Making sense of manufacturing sensors
By turning manufacturing events into actionable data, manufacturing sensors help you streamline and reduce waste. Learn more in our simple guide to sensors.
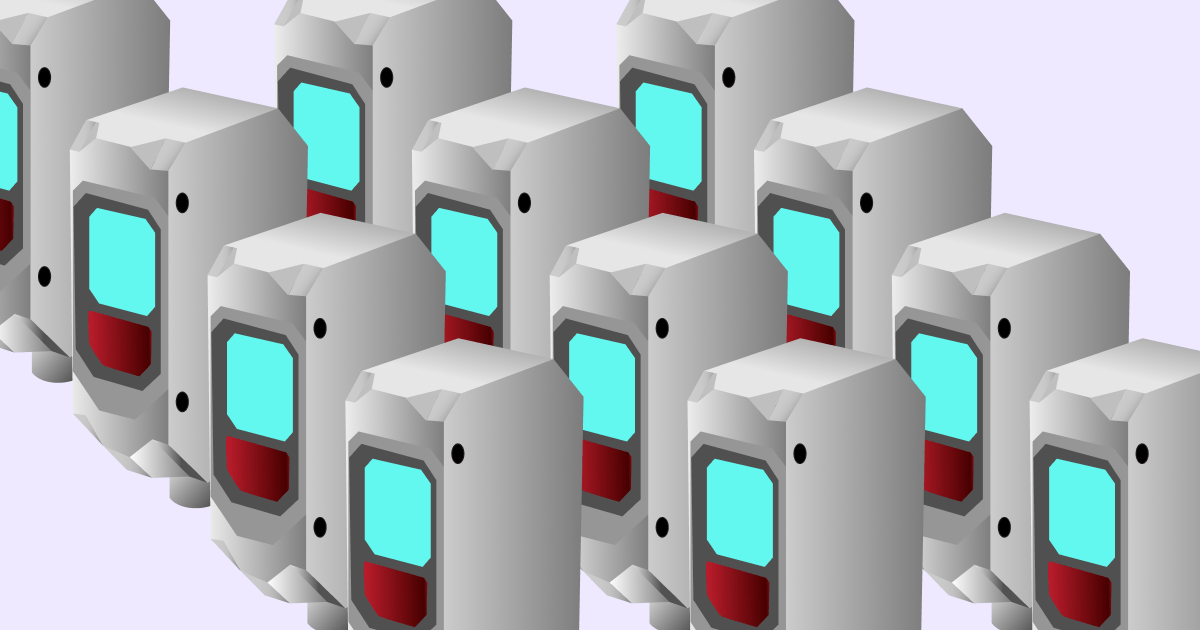
In manufacturing, a lot of your time is taken up with trying to make production more efficient. Guesswork and experience will get you part of the way, but to make the gains you need to stay ahead, you’ll want to use real data from your production lines.
And to get the manufacturing data you want, you’ll need manufacturing sensors.
Production managers, process engineers, and plant managers around the world have already incorporated Manufacturing Intelligence Solutions like Factbird to extract value from their data. And a key part of succeeding at this is strategically using sensors to get a picture of what is happening on production lines.
In this article, we’ll delve into manufacturing sensors (aka manufacturing sensors) and examine their crucial function in monitoring and optimising production activities on the factory floor.
What is a sensor?
Sensors are pieces of equipment that sit at the very edge of where you can get data. In manufacturing, sensors are the eyes and ears of modern manufacturing facilities.
In essence, a sensor is a device that captures real-world data in it’s raw form, meaning physical phenomena such as temperature, pressure, moisture, sound, current, or light.
A sensor then typically converts this data into an output signal for use in other electronics, monitoring the world at a minute level and feeding back information into IoT systems for analysis and action.
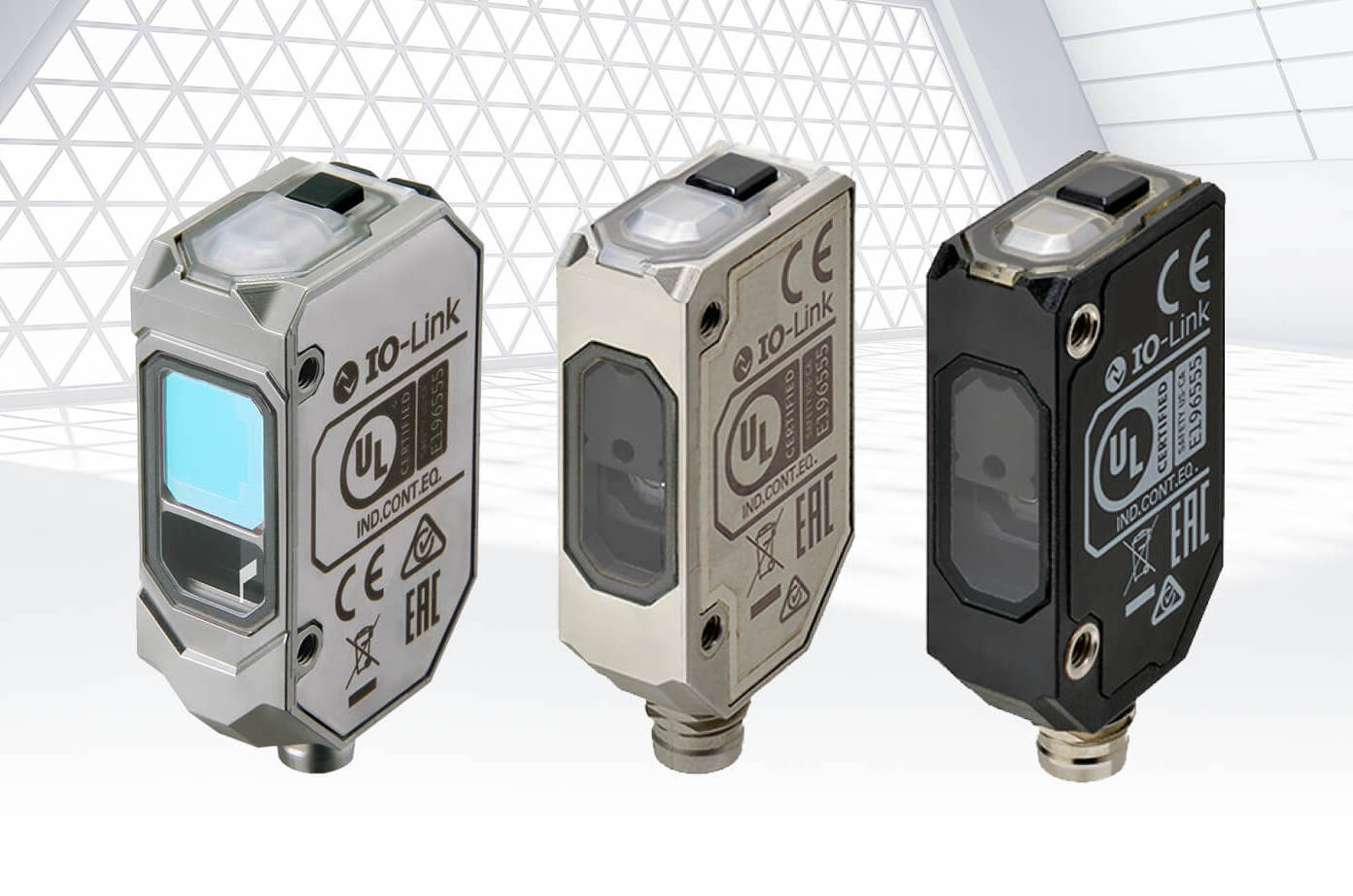
The data collected and analyzed from sensors can be used to monitor, control, and optimize manufacturing processes, driving efficiency, safety, and quality improvements. Manufacturing sensor types are diverse and tailored to specific applications and industries, but they all share a common goal: improving the way we approach manufacturing.
Where are sensors used?
The more manufacturing sensors we put in manufacturing settings to capture data, the more capability we have to show and understand patterns.
They aren’t a new invention, with the “electric tele-thermoscope”, aka thermostat, patent being granted in the US way back in 1883. They’ve come a long way since then and are rapidly getting cheaper, smaller, and far more abundant.
Looking at cars, the U.S. Department of Energy Office of Scientific and Technical Information reported that in 2020 “An average new car has between 60 and 100 sensors, which could double within 6 years.” These sensors are placed throughout the car, including in the fuel injection system, gearbox, fuel tank, wheels, and airbags.
In manufacturing, sensors are used to monitor and control various production processes. Here are some examples of how sensors are put to use on production lines:
Production input and output monitoring can be done with counting sensors, typically photoelectric (light) and inductive sensors, that monitor the numbers of items produced as well as scrap and items that need to be reworked.
Packaging processes are a common cause of bottlenecks, and sensors that accurately measure distances and positioning help reduce packaging problems.
Bottleneck analysis uses video cameras to identify the root cause of stops by viewing timestamped videos.
Condition monitoring of machines with vibration and temperature sensors that detect whether a piece of equipment behaves abnormally.
Consumption monitoring of utilities such as electricity and gas to identify inefficiencies and reduce costs.
Employee safety improvements by using video cameras to analyze what went wrong in the event of an accident.
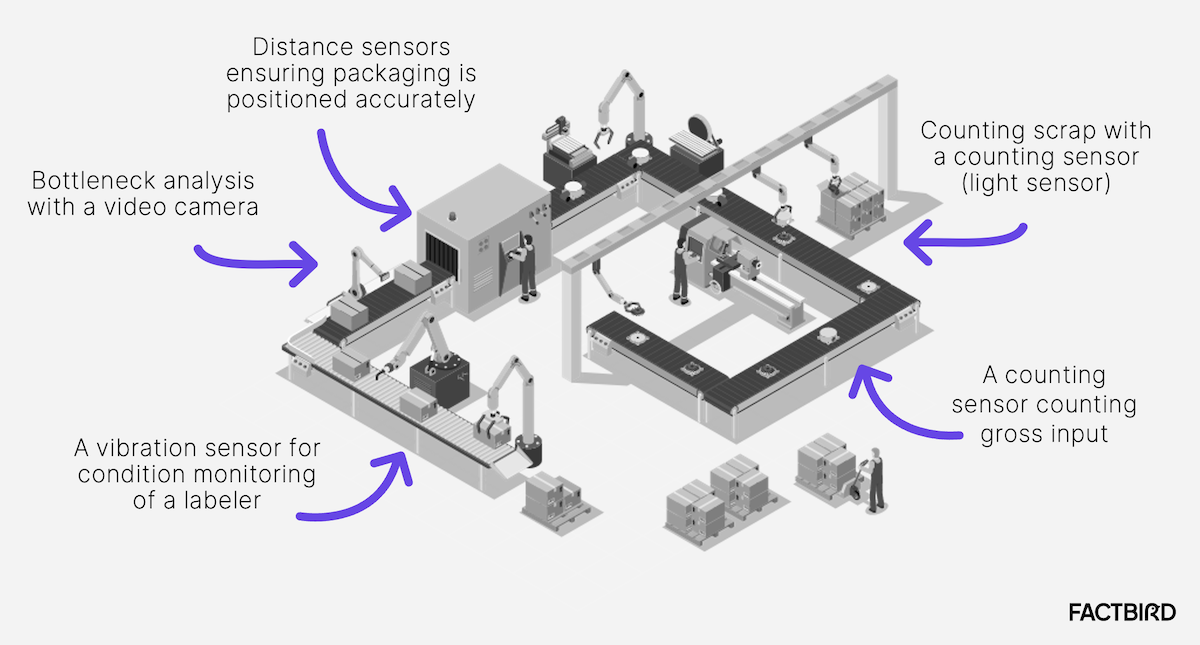
Which types of sensors are used in manufacturing?
Manufacturing sensors play a pivotal role in boosting efficiency through automation, a major goal of Industry 3.0 and 4.0.
They enable the detection, measurement, analysis, and processing of various changes, such as shifts in position, length, height, external factors, and dislocations within manufacturing production facilities.
Smart factories leverage these sensors to monitor real-time output, while automated control systems help reduce potential maintenance costs. Additionally, digitalization enhances production flexibility, providing a competitive edge to advanced manufacturing firms.
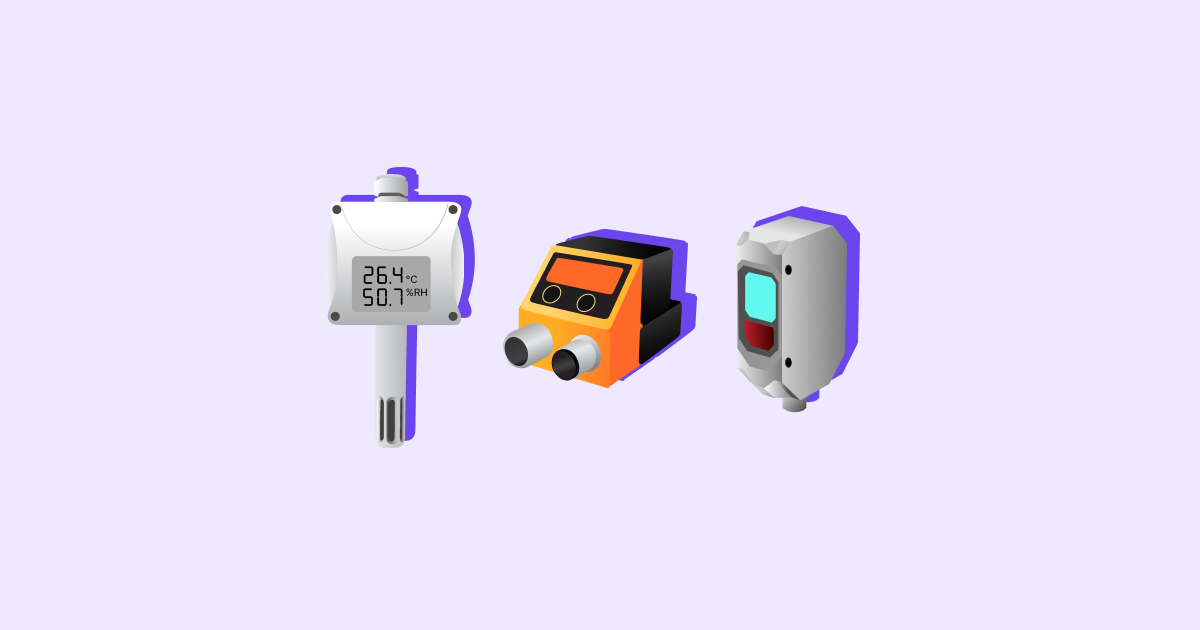
There are various types of sensors on the market, some of which are mass-produced and readily available. The common types of sensors that you will find today are:
- Position sensors can measure the movement of an object or its position relative to a reference point.
- Pressure sensors are essential for monitoring pressure changes in fluids or gases, ensuring safe and efficient operations.
- Flow sensors are crucial for measuring the flow rate of fluids or gases within a system, optimizing throughput, and reducing downtime.
- Temperature sensors measure and monitor temperature variations within manufacturing processes.
- Force sensors detect mechanical forces such as tension, weight, and compression.
- Proximity sensors are key to detecting the presence or absence of an object without physical contact.
- Level sensors keep track of liquid or solid material levels within containers or vessels.
- Vision sensors are integral for capturing images for analysis, such as verifying product quality and streamlining inspection processes.
These sensors find applications in a wide range of manufacturing industries, including pharmaceutical, food and beverage, aerospace, automotive, electronics, and textiles.
Manufacturing sensors as part of the IoT stack
According to McKinsey, "The Internet of Things (IoT) describes physical objects embedded with sensors and actuators that communicate with computing systems via wired or wireless networks—allowing the physical world to be digitally monitored or even controlled.”
From this definition, it’s clear that sensors are a vital part of IoT, Industrial IoT (IIoT), M2M, or whatever you want to call this phenomenon.
A typical IoT system is made up of five parts:
- Sensors convert physical phenomena into electrical signals.
- Edge devices perform tasks such as translating, storing, and processing the signals for communication with a network.
- Connectivity which sends the data to the cloud, such as cellular, LoRaWAN, Wi-Fi, and Ethernet.
- The cloud is software that processes the data and then performs actions such as sending alerts. NB on-premise solutions still occur in manufacturing but are less and less common.
- A user interface is how people view the data that started all the way back at the sensor and has been processed by the cloud application.
Manufacturing sensors might be the eyes and ears of your facility, but it's the data they generate that holds real value. Here’s how a typical setup looks when using Factbird’s plug-and-play Manufacturing intelligence solutions.

Manufacturing Intelligence Solutions like Factbird enable you to collect, store, and analyze data from various sensors, turning raw information into actionable insights.
This data management process involves four key components:
- Providing context for the sensor data (time, location, and process state) to better understand the information and make more informed decisions.
- Filtering and prioritising data based on importance allows you to focus on the most critical aspects of your operations.
- Ensuring consistency in data format and units to promote smooth communication and interoperability between different systems and sensors.
- Converting raw sensor data into meaningful insights that empower you and your team to make informed decisions and take appropriate actions.
What do sensors help improve?
Investing in manufacturing sensors can yield significant benefits for your operations.
Companies collecting and analyzing production data enjoy enhanced productivity through real-time monitoring and optimization of processes, which increase efficiency and reduce downtime.
Improved quality can also be achieved through precise control of manufacturing processes, resulting in higher-quality products with fewer defects.
Increased safety is another advantage, as early detection of hazardous conditions or equipment malfunctions helps prevent accidents and protect employees.
Sensors also contribute to reduced waste by optimizing resource usage and minimizing waste, leading to more sustainable and cost-effective operations.
Finally, monitoring equipment health and performance allows for preventive maintenance and predictive maintenance, allowing for increasingly accurate prediction of potential failures and proactive maintenance, ultimately reducing downtime.
Peering into the future of sensors
As Industry 4.0 and now Industry 5.0 continue to shape the manufacturing landscape, sensors will play an increasingly important role in driving innovation and efficiency.
Sensors help enable better productivity that Industry 4.0 demands while also aiding the people and environmental focus of cutting-edge industry 5.0 concepts.
Anticipated advancements in manufacturing sensor technology include:
- Continued miniaturization will enable the development of smaller, more compact sensors for integration into a wider range of equipment and applications.
- Advanced materials, such as graphene and nanocomposites, will provide increased sensitivity, durability, and versatility.
- The expansion of wireless sensor networks will improve real-time data collection, analysis, and communication across and between manufacturing facilities.
- The integration of artificial intelligence (AI) and machine learning technologies with manufacturing sensor data will enable advanced analytics and predictive capabilities, leading to smarter and more autonomous manufacturing processes.
Learn more about manufacturing sensors
For a deeper dive into the world of manufacturing sensors, check out this Manufacturing Matters podcast episode: What to consider when purchasing manufacturing sensors. In it, you will learn about the critical factors involved in selecting the right sensors for manufacturing applications. The episode emphasizes the importance of balancing cost and performance to prevent costly downtime and enhance operational efficiency.
Closing thoughts
Manufacturing sensors have come a long way since their inception, becoming an indispensable tool for manufacturing executives, production managers, and plant managers to monitor, control, and optimize their operations.
By investing in easy-to-use Manufacturing Intelligence Solutions like Factbird, organizations can harness the full potential of these sensors, transforming raw data into actionable insights that immediately drive efficiency, quality, and profitability.