Free PDCA template for continuous improvement
Kickstart your continuous improvement journey with our free PDCA template (PDF), a step-by-step to guide boost efficiency and solve problems effectively.
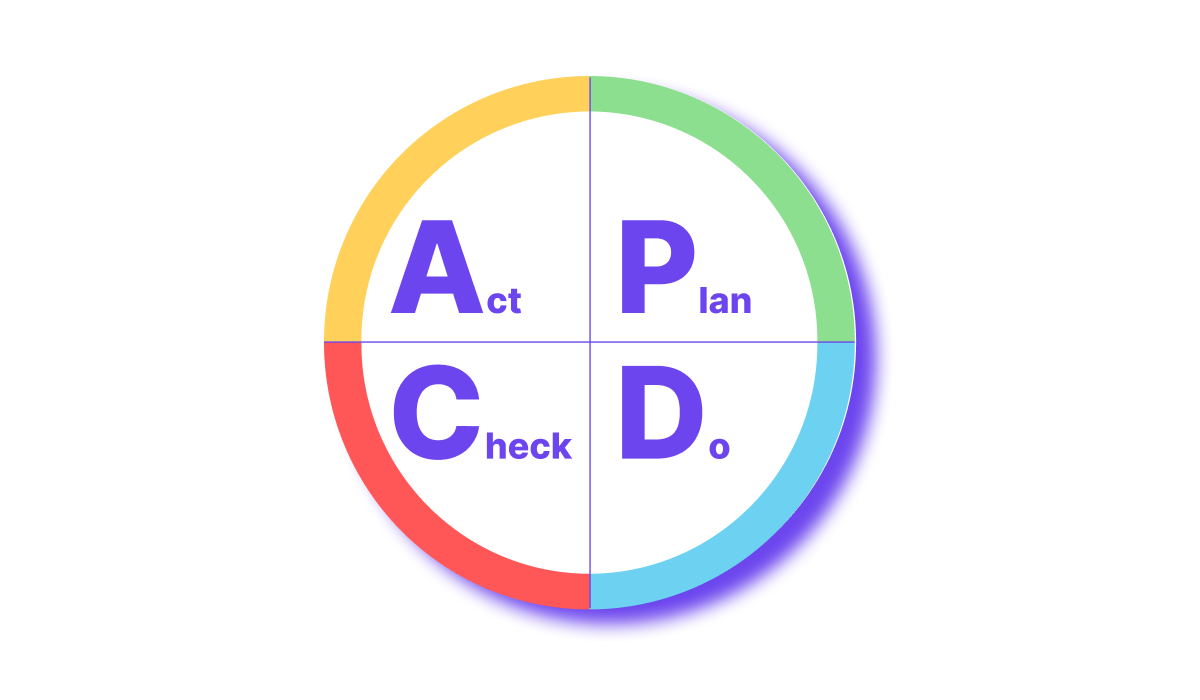
Are you ready to kick-start your continuous improvement journey?
If so, the Plan Do Check Act (PDCA) cycle is the perfect place to begin.
PDCA provides a structured and repeatable method to solve problems sustainably, empowering you to identify root causes and implement long-term solutions.
To make things even easier, I’ve created a free PDCA problem-solving template.
You can download it here in A4 and A3 formats:
Download the PDCA Template (PDF) - DIN A4
Download the PDCA Template (PDF) - DIN A3
Once you have the template, follow this step-by-step guide to put it into action.
Step-by-step guide to Using the PDCA template
Here's how to put your template into action and start driving measurable improvements on your shop floor.
1. Establish your starting point
Start by analyzing your processes and identifying one specific issue to tackle. Focus on areas with measurable impacts, like process bottlenecks or low OEE performance.
2. Develop the “Plan”
Use the template to define the problem or opportunity and be as specific as possible. If your problem can be dealt with with a preliminary fix, then note it down as a starting point. Now deep dive into identifying the root cause of the problem through the fishbone diagram exercise.
3. Execute the “Do” phase
With your root cause analysis completed, create a plan of activities, start collecting additional data, and conduct further analysis. Brainstorm all possible countermeasures and use the impact and effort matrix to prioritize your solutions to find the best-fit or quick-win solutions.
4. Verify in the “Check” phase
Once you have prioritized your solutions, start to create interim Key Performance Indicators (KPIs) to measure the performance of the solution and whether it lives up to the set expectations. The monitoring period can vary depending on the complexity of the problem. Map out any deviations from the KPI’s and determine what their root cause is.
5. Conclude with the “Act” phase
If your solutions succeed, make sure to update relevant documentation, SOP's, guidelines, and training material to reflect the changes and make them standard practice. Make sure to sign off and communicate the changes to the relevant stakeholders.
6. Make PDCA continuous
To make sure that continuous improvement becomes an integral part of daily operations, make sure to integrate PDCA activities into daily meetings and reporting and create a good follow-up cadence. Create a library for all completed PDCA activities as documentation and future reference points.
Additional tools to apply during PDCA activities
To strengthen your root cause problem-solving, consider using some of these tools as well:
Pareto Analysis: Gather data (e.g., with Factbird’s Production Insights App) and create bar charts to identify the biggest contributors to the problem.
Failure Mode and Effect Analysis (FMEA): Use a structured table to evaluate potential failures, their impact, and control measures. Assign Risk Priority Numbers (RPNs) to identify high-risk areas.
5 x Why Analysis: Uncover the root cause by asking “Why?” repeatedly until the fundamental issue becomes clear.
How Factbird supports PDCA
Factbird complements PDCA by providing the real-time data you need for effective continuous improvement.
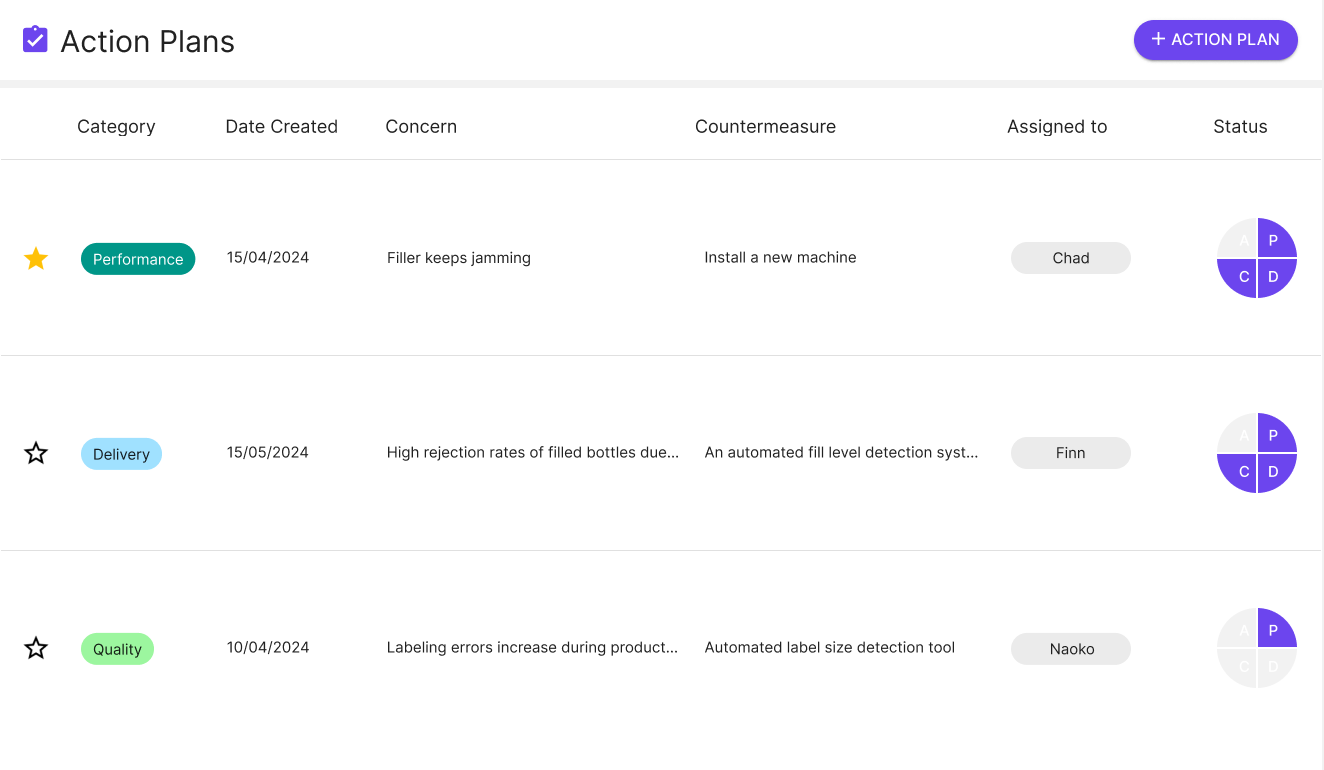
Factbird’s Knowledge Excellence App streamlines the PDCA process by digitizing problem-solving tasks, tracking activities, and centralizing data collection and analysis.
Here’s how Factbird enhances each PDCA phase:
- Plan: Identify issues using Factbird's real-time data insights.
- Do: Use Factbird's tools to execute data-driven improvement activities.
- Check: Monitor KPIs and deviations effortlessly with Factbird's analytics.
- Act: Store and share findings, creating a knowledge database for future projects.
With Factbird's Action Plans, you can:
- Keep teams aligned with data-driven activities across sites.
- Digitize continuous improvement tasks for better visibility and management.
- Preserve problem-solving knowledge to train teams and accelerate efficiency.
Want to see how Factbird can help your team? Book a no-obligation demo here.
Lean management training
Looking to dive deeper into continuous improvement and problem-solving techniques like PDCA?
Check out our Lean Management Training service to equip your team with the skills they need for success.
Learn more about Lean Management Training
Check out our podcast on PDCA
For more insights, listen to our podcast episode, "How to Structure Improvements with PDCA", where we break down how PDCA drives sustainable results in manufacturing.
Thanks for reading this article, and I hope you find the template helpful.
Remember, continuous improvement is a journey, not a destination—so start your first PDCA cycle today and take the first step toward lasting success on your shop floor.