Building a manufacturing tech stack
We will discuss in today’s article: how to build a manufacturing tech stack in 2023 and pick the right software and hardware to boost production.
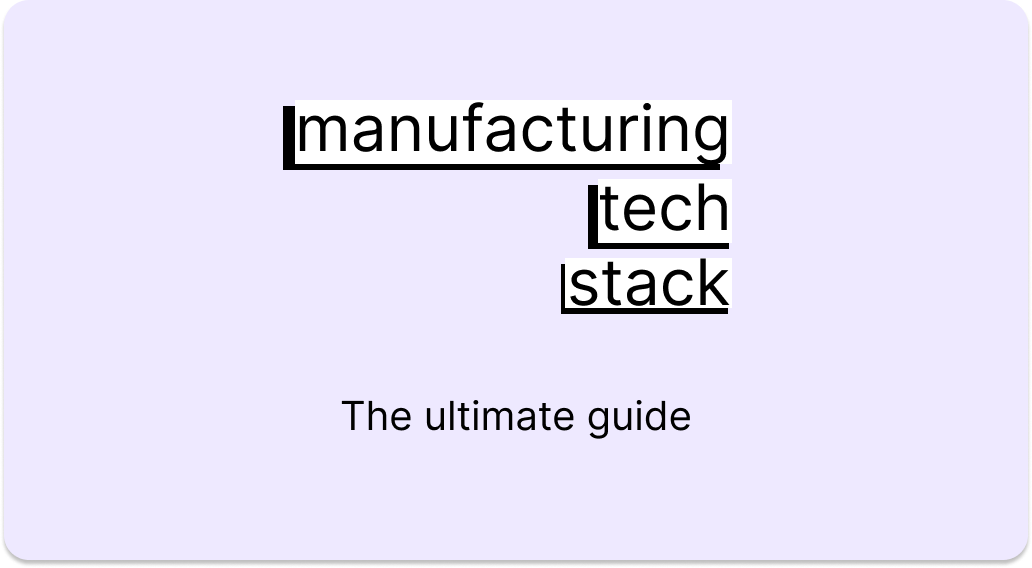
Factories can experience a real challenge when picking software and hardware solutions to serve their production needs. The extensive range of options can overwhelm managers when picking a tailored solution that increases both effectiveness and gives insight into what’s going on with production lines.
Not so long ago, relying on ERP systems with manual data entry, Excel-made reports, and multiple other software layers was the norm, which only increased the manufacturing complexity for operators in general. Thankfully, Manufacturing Intelligence Solutions came to the rescue, providing a much clearer picture of what’s happening in our factories. We will discuss in today’s article: how to build a manufacturing tech stack in 2023. Factories can experience a real challenge when picking software and hardware solutions to serve their production needs. The extensive range of options can overwhelm managers when picking a tailored solution that increases both effectiveness and gives insight into what’s going on with production lines.
Technical glossary
Before dwelling on how to make a manufacturing tech stack, we must explain some core concepts linked to this topic. You can come across some terms that refer to software solutions, which may not be clear enough from a first-approach experience.
- SaaS (Software as a Service): Software as a Service refers to applications that do not require additional downloads or installation procedures from the client side. Most of these applications work in a cloud-based format, using the internet to interact with its interface. Some examples of SaaS applications are Salesforce, Dropbox, Cisco, Google Workspace, and Factbird
- PaaS (Platform as a Service): Platform as a Service brings a framework in which users can create custom applications without worrying about the infrastructure behind the process (storage, operating system, upgrades, etc.). It is mostly intended for system virtualization, such as Windows Azure or AWS Elastic Beanstalk.
- IaaS (Infrastructure as a Service): Infrastructure as a Service attends to users' needs by allowing them to work with on-demand services without buying hardware. It involves a cloud-based computing infrastructure, listing servers, operating systems, storage, etc. Unlike SaaS or PaaS, users are the main ones responsible for the management of maintenance of the operating system. Some popular examples are Amazon Web Services, Cisco Metacloud, and Microsoft Azure.
- SMB: Small and Medium Business Manufacturers.
- CMMS: Computer Maintenance Management System. It is software that centralizes the maintenance-required information, facilitating maintenance operations. At its core, we can consider it a database for maintenance services.
- Visual Workflow System: It is a dashboard solution that lists work instructions to help operators be more efficient in their tasks. Although they are typically used in some industries with large assembly processes (i.e., the automotive industry), they can be used for several other applications, such as maintenance procedures.
- MES: A Manufacturing Execution System, also known as Manufacturing Operations Software Systems, is a software solution that allows operators and managers to monitor, track and document the entire process from raw material to finished product. They work hand-in-hand with Enterprise Resource Planning (ERP) software.
- CRM: The Customer Relationship Management software monitors the interactions with current and potential customers. They are used to help the sales process and help factories keep track of orders made.
- Quoting System: A Configure-Price-Quote (CPQ) software allows users to generate quotes or proposals to send to potential customers. It helps companies to increase sales efficiency by automating the quotation process and usually includes the inventory system, input from the sales department, and integration with CRM.
- WMS: A Warehouse Management System is a software solution used to visualize and control a company’s inventory and supply chain.
- Manufacturing Intelligence Solution: Usually comes in SaaS format that can be accompanied by edge devices that ease the data collection burden; these software solutions help extract real-time data from manufacturing equipment and also to automate workflows.
- IoT: The Internet of Things can be understood as a network of physical elements paired with sensors, software, and other monitoring technologies by which we can exchange real-time data for monitoring, automation, and analysis. IoT helps manufacturers to elevate their production levels through increased efficiency, new unexplored production potential, or to recognize the flaws in manufacturing processes. We can find references to this as IIoT, which stands for Industrial Internet of Things - the area that particularly involves us.
What is a Manufacturing Tech Stack?
A manufacturing tech stack refers to a set of software, platforms, and technologies manufacturers use to support their operations. Manufacturing tech stacks help to manage and monitor product design, supply chain, production processes, and quality control, among other things.
Overall, the intent of using a quality technology stack diagram is to improve efficiency while keeping operative costs under control and increasing a company's competitive advantage. Although many instantly link manufacturing tech stacks with ERP, these days, we need to consider more complex networks in which ERP is just one part of an ecosystem run through IIoT technologies.
What is the tech stack for manufacturing companies composed of?
To properly understand the concept of “tech stack,” let’s begin by studying that software/hardware ecosystem as a series of layers.
The first layer speaks about Logistics. Each factory has to control the influx of raw materials, assembly parts in a production chain, finished goods, and storage. This logistics layer can comprise WMS, MES, or similar IIoT solutions.
Next comes the Production layer, which processes the raw materials into finished products. This production layer is strictly linked to the third layer, as it transforms the raw materials based on managerial input. For this stage, we can count on Incident Management Systems (for reporting/solving technical problems), Machine Monitoring Data Platforms, Visual Workflow Systems, CMMS, or SaaS solutions like Factbird for manufacturing intelligence software.
The third layer refers to Cost and Manufacture, addresses the estimated production costs, handles customer orders, and creates the baselines for manufacturing processes. At this stage, we count on CRM, Quoting Systems, ERP, and SaaS apps (i.e., Factbird).
Finally, we reach the top of this technology stack diagram, the fourth layer, Design. This is where new products are developed or modified, and then instructions are sent to the third layer to estimate production and sales costs. The software/hardware options for this layer depend mostly on the industry. Some niches are CAD/CAE heavily dependent. Others work with 3D modeling software or similar design applications, and so on.
Aside from this, we have to consider other tools in the tech stack of any manufacturing company:
Communication: Software solutions like Microsoft Teams, Slack, Google Spaces, and similar are used to keep in-company chats to link the work of different teams. We can add Google Meets, Skype and Zoom for video call meetings.
Task Management: Microsoft Project, GanttProject are collaborative task management tools to follow up on pending work done or under process.
Documentation: Some companies prefer to work cloud-based, opting for the Google suite (Google Sheets, Google Slides, Google Docs) or Microsoft 365 (Word, Excel, PowerPoint, Access, Project, Visio). The main point to highlight is that documentation systems in manufacturing companies should opt for cloud-based services to easily retrieve data by any authorized user and not depend on computer hardware (flash drives, hard drives, etc.)
Data Exchange: What about when manufacturing companies have to move files between locations? OneDrive, Google Drive, Box, and Mega are used for this purpose. Large files, like video footage, can be easily distributed through a link and accessible by any authorized organization member.
Data Analysis: Databases and data analysis depends heavily on which industry we are working in. Generally, companies opt for solutions like PowerBI, Jupyter Notebook (Python-based), SAS, and Tableau. Databases can be relational, like MySQL, Postgre, SQL, and Oracle, or non-relational, like MongoDB, Apache Cassandra, Oracle NoSQL, etc. Other utilities for data analysis are strictly linked to sales, marketing (Google Analytics), and financial departments.
The IT-related tech stack is entirely dependent on the needs of each project and the work methodology of dev teams, so that we won’t dwell on those items in detail. Generally, they work with Git (version control), PaaS solutions for packing containers like Docker or Kubernetes (DevOps tools), and IDE software like Visual Studio Code.
When should you perform a manufacturing tech stack audit?
There are some leading indicators that the current hardware and software platforms used by factories don’t perform as expected. Check these three points below to evaluate if it is time to perform a software stack audit.
Data feedback isn’t reliable
This is an immediate sign that your technology stack diagram isn’t working as it should. It can present itself in a number of errors being triggered through automation processes, data lost through integrations, or considerable differences in data output.
As data errors tend to be cumulative, even the slightest error can build delays or lead to inaccurate information over time.
Integration issues
Some manufacturers prefer to work through a series of steps for data extraction and reports, which usually involve data from sensors sent from the manufacturing intelligence software to Power BI. When this process triggers many red flags, it is time to ask ourselves if the current technology stack supports that process.
If your team has to lose 20-30 minutes in report creation because the data cannot be sent automatically, then consider you are losing an average of 80-120 minutes a day (in a four-shift scheme). By manually processing data, that is more than 8 hours a week (an entire shift). That simple factor has to be an eye-opener.
Your company is paying for unused tools
There are plenty of wasted opportunities for factories when they purchase software solutions that they later neglect due to not understanding how they work or inconsistent integrations. Instead of paying for that sum, or worse, having perpetual licenses of unused software, opt for audit and training services to extract its potential for your requirements.
Keep an eye on tools that perform the same tasks, and in case that happens, opt for the one that offers better perks and a lesser learning curve for operators.
Is there a difference between small and large companies in their tech stack needs?
Yes, we can find differences between the technology stacks used in small and large companies due to the complexity of their operations.
Small companies tend to opt for more affordable, easy-to-understand solutions. Generally, small companies look for solutions that can be paired with legacy machinery, as fully upgrading shop floors result outside their financial means. Also, since smaller companies have a closer relationship with their personnel, their skills matter much regarding which technologies are picked, so they don’t dwell in hefty training courses to understand new technologies.
In contrast, larger companies seek solutions that allow them to scale their business operations over time. Efficiency is the primary metric sought by larger organizations, and generally, there are no budget restrictions if the upgrade implies a significant performance increase. Larger companies also count on regular training sessions hosted in-company. Hence, their personnel stays up-to-date with the latest trends in the industry, as well as preserve their competitive edge in the market. Using a new, revolutionary solution in their tech stack wouldn’t be an issue considering these factors.
What does the future look like for manufacturing tech stacks?
The path toward the future is Industry 5.0. When considering companies that opt for Industry 4.0 as the benchmark to aspire to, reality tells us that manufacturers are moving away from efficiency, automatization, and big data analytics to a different view of production. What does this mean? Let’s analyze some stats.
- Manufacturing activities contribute to 17% of the environmental impact of the US, according to the National Institute of Standards and Technology (NIST). Unless the trend changes, a 26% increase in emissions from manufacturing processes is expected by 2050.
- Remanufacturing is considered below 2% for most non-consumable products, according to the European Cluster Collaboration Platform.
- Denmark, Germany, Sweden, and Austria are the countries that successfully applied green production specialization models, as initial findings related to the European Green Deal showcase.
Considering these elements, there is a common trend towards greener manufacturing practices, not merely for cost reduction - which could be an Industry 4.0 indicator in terms of efficiency. This gradual mindset shift speaks about the importance of preserving the environment and how much human activity has increased the carbon footprint. Manufacturers must adapt their tech stacks to meet new demands to reach climate neutrality by 2050 in the European Union.
For starters, more and more manufacturers are focusing on energy monitoring data. Opting to reduce unnecessary energy expenses (i.e., machinery on idle/stand-by mode) is just as important as decreasing environmental emissions.
The Industrial Internet of Things will be a major character in the future of manufacturing over the next decade. Here are some areas in which IIoT will influence:
Predictive maintenance: IoT devices can gather data from equipment, creating models that predict maintenance dates, reducing downtime and increasing efficiency.
Quality control: As we mentioned before, reworking pieces is at a very low spectrum. Using IIoT devices, quality control becomes more accurate, decreasing scrap generation. Simultaneously, we can expect machinery to implement new technologies that allow manufacturers to rework scrap pieces to reduce waste generation.
Supply chain optimization: Factories are currently implementing sensors to track goods moving through the different stages on the shop floor. We can expect more insights on inventory levels - probably through integrations with CRM - and transparency for both manufacturers and consumers regarding delivery times.
Automation: The automation of machinery shall only increase, allowing operators to focus on tasks that require human input and decision-making rather than repetitive, time-consuming tasks.
Data-driven decision-making: From the vast amounts of data extracted by IoT devices, predictive models can be created to analyze production performance. This information impacts how operators and managers make decisions, and we can also expect reports to contain detailed data on machinery performance or suggestions for improvement.
Tips on where to focus the manufacturing tech stack to drive value into production
We would like to conclude this article with takeaway tips on where the focus should be to see a powerful impact on production through the manufacturing tech stack.
Data management
By implementing systems that collect, store, and analyze production data, managers can use that information to back-up decision-making. All this information should be secure and protected against cyber-attacks (especially ransomware).
Consider pay-per-use cloud computing services for companies that want to keep their IT expenses at the lower end of the budget. They reduce the complexity of data analysis as your company doesn’t need to build a cluster of PCs to process data. Manufacturing intelligence solutions like Factbird offer cloud-based access through different devices (PC, mobile, tablet) 24/7, drastically decreasing the need to purchase high-end computers.
Robotics
Robotics can be an interesting take to reduce extra working hours by personnel. In some industries, manufactured goods require special protocols for workers’ safety (i.e., chemicals). By implementing robotics into the critical stages, managers can rest assured the organization is preserving its human capital risk-free and possibly increasing production capacity.
Augmented Reality
This point is linked to the prior one, as augmented reality tools can help workers train without risks. Through VR goggles, operators can learn how to weld, handle power lines, and plenty of other risk-involved tasks without incurring hazards or potential injuries.
Real-Time Monitoring
How many units are lost on average when troubleshooting reiterative stop causes in production lines? Especially when failure happens at random moments, it can be time-consuming, frustrating, and negatively impact production. The information extracted from IoT sensors can be synced with video recordings on each product line through real-time manufacturing intelligence software. Management can replay the conditions that triggered the error cause as often as required to understand what happened or retrieve historical maintenance data to troubleshoot problems. Factbird® View is a perfect example of implementing this kind of procedure.
Real-time monitoring can help us understand how machinery and human capital can be better used to improve production time. Also, manufacturing intelligence software helps operators to address common causes of human errors, allowing them to better-up their performance and boost confidence.
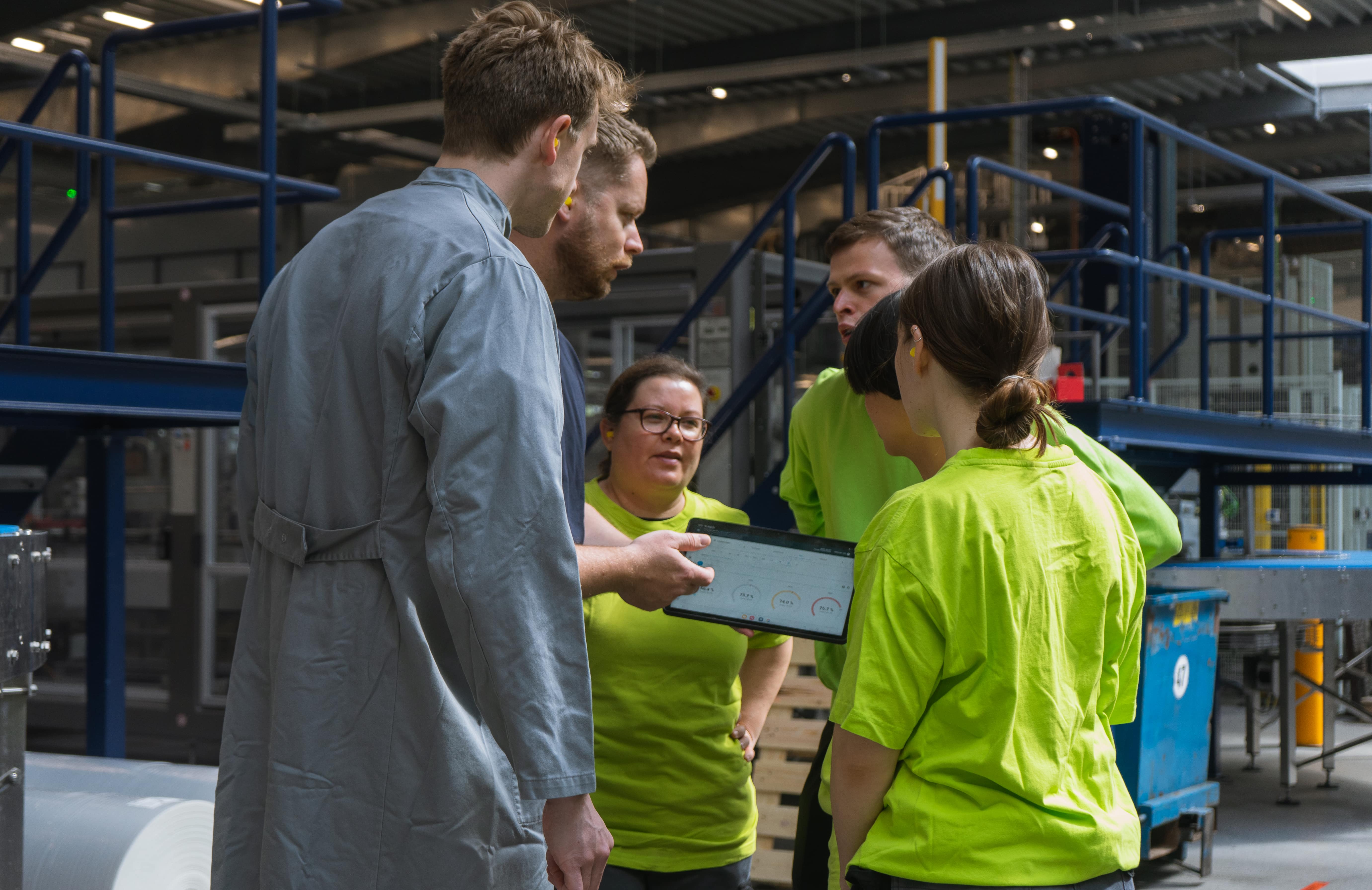
Manufacturing Intelligence: Enhancing Efficiency and Insights with Factbird
Manufacturing intelligence, in the context of the broader manufacturing tech stack, refers to the utilization of advanced software systems and technologies to integrate and analyze manufacturing operations data.
By leveraging technologies such as artificial intelligence, machine learning, IoT (Internet of Things), and cloud computing, manufacturing intelligence empowers manufacturers to gain valuable insights, enhance operational efficiency, and make data-driven decisions.
The integration of manufacturing intelligence within the manufacturing tech stack is pivotal for achieving a comprehensive view of operations. It enables managers, supervisors, and employees to monitor performance, detect issues, and drive continuous improvements. Seamlessly exchanging data between various software solutions, equipment, and departments, the tech stack ensures a seamless flow of information and unlocks the full potential of manufacturing data.
Factbird, a leading provider of manufacturing intelligence, offers a comprehensive solution that seamlessly integrates with various components of the manufacturing tech stack:
- Enterprise Tech (ERP, CRM): Factbird's solution integrates with ERP and CRM systems, enabling seamless data exchange for efficient resource management, order processing, customer interactions, and sales processes.
- Control & Operations (MES, MOM, DCS): Factbird's solution works alongside MES and MOM systems, providing real-time visibility into production processes, facilitating scheduling, resource allocation, and quality control. It can also integrate with Distributed Control Systems (DCS) for centralized control and monitoring of industrial processes.
- Intelligent Devices (Sensors, Production Equipment): Factbird leverages intelligent devices and sensors to capture real-time data from the manufacturing environment, including temperature, pressure, vibration, and machine performance. This enables proactive maintenance, quality control, and optimization of production processes.
By seamlessly integrating with various components of the manufacturing tech stack, Factbird empowers manufacturers to drive operational excellence, streamline processes, and achieve sustainable practices.
Closing Thoughts
As manufacturing companies rethink their tech stacks to keep pace with Industry 4.0 transformation, the integration of IIoT through a manufacturing intelligence solution provides a promising avenue. This approach liberates manufacturers from monolithic systems' constraints, granting them total control and heightened adaptability over the deployed technology. The recognition is growing that broad, horizontal platforms may not fully deliver on their promises, given the depth and complexity required to effect genuine performance enhancements.
Instead, an emerging paradigm is turning to distinct, simple-to-deploy components interconnected via APIs. These can enable precise improvements in manageable stages, extracting immediate value - a key characteristic of these superior components. Specialized IoT solutions are now forming the cornerstone of reimagined technical infrastructures for manufacturers.
Amidst the urgency for swift adaptation, the necessity of risk mitigation is also acknowledged. Questions about replacing the existing MES or whether additional software will yield a positive ROI are considered seriously. To address these, a manufacturing intelligence solution utilizes a data-centric approach to assets, offering a quick, affordable path to improved plant performance-benefits that resonate beyond the factory floor. If required, it's understood that the existing MES systems can be kept operational, preserving their full range of functionalities as manufacturers reshape their tech stacks for the future.