIP Manufacturing
Since installing Factbird on their lines, SIP has been able to eliminate many of their existing manual processes and more accurately identify bottlenecks with real-time production data.
Turn downtime into uptime
Like most manufacturers, the SIP team wanted to understand what was causing downtime—how many stops there were, how frequently they occurred—and convert that downtime into uptime.
Factbird is helping them do this through the registration of downtime and production analysis tools, such as live production KPIs for transparency, Pareto charts that offer an immediate overview of production efficiency, and Overall Equipment Effectiveness (OEE) calculations.
“Factbird has been a really good tool for showing us where those trends are happening, the frequency of our downtime, and our stops.”
Johnnie Green, VP of Operations at SIP Manufacturing
On the flip side, it is also helpful for SIP to identify when production is running well. According to Johnnie Green, Factbird is “also showing us the good trends. Like when we're running long, we're running well, and when we're not stopping, we're able to replicate that.”
Easy to install and use
Factbird's emphasis on creating plug-and-play data collection solutions along with user-friendly cloud-based software was ultimately a major factor in the SIP team's selection of the company.
Johnnie Green said, “Factbird was pretty user-friendly; I've seen other modules that have a high level of complexity. The users aren't able to understand enough. The data becomes a little intimidating.”
Real-time data was another key demand for Johnnie Green, who says, “As an operations lead, I'm very interested in that information in real time. So that was one of the things that was really beneficial to that and to use in Factbird. And it's just really easy to use and navigate through.
The results
SIP Manufacturing has found Factbird extremely useful in helping them meet their production KPIs.
10% reduction in waste
The automatic collection of production data helped SIP Manufacturing reduce waste and increase revenue.
“Factbird was really beneficial in identifying the delta between product that ran through the filler and product that was actually packaged and shipped," said Johhnie Green.
“That translated into almost a 10% reduction in waste. And obviously, based on the cost of our products, the bottom line was impacted in a positive way from a revenue standpoint.”
Reduced turnover rate
An interesting result that would not typically be top of mind when implementing manufacturing intelligence solutions was a decrease in SIP’s staff turnover rate.
According to Johnnie Green, “I wasn't really looking for turnover rate to coincide with some of these metrics. But as we were able to use Factbird as a tool to train employees and help them monitor their own metrics, we saw a reduction in our turnover rate.
“This was directly correlated to the incentive program that we implemented. So we wanted to incentivize our employees by, you know, meeting their daily metrics, their shift target metrics, and their weekly metrics.
“They were much more able to control what they were doing on a day-to-day basis. And we saw that the employee turnover was a lot less.”
Johnnie Green, VP of Operations at SIP Manufacturing
Improved knowledge sharing
According to Johnnie Green, Factbird is “helping teammates train other teammates, although there is a little bit of a competitive spirit that comes when you're measuring.
“We like to share the best practices—how some of our best performers really know how to leverage the information that's presented in Factbird. So we really look for the teammates to share what they're actually utilizing it for, as well as for upper management, so we can find better ways to leverage the system every day.”
Consistency of productivity
According to Johnnie Green, a significant benefit of SIP has been increased productivity consistency.
He said, “It's given the plant a much more serious approach towards manufacturing; when you can actually see what you're producing from a day-to-day standpoint, even from minute-to-minute or from an hour-to-hour standpoint, it keeps the team engaged throughout the day.”
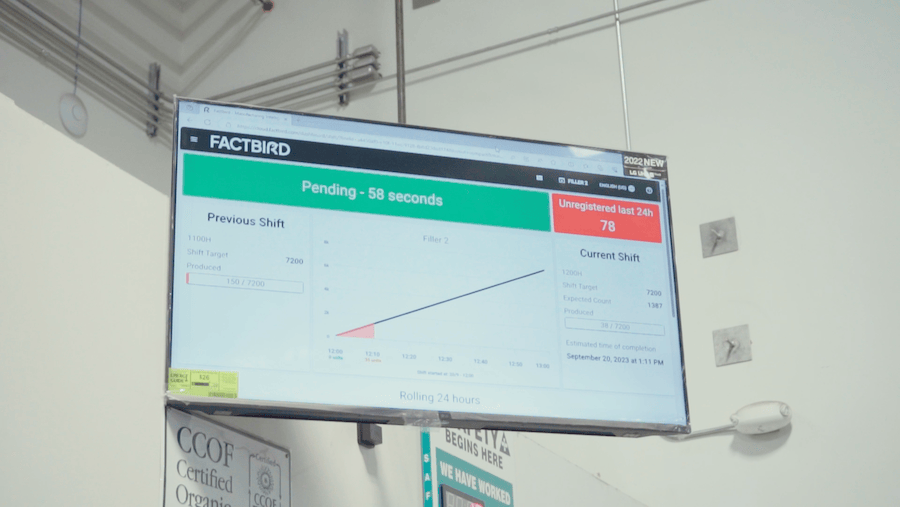
Excellent support
Factbird's responsiveness impressed Johnnie Green. “Factbird has been very responsive, almost to the point where you might even question how you guys are able to be that responsive. Our points of contact are very capable of answering questions, from the equipment to questions about the application. And their response time has never been more than a few minutes in most cases.
“Factbird has been very responsive, almost to the point where you might even question how you guys are able to be that responsive.”
Johnnie Green, VP of Operations at SIP Manufacturing
“Sometimes we request a different way to look at some of the analytics, and within the conversation with the technicians or support, they're able to resolve that in real time. So they’ve been very responsive, probably second to none from what I've seen in the industry.”
Continuous improvement
SIP was quickly able to identify how they could best use Factbird to get the continual improvement they were looking for.
Johnnie Green said, “The system has the ability to customize the shifts based off of days and times. And we were finding that we were a little bit more successful in making improvements from shift to shift if we measured the shifts in smaller increments.
“So we actually broke down each shift into hours to be able to measure productivity from one hour to the next. We were also able to measure stops from one hour to the next. So just dividing that shift from an eight-hour or 12-hour shift into one-hour time slots, we were able to say, if we can meet our goals for one hour and do that consistently, then the shift will take care of itself.”
Data for business cases
SIP Manufacturing has been using data from Factbird to support new business cases as well.
According to Johnnie Green, “One of the things that we have to be able to do is to present business cases. And in the manufacturing world, that's all based off of product throughput, stops, downtime, and uptime. Factbird was the data that we were actually able to use to justify a lot of things.
“Factbird has been really good at showing us where some of our gaps and opportunities are throughout the lines, and we're able to make investment solutions and put together teams and Kaizen events to say, Hey, this has been identified here; let's look at these trends and decide if we need another piece of equipment or if we need another system in place.”
Two weeks to implement
As mentioned at the beginning of this case study, SIP Manufacturing had the common struggle of manual data collection without the possibility of truly accurate and real-time analysis. Factbird helped them automate their production monitoring processes within two weeks.
“We went from having zero data to having a fairly substantial amount of data in about two weeks.”
Johnnie Green, VP of Operations at SIP Manufacturing
Johnnie Green stated, “Depending on how you look at the data, you want to have it consistent for that same time period. So once we found the groove of what we wanted to look at, to the point of looking at things hourly versus looking at things over the course of a day, we went from having zero data to having a fairly substantial amount of data in about two weeks.”
Comparing shifts
Finally, Johnnie Green touched on how they can now analyze productivity between shifts and make adjustments based on the data. He said, “You can see different groups at different times. And you can also see the same group at different times. So a shift that normally performs really well on the weekends might perhaps underperform on their weekday weeks.
“Our management operations teams can look back and say, Hey, this is how you guys can stay consistent within the shift without necessarily changing the days of the week.”
Conclusion
For SIP Manufacturing, “Factbird has been positioned as our complete metrics, lean manufacturing, and overall improvement platform. So it's been really good.”
If you would like to learn more about how Factbird can help your business, get in touch with one of our experts or check out a demo video of the Factbird Cloud Application.