Building a culture of maintenance excellence with operator-driven reliability (ODR)
By empowering operators, manufacturers address maintenance needs before they become critical failures. Operator-driven maintenance drastically reduces downtime.
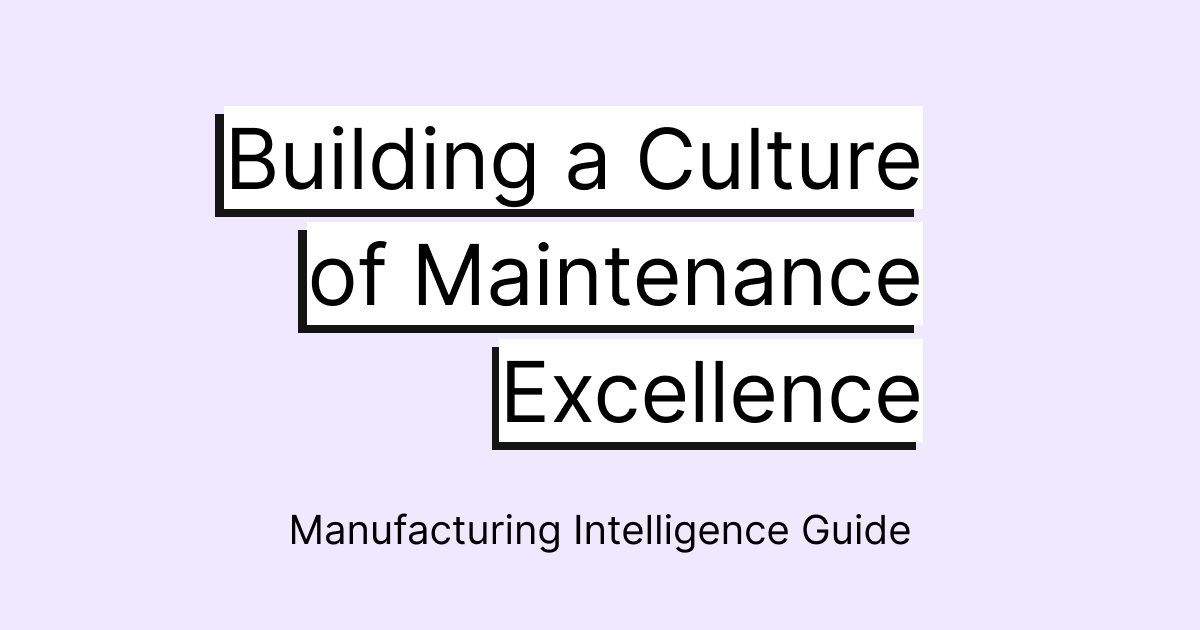
In today's fast-paced industrial landscape, you always need to be on the look out for new ways to enhance efficiency, reduce costs, and maintain uninterrupted productivity.
One area with significant opportunities for manufacturers is in the realm of maintenance.
According to Mckinsey’s survey (2023), many companies are missing out on significant opportunities to increase the value of their maintenance efforts and reduce costs.
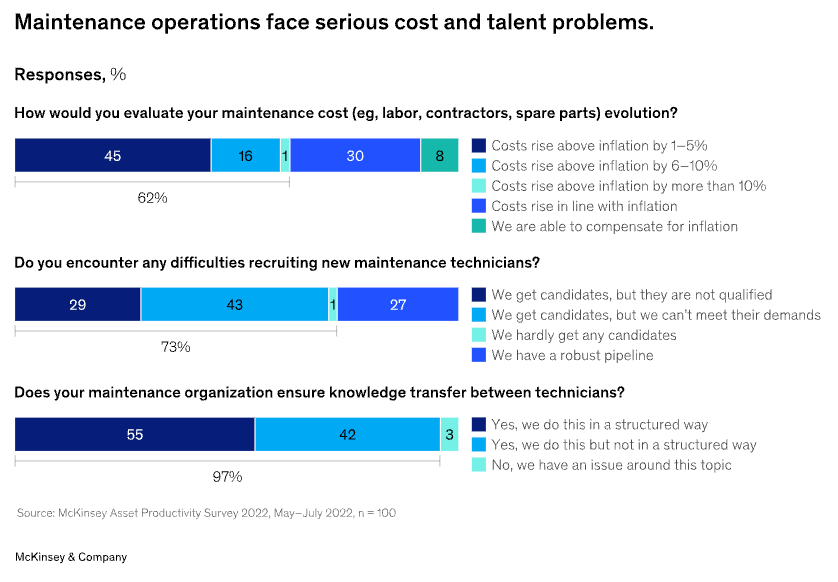
The power of preventive maintenance cannot be overstated. By being proactive, organizations can address maintenance needs before they escalate into critical failures. This approach, which includes regular inspections and timely repairs, can prevent equipment breakdowns and costly downtime.
However, there's an additional layer to optimizing maintenance, known as Operator-Driven Reliability (ODR). When operators — the frontline personnel with deep knowledge of the equipment and processes — are involved in identifying and resolving maintenance issues, it allows for the timely correction of small issues before they turn into major problems.
Through operator-driven reliability, organizations can optimize their resources more effectively. When utilizing operators to identify and resolve minor issues, technicians and engineers can focus on more critical maintenance tasks. This targeted allocation of resources ensures that expertise is used where it matters most, leading to better overall maintenance outcomes and cost savings.
When utilizing operators to identify and resolve minor issues, technicians and engineers can focus on more critical maintenance tasks.
In this article, we will explore how to cultivate an operator-driven maintenance culture, and how Factbird can support you in this transformative journey.
What is Operator-Driven Reliability (ODR)
In industrial settings, reliability is a paramount concern. The smooth operation of complex machinery and processes is critical for productivity, profitability, and, most importantly, the safety of personnel.
Traditionally, reliability efforts have primarily focused on maintenance strategies and equipment design improvements.
However, a new approach is emerging that recognizes the invaluable role operators play in ensuring reliability—Operator-Driven Reliability (ODR).
ODR is a concept that harnesses the knowledge, experience, and expertise of operators to enhance reliability in industrial environments. By actively involving operators in the reliability process, organizations can tap into their deep understanding of the systems they operate, enabling them to detect, diagnose, and address issues before they escalate into failures or safety incidents.
The foundation of ODR lies in empowering operators to take ownership of reliability. By providing them with the necessary tools, training, and authority, organizations can transform operators from mere machine operators into proactive reliability champions. This shift in mindset enables operators to become the first line of defense against unplanned downtime, equipment failures, and potential hazards.
One of the key elements of ODR is fostering a culture of collaboration between operators, maintenance teams, and engineering departments. Open communication channels and cross-functional cooperation allow operators to share their insights, observations, and concerns with maintenance personnel and engineers. This collaborative approach ensures that all stakeholders are aligned in their efforts to improve reliability and safety.
Strategies for Adopting an Operator-Driven Approach
To facilitate ODR, organizations can implement various strategies and leverage technologies. Here are a few examples:
Operator training and development: Comprehensive training programs equip operators with the knowledge and skills to identify early warning signs of potential failures, understand equipment limitations, and perform basic troubleshooting. By investing in their professional development, organizations empower operators to make informed decisions that positively impact reliability.
Standardized operating procedures: Well-defined and consistently followed operating procedures reduce the risk of human error and variability in system operation. Clear guidelines and protocols enable operators to execute tasks more effectively, minimizing the likelihood of reliability issues arising from incorrect operation.
Condition monitoring and data analytics: Deploying advanced monitoring technologies such as sensors, IoT devices, and data analytics platforms can provide real-time insights into equipment performance. Operators can leverage this data to detect anomalies, track trends, and take proactive measures to address potential issues promptly.
Root cause analysis: Encouraging operators to participate in root cause analysis efforts when failures occur allows them to contribute their firsthand knowledge and observations. This involvement not only enhances problem-solving capabilities but also helps develop a sense of ownership and accountability among operators.
Feedback mechanisms: Establishing feedback loops between operators and maintenance teams is crucial for continuous improvement. Operators should be encouraged to provide feedback on equipment reliability, highlight recurring issues, and suggest potential solutions. This information serves as valuable input for maintenance planning and equipment design modifications.
The benefits of implementing ODR extend beyond improved reliability. Engaging operators in the reliability process can boost employee morale and job satisfaction, as they feel more valued and involved in the success of the organization. Moreover, by empowering operators to actively contribute to safety and reliability, the overall safety culture of the organization is strengthened, resulting in fewer incidents and reduced risks for personnel.
Operator-Driven Reliability represents a paradigm shift in how organizations approach reliability and safety. By recognizing the expertise and insights of operators, organizations can unlock significant untapped potential to enhance efficiency, minimize downtime, and ensure a safer work environment.
Elevating Maintenance Practices for Optimal Efficiency and Reliability
Factbird's Preventive Maintenance module offers organizations an easy-to-implement solution to enhance their maintenance practices and empower operators to perform tasks efficiently and reliably. By actively involving operators in maintenance planning and execution, the platform provides a centralized space to create and manage maintenance plans, schedule recurring tasks, and allocate resources effectively.
Efficient task management is crucial for successful maintenance operations, and Factbird's module simplifies the process. Operators gain a clear overview of scheduled maintenance activities, assigned tasks, and their status. Real-time updates and notifications ensure effective communication, enabling operators to track and complete tasks on time, reducing delays and improving overall efficiency.
When leveraging Factbird's preventive maintenance capabilities, operators can optimize equipment performance. Regular maintenance tasks, such as inspections, lubrication, and calibrations, empower operators to identify and address performance deviations promptly. This proactive maintenance approach maximizes equipment performance, reduces energy consumption, and minimizes the risk of breakdowns or inefficiencies.
Moving from reactive to proactive maintenance: Watch the webinar >
Factbird's Preventive Maintenance module also offers a unique advantage by prioritizing counts-based preventive maintenance over calendar time. It provides a simple plug-n-play solution that seamlessly integrates preventive maintenance management with live production data. Unlike traditional CMMS systems, which require manual entry of cycle counts or complex integrations with PLC data, Factbird streamlines the process, ensuring accurate and efficient preventive maintenance based on real-time production data. This innovative approach eliminates the need for manual tracking and enhances the overall effectiveness of maintenance practices.
Start Prioritising Maintenance
Maintenance is a cornerstone in the world of industrial operations and reliability, with Operator-Driven Reliability (ODR) adding a powerful layer of practical insight. ODR shifts some essential maintenance tasks from technicians to operators, who are closely familiar with the equipment's daily behavior and output. As a result, operators are often best suited to spot early signs of potential issues.
When combined, effective maintenance practices and ODR create a powerful partnership that significantly enhances the reliability and performance of industrial assets.
Regular inspections, timely repairs, and proactive maintenance strategies help organizations reduce unexpected downtime, optimize equipment usage, extend asset lifespan, and cut costs. Maintenance teams are indispensable, supporting operators in fostering a culture of reliability and operational excellence. Their expertise in maintaining and servicing equipment forms a key pillar of industrial reliability, ensuring smooth operations and safety for both personnel and assets.
Factbird's Preventive Maintenance module offers a way to supercharge your maintenance practices and empower operators for efficient and reliable task execution. By using this module, organizations can adopt a proactive stance, boost equipment performance, optimize resources, and reach peak efficiency and reliability. This synergy of preventive maintenance and operator-driven reliability paves the way for operational excellence and long-term industrial success.