Danfoss achieved a 40% increase in production performance in less than a year by getting reliable data
About Danfoss
Danfoss, an industry-leading global manufacturer of hydraulic, climate, and power solutions has been one of Europe’s most notable industrial manufacturers for nearly a century. With 95 manufacturing facilities worldwide and more than 40,000 employees, Danfoss continuously seeks to innovate and optimize its manufacturing processes.
Watch the full interview on how Danfoss improved production performance by 40% below.
Challenges and decision making
Danfoss recognized the potential of getting real-time aggregated data from the machinery to optimize preventive action and efficiency even further. Martin Ole Madsen, Manager of Operating Excellence SVS, Danfoss, believed that if they could somehow pull all the production data from their databases and industrial equipment, and aggregate it in one tool and use it as a ground base for driving analytics that could lead to major process improvements.
Due to the rapid rise in energy prices as a result of issues plaguing today’s volatile geopolitical landscape, Danfoss expedited its plans to cut down on resource costs and process waste by increasing the efficiency and output of its existing production lines. To accomplish their goal, they would need reliable data insights they could trust and use to narrow down improvement areas and root causes of unplanned downtime. Special focus was put on solutions that could automate their data collection, rather than losing countless project hours on processes prone to human error.
Danfoss met with Factbird in early 2021, and after preliminary discussions were held, a pilot program was started to evaluate the solution. The main project objective was access to data aggregated in a single, easy-to-access ecosystem, analyzed and available 24/7 from anywhere in the world.
Implementation phase
Roll out of the pilot on three machines
The pilot was rolled-out in no time at all. Within 3 days of approval, the plant had already installed sensors and cameras on three different machines. Installation took only one hour, much to their surprise, as process improvements to date had taken months to implement.
Information could now be accessed via tablets, PCs, and smartphones in real-time, by anyone in the organization. The pilot itself took a total of five months, and all the data captured as a result were used to influence decisions that helped Danfoss achieve incredible results in efficiency.
With the help of accurate data, root causes of unplanned stoppages could be addressed in record times. And thanks to the impact of this single factor, management decided to roll the solution out across the entire facility.
Gradual implementation in the plant
After the success of the pilot, Danfoss gradually rolled Factbird out across several of their facilities, one machine at a time.
We could see when the machine was stopping when we had a pause or break in the plant shift, but also why the machine stood still. This became an eye-opener because you have a quite new system of machines plugged into one system, and maybe one simple part can make the whole system stand still for several hours. Several hours is equal to a lot of money wasted in production, so by adding the cameras and sensors, we could see the relevant data so we could locate the problem in the production line and fix it much faster.
Martin Ole Madsen, Manager - Operations Excellence SVS EUR at Danfoss Power Solutions.
Sensors installed throughout different points of production not only increased their visibility into their manufacturing processes but also improved how they measured energy, helping them significantly cut down on consumption.
Easy-to-access data
The project objective was to get reliable data, viewed in real-time. And the insights gained as a result were used to influence decision-making and set efficiency benchmarks.
We had a lot of data. It is a big company, but it was a kind of hidden knowledge before the digitalization using Factbird. Now with the information and data reports in front of every people, we have information to react on.
Martin Ole Madsen, Manager - Operations Excellence SVS EUR at Danfoss Power Solutions.
Application areas
Troubleshooting turned into an easy, traceable process
With daily logs detailing stop times, their causes, and their locations, Factbird's technology transformed what used to be a laborious process, into an almost instant one. Maintenance operators could now track stop error messages and evaluate the need for upgrades without interrupting production.
Optimizing energy consumption
Sustainability is the core value behind Danfoss’ 2025 strategy. Evaluating energy consumption and reducing resource waste is crucial in achieving their objectives. The introduction of production monitoring software allows Danfoss to research which strategies could help them align their manufacturing with their core values. Factbird's data insights suggested there was an opportunity to reduce stand-by energy consumption by as much as 77% by simply applying minor adjustments to their production workflow.
Performance impact
40% increase in production output thanks to reliable data
Less than a year after the project’s inception, Danfoss had measured an incredible increase in their production line outputs, with up to 40% on one of the production lines. This was made possible, in large part, thanks to Factbird's industry-leading ease-of-installation, guaranteeing uninterrupted work while tracking efficiency, and stop-causes, and shedding light on areas for improvement.
Decisions based on data-supported facts lead to 20% fewer production stops
Giving every team member in production access to Factbird's data insights helped them shed light on areas of improvement. Danfoss has used the Factbird application to manage their stop-cause registration process and analyze the data to find root causes for downtime, take action, and evaluate the effectiveness of those actions. They are experiencing on average 20% less production stops than when they have started.
Below you can see how that is displayed for Danfoss.
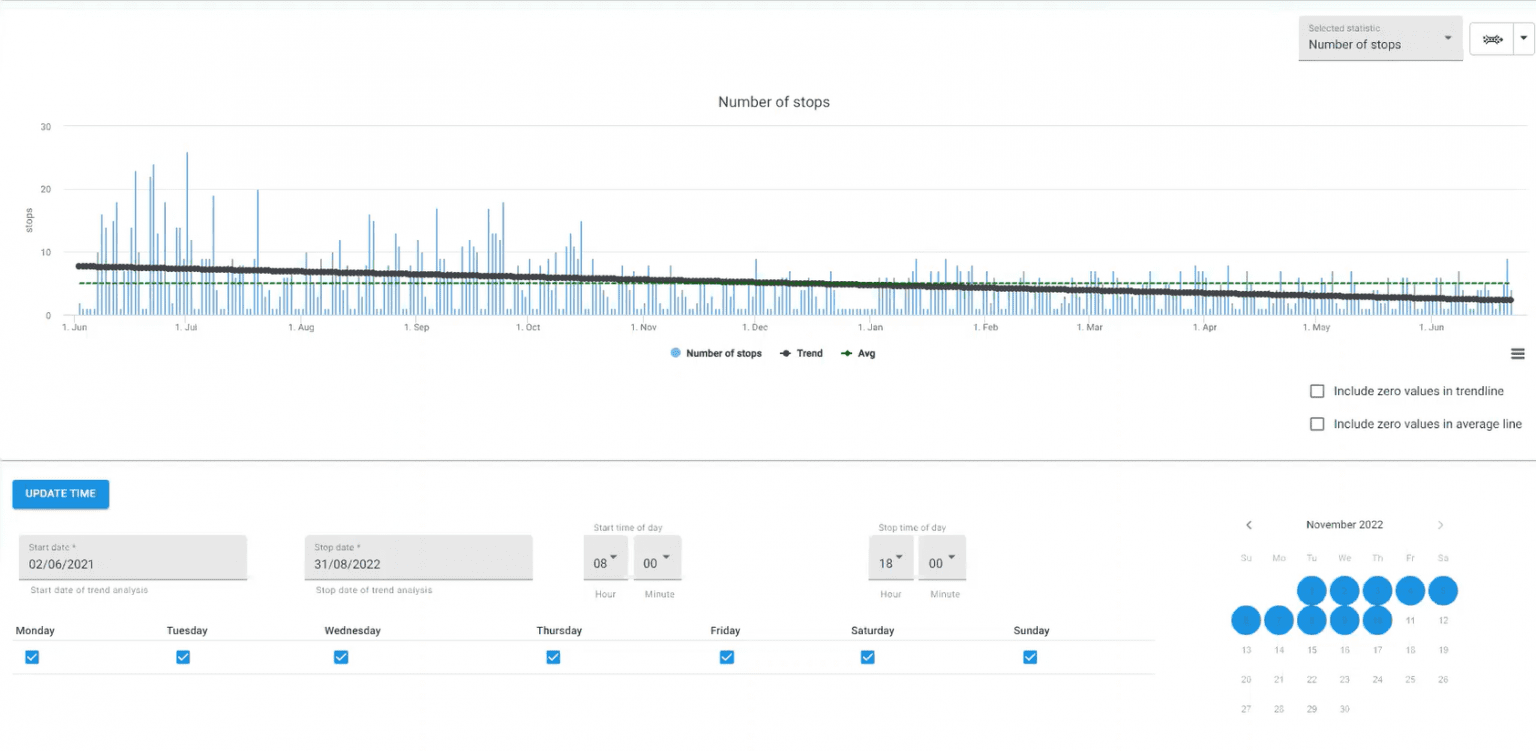