Factbird’s OEE Waterfall
Now it’s time for us to move on from the Nakajima method for calculating Overall Equipment Effectiveness (OEE) and look at Factbird’s waterfall method.
What are OEE waterfall charts?
The waterfall method of analyzing OEE is popular throughout the manufacturing landscape.
A waterfall chart shows a running total as values are added or subtracted, making it easy to visualize how a starting value is affected by a sequence of positive and negative changes. Commonly used in financial and operational analysis, waterfall charts help break down complex data into clear, incremental steps, like tracking how revenue turns into net income.
In the context of OEE, a waterfall chart illustrates how different types of production losses, such as downtime, slow cycles, and quality defects, reduce the theoretical maximum efficiency of a production line (100%) to its actual OEE scores. By clearly separating the impact of each loss category, the OEE waterfall makes it easier for teams to identify where the biggest improvements can be made.
This is a more modern approach for calculating OEE and factbird’s take on the waterfall has been helping manufacturers around the globe across multiple industries since 2016.
Introduction to Factbird's OEE waterfall method
Here is an overview of Factbird’s OEE waterfall.
You’ll see that the terminology is slightly different from the Nakajima OEE method, and we have added another level called Total Equipment Time.
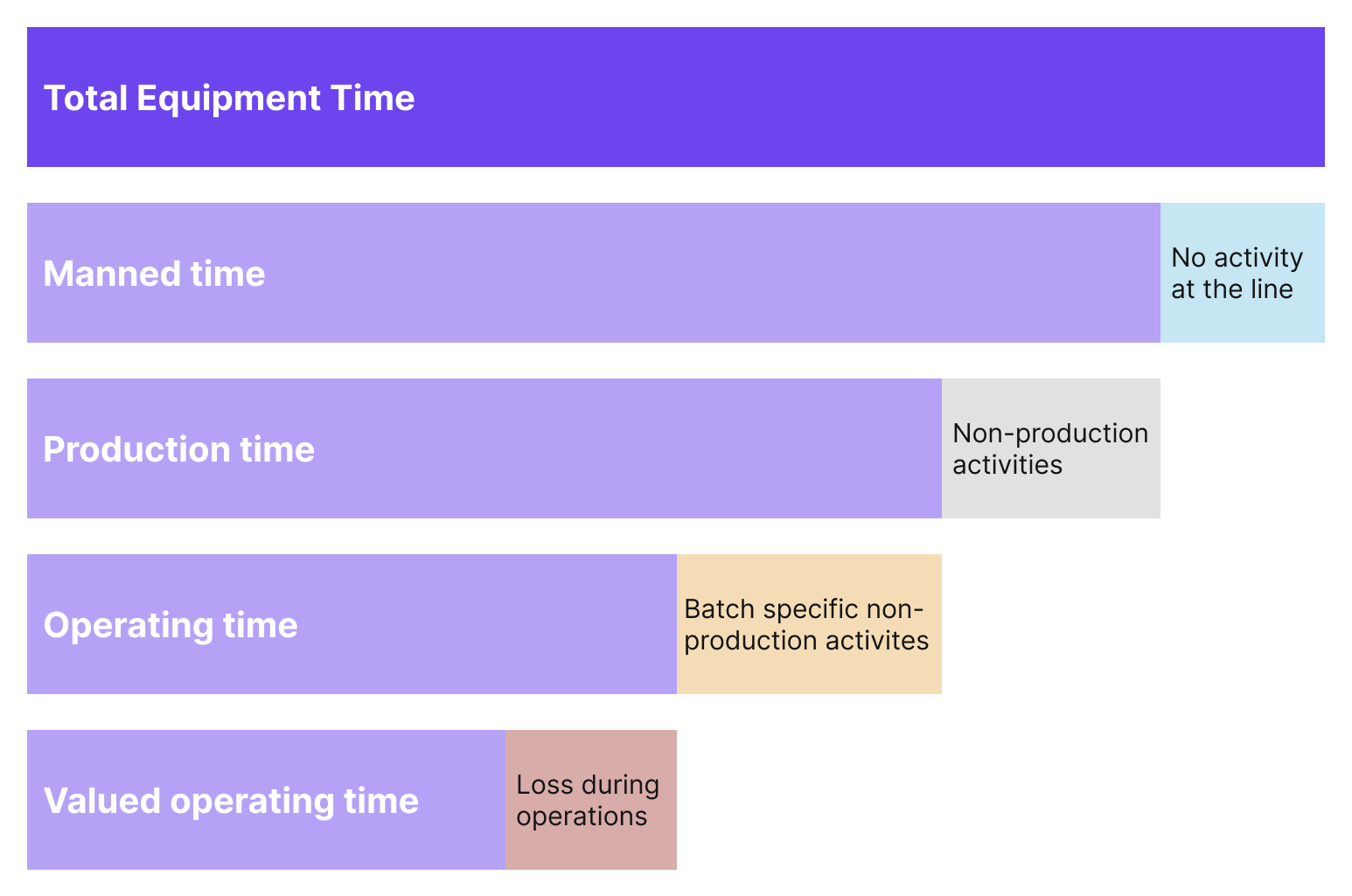
The total equipment time represents the plant’s total potential operation time. When we know this, we can also optimize the time where there is no planned production in our improvement efforts.
This means that you can still separate out unmanned non-production time if you have a lack of orders, don’t work weekends, or operate one shift a day instead of 24/7.
Otherwise, manned time, production time, operating time, and valued operating time are similar concepts to those introduced by Nakajima, but with some differences in how we allocate downtime losses.
We then use these values to break OEE down into four components: OEE1, OEE2, OEE3, and total capacity utilization (TCU).
Let’s take a look at how we define these to get a good understanding of the technique and prepare us for our next lesson, where we demonstrate how stop causes are defined.
Valued operating time
The valued operating time is at the core of everything.
This is the time that we want to increase because this is when our production line or equipment is creating value.
The valued operating time is the value that the other measurements are compared to when calculating OEE1, OEE2, OEE3, and TCU.
And these are the values that we will look into now.
Operating time, Loss during operation, and OEE1
OEE1 looks at the ratio of valued operating time to the operating time, also described as the expected run time.
OEE1 = Valued operating time / Operating time
The stop causes that affect this are categorized as “Loss during operation”.
You can say that in practice, OEE1 is:
OEE1 = (Produced amount / Validated speed) / Time producing
When you know OEE1, you understand the amount of time your production line has actually had available to produce units and the amount of time it has actually spent doing that.
OEE1 takes into account any unplanned downtime and everything else is not taken into account.
Potential OEE1 stop causes are:
- Machine defects
- Process defects
- Waiting time (e.g. materials, operators)
- IT-related stops
- Unplanned cleaning (e.g. after a defect like bottles breaking)
To put OEE measurements in context, let’s take a look at the OEE dashboard in Factbird’s Cloud Application.
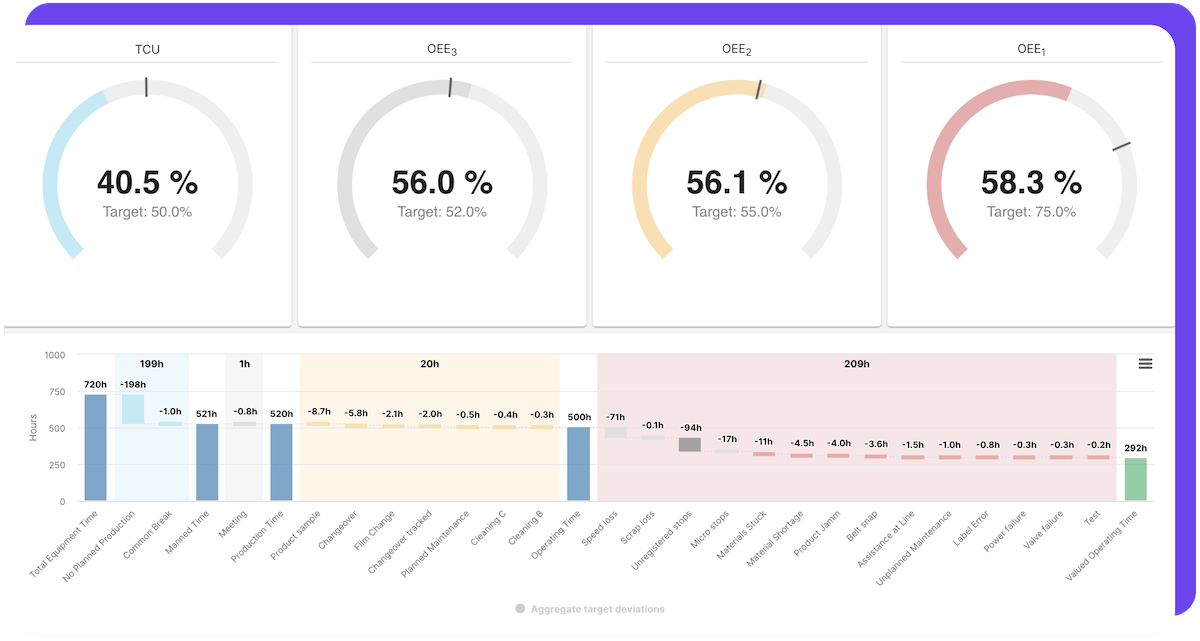
Factbird automatically calculates the different OEE scores based on automatically collected parameters on your shop floor and the stop-causes inputted by your operators.
The OEE snapshot we are looking at covers a period of 720 hours, or 30 days for a large FMCG company.
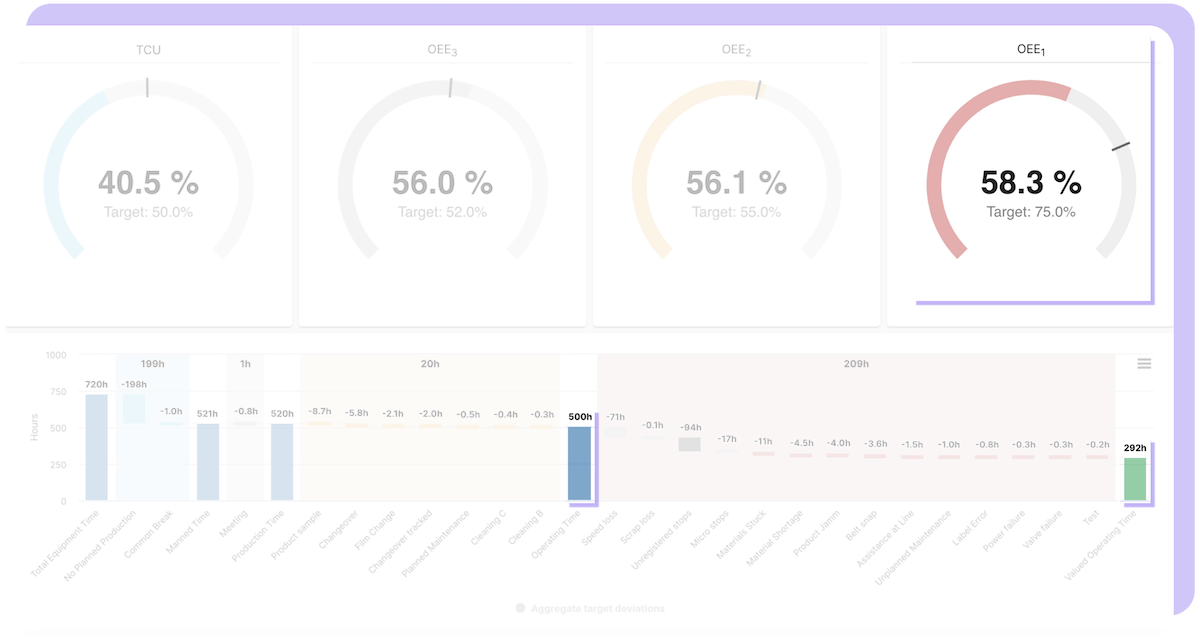
During these 720 hours, we have had 500 hours of operating time where we should have been producing product, and out of that, we have been online for 292 hours.
This leaves us with a 58.3% OEE1 score.
Production time, Batch specific non-operation, and OEE2
OEE2 takes into account the time a production line is not running due to batch changeovers, resupplies, and cleaning.
We call these stops Batch specific non-operation.
OEE2 = Valued operating time / Production time
In practice, this is
OEE2 = (Produced amount / Validated speed) / Time doing batch-related work
Although these stops are planned, they take a significant amount of time from the total available time.
Manufacturers tend to focus on the OEE1 stops the most because they are unplanned and annoying, but I’d recommend spending just as much time looking into your planned stops and seeing how you can optimize them as well.
Potential OEE2 stop causes are:
- Batch Changeover (e.g. preparation, re-tooling)
- Resupply (e.g. material, packaging, labels)
- Cleaning (e.g. end-of-shift cleaning)
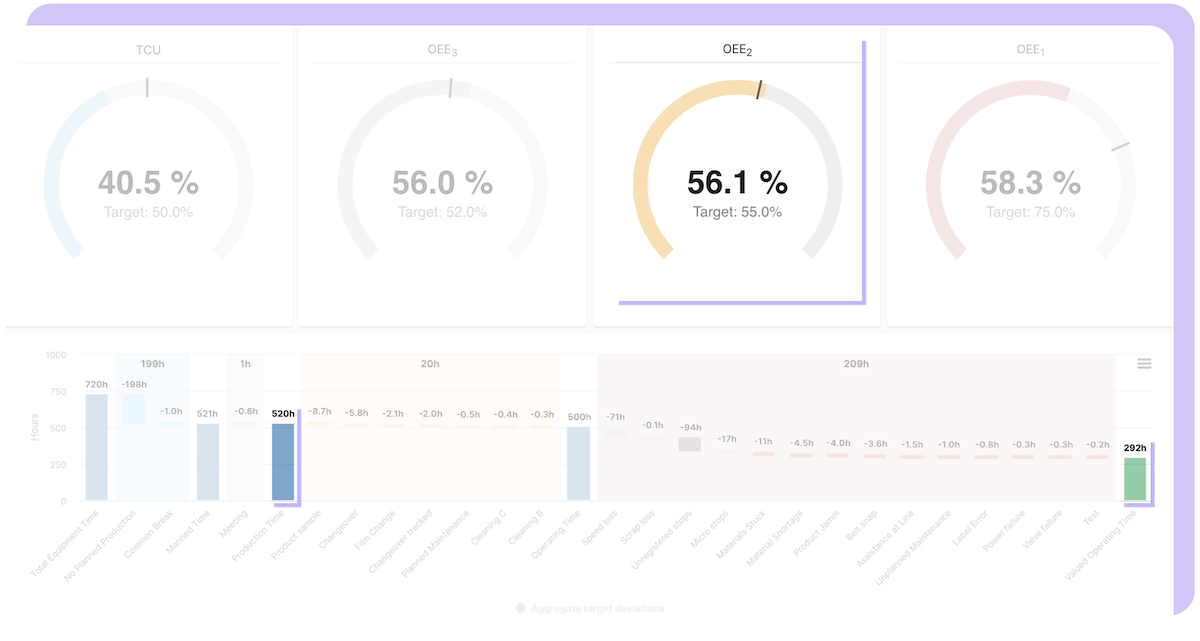
In the example, we have had 520 hours of production time over 30 days.
Once again, taking the total valued operating time of 292 hours into account, we get an OEE2 score of 56.1%.
Manned time, Non-production activities, and OEE3
OEE3 accounts for all the planned stops, such as meetings and training.
We call this category of stops Non-production activities.
OEE3 = Valued operating time / Manned time
In practice, this is
OEE3 = (Produced amount / Validated speed) / Manned activity time on the line
Some OEE3 stop-cause examples are:
- Planned maintenance
- Quality inspections
- Personnel activities (e.g. meetings, training)
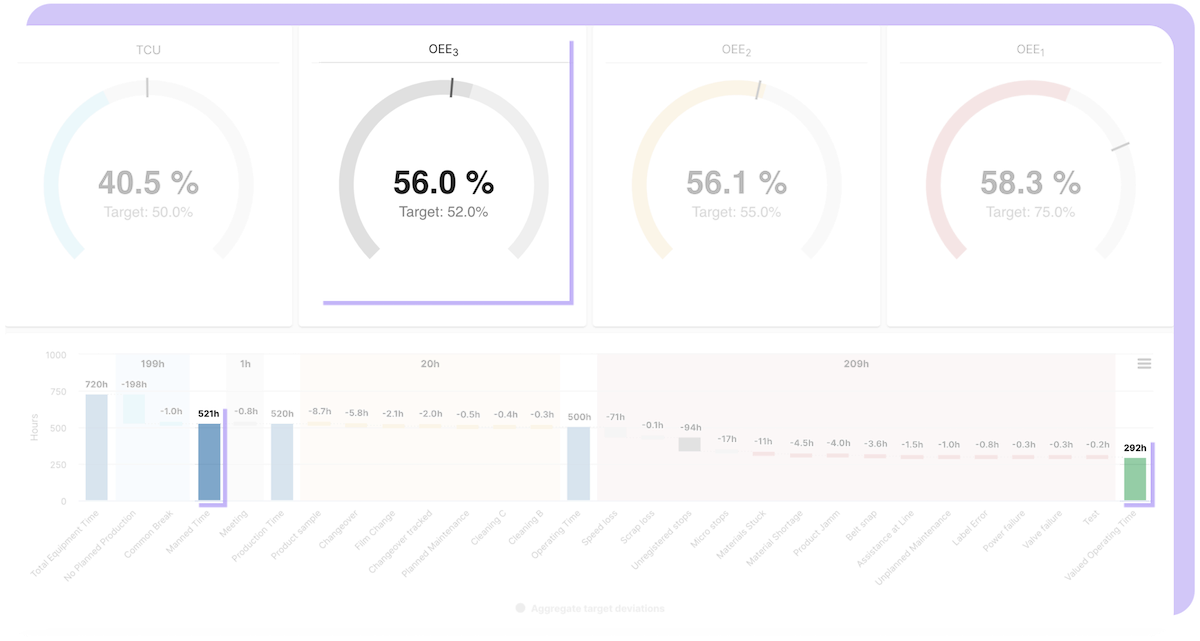
In the example, our manned time is 521 hours thanks to having only 1 hour of meetings.
This leaves us with an OEE3 score of 56.0%.
Total Capacity Utilization (TCU)
Finally, TCU takes into account planned downtime due to vacations, company breaks, or simply no planned production.
TCU = Valued operating time / Total equipment time
In practice, this is
TCU = (Produced amount / Validated speed) / Total period of measurement
If TCU is 100%, then your machine, production line, or plant is running at 100% capacity and you should be teaching us how to improve OEE.
In reality, if you are in or near this situation, you then know that the best thing you can do would be to increase production time.
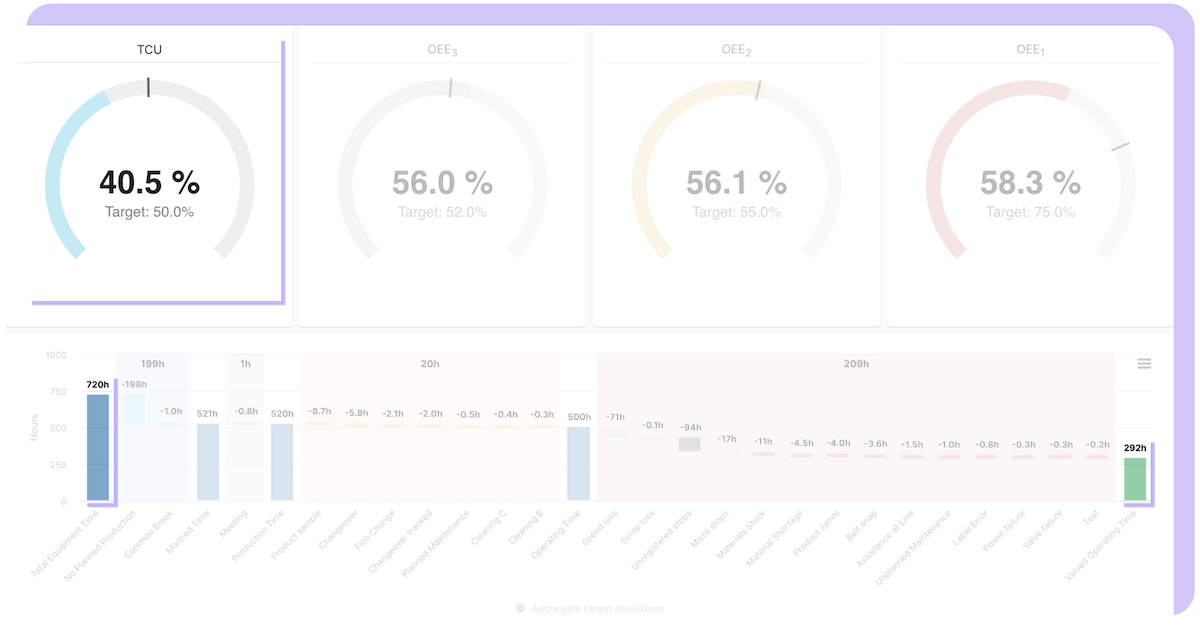
In this example, our total equipment time is 720 hours, which is 30 days at 24 hours a day. We end up with a TCU of 40.5% after dividing the total equipment time by 292 hours of valued operating time.
And that's it. This was just a brief introduction to the OEE waterfall and it's different components.
Next up, we're going to take a more thorough look at how to calculate OEE using Factbirds methods including a deep dive into stop causes and how to allocate them.