How Danfoss achieved a 33% reduction in equipment energy consumption
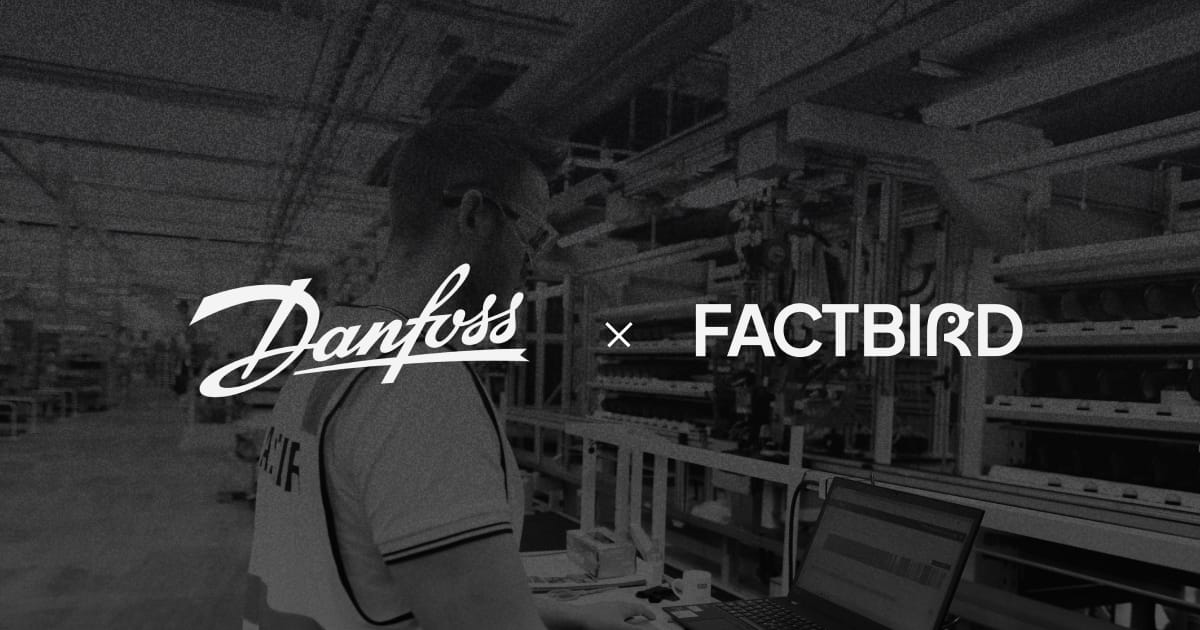
About Danfoss
Danfoss is a Danish multinational manufacturer of hydraulic, temperature control, and power solutions. They recently combined their heating and cooling segments into a single, climate-focused business entity that has accelerated their scope for developing integrated, energy-efficient solutions to power the smart cities of tomorrow.
With more than 40,000 employees and 95 factories worldwide, Danfoss has pledged sustainability as the centerpiece of its production optimization strategy ahead of 2025.
Watch the interview with Martin Ole Madsen, Manager – Operations Excellence SVS EUR at Danfoss, to get the full story on how Danfoss uses Factbird to monitor energy consumption at machine level, helping them meet their ESG and cost reduction targets.
Previous operational challenges
As part of their goal of becoming carbon-neutral by 2030, Danfoss began monitoring the energy consumption of all their production facilities and retail locations.
Considering just how much their energy costs have increased, Danfoss opted for a detailed approach, going as far as comparing energy consumption reports for each production line against their traditional meters and metrics. They began to track the consumption of electricity and analyze the data in detail to help them understand where they could improve efficiency.
Evaluating energy consumption
But from the project’s onset, one challenge looked more difficult than the rest: managing their standby energy consumption. This seems to be a common issue in a lot of production plants because of the amount of equipment with specific power cycling needs. For instance, equipment that requires power to keep hydraulic fluid warm during operation whether or not you’re actually producing.
Implementation phase
Applying a new data measuring strategy
Roll out of Factbird’s energy meters began with a pilot on three different machines in one of their newly built production facilities. Implementation was quick and easy, with Danfoss adding a Factbird Duo device to each line, and letting them monitor energy consumption in real-time. Our devices come with cellular and Wi-Fi connectivity standards and send data directly to the cloud where it’s aggregated, analyzed, and visualized by the Factbird application.
Consumption vs. output
To support their energy-saving initiative, Danfoss, in partnership with Factbird, developed a Digital performance dashboard that displays both their machinery’s energy consumption and manufacturing output, as well as a live camera feed timestamped to production flow.
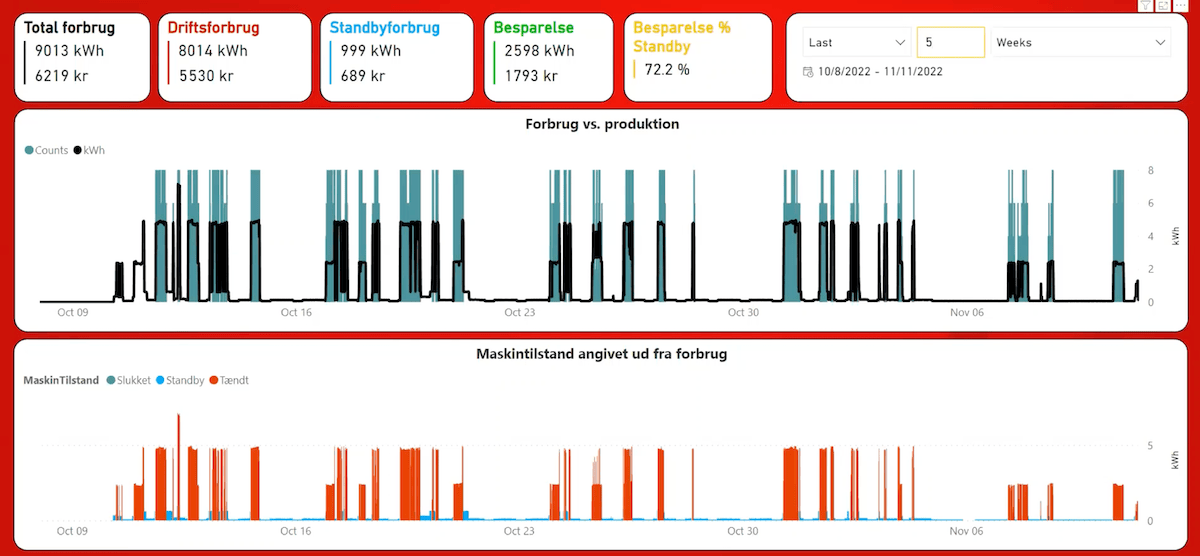
Danfoss has an energy-saving KPI so managers can quickly track every resource used in production departments to help them evaluate how to reduce the consumption of electricity. All this data is gathered and presented in an easy-to-understand way, helping them narrow down improvement opportunities and focus areas more quickly.
The impact of data-based decisions in everyday production
Comparing energy consumption and output side-by-side was eye-opening for their operations managers. Factbird’s data insights helped shed light on just how much power Danfoss’ equipment had been using when left on standby. And the numbers were shocking! The power that a machine consumed on average during standby was the equivalent of the average energy usage of 20 resident users or 9 households in Denmark.
Comparing energy consumption and output side-by-side was eye-opening for their operations managers.
During the weekend, every machine was left on standby mode to help reduce how long it took to start up before production. The Factbird solution tracks and accounts for every second of the day and night, automating your KPI tracking process.
When managers arrived that first Monday morning to review their findings, reports showed that standby mode had been costing the company considerably more than they had originally expected. They have decided to look into options to shut off equipment and ways to lower the standby power consumption.
Reliable data shapes mindset
Updated reports indicated the experiment could save Danfoss up to 77% of their standby power consumption on the machinery used in the pilot project. They advised managers in every production department to do the same, moving the company closer to meeting its sustainability goals and lowering its operational energy costs significantly.