How to take operations to the next level with Manufacturing intelligence
The first annual Manufacturing Intelligence Summit took place on June 20, 2024. Here’s a summary of the insights shared by the expert guests.
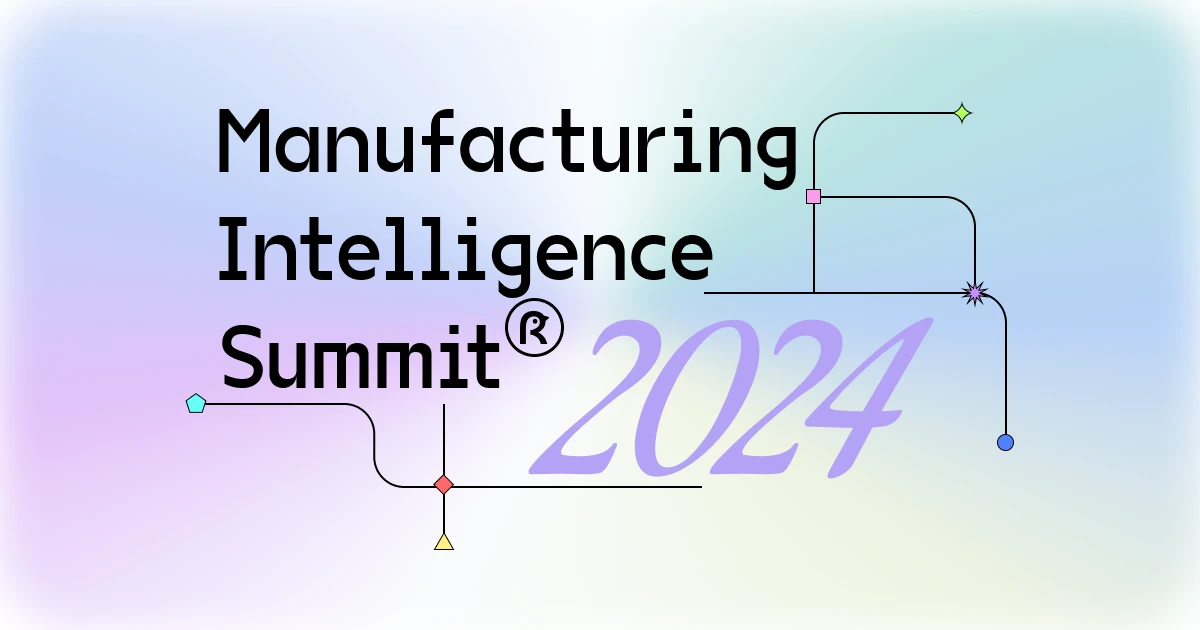
At the Manufacturing Intelligence Summit 2024, we were privileged to have a range of speakers and guests from the manufacturing industry join us.
It’s a testament to how far we have come since being founded in 2016 that we are now driving the agenda with an improvement framework we call Manufacturing Intelligence.
Since working with Royal Unibrew in 2016 at the very beginning of the Factbird journey, giving them visibility into their filling lines and increasing output, we have focused on making it easier to have more good days in production.
At the core of this is data. You need to know the numbers to be able to make better decisions and fulfill the potential of the resources you have. Our co-founder Finn Hunneche, likens this to picking up gold off the factory floor. And that is what Manufacturing Intelligence is helping manufacturers throughout the world achieve every day.
Now let’s dig into what our guests had to say during the first ever Manufacturing Intelligence Summit.
The State of Manufacturing Intelligence
Speaker: Søren Schønnemann, CEO at Factbird
Data is transforming manufacturing by enabling automation and more intelligent decision-making, and the current incarnation of how we are doing this is normally labeled as Industry 4.0.
But despite the long recognition that Industry 4.0 has tremendous advantages, we still face significant challenges to getting there. These challenges include:
- Retention and attraction of employees
- Supply chain disruptions
- Adopting new regulations
- Cyber-security threats
- Integrating new technology
So, is it all bad? No, there are plenty of things to be excited about. Rapid technological change and the adoption of new technologies like IoT, cloud computing, and automation present true value.
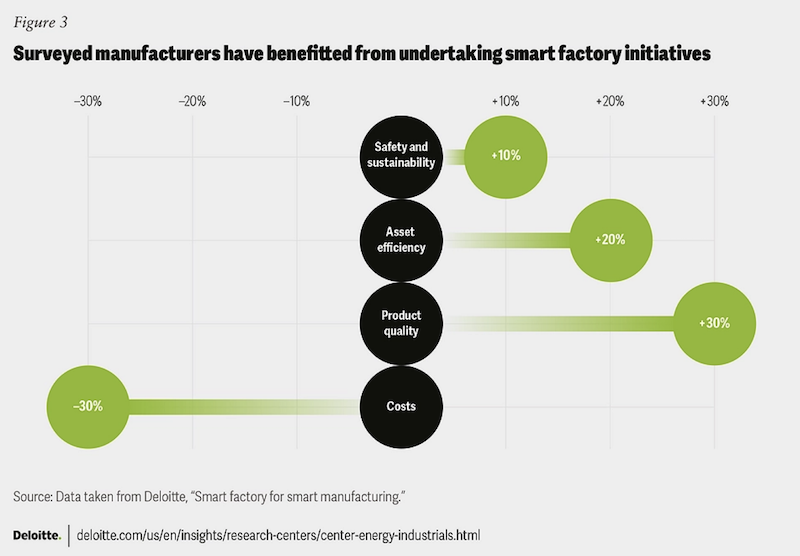
Manufacturers who invest in these technologies to stay competitive. And despite significant upfront costs and integration efforts, adopting new technologies is worth the pain.
At the center of this is Data. Without it, you get nowhere! Data is what can help you overcome these macro and micro challenges, reducing costs and waste, and improving productivity.
We call the use of data to optimize production Manufacturing intelligence, and we define it as having three parts.
Capture: Manufacturing intelligence provides real-time visibility into production processes by integrating data from various sources.
Understand: Once data is captured, we need to analyze it. Analytics need to happen on the stop causes and other key KPIs in a format which is easily understandable and digestible for anyone to understand.
Action: Good data and analysis helps you to make the right decisions and reap the benefits. The captured data, which you now fully understand, needs to be actionable. Without the ability to act on the insights, what are the benefits?
Lastly, the process of capturing data, understanding data, and acting on data cannot be a one off exercise. This process needs to happen in loops where data is taken, measured, and standardized for continuous learning and improvements in manufacturing processes. This is supported by lean practices, and is at the core of manufacturing intelligence.
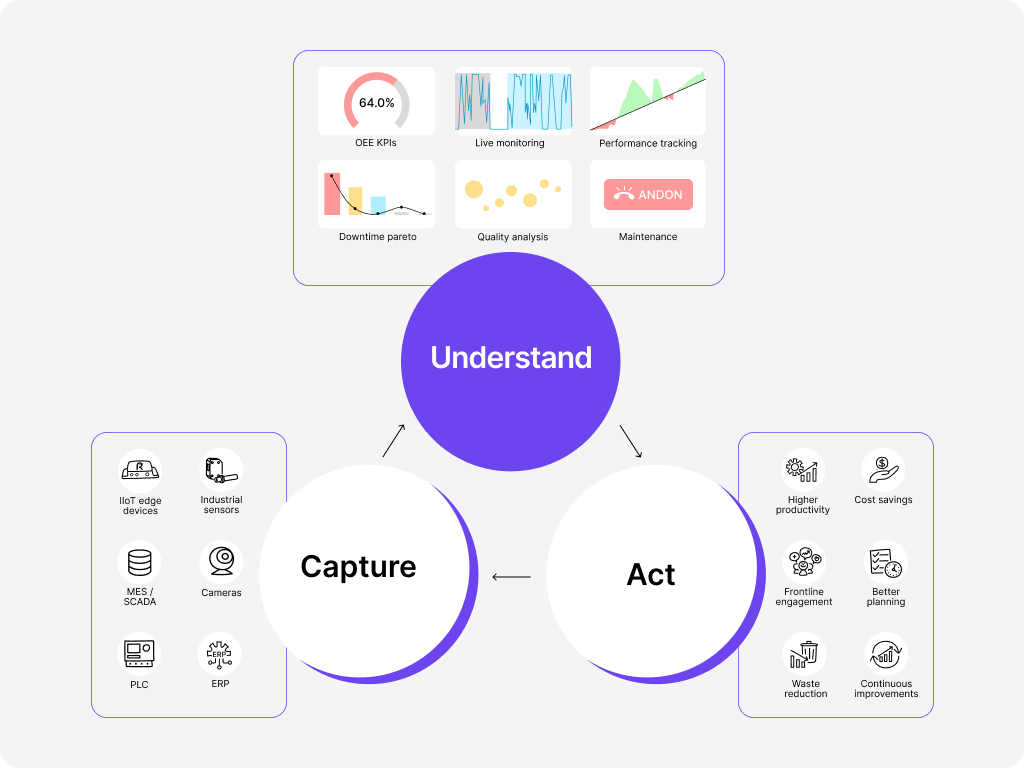
So what is the conclusion?
Well, the benefits of intelligent manufacturing are clear. You can gain a lot from getting more out of your existing equipment and enabling your people, but you have to capture the data, understand the data and act on the data.
How to succeed in Food and Bev Manufacturing in 2024
Speaker: Lance Olmsted, Manufacturing Expert
Lance Olmsted, CEO of MEMCO and former Senior Vice President for RedZone, highlighted several challenges faced by the industry, including difficulties in attracting and retaining talent, underinvestment in capital, and understaffed teams. These factors have collectively led to a productivity drag and increased manufacturing costs. Additionally, higher input costs and low unemployment rates further pressure industry leaders to reduce costs while maintaining adequate staffing levels.
The high cost of employee turnover makes these challenges critical, with turnover expenses amounting to about 35% of an employee's annual salary. This not only incurs direct financial costs but also affects team cohesion and productivity. According to a recent Deloitte study, 45% of manufacturing executives are turning away new business due to fears of being unable to meet demand, underscoring the urgency of addressing staffing challenges.
To tackle these issues, Lance emphasized a multifaceted approach to improve workforce engagement and retention. He suggested creating a stronger sense of purpose among employees, aligning their performance with real-time, measurable KPIs, and ensuring departmental goals are cohesive. By fostering a collaborative environment, manufacturers can enhance employee satisfaction and productivity.
Lance strongly advocated for digital solutions, recommending that manufacturers move away from paper-based systems and, for example, set up projects to implement digital solutions within 90 days.
Lance shared examples of successful implementations of these strategies. One of the cases was a pet food manufacturer that saw an 18% increase in throughput by improving collaboration and real-time response capabilities among factory floor teams.
Lance Olmsted's insights underscore the importance of embracing technology and addressing workforce challenges to drive productivity and growth in the food and beverage industry. His practical examples and strategic recommendations provide valuable guidance for industry leaders looking to navigate these complex issues.
Manufacturing in the Digital Age: Trends and Challenges
Panel discussion
The final segment of the Manufacturing Intelligence Summit was a panel discussion involving experts from different areas of the manufacturing industry.
The three panelists discussion the topic of “Manufacturing in the Digital Age: Trends and Challenges” were:
- Mikkel Rauff Simonsen: Senior Manager of Plant Optimization at Danish Crown, one of the world's largest exporters and one of Europe's largest producers of pork.
- Kenneth Ranzau: Key account management for OMRON Industrial Automation Europe, a large equipment manufacturer of Industrial Automation Solutions.
- Mats Ekenstam: CEO and cofounder at Boards on Fire, a provider of digital tools for Lean, daily management, and continuous improvement.
Here are the questions they were asked with brief summaries of their replies.
What is digitalization in manufacturing from your perspective?
Kenneth: It’s about transforming production data into value.
Mikkel: It’s also about taking analogue processes and transforming them into digital formats. The other part of it is that it’s a paradigm change in the industry, and you need to remember the people that are part of the big culture change.
Mats: Our company Boards on Fire is an example of data and digitalisation. The local municipality had whiteboards that they wanted to digitize, and that's what the founders built.
What is the current state of digitalization in manufacturing? What technologies are driving change?
Mikkel: Robots and optimization were initially driving digitalization to reduce labor costs. Now we are also talking about AI, predictive maintenance, and IoT solutions. Integration is a big part of it, and how we use this data.
Kenneth: A question that we often get out in the field is how do we collect data from all of our existing lines and combine that with our new lines. As Mikkels says, there are 20 systems handling the data and it’s about how we integrate them. It’s also about helping the employees improve their performance and working together as a team. That is probably the hardest part of using digitalisation.
Mats: We have a customer called Systemair, and they were measuring OEE, but they forgot the people. So Boards on Fire helped management communicate upwards and downwards, and use the data in tandem with helping people.
How do you see the discrepancy between the shop-floor and management talking about things like AI?
Mikkel: A lot of people AI can fix everything, but we need to understand it and use it in the right way. I would really like to use it in predictive maintenance, analyzing patterns, and historical analysis. I think AI can help us understand all of the data we have.
Kenneth: To use AI we need to start collecting the data and being capable of getting the right data.
Mats: Mikkel mentioned that at Danish Crown they have over 50 languages that people use. So I think AI would be valuable in helping people use their native language. We are also working with something where people can take a photo of an issue and AI assists with describing the issue based on the photo.
What are the biggest benefits of digitalization within manufacturing?
Mats: It’s about making things better, faster, more inclusive, and making the company more profit.
Kenneth: I think it’s also about driving society to a better place. We need to use data to reduce waste and be more productive. This is something that OMRON is trying to do, getting a better society through our technology.
Mikkel: Of course I need to say reduce costs, raise efficiency and productivity as well. But for me it’s also about what data can do for the people, how it can combine people in new ways. For example, the technical department and production will point fingers at each other (when a problem arises), and now we can use data to help us. It’s not your fault, it’s our issue and we have common goals.
What about pushback to these new technologies, how can that be handled?
Mikkel: Get people involved early.
Mats: I totally agree that it comes down to the people and understanding why. And also if you start slow, then work from there, then it will work.
Kenneth: I agree, and I think also it’s not only the employees and operators seeing everything, it’s also about giving them insights into what they can actually change. Maybe OEE is something more for management, for example.
What are the biggest challenges manufacturers face when digitizing operations?
Mikkel: We say we want to be data-driven, we say we want to work with data. But do we actually know what the data is? Do we know what a pareto diagram is or OEE? We need to educate and train people in these. It’s also about how we can combine all of the systems that are coming up through digitalization.
Kenneth: I think it’s about investments on collecting all the data from all the different machines that you have. The management thinks it’s a huge investment because they need to change their MES system etc. and train the employees. But if you always have this issue that it’s a huge investment, you will never start. Using something like the Factbird DUO you can start collecting data easily and start using it. After you have the knowledge how to use it, you can scale it up.
Mats: Manufacturing companies that I visit have all the high tech machinery and robots and everything, but they still lack the information from the people.
How do you see digitalization in manufacturing evolving over the next five years?
Kenneth: I think many are still on the journey on how to use the data and how to get the data.
Mikkel: Big companies are going ahead and testing some things. But there will still be a lot of pushing for real-time monitoring systems, IoT systems. I think the data analytics part of it will have evolved massively.
Mats: If we go back four years, we had a pandemic. And if we go four or five years ahead, maybe there will be another one. We have to prepare for the future.
What advice would you give to companies just beginning their digitalization journey?
Mikkel: Knowledge sharing and networking is important. You can gain knowledge from experts, not only in the same industries and from other countries. You should not do everything by yourself. Seek the inspiration.
Kenneth: It’s important to find a way of starting data analytics.
Mats: To be curious is important, always be curious. And listen to the people. We forget this so much when we are focused only on the data.
Watch the full summit for more insights
Thanks for your interest in the first annual Manufacturing Intelligence Summit! We hope you gained some valuable insights from it. If you would like to stay informed about future events like this from Factbird, you can sign up to our newsletter to stay in the loop.