Unveiling Factbird's product vision for 2025 and beyond
Explore Factbird’s new apps for manufacturers: Production Insights, Connected Operations, and Knowledge Excellence.
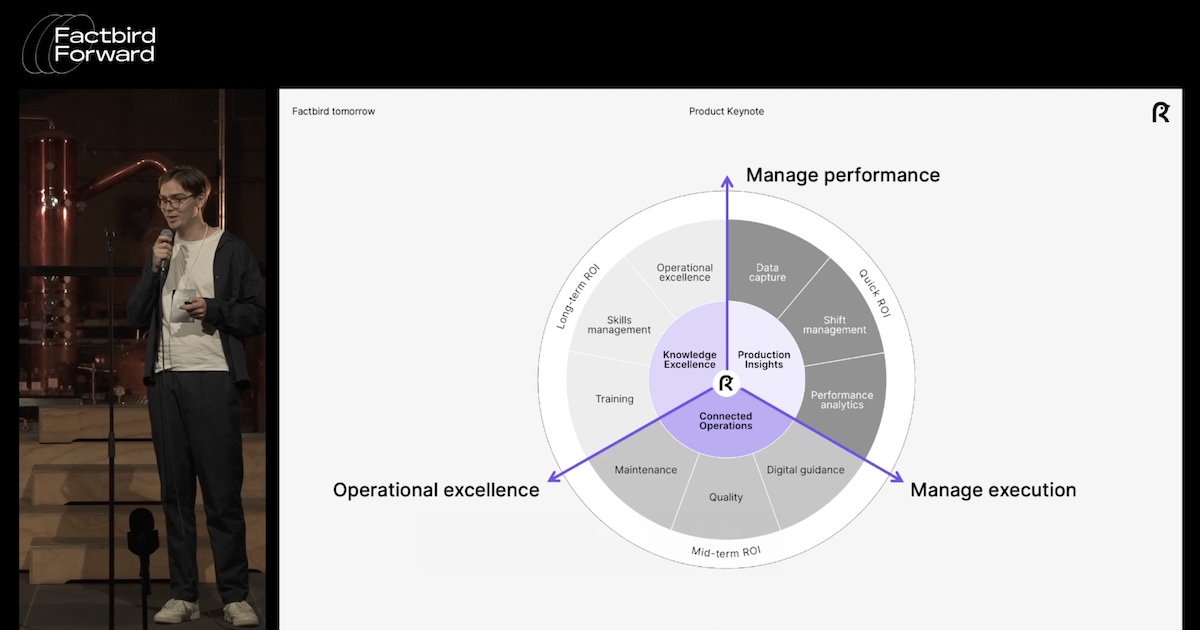
At Factbird Forward 2024, Nikolaj Arslev unveiled a first look at Factbird’s new product launches and improvements coming in 2025 and beyond.
We are expanding our technology stack to better serve our manufacturers, offering improved production insights and an array of new capabilities in the connected operations and knowledge excellence spaces.
The following is a summary of what Nikolaj had to say at the event.
Customer-driven innovation
We've been developing solutions for 7 or 8 years now. Reiterating, refining, and developing, all with the promise of delivering a plug-and-play solution that can link your production equipment to the cloud and provide you with data to make informed decisions that drive improvements and eliminate waste.
And we're still on that mission. For the past two years or so, we have been experimenting with adding new features to our platform, all based on input from you guys.
You might be familiar with existing Factbird tools like preventive maintenance, Andon, condition monitoring, manual counters, and action plans. All of these came from your ideas.
But when we started 2024, we knew that we had to change. We still want to be an outside-in development organization, but we need to take a more holistic approach.
At Factbird, everything we do revolves around the factory and the shop floor. And we need to understand and help you guys get the job done, especially when we're considering the interaction between plant managers, team leaders, and operators.
And we still need to provide this fit-for-purpose solution that's simple to use and easy to get value from.
Three dimensions of value
We are tackling this challenge by addressing your “jobs to be done” in three dimensions.
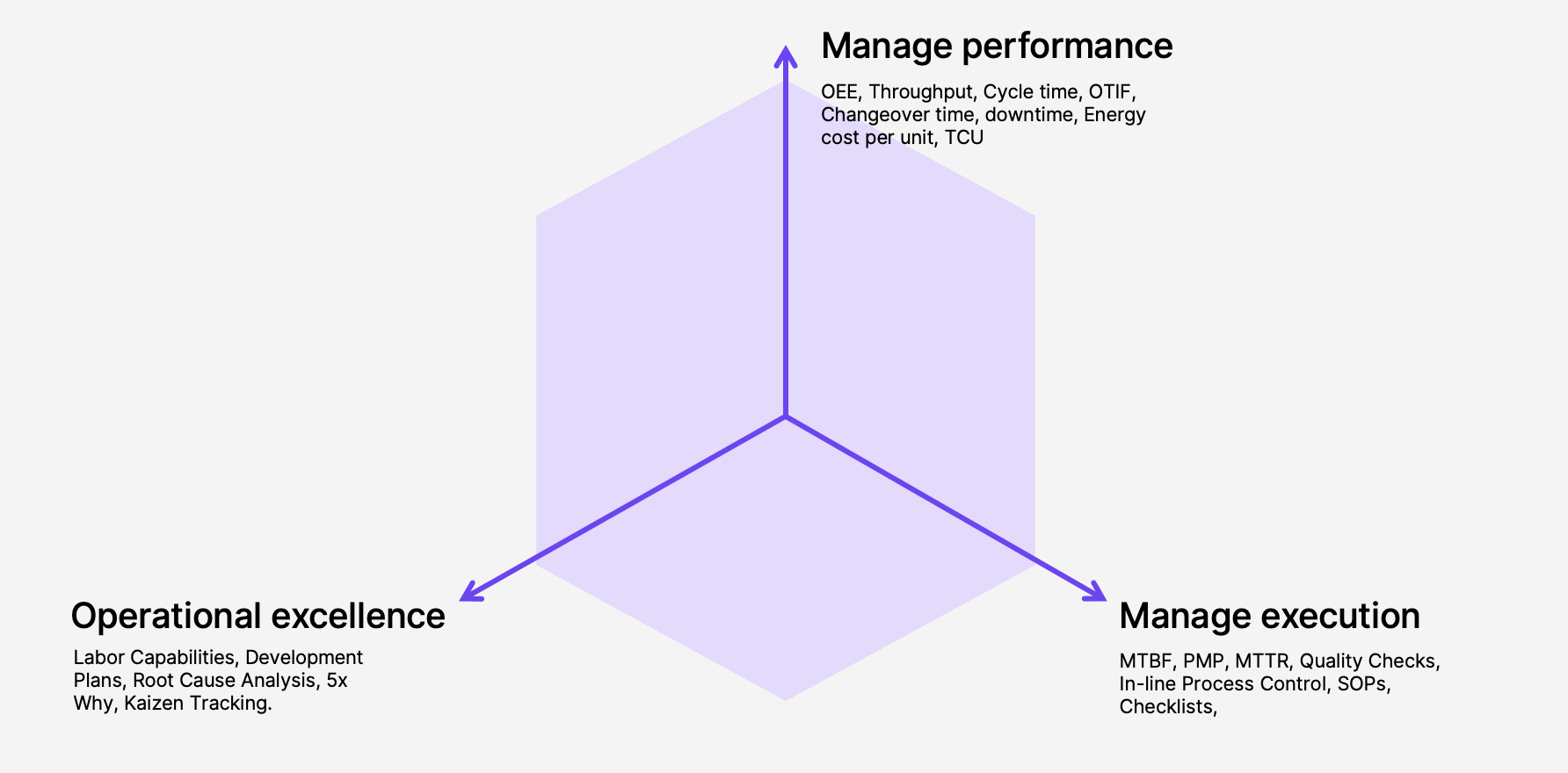
Dimension 1: Manage performance
The first dimension is what we're currently doing, which is helping you guys manage performance.
Tracking data and understanding your downtime to drive informed decisions on how you can make improvements. Understanding how your OEE is developing and trending over time. Setting targets and understanding why we are not hitting them, diving into the gaps, and making the right decisions on how we can improve.
We will continue down this path, but we are adding two more dimensions to our product.
Dimension 2: Manage execution
We've been focused on what is happening with the production line. And now we want to expand upon that scope. So we'd like to focus on the shop floor and all the activities that are carried out around a production line
So whether that is quality checks, inline process controls, or maintenance tasks, whether it's preventive or reactive. We need to be able to assist you with all those activities.
Dimension 3: Operational excellence
Thirdly, every production company is on a journey towards operational excellence, whether they have just begun or have been working on it for many, many years.
We want to be part of that journey. When we think about operational excellence here at Factbird, it's about improving people and improving processes. We need to make sure that people are properly trained and that we equip them with the capabilities to carry out the jobs that we're asking them to do. And we need to be able to manage that in a simple way.
Then we also need to consider processes, because not all processes are easy to understand and carry out. We need to continuously improve upon the way we do things. This will make it easier for our employees to perform their tasks.
Factbird as three applications
The way we will support your “jobs to be done” is by introducing three applications: Production Insights, Connected operations, and Knowledge excellence.
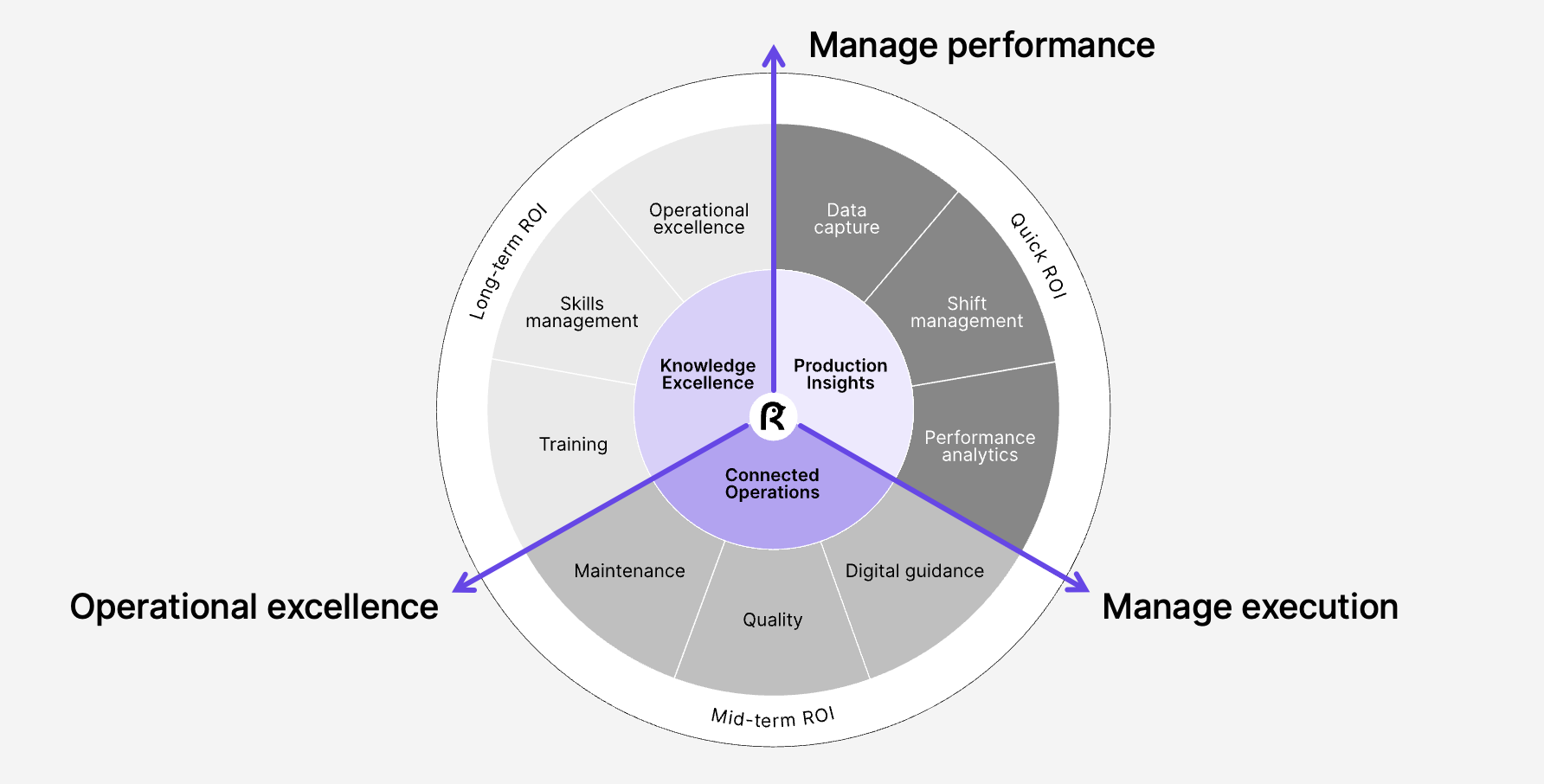
Production Insights
When you think about production insights, I want you to think about more or less all the features that you know in Factbird today.
When we address the product, when we think about the product, it has three main capabilities: it's data capturing, it's shift management, and then performance analytics.
And it's especially in the performance analytics part where we believe that we can do a better job.
We will provide you with more automated analytics tools where you don't have to go in and look for the data or export it out of the Factbird system, tamper with it in Excel, Tableau, Power BI, or tools like that, but simply do it within our system.
Preview: Factory Overview
One of the features that we're introducing in January 2025 is what we call Factory Overview.
Here’s an example of a medium-sized company known as Factbird Brewery, where you can see that production lines exist both in Europe and North America. Here you have the consolidated view of the performance of all those assets within the two regions.
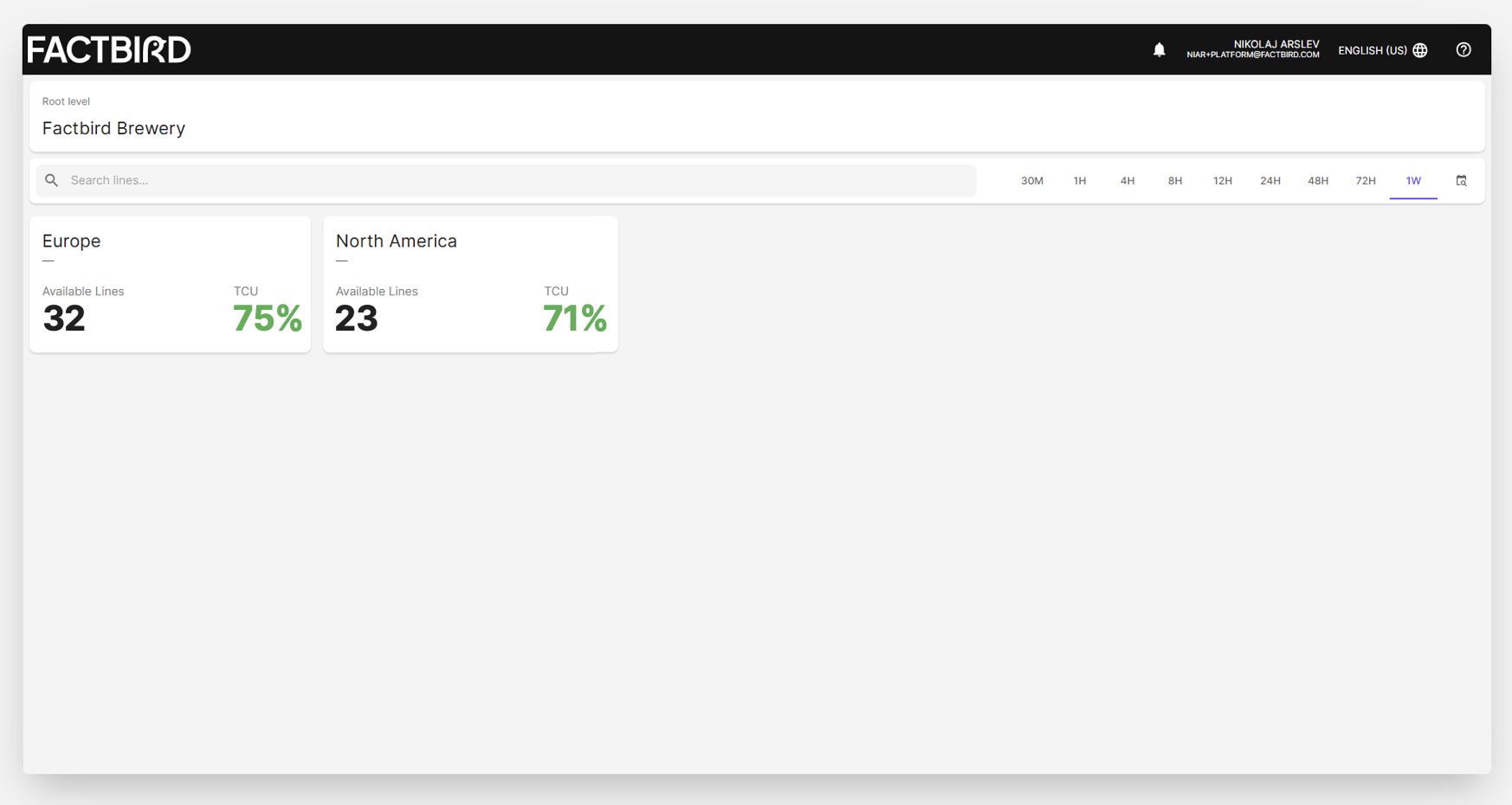
You can then navigate down to Europe and see how you're organized. Here we have sites in Denmark, Sweden, and Norway.
And once again, you can see the consolidated performance of those countries.

And then we dive down to the most granular level, which is the shop floor and the production line. This provides you with a simple overview of all the assets that are running their status.
You can see where you should focus more, where you should put your attention, and where the biggest need is currently.
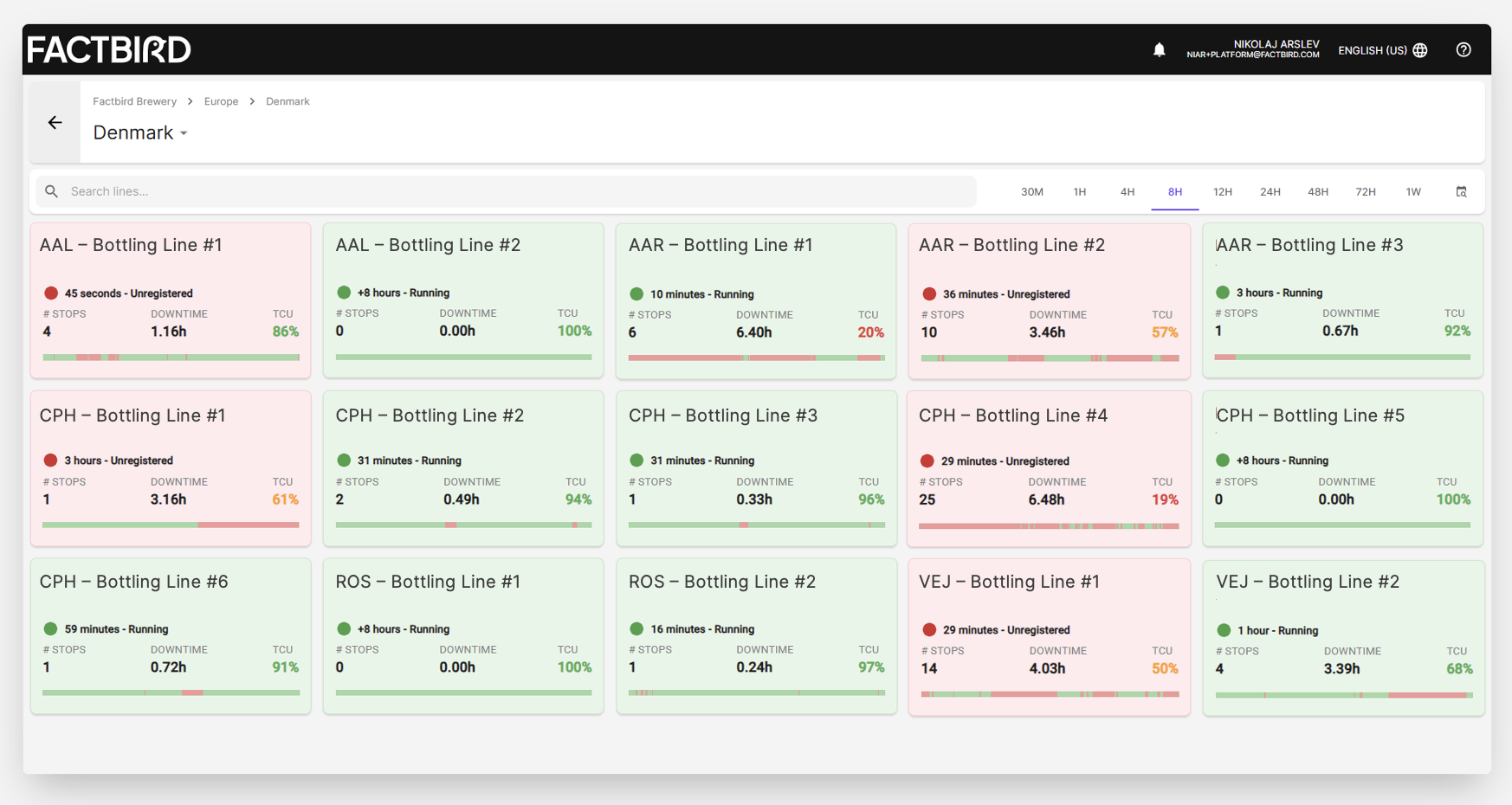
And all of this will work according to the way you set up your organization in Factbird. So whether you have business organizations, regions, or countries, it will be reflected in the system once you have set up your organization.
Preview: AI-powered insights
And then, like a lot of other companies, we've been following along with the developments within the AI and especially large language models.
We have been trying to figure out how to best apply this technology. We must effectively utilize this tool to generate value for you all.
Our vision is to introduce an assistant to the market where you can simply ask questions and receive a helpful response.
In the ideal scenario, a shift manager would be able to ask the question, What's my top five priorities for the upcoming shift? And it would guide you in the direction.
I also have to mention that at this point in time, we are not there yet. We'd like to invite you guys on the journey towards getting to that point. When we release the Farbird Assistant, it will be in a beta version, and we will value the inputs you provide to improve the product.
Connected Operations
For us, the concept of connected operations involves connecting all activities taking place on the shop floor to the cloud. Some call this paperless execution. It’s about understanding what people are doing but also equipping them with instructions on how to do things when needed.
We also need to be able to track how it actually went so that they can put feedback into the system and we can go back and look at it historically. And for us, this is both raising quality but also ensuring that our maintenance activities are addressing the proper needs.
Preview: Activities
If we go back to the Factbird brewery, I'm here at bottling line number one, and you can see that I have a list of different activities.
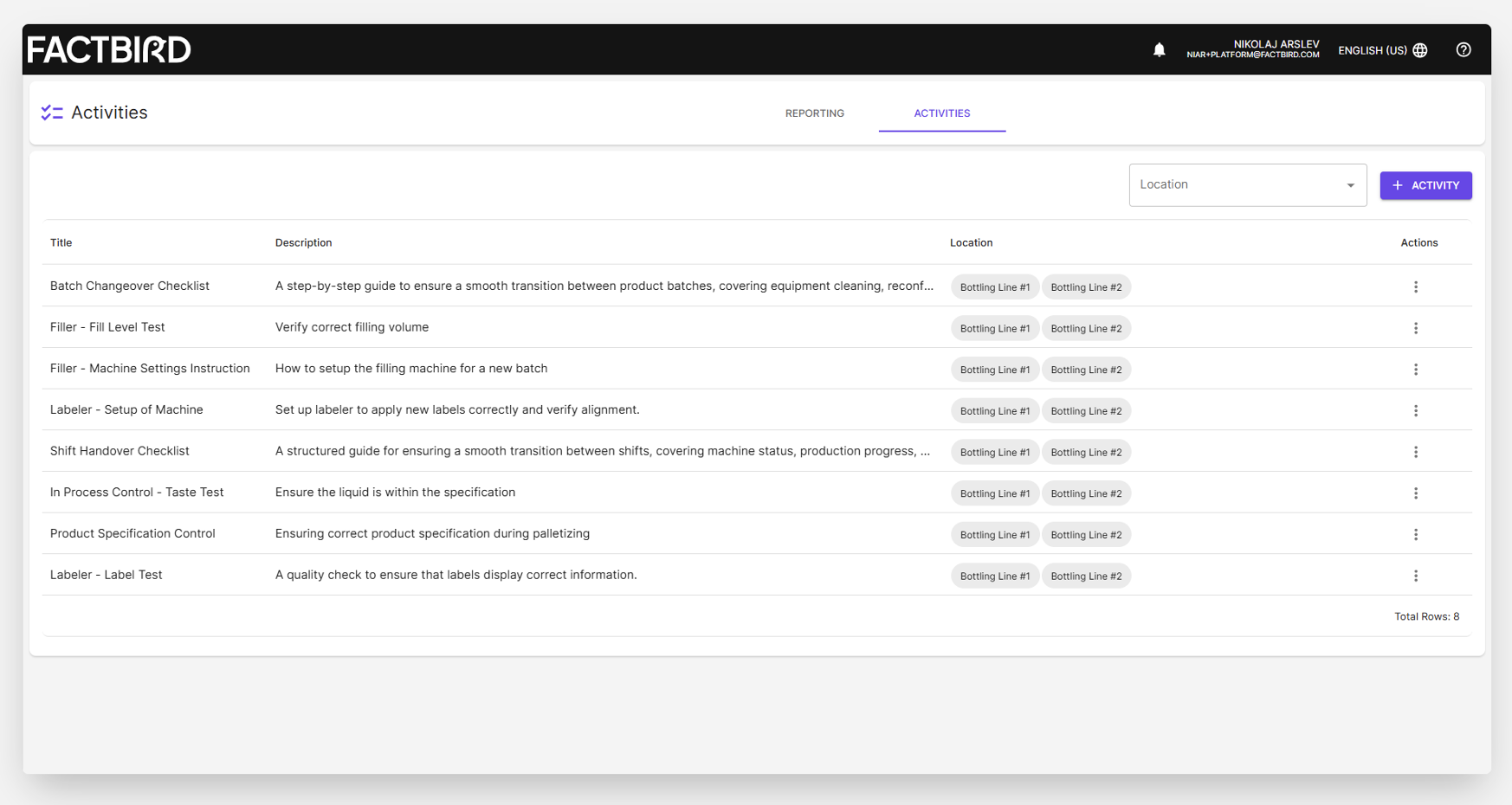
You'll notice that I have my batch changeover checklist. I have various in-process controls and quality checks. I have a shift handover checklist and instructions for how to properly set up my equipment.
The idea behind this is that you can tailor it to your factory and your company because we know that this looks different from company to company.
You can easily delete and create new activities, or you can edit existing ones.
For example, I have a fill level test on my filler, where I have put in some instructions on what I expect to be done and inputs based on the measurements that are done on the shop floor.
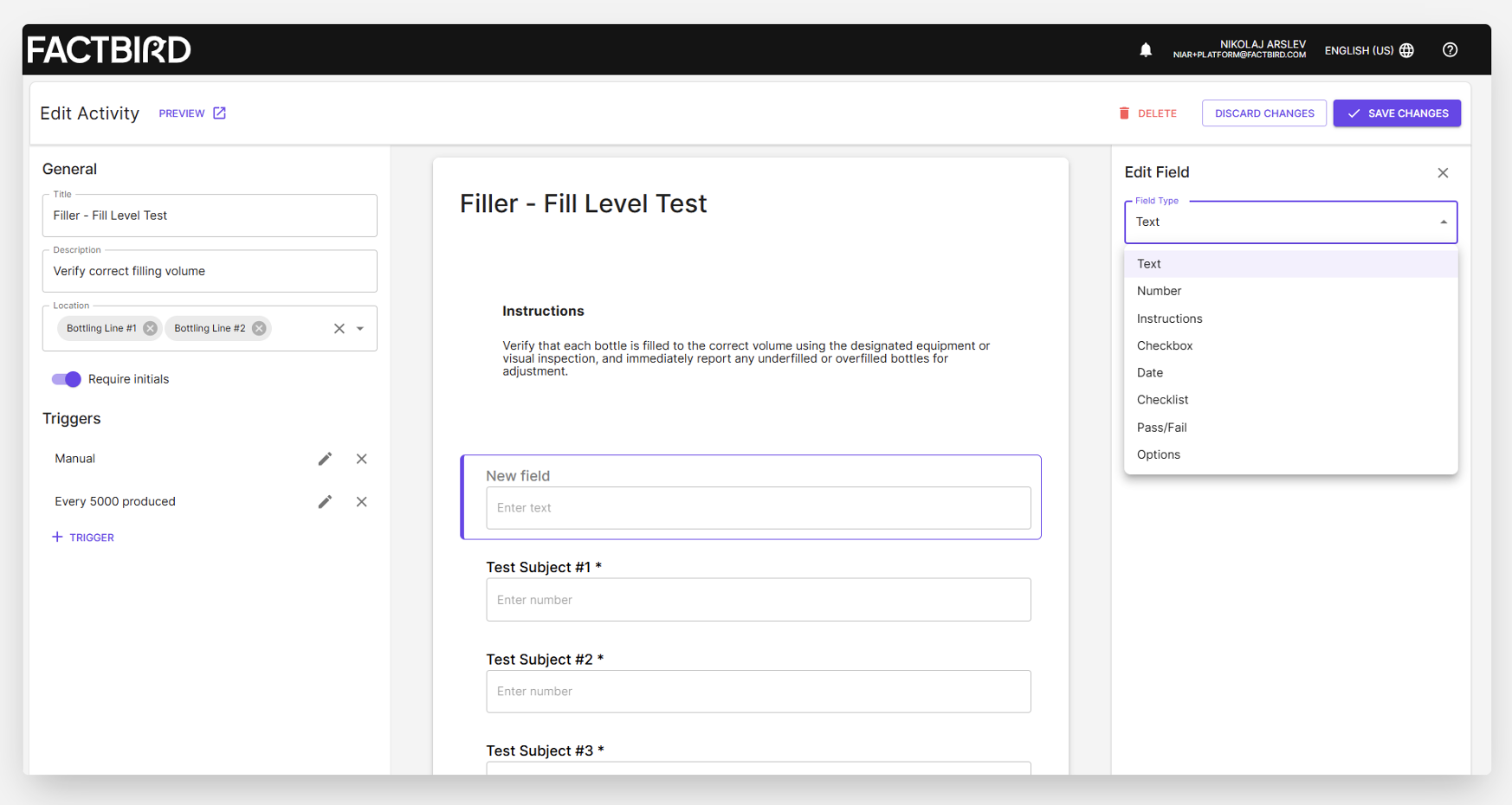
I can change how this activity looks by introducing different elements, whether that be adding a date, marking pass or fail, inputting numbers, and adding images that help better understand what it is that I actually need to be doing.
This is the first part of connected operations. This is establishing the standards and what we expect our people to do.
The second part is probably just as important. It ensures the timely presentation of your Activities to front-line workers.
If you have used our product-specific controls, you are likely familiar with the functionality of triggers.
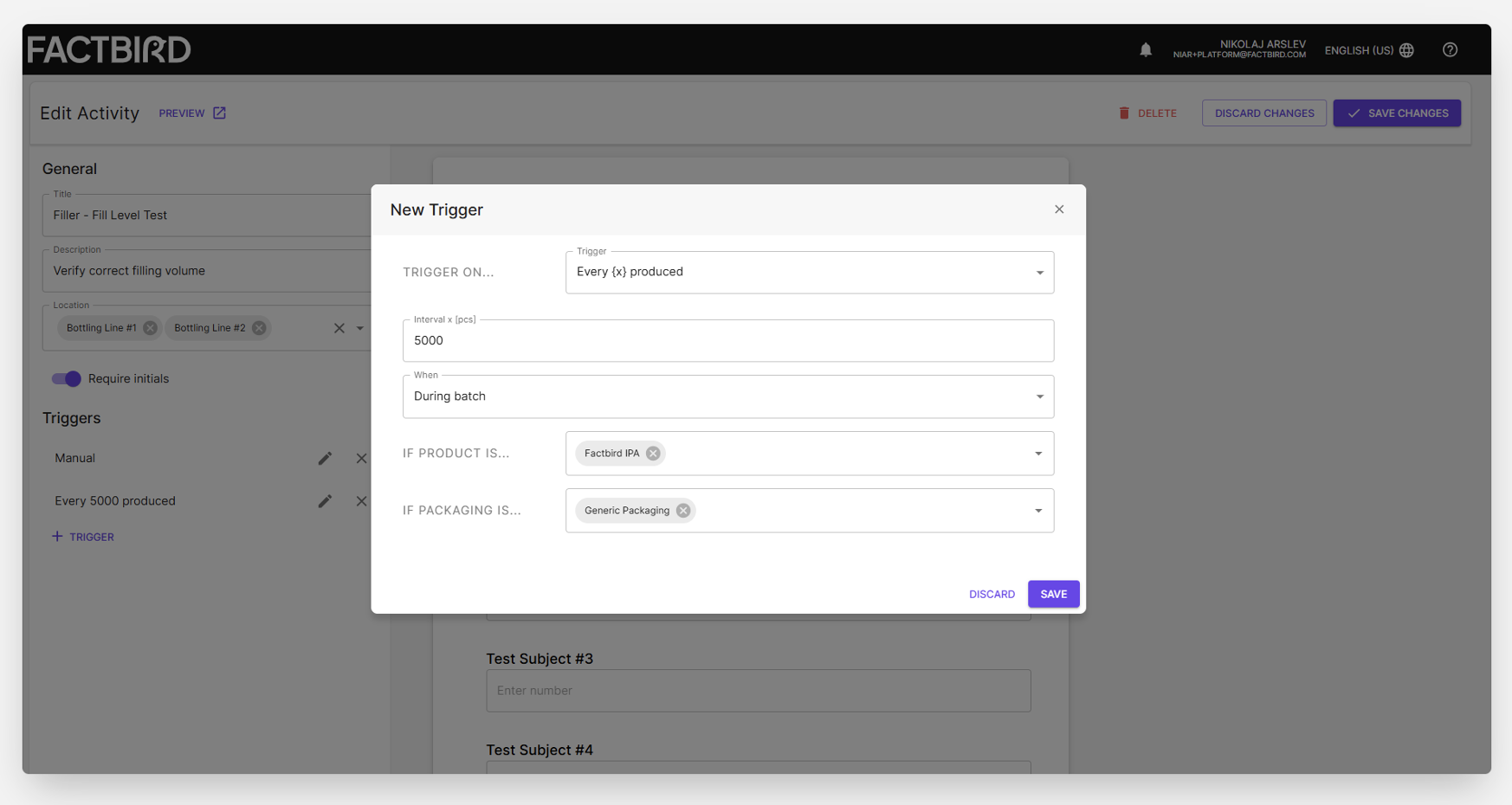
Triggers give you the opportunity to instruct when an activity should happen on the shop floor. So, if I'm an operator, I know when I need to do a task.
Previously, we only linked this to batches, but we understand that more flexibility is needed. Therefore, we are implementing new functionality that allows you to schedule tasks based on shifts, specific stop causes, or a calendar view, where a specific task needs to be completed once a week, twice a week, and so on.
And then what does all this look like?
Well, if I'm an operator and I get presented with the fill level test, I can see my instructions up top for measurements that I have to put in. I have to mark whether this test fails or not, and then put in my initials.
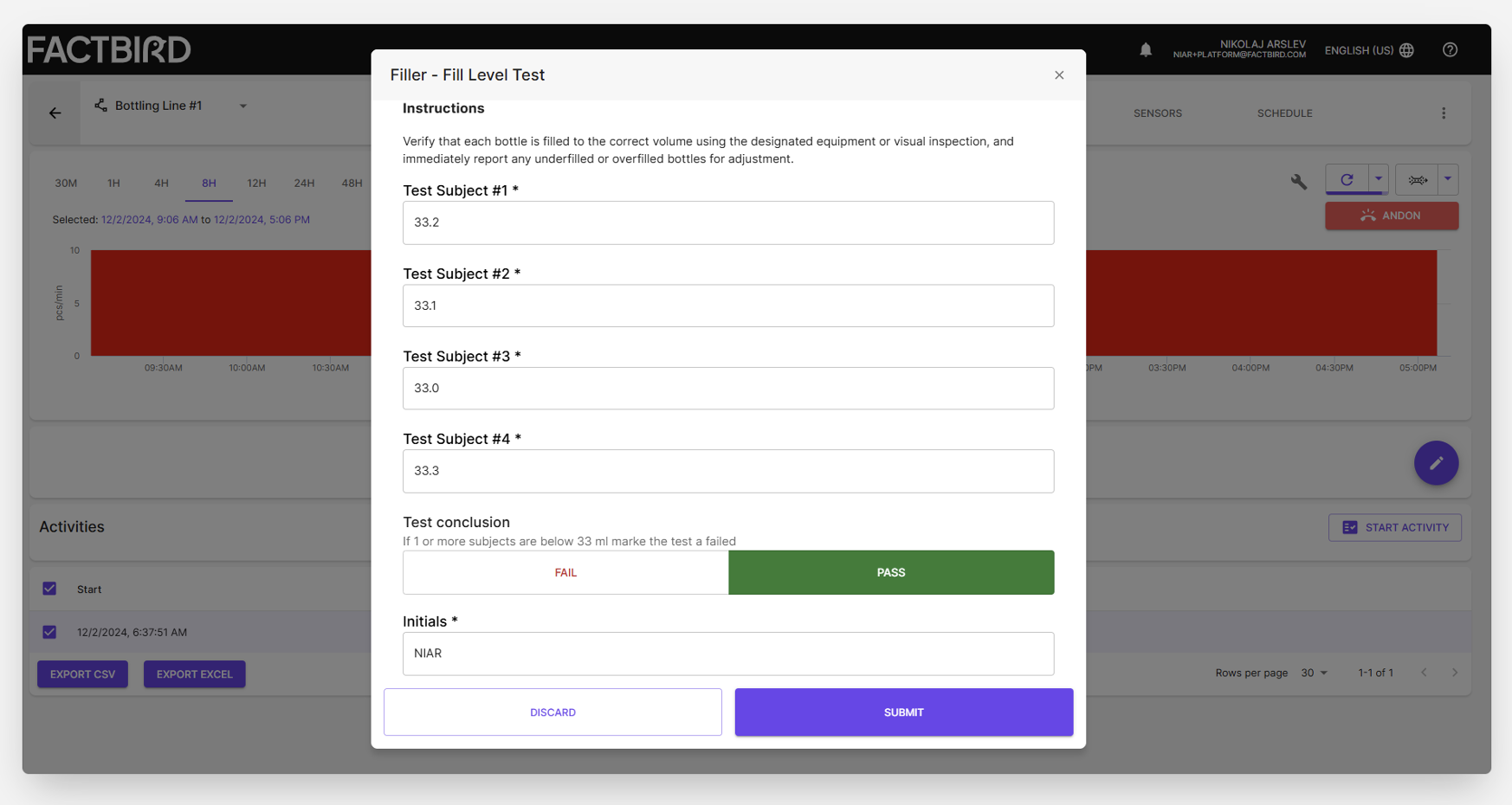
This will enable you to go back in time and track how things are going.
You will be able to look at a time range and understand all the activities that were done on the shop floor.
For example, I can go back in time and look at my fill volume test to see what data was inputted and see what actually happened on the floor.
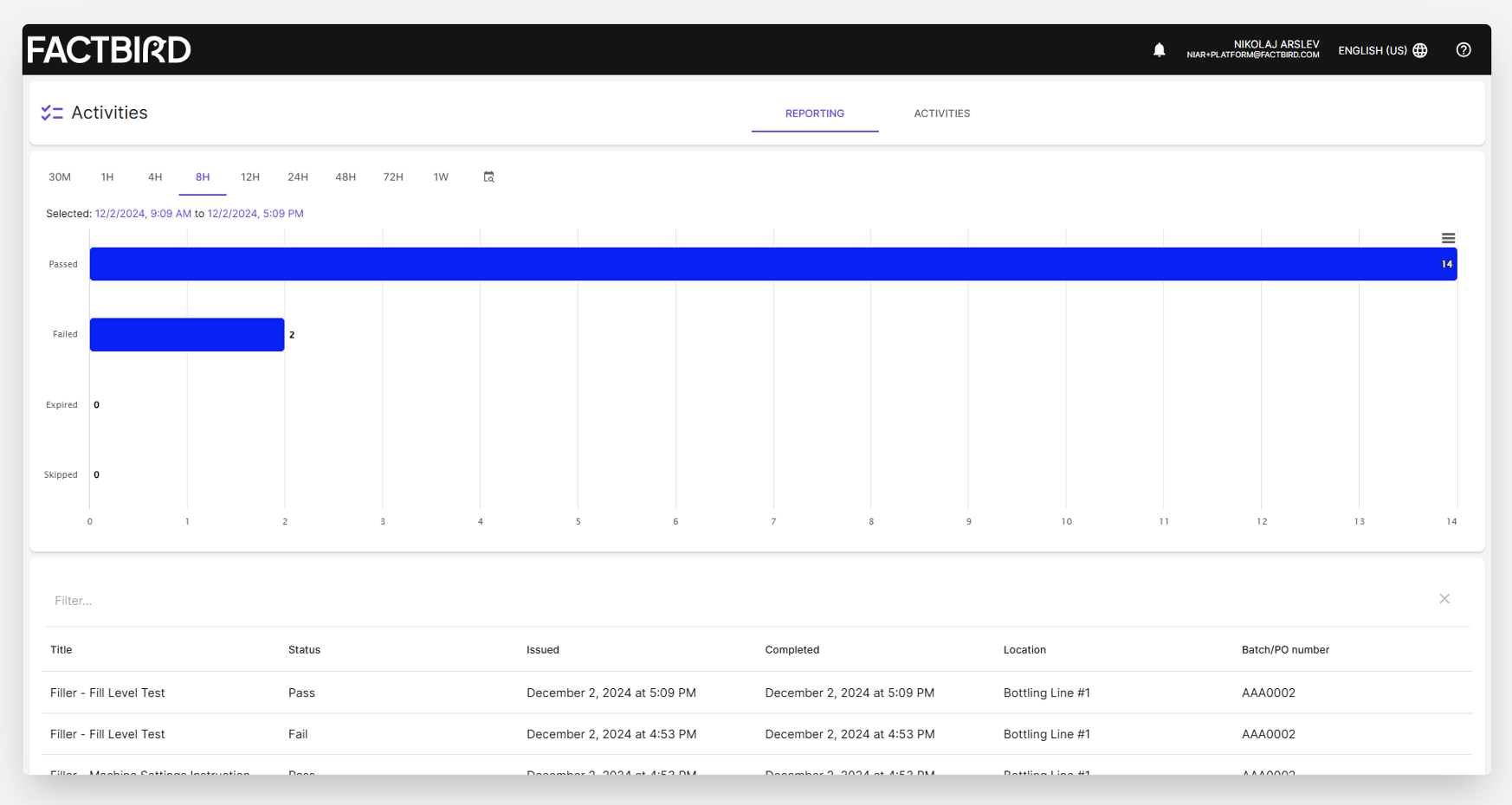
And if you need to be more specific and understand how a certain batch went, you just filter and search for that specific batch, and you will get the full story.
Here we have a failed activity, and I would like to understand in more detail why that is.
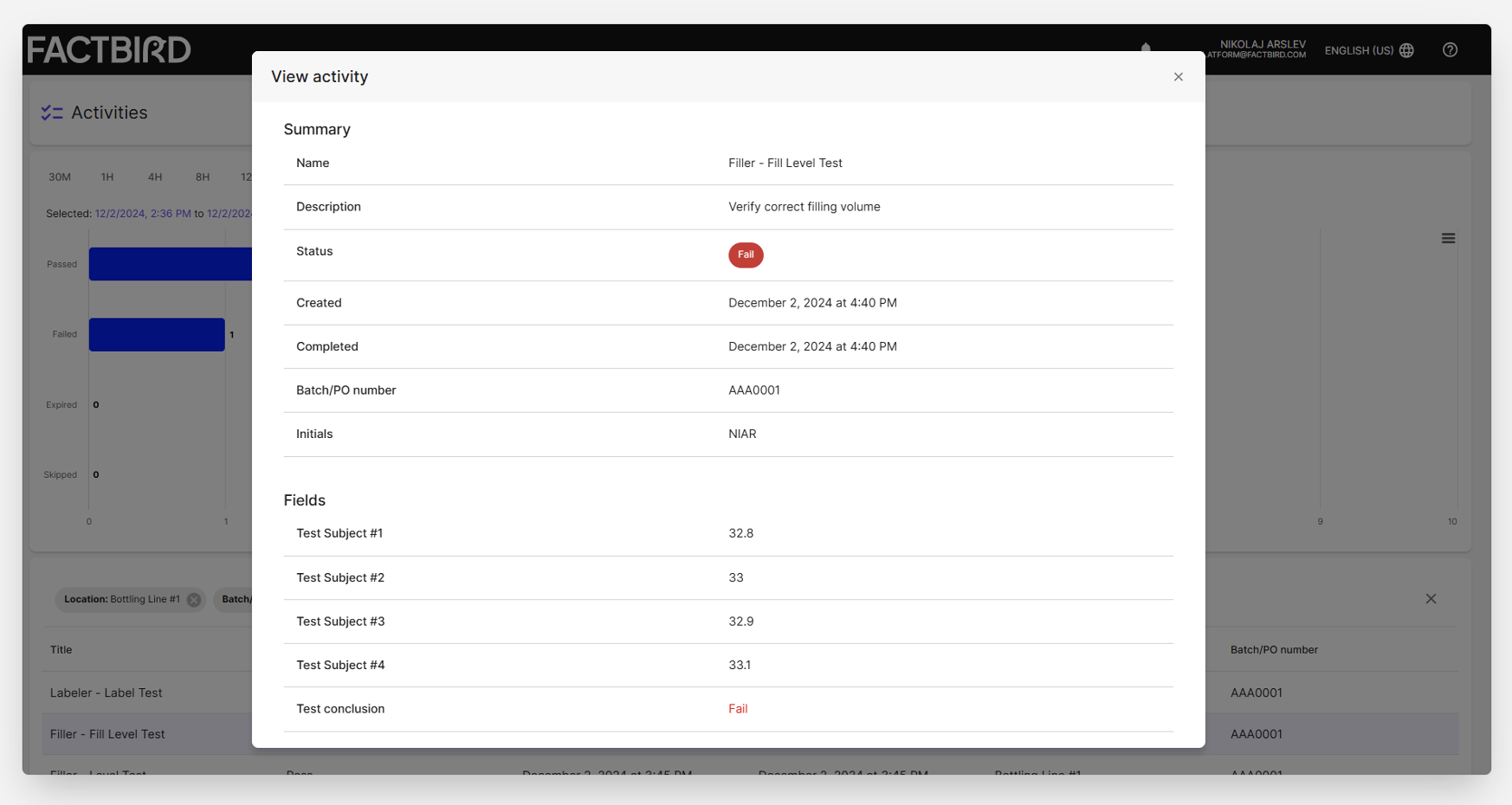
I ’m able to simply open it up and see all the information that the operator put in at the time of execution.
Knowledge Excellence
As mentioned, our goal is improving people and processes. And that's why when we consider this, we look at three main capabilities; training, skills management, and then operational excellence.
We believe this is crucial because without equipping people with the necessary skills, they won't be successful, and we’ll face more downtime.
Secondly, we need to make sure that what we ask them to do is a simple process that is easy to understand and is easy to carry out. So we need tools that can help us improve upon those processes.
Preview: Skills Management
In January, we will introduce our new learning management system for the shop floor. And here we are once again back at bottling line number one at the Factbird brewery.
This is a simple overview of my employees and the skills they need to operate this production line.
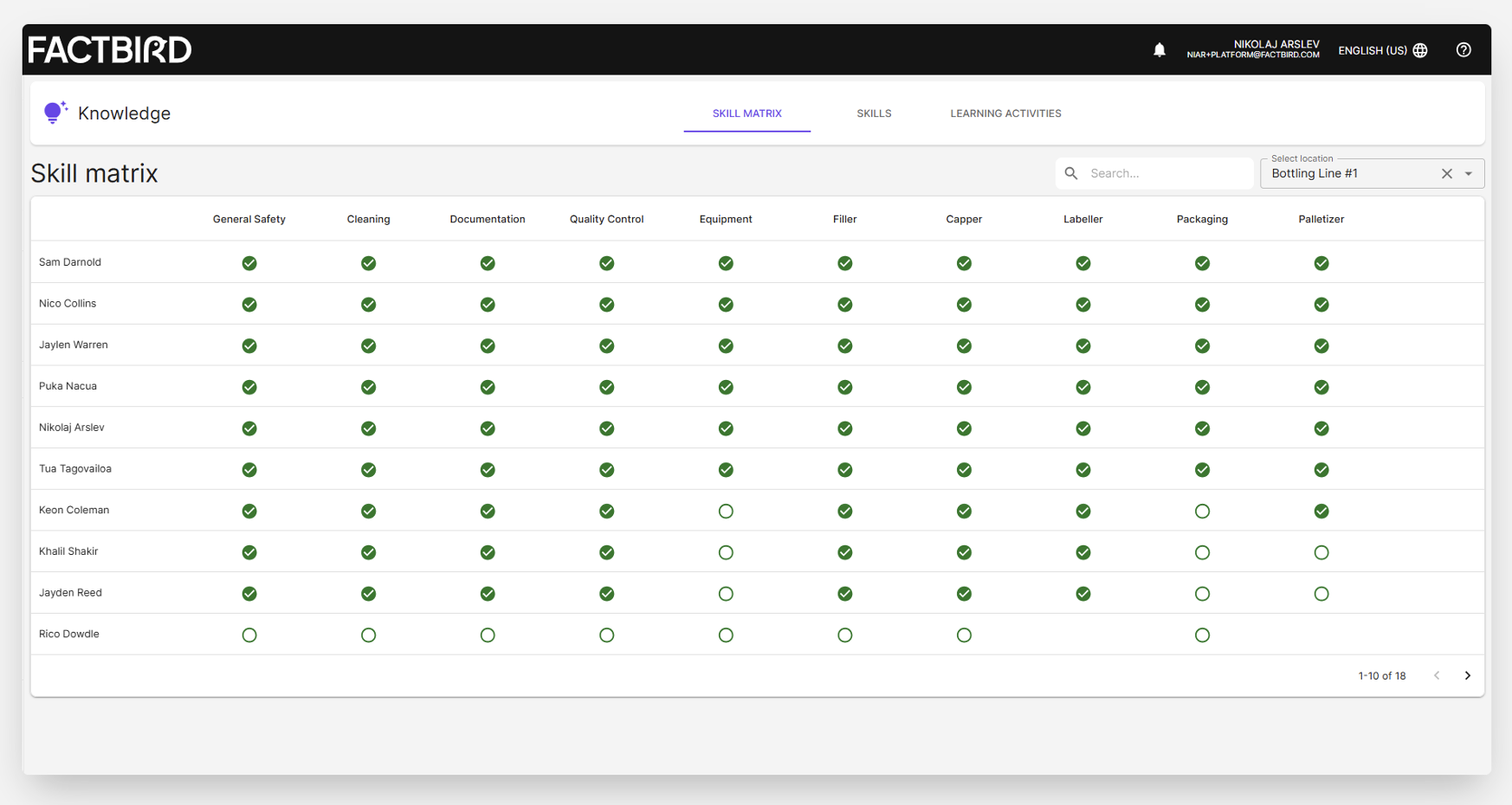
You can see who has completed the training, who has training pending, and who hasn't been assigned yet.
Now you can easily manage who should be enrolled into the different skills and see what training is needed.
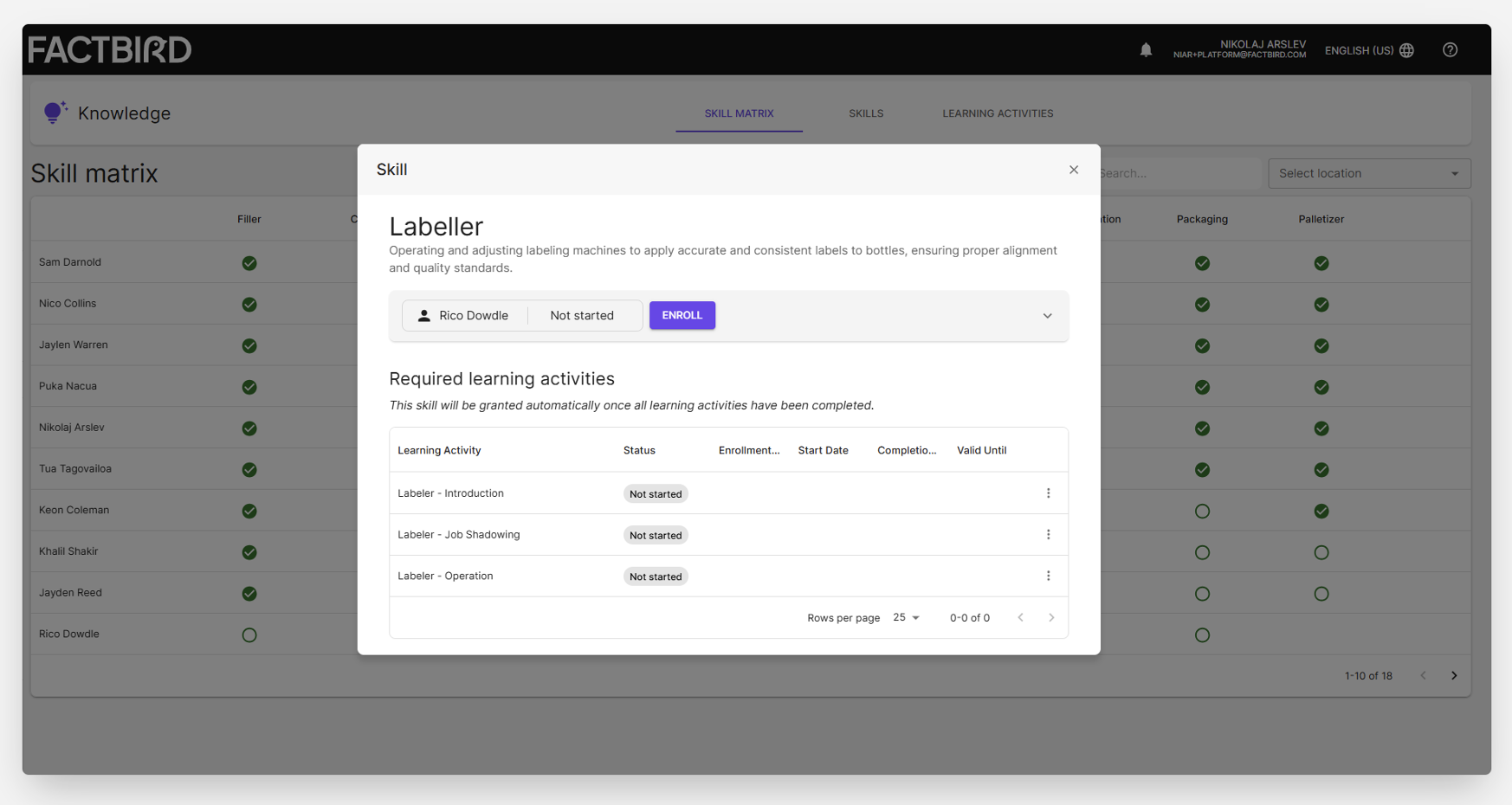
When the employee has carried out the training, the skills matrix will update accordingly. This allows you to monitor skill gaps and areas that require additional effort to ensure that your employees possess the necessary skills to perform the tasks you have assigned them.
Similarly to Activities, we know that no plant is the same, especially not when you're considering company to company.
Here, I've developed my skills specifically for the Factbird brewery bottling line number one. These skills include general cleaning, quality control, and equipment understanding, with each line receiving specialized training to ensure proper operation.
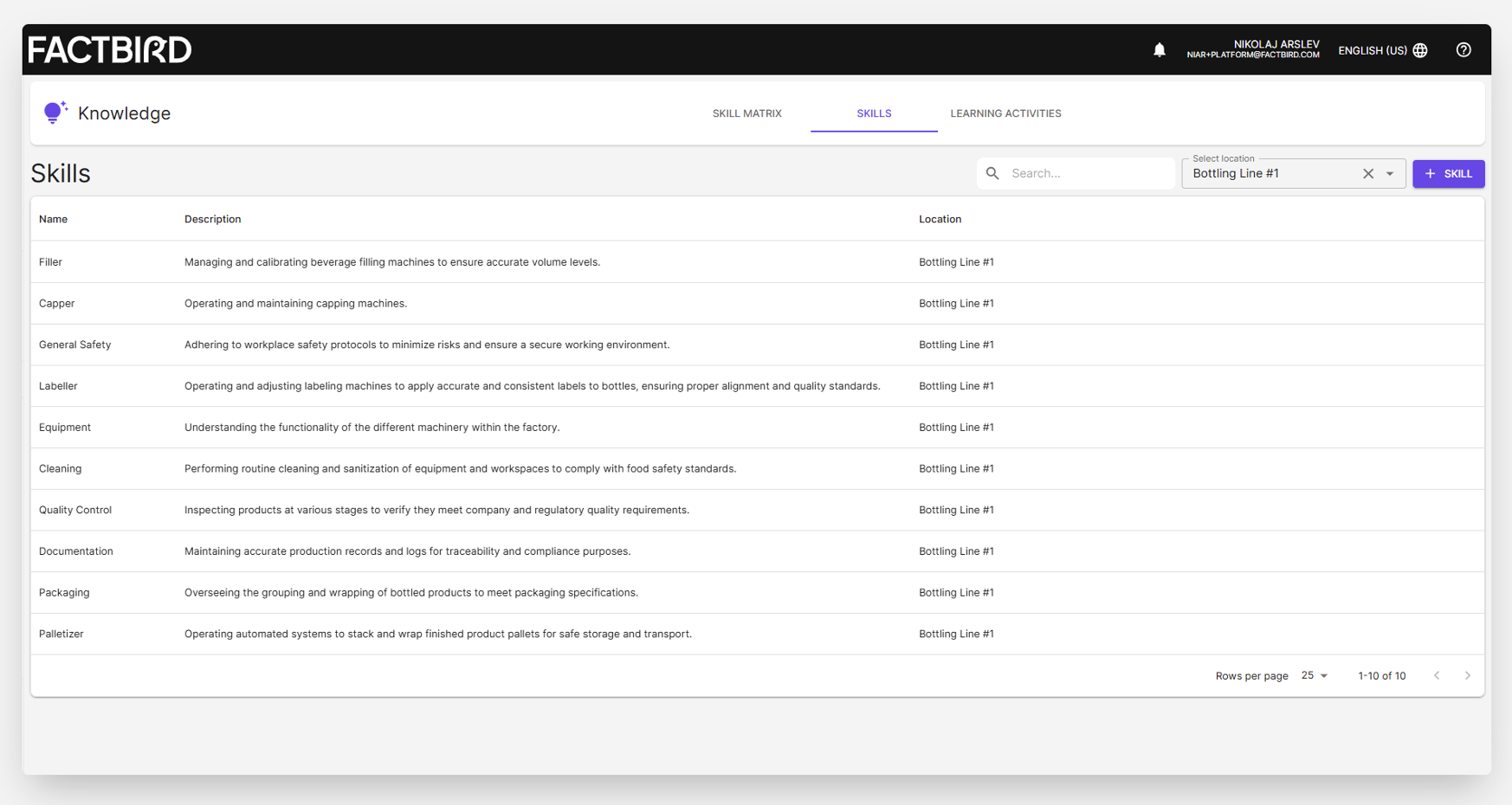
And again, this is fully customizable. You can delete, add, or edit existing skills, and make sure that the correct training and learning activities are associated with that skill. So, if we look at the labeler, for instance, I expect operators to go through three learning activities before operating the labeler.
Here, that involves an introduction to the equipment, a job shadowing session where I'm following a colleague that shows me how the work is done, and showing myself that I can operate the equipment autonomously.
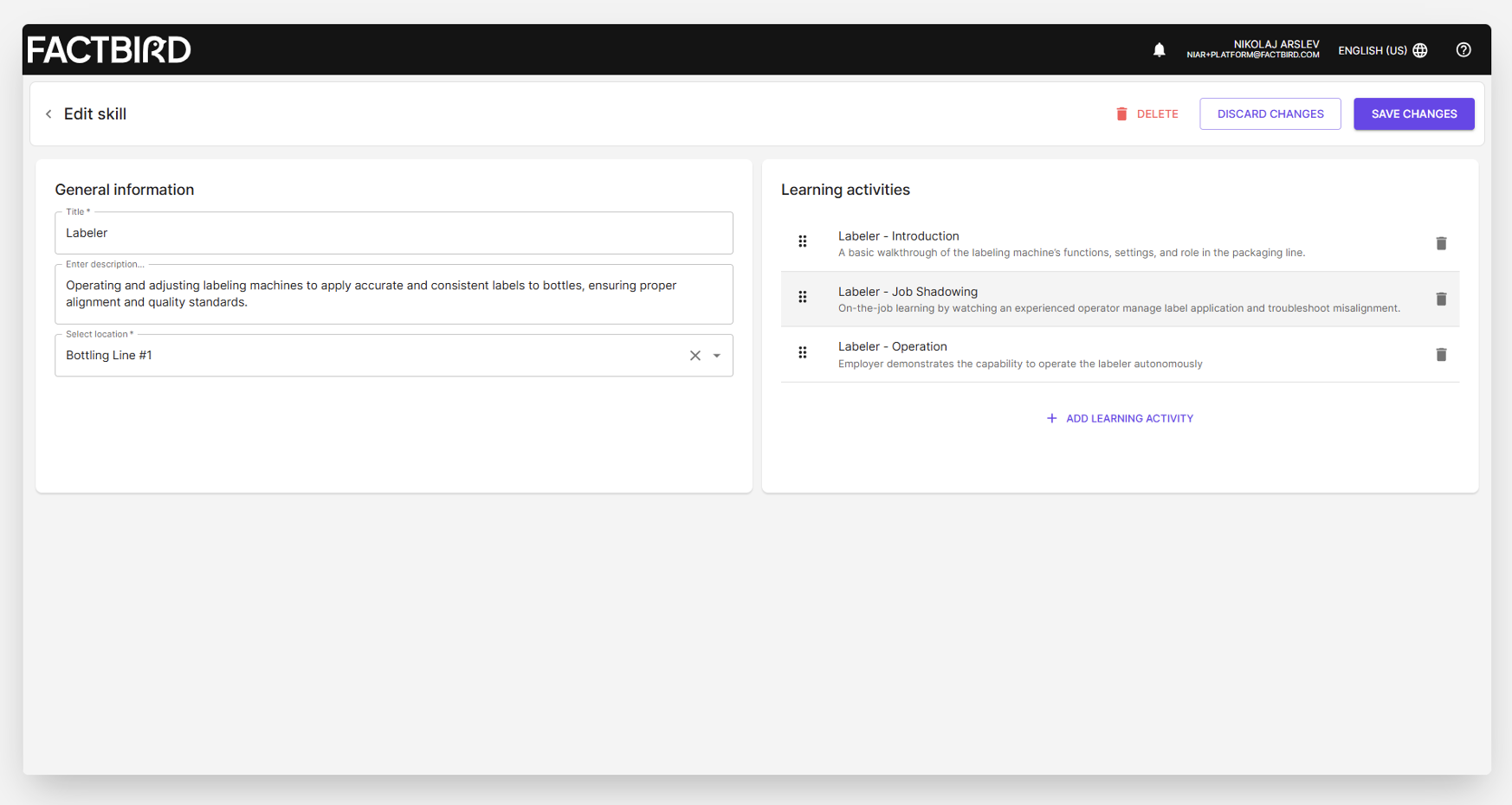
The way we think about learning activities is a representation of some sort of training. It can be taking a test, reading a document, attending a classroom training, or shop-floor training. It can be displaying that you know how to operate equipment on your own.
This is a fully customizable and flexible solution. You can go in and you can see that here I have an outline for a job shadowing session and what I'm expecting the employee to go through to perform this training, looking over the shoulders of another employee and making sure that I go through all of these activities.
Operators on the shop floor will have a personal view of all their existing skills, what we're expecting of them in terms of training they need to attend, and what they have yet to do.
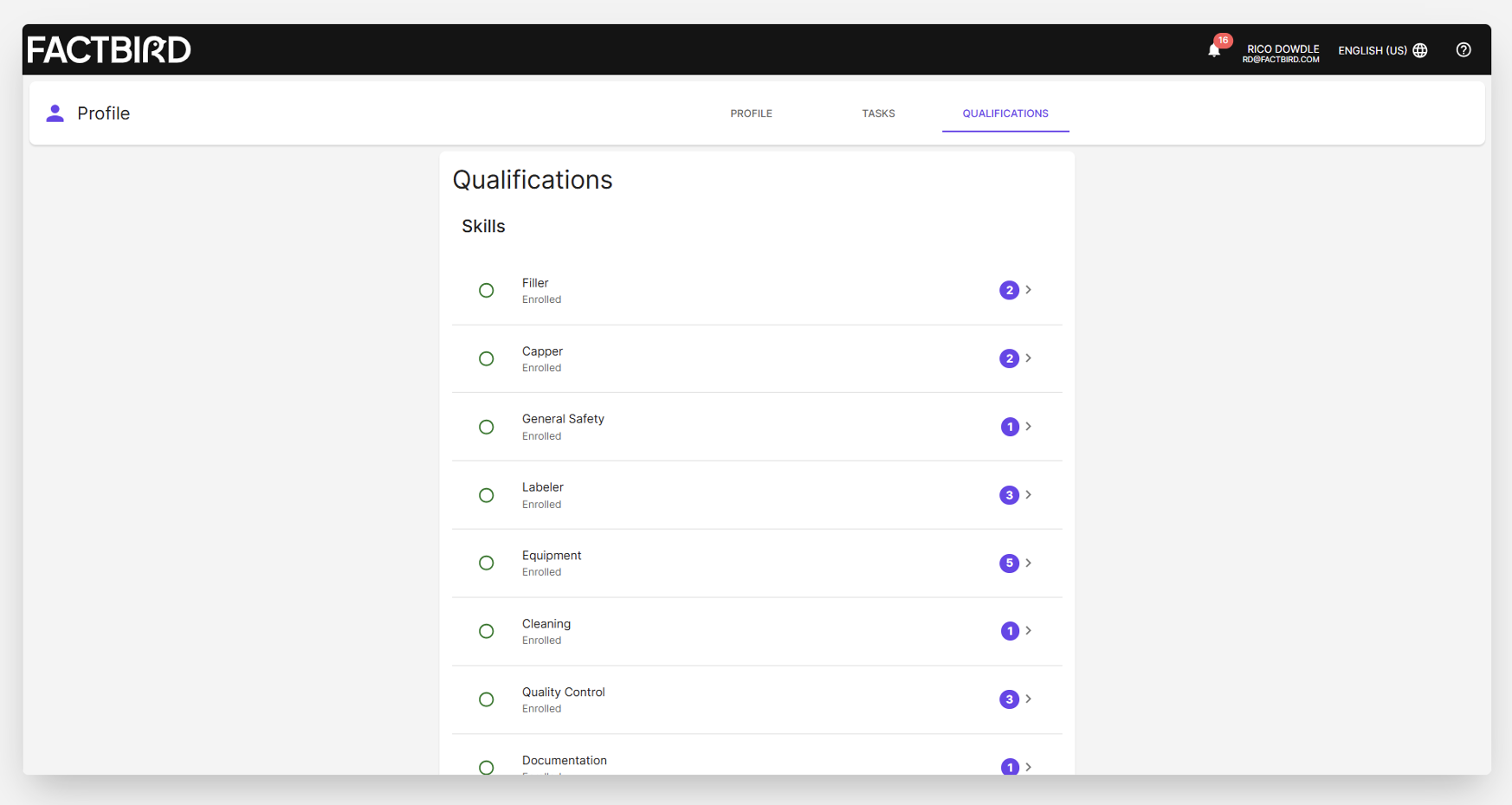
As you can see, I have a new employee who has enrolled in all the necessary training but has not yet completed it.
Finally, everything is presented to the individual in a personalized view of their tasks to complete.
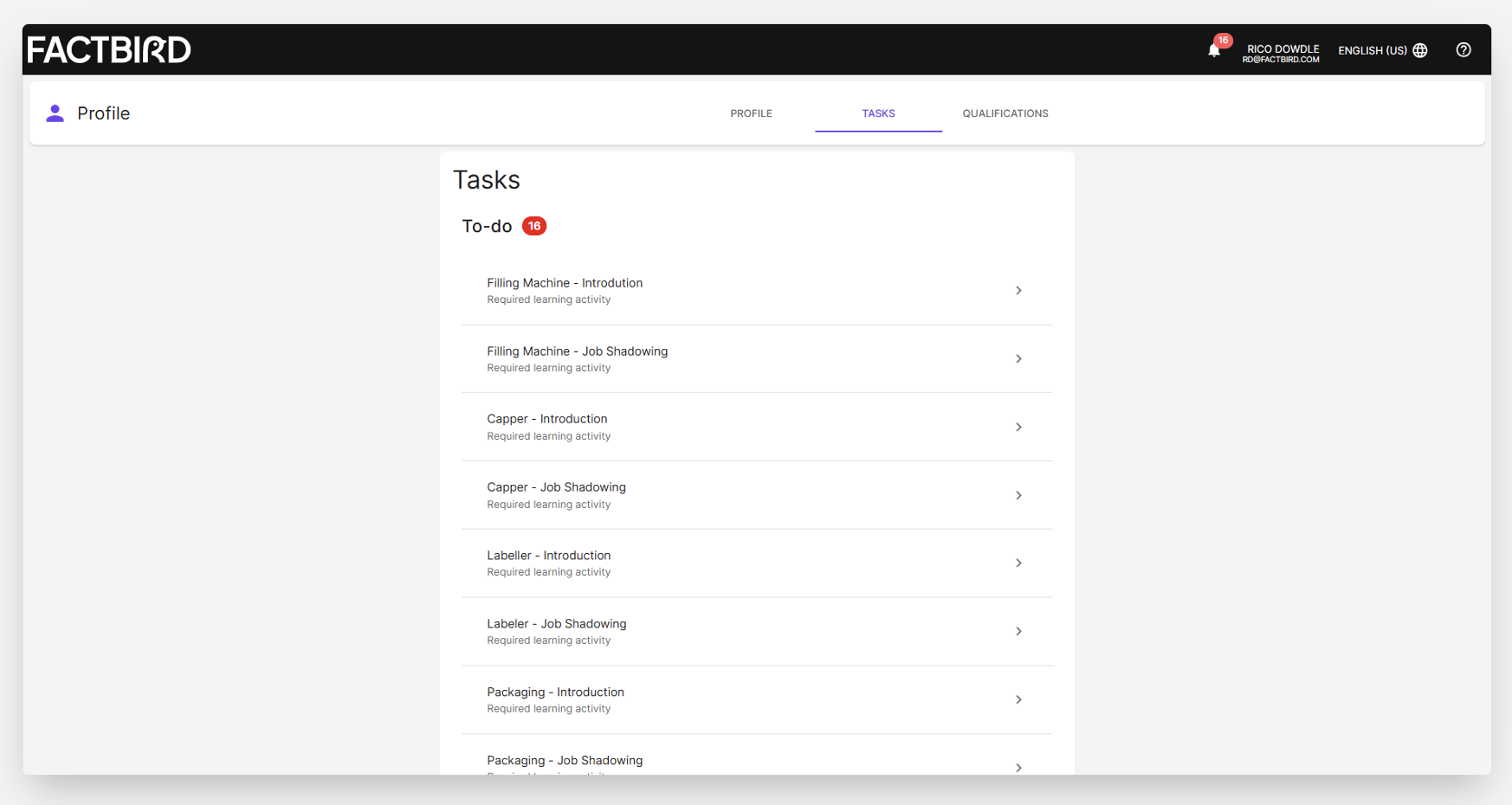
Factbird’s 2025 Product Roadmap
The next step for Factbird is to bring these three applications to market.
Through Production Insights, we'll continue to help you to manage performance.
Through Connected Operations, we will enable you to better manage execution.
With Knowledge Excellence, we will ensure that we are part of your journey towards continuous improvement so you can improve upon your operations.
Here is a roadmap of the development within the three applications.

I won't bore you with all the details, but I want to let you know that we will continue to develop our existing product through production insights, and we'll add to the capabilities of both connected operations and knowledge excellence as we progress throughout next year.
Thank you for your time!