Factbird Forward panel Q&A session
Watch Factbird Forward's panel of experts tackling audience questions, sharing their perspectives on the current landscape and the future of manufacturing.
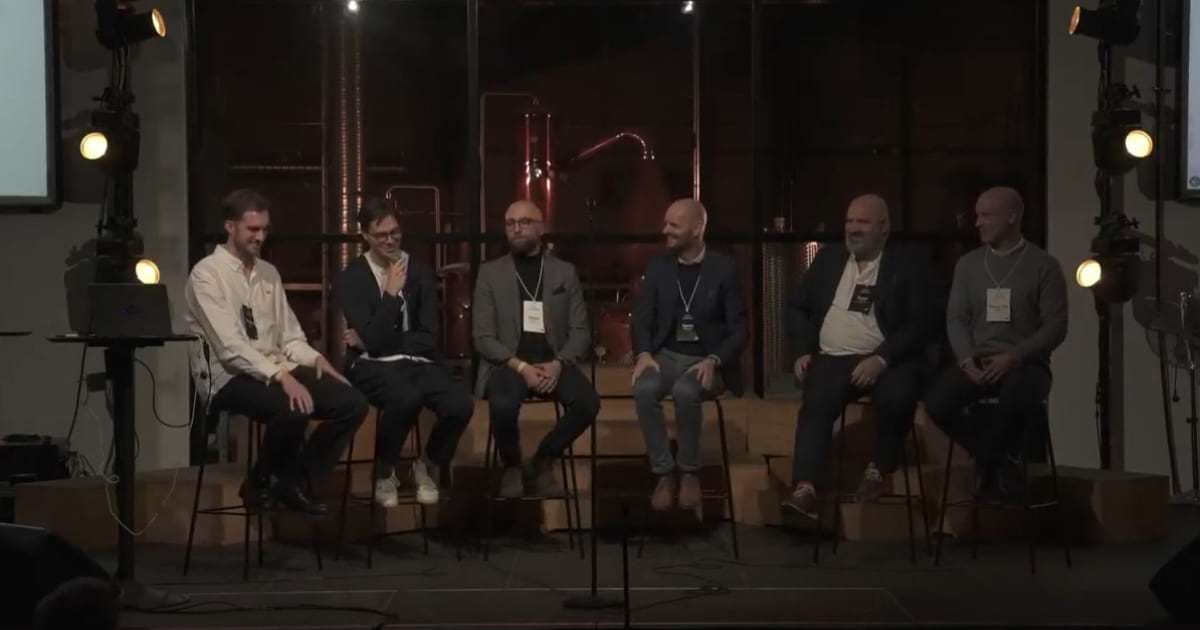
After an insightful presentation from Trevor Hewson, we moved on to the final segment of Factbird Forward, a panel discussion involving experts from different areas of the manufacturing industry. We discussed the current state of the industry and the future of Manufacturing Intelligence. The group took questions from the audience, both on-site and online.
For the panel discussion and Q&A session, we had the pleasure of conversing with:
- Martin Ole Madsen: Manager - Operations Excellence SVR EUR at Danfoss, a Danish multinational manufacturer of hydraulic, temperature control, and power solutions.
- Mikkel Rauff Simonsen: Senior Manager of Plant Optimization at Danish Crown, the largest meat-processing company in Europe and one of the world's leading exporters of pork and beef.
- Trevor Hewson: Leveraging over 30 years of expertise in the manufacturing sector, Trevor is a lecturer in Food Manufacturing at the University of Lincoln.
Here are the highlights of the Q&A session: the questions they were asked with brief summaries of their replies.
So I'll actually start with a question that was sent in from an existing customer. And I guess this one will be directed towards you, Nikolaj and you, Søren. They were sharing that they have been a customer for just over 12 months and they're very excited at all these future looking developments that were out. And it might be a concern or a thought shared by a lot of people in this room that the current system, as good as is, it's not perfect. And there are features that people are requesting for our base operations. And so this particular customer was saying: okay, all of this seems super exciting, but what about the things that we're requesting for the existing system? Is that still a priority?
Nikolaj: Definitely still a priority. I think, just to give you some clarification, the way we have organized ourselves within Factbird, we have designated development teams for each of the three applications that I just mentioned, which means that we're still heavily invested in improving the existing product and adding more features because we know that that's still a journey. But we also had the opportunity to add additional resources and make investment to make the second and the third application possible as well. I don't know if you have anything to add?
Søren: I think you're you're spot on, Nikolaj. And, and I think it was mentioned in the presentation as well, that's the beauty of a software as a service, It's a relationship that it keeps adding and keeps giving. So, yeah, without necessarily the price going up dramatically. Right?
And this is for you, Mikkel. They're asking: you've implemented Factbird on a lot of sites. What is your advice to get adaptation for people actually using it and implementing it in everyday life?
Mikkel: Yeah, that's a good question. I think, what we have focused a lot on is to turn a little bit around instead of focus on the operations, what we need from there, try to focus on, on the shop floor, on the value created for, for the operators down there. So we have failed. Also, when we started the implementation, we failed big, to be honest. And that is what we have learned from. So we we re-scoped ourselves to start focus on, okay, we need to have this to live on a daily basis. We need this to be driven by the operators, not driven by us, but driven on the daily business on how they can support their daily business. So try to re-scope in that format to say, how can we create value for you? And, as we talked about OEE a lot, they ask the question almost every day. "What is OEE? We don't understand it". So try to break it down on a on another level to say, "Okay, when we just talking about the downtime, how can you work on improving the downtime on a daily basis when we're talking about the changeovers or can you do to to improve your change?" So it was also for the micro stops. How can we balance out the line so they can start to see, "Okay, if we do this, how do we create value for them?" Have a better pay as well. Also, a better production, start to focus on that. When we turn that around and make our step-by-step procedure instead of implementing everything at once. Because as you can see today, Factbird is delivering a lot of different solutions into the whole system, but focused on where to start and create value step-by-step. I think that is why we have had success, and we see the utilization of Factbird and the data as well.
Søren: You're discussing or sharing your story as a big company rolling out and I think that's valuable for big companies as it is valuable for small companies, making sure that we activate the operators on the shop floor, making sure that they see the technology as a partner and not as a piece of technology that will work against them. I've had and heard many stories, also tonight, about the entry point of introducing new technology was perceived as something that is going to monitor or work against them. But once embraced and start to be leveraged and used, it can actually be an amplifier of doing a better job, doing more quality job, which essentially everyone wants to do. So I think the successful implementation is about making sure that the voice of the operator is being heard. Those are the two points driver. And making sure that it's activated from grounds ops, it doesn't become a top down project and another IT project. But more so something that is enforced in order to make operators the heroes of the day.
Mikkel: Just, just to come into that analysis, because I fully agree on that. But I also think if we look at the market now and all of that in the businesses, we look at a place where we have a lot of different generations on the market, we have generations who are not born with technology, and we have generations who are born with technology from an early age. So how to to fit them all? I think that's just the toughest thing. And this is still something we are struggling with, everyday, to be honest, because we have one super operator who is used to apps and smartphones and everything. He's just connecting immediately. And then we have one guy still using, an old Sony Ericsson Nokia. He's never touched any screen before. So how to limit that out in the culture transformation? That is the the real challenge for us every day. Still, I think, it will be for many years.
And Trevor, just in in your presentation I think these characters that we're hearing about could be considered the blockers to change, the blockers to progress in that continuous improvement journey. Do you have any tips on how you can get these people on board or how you could, you know, get them onside?
Trevor: Yeah, I think you have to use them, get them to actually do the tasks themselves but allow them to do it. You know, historically we've stopped them doing it. We stopped them taking the benefit from there. Let them make mistakes. They will make mistakes. Embrace those mistakes. Embrace that as part of the process because they've got to learn. If they don't learn and are not given the opportunity, they then become even stronger blockers. They become more and more resistant. Every time we try and give people the opportunity to improve and we stop them from doing that, they become more and more resistant. So you've got to allow them access to it. And yes, they will make mistakes. They'll also make some great improvements. And one of the things we used to do, we used to get anybody off the shop floor, and they used to come in to the monthly review meeting with the regional director to present what they'd done. And, you know, it was very nerve wracking for them. They'd go and can be sort of in amongst people they wouldn't normally be with, but it generated a real sort of buzz. They'd go back and tell the mate "You'll never guess what I've just been doing. I've been stuck in the board room. We had pizza afterwards as well. It was a cracking session". And it breaks down those barriers, and those layers upon layers of resistance melt away very quickly. And once we did that, in the example I gave, that's when the real churn of improvement started. Giving people the opportunity.
The same question towards you, Martin, actually, because you're not in the same company as Mikkel. Maybe you have different views on it?
Martin: I think that one thing that is very much in common, whether you're a small company or a big company, whether you're in food or whether you're in industrial engineering, is that you need to assess your maturity level before going into installations of systems, it could be Factbird or others. Because if you're talking maybe to smaller companies, they are not afraid of the system or, doing the small incremental stuff, but still they need to be aware of where are we at this point? Because I can see, from Danfoss perspective, we are quite high in maturity level. We're not perfect at all. But but we are quite high. Does that mean we are getting better than others in a faster pace? I don't think. It's meaning that we have access to a lot of data that maybe the smaller companies don't have, and we need to respect that, but also we need to have people on board on the bus driving that journey. Also echoing what you said, at the beginning, actually, I drove the first pilot in Danfoss and it was only on one single machine in one area. And what we actually did was presenting it to the CEO of the segment. And he was like, he actually stopped me presenting, and he was like, "Get that app on my phone, and I will try to watch all your lines while you keep getting lines into the system". So that was, again, igniting a fire or at least some spirit in people that actually what you're doing is creating differences and you're becoming better. And that's pretty much good for everybody in the company.
It's my impression that the solution is fundamentally, galvanically separated from the OT network. But, I assume the more that gets integrated in the shop floor systems, the more you will touch upon regulations like NIST2, Cybersecurity Act, IEC 62443 and all those standards. Could you put some words on your strategy about that?
Søren: Definitely. Part of, on at least part of the roadmap is addressing needs too specifically, because as you were alluding to, we're slowly maybe entering an area where we are not a noninvasive, solution anymore, but actually affecting what's going on on the shop floor. And I think we need to be very delicate in how we maneuver it, because as of right now, we simply provide information and guide. But we don't tell the machine how to do its job. We instruct people on how they can perform it. The strategy is to still steer away from OT, that we don't become a part of actually telling the machine what to do, but have the approach of the human in the loop. And I think we, at least at Factbird, believe that people will play an essential role in running factories for many, many years. I think some industry leading companies may have fully automated lines where no human touch the finished product from raw materials all the way to the end, but it's a selected few. And there's still a lot of companies out there that we can help with our solution where we equip the individual to make sure that they know how to do their job, and provide value. So, yeah, overall strategy is still to steer, steer outside of OT, if that makes sense.
First, thanks for giving us this easy way to look at our data in the factory. So, really, really helpful for us on the shop floor. And I can really relate to the new features. Can you maybe help describing a little bit more on the CI part and, you know, it's easy now to see how our machines run, but, you know, looking into lean and CI, flow is really king for us. So how do you see Factbird can support us looking at the flow and for instance, lead time of our batches and our products, maybe passing through many machines?
Nikolaj: I think, first of all, the way we're thinking about it and trying to address it is to make, you know, proven tools from Lean and Six Sigma readily available so that you have a standard format or standard process for how you do your root cause analysis. So if we can introduce the tool within Factbird and let you easily navigate to the process of identifying your root cause, we'll make that simpler. So when you are looking at all your stops, causes, and try to address the biggest one, then we can help you guide towards getting to the root cause. So we are thinking about making those tools readily available, easy to use, but that you also have the history of it, because often what happens is that you will do a session on the shop floor, it's left in an Excel spreadsheet or on a whiteboard, and then you move on to the next one and you maybe forgot what you did last time. But here, linking it to the history, so you can go back. In terms of establishing flow and understanding lead time, I think that calls, at least, for the Factbird solution for a broader line concept than what we currently offer. It's something that we're investigating so we not only track the bottleneck, but, in the future, can actually track the entire line. It's not part of the roadmap for next year. But definitely on the drawing boards for the future.
I think, Martin and Mikkel, I'd be quite curious to hear about how the implementation of Factbird on this topic has adapted to the continuous improvement efforts across your two companies as to how it's changed, how it's had that impact there?
Martin: So you want to know about the the impact that the system has done in our case. Well, as I said before, we started with one single pilot on one machinery, and now we are across the whole factory, and also other factories in Europe and the US. But it has been a journey for us also to develop together with you guys. So, for instance, we are very much into ESG and how we collect data on our energy consumption so that we have developed together with you. Now I think we have, it's a guess, but I think we have maybe the most monitored factory in Denmark towards having the view of energy consumption. And we see quite some heavy paybacks on our investment there. It's something we do along the way, that we develop new things. And also utilizing things that you guys develop to us. So, I would not call it an official partnership, but it's something that we do together. Whenever we asked you guys to develop something, you never say no. I never, I never heard it. I think the worst answer I can get is "we put it on our roadmap". That's the worst thing I ever heard. Because usually every time you say something. "Yeah, we can try to create that". And we will have a consultant from you guys calling us, or texting us maybe a week after with a solution. If you don't have it in place, you simply develop. And that's also been a key driver for us to really evolve in what we do with you guys.
Mikkel: To support you as well, Martin, I haven't heard "roadmap" but I've heard "backlog" for a long time. But super service and super support. We always find a solution, one way or the other. So that's also a great service to get. But I think the most, what really kicked in for us was when we started to do it. We have a civil war between our engineers, technicians and the floors, the guys on the floor. They would never agree on the stop causes because this was a a stomach gut, to be honest. So now we got the the real time data. We got some data, some facts that you actually could use. So now we can get the data immediately, instead of using time on typing into Excel. First, we had the figures maybe next day, or we will see, so we will have it tomorrow. Now we have it in real time. All the board meetings are prepared. The data is there. We can discuss if it's valid or not. It depends on the structure, but we can follow up on that. Then, we're starting to have a journey, starting to focus on the valid data, and afterwards we can start to trust the data. When we can start to trust the data, we see the real impact. I remember the first, one of the first roll outs with data, just to make a short story. We had, the whole factory had some issues with the fall for a long time, and the management weren't here for them, you can't prove it. And, procurement, you can't get a new fall, it's too expensive. We got Factbird on the line, and after two months, we could prove we had a loss on the file for 1.3 million a year. We showed that to procurement, and I said well, what would a more thick layer of falls cost? It would cost 100,000. I think the business case is there. We changed the file and we didn't have one break at the fall for four weeks in a row. I think that's a good case. Where employers really had the drive to show something for the management.
When you talk about the continuous improvement, when we train our staff we want to have all the skills. And in the coming training matrix you have, we can see the skills. So we have a lot of skills on each employee. When we shift him over from a mixing area to a packing area, we lose the skills. Will the new training matrix then see if I said "on this machine I need five people to have the skills". So the guy I take from one department to another when his skills is going up, it will show on Factbird "Now I need to train, maybe three people into the new skills we are having less of"?
Nikolaj: Really good question. I think in the initial version, the one you just saw, that will not be possible. But for us, it's making sure that these three applications work together, to better help you guys out and what we're envisioning for Production Insights is making a solution where you can adjust and plan out how you're manning your different shifts and your different equipment. And a straightforward idea here is exactly what you are addressing. And what we have on the drawing board is to make sure that that interacts with the skills matrix. So you see the implications of when I'm doing my manning and the planning of my manning, I can see that I have the sufficient capabilities at the different shifts. And if I remove operator A and B and put them to the nightshift, all of a sudden I'm vulnerable during the day because I have no one to operate equipment A. That's definitely on the roadmap, to be developed.
Regarding the CI tools such as full cost analysis and action plans, will these be available to extract as supporting evidence towards our own, already standardized internal forms? And, will the upcoming roadmap that Factbird are currently working on regarding development and new tools, including timeline, be ready and available for us to share with others within our businesses?
Nikolaj: Regarding CI tools such as full cost analysis and action plans, will they be available for extracting to supporting evidence for existing, already owned systems? Yeah, definitely. I don't think I can promise a direct integration to already existing, but extracting them from the system, most definitely. And then there was a question about the roadmap and the timeline? Yes. Yeah, so everything I demoed here tonight will be available in January. As of next year. And then we'll continuously add to the functionality and build new capabilities throughout next year. That will come... We haven't got the exact launch dates yet, but summer next year and then end or beginning of 26, end of 25 or beginning of 26.
So, Nikolaj, you were talking about LLM models that you want to implement later on. Have you have any thoughts? And discussed any investments in Gen AI to move forward, or do you expect that to be done from partners?
Nikolaj: I don't see us as an AI company. I don't think we're the best at that. I think others have better skills, better capabilities to develop that. But for us, it's about applying that technology as a tool to empower our product and make that better. And right now, we are experimenting with different models, whether that's Claude or ChatGPT from OpenAI. But we'll select the one that performs the best and the one that gives us the best results, and not rely on sort of internal development of models.
Trevor, there's a question regarding industry 3.0, 4.0. There's talks about 5.0. When educating the new generation of frontline workers, what are you focusing on?
Trevor: I think because it's changing so rapidly, we've got to keep scanning the horizon and looking at what is next. So yes, 4.0 is is upon us. Some business are still not even at 3.0 properly yet. And we've got to acknowledge them. We've got to make sure that you pull the chain upwards as well as scan the horizon and see what's coming next. So I think the answer to that is everything, really. But we've got to be looking for that. We are trying to build in industry 4.0, but it will rapidly come to pass that. It's happening at a pace that we've not seen for a long, long time, and you've got to keep right at the forefront of that. And it's difficult. You've got to make sure that the information that you give is up to date. Today is not a date tomorrow. The gentleman down there mentioned AI. AI is evolving so rapidly we're struggling to keep pace with it as educators. I am so amazed that people are keeping pace with it in their industry as well. All those things are changing, but what you can't do is stand still. And so you've got to keep looking at how that leverage happens and how you get access to it.
Martin, you were speaking about Smart Factory and next gen technologies. Where does Factbird fit in there? And where is your focus on adding new technologies, and what are you considering when adding technologies?
Martin: I think with the reference in the automation pyramid. So, we also heard that they don't really focus on being the number one system on top, controlling everything where we have the ERP and the scatter and the mist system. I see Factbird as a system just beneath that one. So you have the control from the PLC on top doing smart things and integrating with surrounding systems. And also, if you look at the automation pyramid, the lower you get, the more room they have to play in the pyramid, right? So I think Factbird has now proven for quite a long time that they are innovative and they can really take up that space in the bottom of the pyramid, enabling new things for us. So when buying new equipment, smart technologies, we need to be aware that Factbird is there to grab all those things. Then we can talk about with the PLC beyond the machinery, after the next ten years. That's a question. But at least we should have the system to give us that data, at least in the meantime. And I'm sure that within ten years from now, you will just have a new solution so we can keep having the data subtracted. Also echoing a bit the last question about the AI and the industry 5.0, I think we should maybe just pause a bit and ask ourselves, are we done doing industry 4.0 really? Because there was a lot in that circle of knowledge. And one thing that not many people are aware of is that robotics and AI have two things in common. The terms are more than 50 years old. We have known them for more than 50 years. And look at just 10 years ago. Where are we then with AI? Not very far. Right? So I think they are still part of the industry 4.0. But let's finish that off before we know what should be in industry 5.0. Of course, I don't have the answer here because then I would be a genius, but yeah, that's my way of looking at the new investment and the industrial revolution.
Thank you
A huge thank you to our amazing customers, inspiring speakers, and everyone who joined us—whether in person or online—for this unforgettable event. Your insights, input, and support are the driving force behind our mission to accelerate manufacturers’ digital transformation. If you would like to stay informed about future events like this from Factbird, you can sign up to our newsletter to stay in the loop.