Data without borders: Danish Crown's global rollout of manufacturing intelligence
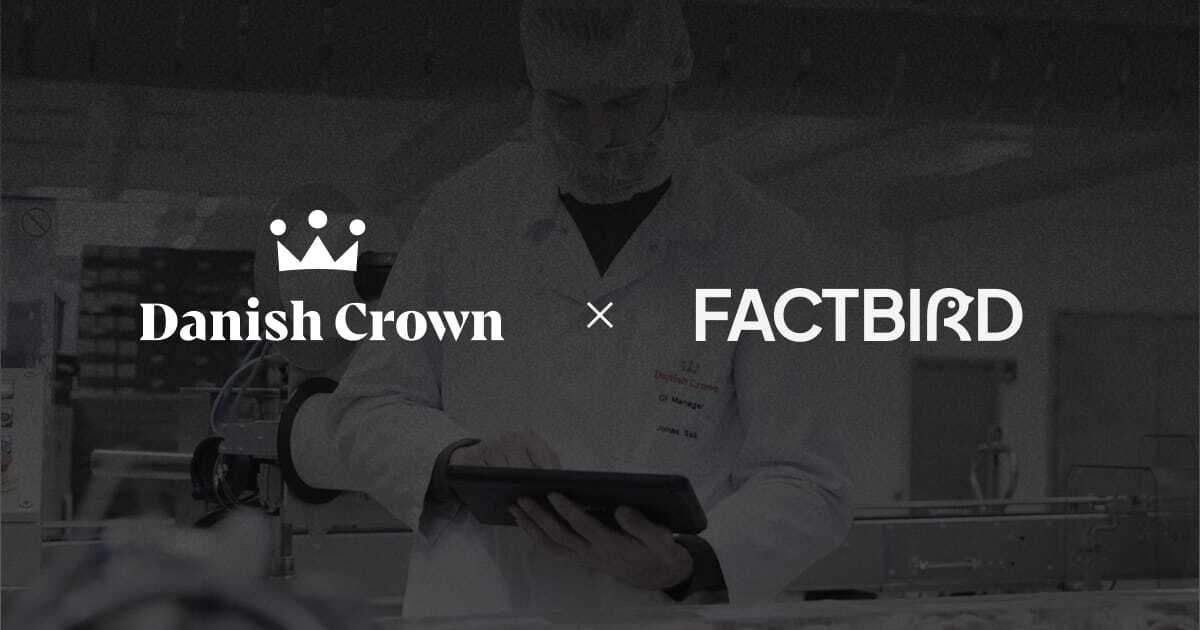
Meet Danish Crown
Danish Crown is the largest meat-processing company in Europe and one of the world's leading exporters of pork and beef, with facilities in multiple countries including Denmark, Germany, the UK, and China, among others. They are owned by over 5,000 Danish farmers and provide services to over 49 million consumers worldwide.
To find out more about their success using Factbird for continuous improvement, we visited Danish Crown sites in Denmark, Netherlands and Germany and talked to operators, managers, technicians, and engineers. The following case study draws on their diverse perspectives and will give you some valuable pointers on rolling our data-based continuous improvement across international production sites.
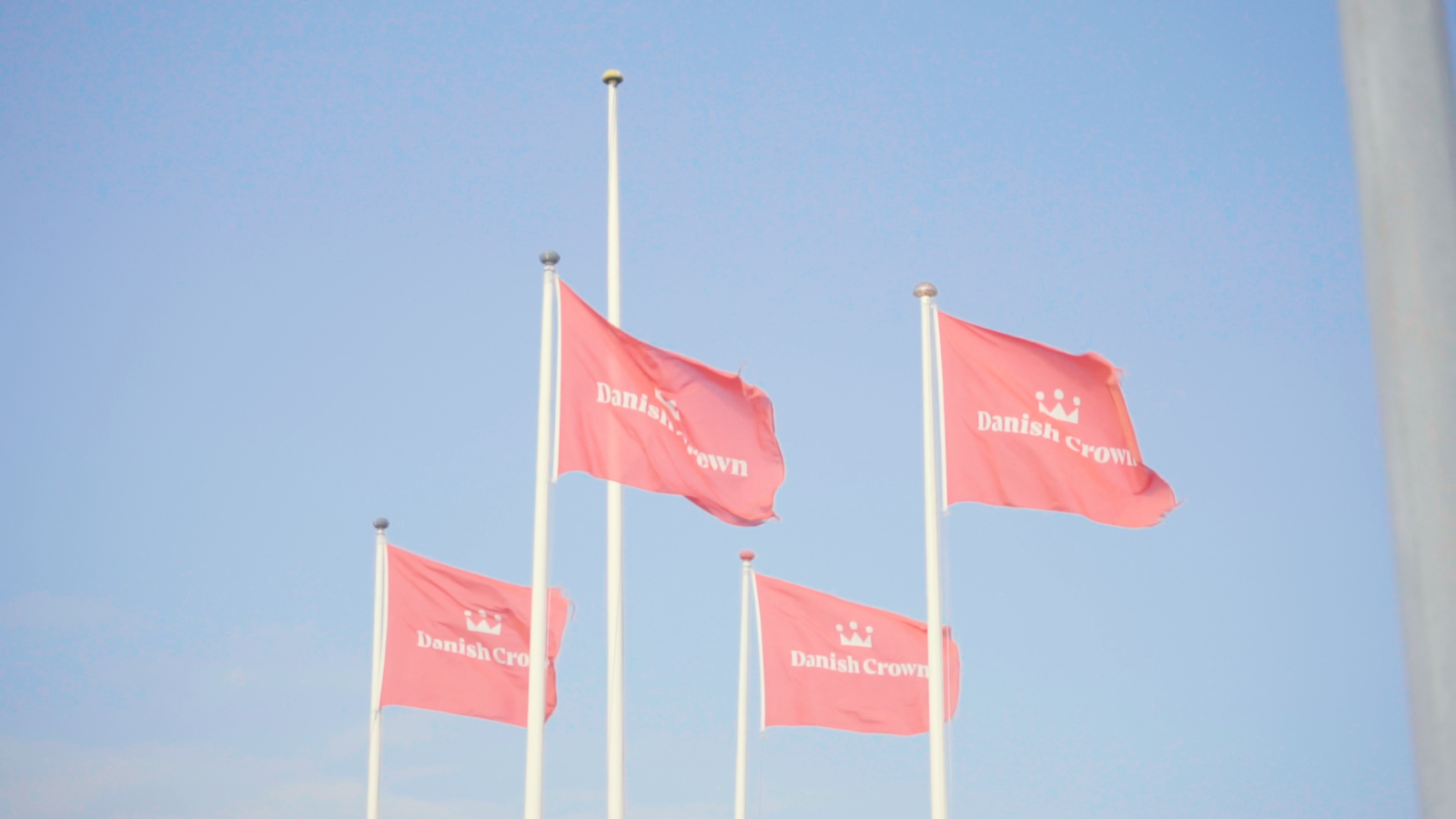
The challenge
As a multinational company producing a broad range of products in the challenging food and beverage industry, Danish Crown has a strong drive to improve the efficiency of their operations to reduce costs, increase output, and improve sustainability.
Here is a breakdown of the specific challenges they were facing that led to their decision to use Factbird’s manufacturing intelligence solutions.
Unreliable data and analysis
Before Factbird, Danish Crown's operations faced a major lack of data and a limited understanding of Overall Equipment Effectiveness (OEE). As Mikkel Simonsen, Senior Manager in Continuous Improvement at Danish Crown, puts it, "Missing data, I would say is the main problem."
“Our company has limited stop data and limited knowledge into the OEE concept.”
- Mikkel Simonsen, the Senior Manager in Continuous Improvement at Danish Crown
The lack of detailed data and limited knowledge of OEE made it hard to compare performance and make informed decisions. Consequently, Danish Crown missed opportunities for optimizing production processes, reducing downtime, and enhancing overall productivity. This gap in data-driven insights not only affected day-to-day operational decisions, but also impeded long-term strategic planning and growth initiatives.
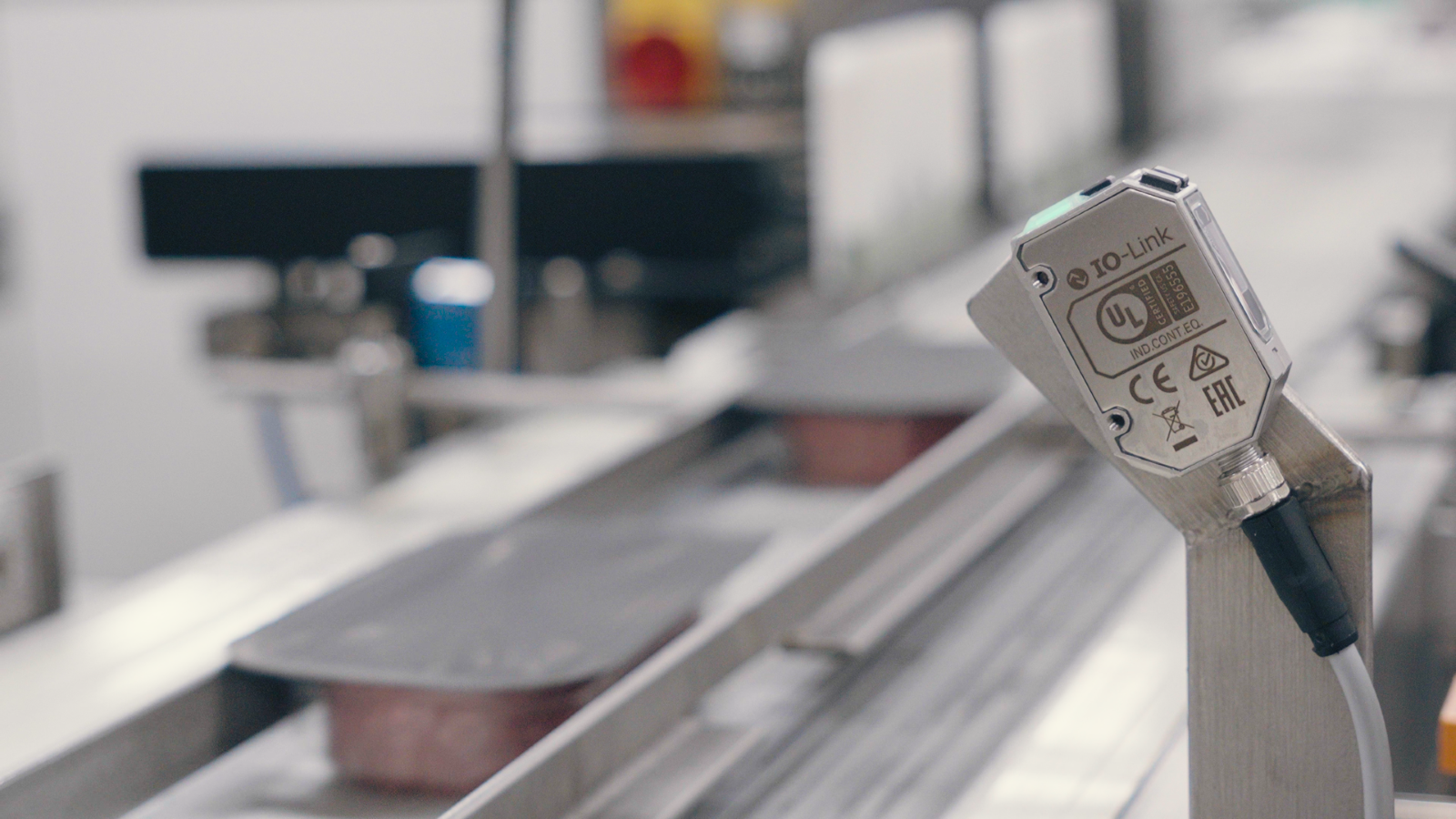
The complexity of scale and scope
Danish Crown's expansive operations, spanning over 80 sites across different geographical regions, added layers of complexity to the challenge. Each site, with its unique set of machinery and operational nuances, required an approach to data collection that aids the continuous improvement of all sites. The absence of a unified system meant that performance data, when available, was siloed, making it nearly impossible to conduct cross-site comparisons or benchmarking. "Many of our machines don't have a network connection. Therefore, we have not connected to SCADA," Mikkel points out, highlighting the logistical challenge that further complicated data collection efforts.
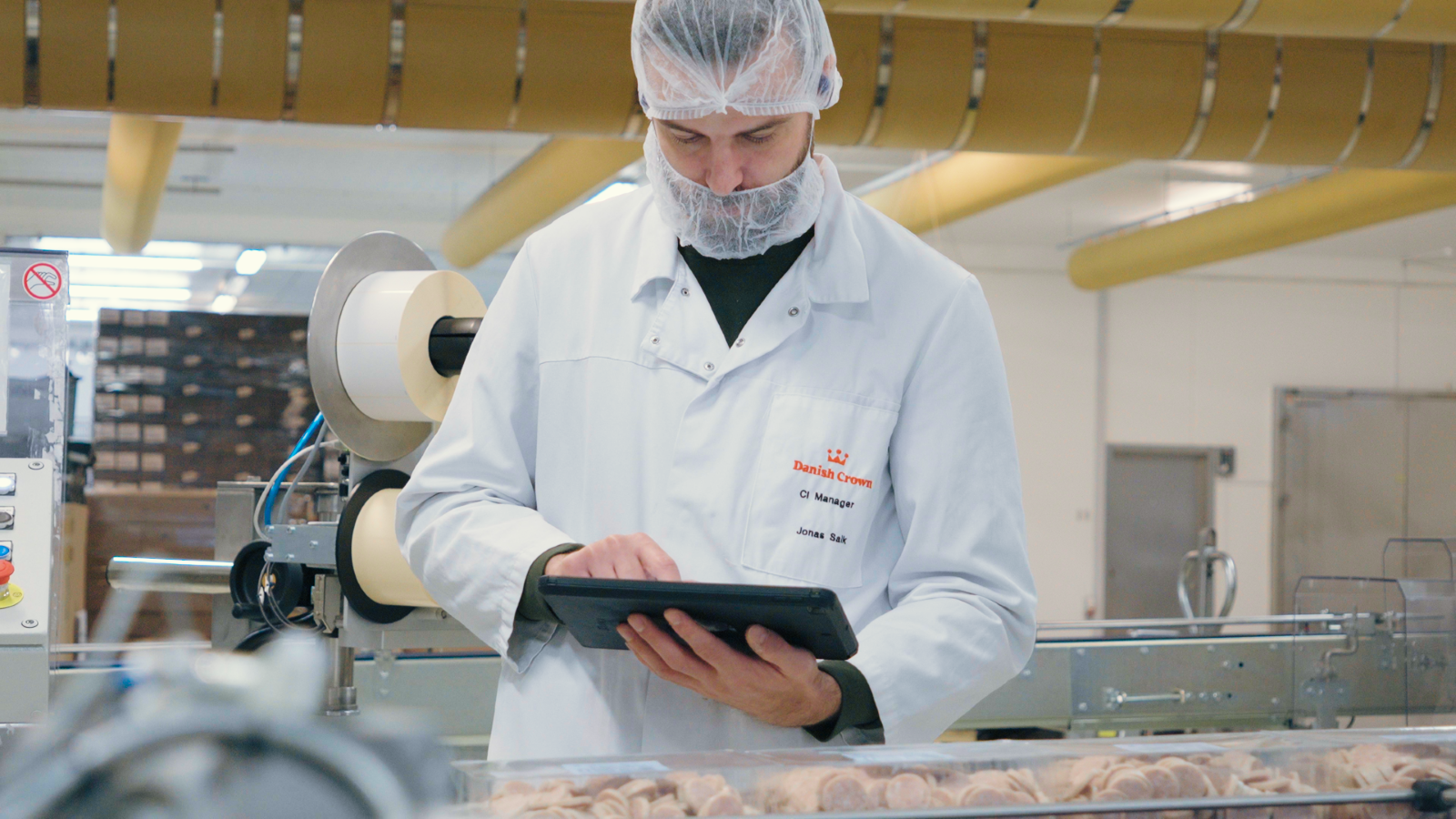
The newness of OEE
The concept of OEE as a measure of production efficiency was relatively new to Danish Crown. This metric, which offers a comprehensive glimpse into how effectively a manufacturing operation utilizes its resources, was underutilized due to a lack of understanding and standardized implementation across the company's various sites. "Our company has, what we call, as mentioned before, limited stop data, and limited knowledge into the OEE concept," Mikkel acknowledges, shedding light on the initial knowledge gaps that slowed down the use of this important performance measure.
Lack of standardization
Danish Crown’s varied activities meant that they didn't have a uniform way to measure and talk about performance, making it hard to share insights and best practices between sites. The need for a unified approach was clear, as Mikkel elaborates on the selection process for Factbird, "OEE can be measured in many ways... But the most important one is that we measure the same way, we use the same calculation. That's the main reason we have one common system."
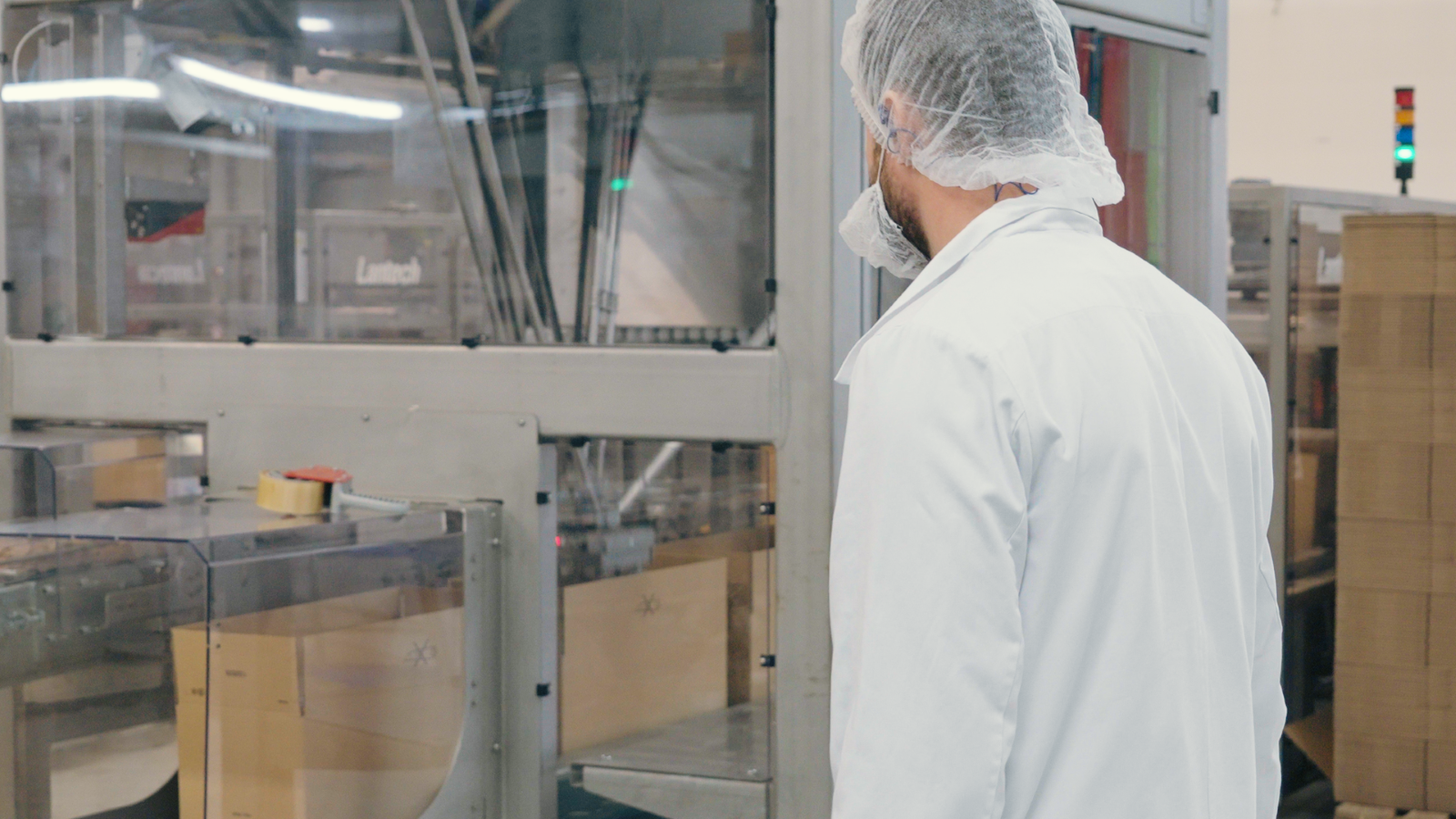
The solution
Danish Crown decided to use Factbird because of its simplicity, user-friendly interface, and prior positive experiences within the IT department. Bo Jensen, Continuous Improvement Manager in Vejle, remarked, "Factbird stood out for its easy-to-use interface, making it an obvious choice for us."
Factbird's ability to offer a unified language and standardized approach to measuring OEE across various sites was particularly appealing. "We have a common language in Danish Crown because of one solution at all sites," Mikkel notes, showing how the system helped create a united way of working.
The Highway Solution
Danish Crown adopted a structured five-step implementation strategy for Factbird they dubbed the Highway Solution, emphasizing the importance of signal capture, stop registration, data validation, registration optimization, and adding intelligence.
Thinking globally while still acting locally, each site implemented the Highway Systems to align with overall business goals.
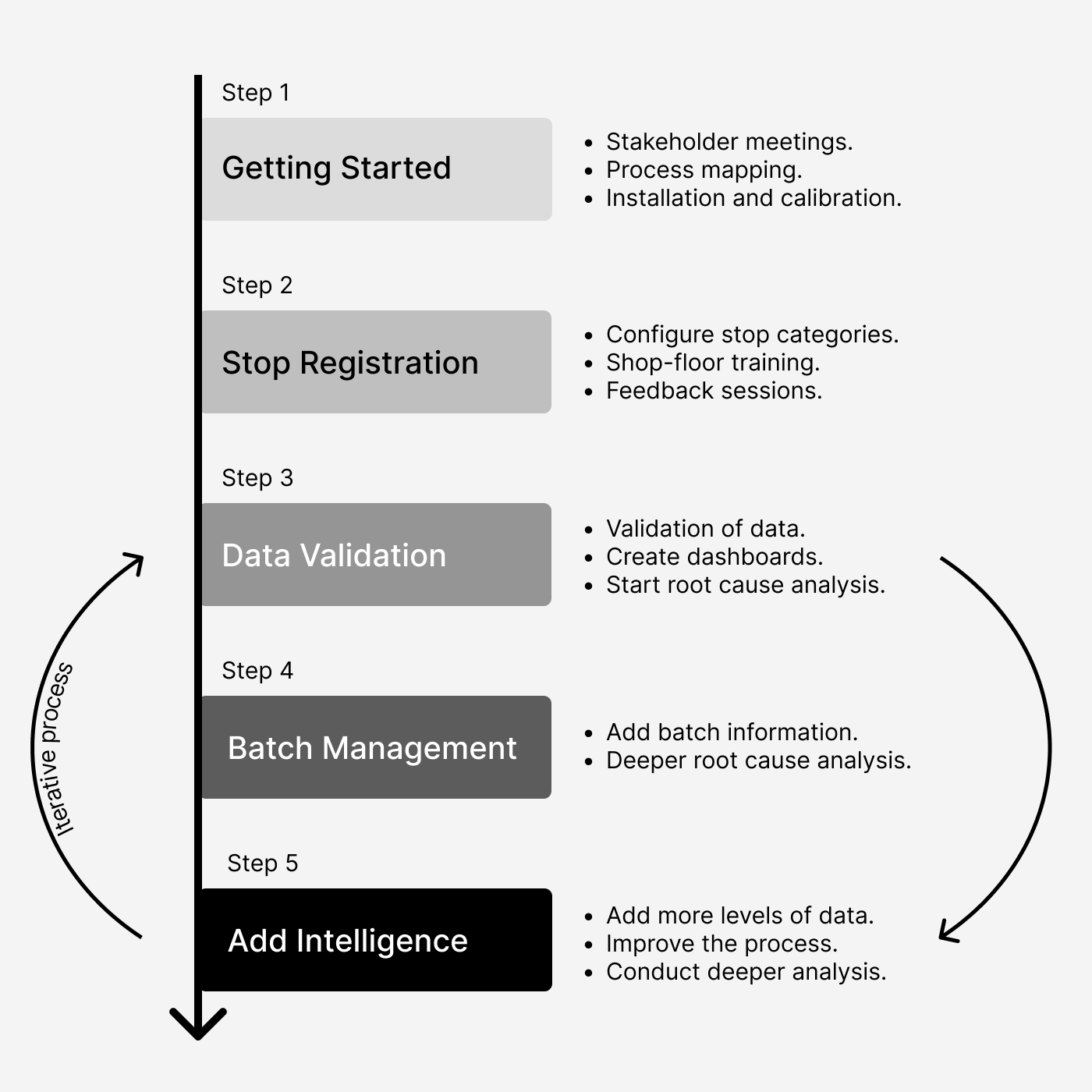
Step 1: First meeting / Getting started
The Highway Solution starts with a kick-off meeting, sensor placement, and starting to gather data through Factbird’s IoT gateways or Kepware integration. This initial data includes both numbers, like how much is produced, and statuses, like if a machine is on or off.
Step 2: Training / Stop registration
Here, the focus is on training, additional sensor configuration, and stop registration. The team investigates why and where stops occur on all lines and machines so that it’s possible to understand what needs to get better.
Step 3: Data validation
Stakeholders make sure the data about stops and signals is true and reflects what's actually happening. This check is crucial for using the data correctly in reports and root cause analysis.
Step 4: Batch management
This step is about improving how work is planned and gaining more in-depth root cause analysis. Adding batch information helps you understand what's made, why it's made in a certain order, and where batch specific improvements can be made.
Step 5: Add intelligence
For deeper analysis, you can start adding extra process data and production data such as quality (scrap and rework), temperature, vibration, voltage, and so on. Mikkel brought up the example of Factbird VIEW here. Factbird VIEW is a video monitoring solution that correlates video footage with production data. This step also captures Factbird developing new AI and machine learning features that Danish Crown will incorporate and use for even deeper insights.
The structured Highway Solution outlines Danish Crown's systematic approach to leveraging data for achieving operational excellence and informed strategic planning.
The results
Danish Crown has been using Factbird since 2020 and has Factbird’s solutions installed on 405 lines in five different countries (Denmark, Germany, Sweden, England, and the Netherlands) as of April 2024. Here are some of the improvements that they have seen so far.
Data-driven decision making
Factbird helps Danish Crown capture and validate accurate production data, revealing valuable insights that were previously based on hunches. This more robust, data-driven approach has led to improved operational efficiency across its sites globally.
The transition to a data-driven culture has not only improved operational transparency but also empowered the management team and operators with real-time insights for immediate action.
As noted by Jannek Segebrecht from the Time and Study Department in Oldenburg, "Factbird has enabled us to visualize the performance in production more precisely... and then act." The detailed data gathering has led to better analysis and faster solving of production problems.
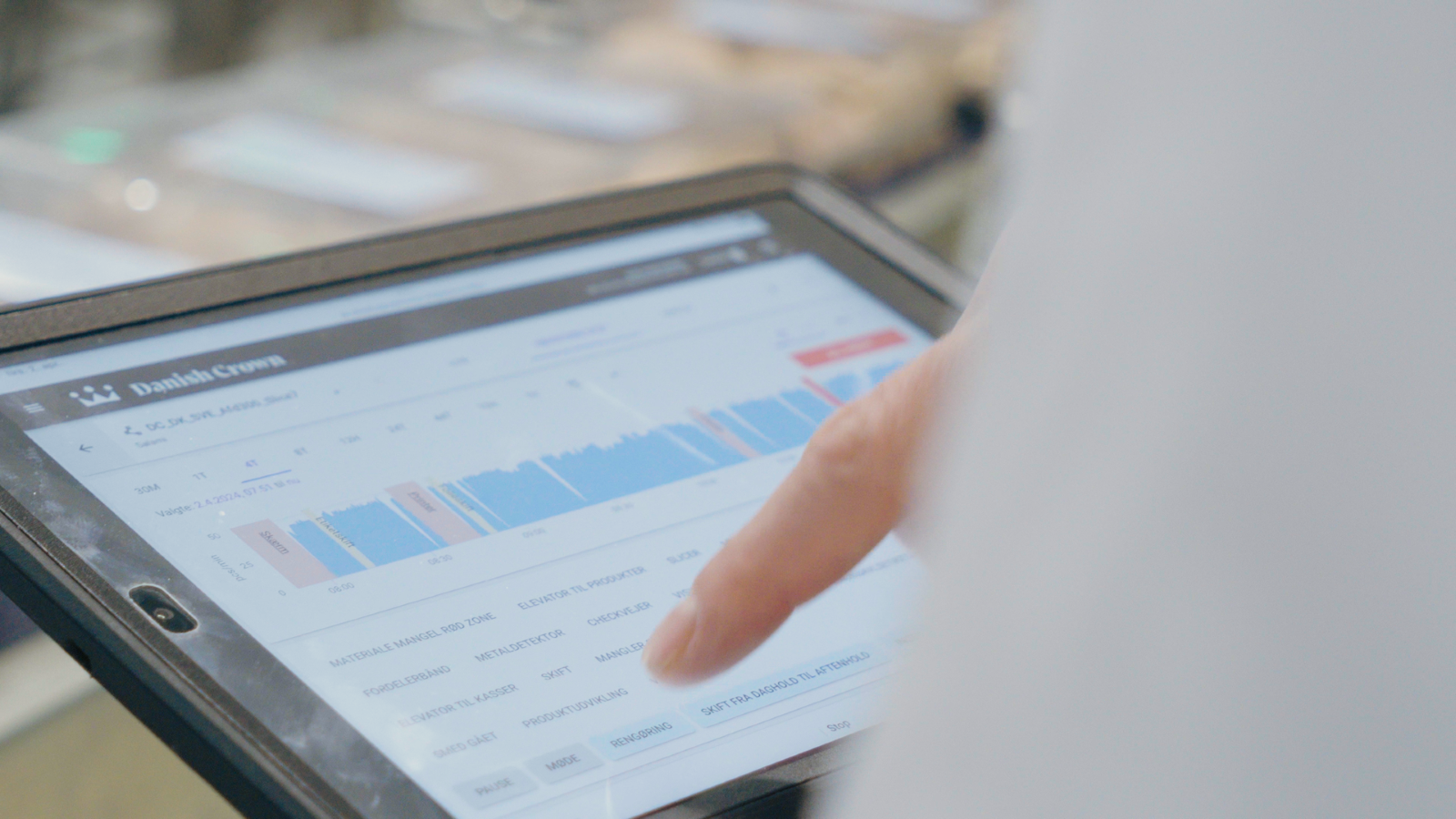
Benchmarking and performance improvement
A key outcome that Danish Crown has experienced using Factbird is the ability to compare performance across different locations thanks to a standardized approach to improving operations. This makes it easier to prioritise resource allocation and make decisions on about where adjustments are needed most, among other things.
At the site level, standardisation means less work for operators. Glenn Ganderup, an Industrial Operator in Vejle, remarks, "My efficiency has improved due to the speed of typing in when you get a stop. Standard stops only require a few clicks and then you have the information you need in the system."
Operational excellence and continuous improvemt
The comprehensive data from Factbird has helped identify improvement opportunities, leading to a 15 % increase in OEE.
"And we have improved very significantly on some lines—in some cases, 15% more OEE performance. And the system itself has already helped us a lot to evaluate this better."
- Christian Kretzer, Packaging Specialist, Oldenburg in Danish Crown
Christian Kretzer, the Packaging Specialist in Oldenburg, emphasized the system's role in enhancing process analysis, which ultimately results in improved efficiency; "The biggest advantage for me is simply that you can analyse processes better, that you can analyse problems and disruptions on the machines better."
Collaborative problem-solving
Beyond individual benefits, Factbird has fostered a culture of collaboration and problem-solving within Danish Crown. As Johan Molenaar, Engineer and Maintenance Manager in Haarlem, pointed out, "Because of Factbird, that circle of communication runs much better now than it used to before the use of Factbird," illustrating how the system has improved communication and teamwork across departments.
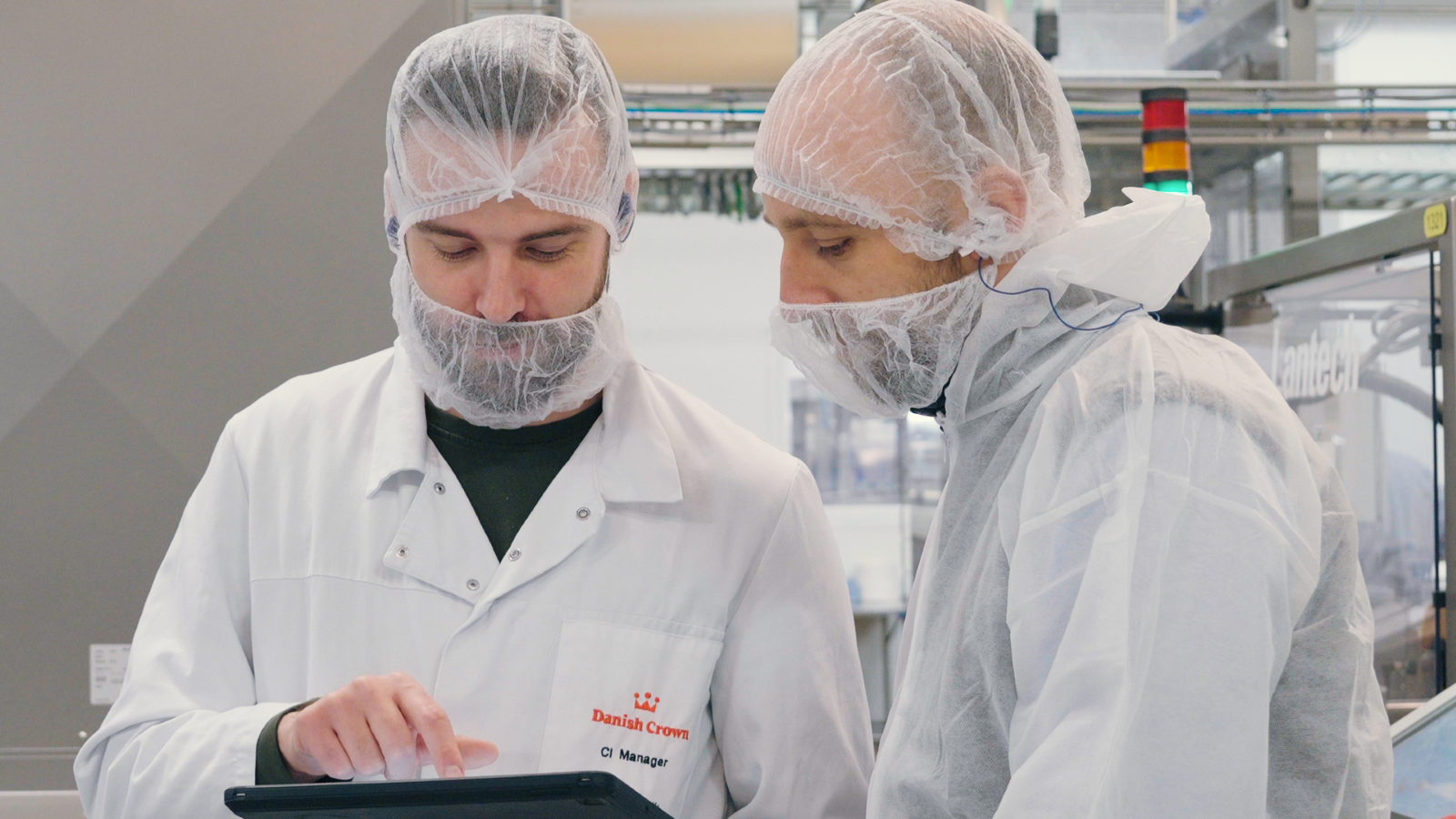
Conclusion
Danish Crown's use of Factbird has marked a shift from intuition-based decisions to a data-driven approach that enhances efficiency across its global operations.
Factbird's ability to help Danish Crown standardize data collection and analysis has provided the team with a better platform for continuous improvement and strategic planning, while also addressing the challenges of operational silos and diverse practices.
The Time and Study Technician in Oldenburg, Jannek Segebrecht, captures the impact of Factbird succinctly by saying, "Factbird has enabled us to visualize the performance in production more precisely and then act."
Jannek’s statement highlights the impact that accurate, real-time data has had on Danish Crown’s ability to not only monitor but continuously improve its manufacturing processes and further its innovation in the food industry.