Improving quality control in manufacturing
This article will discuss the significance of quality control and explore techniques for improving quality control using data-driven solutions.
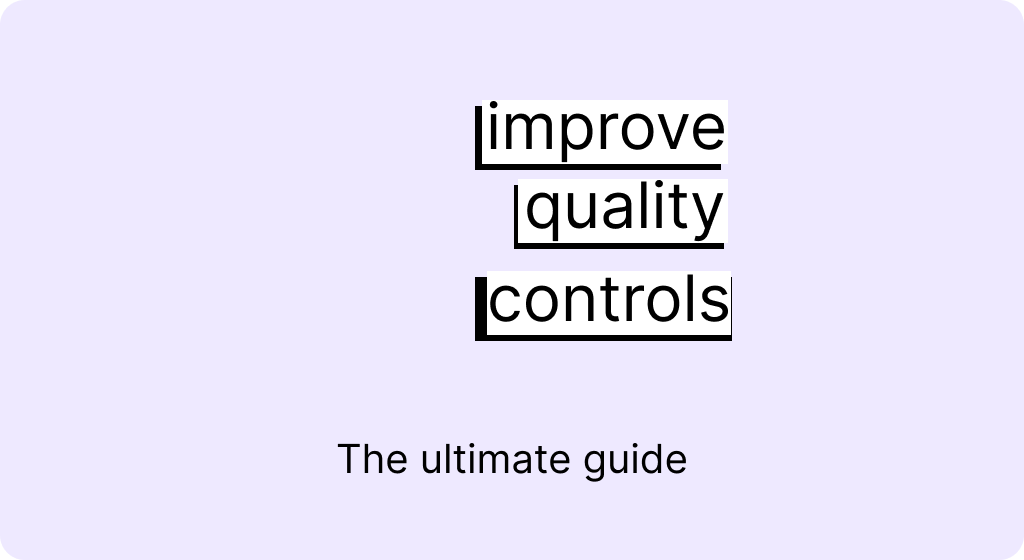
Quality control is an essential component of modern manufacturing. In a world where customers demand the highest levels of performance, durability, and safety, it is the responsibility of production managers and plant managers to ensure that their facilities consistently produce high-quality products.
And in today's competitive market, manufacturers simply must prioritize quality control (QC) in their operations. Quality control in manufacturing not only helps maintain high production standards but also enhances customer satisfaction
One solution that has emerged to assist in this pursuit is the adoption of manufacturing performance software, such as Factbird. Adopting manufacturing data software like Factbird can be a game-changer in optimizing quality control processes.
This article will discuss the significance of quality control in manufacturing, compare quality control and quality assurance, and explore various methods and techniques for improving quality control using data-driven solutions.
Quality Control in Manufacturing: A Crucial Component
Quality control in manufacturing is the process of ensuring that products meet the desired standards of quality, safety, and performance. This is achieved through a combination of inspection, testing, and corrective action, which helps to identify and eliminate any defects or inconsistencies in the final products (1). Quality control is essential for maintaining the reputation of a brand, ensuring customer satisfaction, and complying with industry regulations.
Effective quality control processes help to identify and address defects and inconsistencies early in the manufacturing process, significantly reducing the need for rework, scrapping, or repairing faulty products. By minimizing waste and reducing production costs, quality control directly contributes to the financial success of a manufacturing company (1).
Factbird assists manufacturers in enhancing their quality control efforts by gathering and analyzing data from various stages of the production process. This data-driven approach helps identify trends and patterns that may not be apparent through traditional quality control methods, enabling manufacturers to make more informed decisions on process improvements and defect prevention (2). By providing real-time insights, Factbird allows production managers to quickly identify and address quality issues, preventing costly delays or recalls.
Quality Control vs. Quality Assurance: Understanding the difference
It's important to distinguish between quality control and quality assurance. While both aim to ensure the production of high-quality products, quality control is a reactive process focused on identifying and addressing defects and non-conformities in products. On the other hand, quality assurance is a proactive approach, centered on designing and implementing processes and procedures to prevent quality issues from arising in the first place (3). Both quality control and quality assurance are essential components of a comprehensive quality management system, with each playing a vital role in ensuring that products meet the required standards.
In essence, quality control and quality assurance (QA) are both critical for product quality but serve different purposes in the manufacturing process:
- Quality Control: QC is a product-oriented approach that focuses on detecting and correcting defects in finished products through inspections and tests.
- Quality Assurance: QA is a process-oriented approach that aims to prevent defects by improving manufacturing processes, procedures, and systems.
Why Quality Control is Important in Manufacturing
Quality control plays a critical role in the manufacturing industry. Its importance spans across various aspects, including maintaining brand reputation, ensuring customer satisfaction, and complying with industry regulations.
Compliance with industry regulations and standards is another critical reason for implementing effective quality control measures. Many industries, such as automotive, pharmaceuticals, and aerospace, have stringent regulations and standards that must be met. These regulations are in place to protect consumers and ensure that products are safe, reliable, and perform as expected. Quality control helps manufacturers adhere to these regulations, reducing the risk of penalties, legal action, or recalls that could damage the company's reputation and financial stability.
Maintaining brand reputation is one of the essential reasons why quality control is crucial in manufacturing. A company's reputation is built on the consistent production of high-quality products. When customers trust that a brand will provide superior products, they are more likely to remain loyal and recommend the brand to others. Conversely, companies with a history of quality issues may find it challenging to regain consumer trust, leading to potential loss of market share.
Quality control plays a vital role in manufacturing, offering benefits such as:
- Improved Product Quality: Regular inspections and tests identify defects early, allowing manufacturers to address issues promptly.
- Reduced Costs: Effective QC minimizes waste, rework, and returns, ultimately lowering production costs and increasing profitability.
- Compliance with Regulations: Adhering to established quality standards helps manufacturers comply with industry-specific regulations and certifications.
- Enhanced Brand Reputation: Consistent product quality builds trust with customers, leading to increased sales and repeat business.
Methods to Increase Quality Control: Methods and Techniques
As manufacturing companies strive to improve product quality, it is vital to explore various methods and strategies that can bolster their quality control efforts. Next up are methods to be employed to enhance quality control, streamline processes, and ensure consistent production of high-quality products.
By understanding and implementing these techniques, manufacturers can optimize their operations and stay ahead in today's competitive market landscape.
Several methods and techniques can help improve quality control in manufacturing:
- Just in Time (JIT): JIT is a production strategy that aims to minimize inventory levels by producing and delivering goods just as they are needed, reducing waste and inefficiencies.
- Workstation Quality: Ensuring that workstations are well-organized, clean, and equipped with the necessary tools and resources can help prevent errors and promote quality.
- Statistical Quality Control: This method uses statistical techniques to monitor and control manufacturing processes, identifying variations that may lead to defects.
- Inspection: Regular inspections of finished products help detect visible defects, such as surface imperfections or incorrect labeling.
- Total Quality Management (TQM): TQM is an organization-wide approach to quality management that focuses on continuous improvement in all aspects of the business, including manufacturing processes and customer satisfaction.
Improving Quality Control in Manufacturing
In today's competitive manufacturing landscape, enhancing quality control is paramount for organizations looking to maintain a strong market presence and achieve long-term success. A holistic approach to improving quality control involves implementing key strategies and ensuring a continuous theme throughout each aspect of the process. This includes auditing processes, collecting data, adopting the latest technologies, fostering a culture of continuous improvement, and promoting collaboration and communication throughout the organization.
The foundation for enhancing quality control lies in conducting regular audits of production processes. By identifying potential areas for improvement and ensuring that procedures are consistently followed, organizations can lay the groundwork for a robust quality control system. This system will enable manufacturers to make targeted improvements to their production processes, ultimately resulting in better overall quality.
Building upon the foundation of auditing processes, collecting and analyzing data on product quality, production processes, and equipment performance is the next crucial step. This data-driven approach enables more informed decision-making and helps organizations identify trends and patterns that may not be apparent through traditional inspection methods. By leveraging the insights gained from data analysis, manufacturers can focus their improvement efforts on areas with the most significant potential impact, further strengthening their quality control practices.
As organizations progress in their quality control journey, adopting the latest technologies becomes essential for staying ahead in the competitive landscape. Incorporating advanced automation and robotics can reduce human error and increase precision in the manufacturing process. Similarly, implementing machine learning and artificial intelligence algorithms can help organizations analyze large volumes of data more efficiently, identifying patterns or trends that may indicate potential quality issues. By embracing technological advancements, manufacturers can continuously refine their quality control strategies, resulting in higher-quality products.
Cultivating a culture of continuous improvement is another vital aspect of a holistic approach to quality control. Encouraging employees at all levels to take an active role in identifying potential quality issues and suggesting improvements helps create an environment where quality control practices are consistently evolving. Providing ongoing training and development opportunities ensures that employees stay up-to-date with the latest industry standards and best practices, enabling them to maintain high-quality production processes.
Lastly, fostering collaboration and communication among different departments within the organization is essential for a cohesive quality control strategy. By ensuring open lines of communication between production, engineering, and quality control teams, organizations can create a unified approach to identifying and resolving quality concerns. This collaborative environment allows for more efficient problem-solving and streamlines the overall quality control process.
Therefore, it's important to have a holistic approach to improving quality control in manufacturing which involves weaving a continuous theme throughout each aspect of the process. By implementing strategies such as auditing processes, collecting and analyzing data, adopting the latest technologies, fostering a culture of continuous improvement, and promoting collaboration and communication, manufacturers can enhance their quality control efforts. This comprehensive approach results in higher-quality products, increased customer satisfaction, and a stronger competitive position in the market.
Using a Data Collection Software
In the quest for enhanced quality control in manufacturing, adopting sophisticated tools like Factbird can prove invaluable. As a manufacturing performance software, Factbird provides a comprehensive solution that seamlessly ties each aspect of quality control together, enabling manufacturers to monitor their production lines, collect data, analyze it for insights, locate downtimes and errors, address them efficiently, and ultimately increase their Overall Equipment Effectiveness (OEE). Here's a rundown of what you're able to do:
Monitoring Production Lines
One of the key advantages of Factbird is its ability to provide real-time monitoring of production lines. This feature allows manufacturers to gain a comprehensive understanding of their operations, identify inefficiencies or potential issues, and make timely adjustments to maintain product quality. By offering a clear, visual representation of the entire production process, Factbird empowers manufacturers to make informed decisions and keep their quality control efforts on track.
Collecting and Analyzing Data
Factbird excels at collecting and analyzing data from various stages of the production process. This data-driven approach helps manufacturers identify trends, patterns, and potential bottlenecks that may be impacting product quality. With Factbird's powerful analytics tools, manufacturers can dive deep into the data to uncover insights that may have otherwise gone unnoticed. This information enables organizations to make targeted improvements to their production processes, further bolstering their quality control efforts
Locating Downtimes and Errors
Downtimes and errors can significantly impact product quality and overall manufacturing efficiency. Factbird's advanced monitoring and analytics capabilities allow manufacturers to pinpoint these issues quickly and accurately. By identifying the root causes of downtimes and errors, organizations can swiftly implement corrective actions and prevent further disruptions to their production process. This proactive approach to addressing issues helps manufacturers maintain consistent product quality and reduce the likelihood of costly recalls or customer dissatisfaction.
Fixing Errors and Increasing OEE
Once Factbird has identified downtimes and errors, manufacturers can take targeted steps to address them and improve their overall equipment effectiveness (OEE). By leveraging Factbird's insights, organizations can implement strategic changes to their production processes, equipment maintenance schedules, and employee training programs. These targeted improvements not only enhance product quality but also increase efficiency and productivity, ultimately contributing to a higher OEE.
Closing Thoughts
Quality control in manufacturing is crucial for ensuring consistent product quality, maintaining a competitive edge, and fostering customer satisfaction. Understanding the differences between quality control and quality assurance, implementing various quality control methods and techniques, and leveraging data-driven solutions like Factbird, manufacturing executives, production managers, and plant managers can significantly improve their quality control processes. Investing in manufacturing data software like Factbird can streamline and optimize quality control efforts, ultimately resulting in higher product quality, reduced costs, and a stronger brand reputation.