What is Overall Equipment Effectiveness?
Key takeaways:
- Overall Equipment Effectiveness (OEE) measures the productivity of manufacturing operations.
- OEE assesses availability, performance, and quality with a single percentage metric.
- Originated in Japan's 1960s TPM program to enhance manufacturing processes.
- Identifies losses, improves productivity, and enhances profitability.
- A tactical and strategic metric for continuous improvement and decision-making.
Introduction to this OEE course
Factbird makes it easy for manufacturers to collect production data, analyze OEE, and improve productivity. Manufacturers have been using our OEE solutions for over eight years to reduce waste and increase productivity. And now I would like to share some of our OEE expertise with you.
In this course, we will guide you through the fundamentals of OEE, its calculation methodologies, examples of OEE in practice, and useful insights that will help you optimize production.
Whether you're new to the concept of OEE or looking to refine your expertise, this course offers valuable tools and strategies to improve your manufacturing processes and drive significant operational gains.
This first lesson will lay the foundation for the next steps of calculating, analyzing, and improving OEE.
We’ll look at a simple definition of OEE and then discuss why OEE is important.
But first off, let’s start with a short history of OEE.
A brief history of OEE
Originating in Japan as part of the Total Productive Maintenance (TPM) program in the 1960s, OEE was developed to aid in the improvement of manufacturing processes.
OEE gave manufacturers a clear reference point for the productivity of individual equipment in a factory and was a big help for continuous improvement.
As a side note, Nakajima later said the total productive maintenance program should have been called total productive manufacturing instead. This is because TPM about improving the production process in the plant, not just the equipment. Equipment is part of production effectiveness, but OEE can have a broader business perspective by focusing on the entire production system.
Over time, OEE evolved to become a standard metric for assessing production efficiency, not just in Japan but globally. Most people believe that Nakajima’s 1988 publication of the book Introduction to TPM: Total Productive Maintenance is what first popularized OEE in the West.
Since 1988, OEE has become the gold standard for measuring manufacturing productivity and is used as a key performance indicator (KPI) for production plants, factories, and workshops that are looking to improve.
The definition of OEE
Manufacturers use Overall Equipment Effectiveness (OEE) to understand how well they’re using their resources. Measured as a percentage, a score of 100% means the equipment is running at peak performance; producing only good parts, as fast as possible, with no downtime. By highlighting how much of the planned production time is truly productive, OEE gives a clear, unified view of availability, performance. We begin to dive into these three components of OEE in the next lesson.
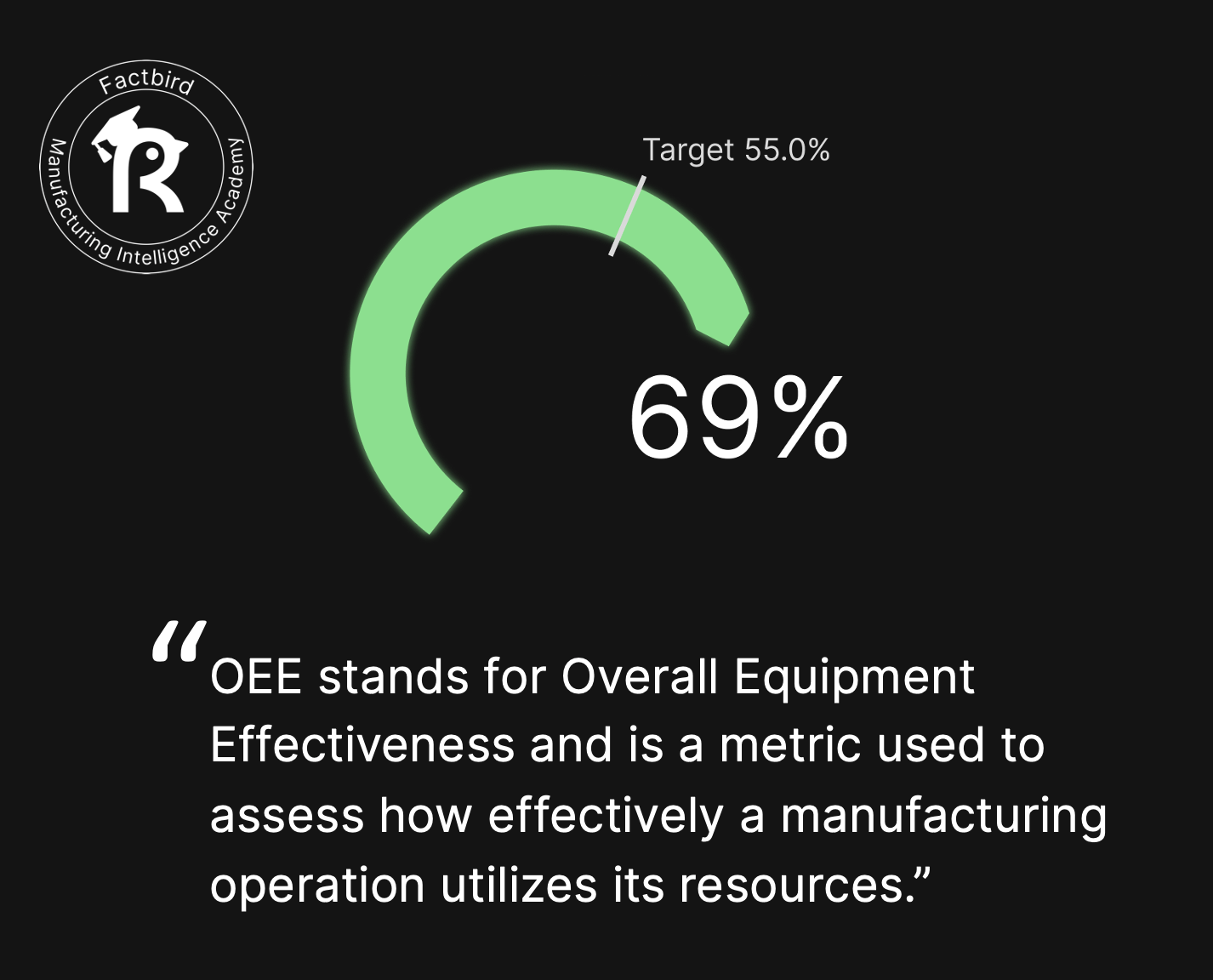
OEE gets worse when the machine:
- Is not in use
- Has stopped
- Runs slower than the maximum speed
- Makes faulty items (scrap)
An good example of OEE analysis
Here’s a short example of a process for measuring and optimizing OEE:
First, define perfection.
How much could you make if you ran a standard product mix every hour of the year, making 100% first-time-right product (with maximum yield), without losses due to changeovers and meetings, at 100% of your maximum demonstrated sustainable rate?
Next, define reality.
This is when you record how much you are actually making.
Then define your losses.
It’s time to do some investigation into the gap between perfection and reality. What losses are causing the gap?
At this point, you have your OEE. Now it’s time to take action on your OEE analysis.
Now consider whether the losses are acceptable.
Some losses will be acceptable. You will have some planned and unplanned downtime. But are you effectively managing the losses that you have identified? Where the answer is no, this is what you optimize.
Why is OEE important?
So why do so many manufacturers use OEE as a key part of their production analysis?
The importance of OEE in manufacturing lies in its ability to provide a clear and measurable way to identify losses, benchmark progress, improve the productivity of manufacturing equipment, and drive change from the shopfloor to the boardroom.
It’s a crucial tool for identifying areas for improvement in production processes, ensuring equipment is used to its full potential, and ultimately improving sustainability and enhancing profitability.
OEE’s comprehensive overview of how well manufacturing operations are running helps organizations to:
Identify Weaknesses: OEE allows manufacturers to pinpoint areas of inefficiency and waste, unveiling opportunities to enhance production and mitigate losses.
Optimize Productivity: The insights derived from OEE help manufacturers make informed decisions, streamline processes, and optimize machinery utilization, which, in turn, bolsters productivity.
Improve Quality: By focusing on the quality component of OEE, manufacturers can optimize their processes by increasing units produced and reducing waste.
Increase Profitability: Enhanced productivity and quality, coupled with reduced waste and downtime, lead to increased profitability, allowing organizations to stay competitive in the ever-evolving manufacturing landscape.
OEE is both a tactical and strategic metric:
- Tactical: OEE helps you identify and minimize day-to-day and week-to-week losses.
- Strategic: OEE helps you identify potential capacity for future expansion.
For example, OEE lets you evaluate whether or not to invest in new equipment.
If your production lines are running under capacity, say with an OEE of 50% when the average for similar operations is 65%, then you know that optimizing your existing equipment would make a lot of sense before throwing more equipment at it and increasing costs.
I hope this was a helpful overview of what OEE is for you. You should now know a bit about the history of OEE, know what OEE is based on our short definition of OEE, and know why OEE is so important in manufacturing.
Join us in the next lesson where we dive into the components of OEE.