What to consider when purchasing manufacturing sensors
Manufacturing Matters Ep. 17
Featuring David Pavone, Account Manager at Factbird
Release Date: November 11, 2024
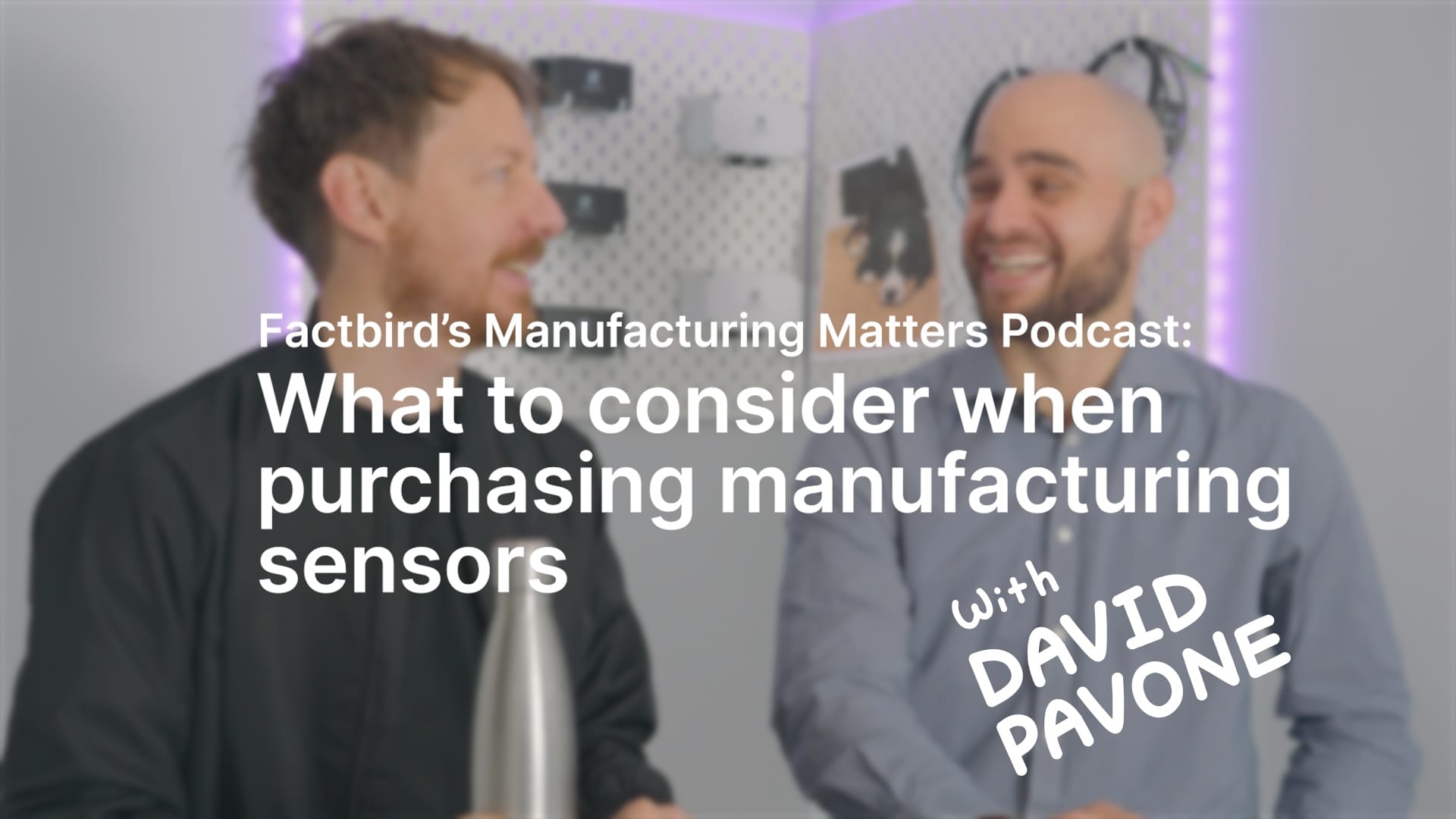
Summary:
- Balancing cost and performance is essential; cheap options can lead to expensive failures and downtime.
- Consider what you need to detect and assess environmental conditions like high heat, wash-down areas, high pressure, and electromagnetic interference.
- Focus on total cost of ownership over upfront price to avoid hidden costs associated with using the wrong sensors.
In episode 17 of Factbird's Manufacturing Matters Podcast, we delve into the critical factors to consider when selecting sensors for manufacturing environments.
To get a better understanding of the ins-and-outs of sensor selection, I sat down with David Pavone, who is currently an Account Manager at H.H. Barnum Company, a premier distributor of products, solutions, and controls for factory automation in the US. With extensive experience in manufacturing sensor technology and the broader manufacturing industry, David shared insights on how balancing cost and performance can significantly impact operational efficiency and profitability.
The importance of balancing cost and performance
David emphasizes that while it might be tempting to opt for the least expensive sensors on the market, this approach can lead to higher costs in the long run. The initial price tag doesn't account for the hidden expenses associated with sensor failure, downtime, and maintenance.
In many manufacturing contexts, even a minute of downtime can result in substantial financial losses, far outweighing the savings from purchasing cheaper sensors.
Real-world example:
In the podcast, David shares a compelling example from his experience in the automotive industry in a high-heat environment where welding and stamping take place.
In a setting like this, the use of cheap, unsuitable sensors led to frequent failures. Each failure resulted in approximately 15 minutes of downtime, and with downtime costs reaching up to $22,000 per minute, a single sensor failure could cost north of $300,000.
He explains:
"In that industry specifically, I've worked with plants that would see $22,000 in downtime cost per minute. To replace a cable and a sensor, you're talking about 15 minutes. You're losing hundreds of thousands of dollars in production. Yes, you saved $200 on the sensor, but if you replace it six times in the last year at 15 minutes a piece, we've lost a lot more money than we actually gained on buying the cheaper product."
This scenario underscores the importance of considering the total cost of ownership rather than just the upfront cost.
Key factors to consider when choosing sensors
When selecting sensors for your manufacturing processes, David suggests focusing on two main attributes:
1. Understanding what you are trying to detect
Type of target: Determine whether the sensor needs to detect standard (opaque) targets or transparent ones. Standard targets are generally easier to detect, allowing for a wider range of sensor options. Transparent targets, like glass or clear plastic, require specialized sensors that can accurately detect them without false readings.
Detection requirements: Consider if the application involves detecting contrast differences, such as registration marks on packaging materials. This might necessitate sensors with advanced capabilities or specialized vision systems for precise detection.
2. Assessing the environmental conditions
Now you’ll want to consider the type of environment your sensors are operating in and what situations they will be exposed to. Here are some common examples.
High-heat environments:
Applications involving welding or metal stamping generate extreme heat and flying molten metal (sparks). Standard sensors may fail under these conditions due to the intense heat and physical impact.
Invest in sensors with heat-resistant materials, such as full stainless-steel construction and Teflon-coated cables. These sensors are designed to withstand high temperatures and physical abrasion.
While these specialized sensors may cost around $250 each—significantly more than a standard $30 plastic sensor—the reduction in downtime and maintenance costs justifies the investment. As David notes, saving $200 per sensor doesn't compare to the potential loss of hundreds of thousands of dollars from a single downtime event.
Wash-down environments:
In the food and beverage industry, sensors are exposed to frequent cleaning with high-pressure water and chemicals. Standard sensors may not withstand these conditions, leading to water ingress and corrosion.
Here, you should use sensors with a high Ingress Protection (IP) rating, such as IP69K, which are hermetically sealed to prevent water and chemical damage.
High-pressure environments
Processes involving tanks or vessels under pressure require sensors that can withstand significant force without compromising performance.
High-pressure environments can be found in the extreme demands of military applications, for example. David elaborates, “I did an application for military missiles on a submarine. You're in a submarine under extreme pressure, and they need to be able to see that the missile was loaded into the actual firing chamber for that submarine. Being able to sense and make sure that that missile has been properly positioned in an environment that's extremely high pressure is something only a very specialized solution would be able to enable."
That’s interesting, but for typical manufacturers, you would find high-pressure environments in tanks where you have liquids like water or milk siloed.
According to David, “At the end of the day, the bottom of that tank is going to have a large pressure buildup. So, you're going to want to ensure if you're cutting a hole in that tank and using that sensor as kind of a floodgate stop but also something to sense that the material is there, you would want a high-pressure sensor in an instance like that."
Here, using the appropriate sensors prevents failures that could lead to leaks, spills, or even catastrophic equipment damage, all of which can be costly and dangerous.
Electromagnetic Interference (EMI) environments
EMI can significantly disrupt sensor performance, leading to false readings, erratic behavior, or complete sensor failure. To mitigate EMI effects, it's crucial to select sensors with built-in EMI shielding or those specifically designed to operate in high-EMI environments. Using shielded cables, proper grounding techniques, and ensuring adequate distance between sensors and EMI-generating equipment can also help reduce interference.
EMI is commonly generated by equipment such as welding machines, CNC machines, and X-ray equipment. David elaborates, “One that I've specifically run into is within the welding industry, but also when you're buying machining or CNC equipment. Electromagnetic interference becomes a problem at times, and this is specifically through the wiring.
“Certain machines—and this can also happen in food and beverage near X-ray equipment—you always have that at the end of the line for checking. There might be an EMI field being created by that machine. In that instance, technology around it starts to get disturbed from a signal perspective.
“There are specialized solutions that can see through that electromagnetic interference, specifically used in those types of applications. Because again, if your sensor is triggering a lot more than you wanted to, which will happen if there's magnetic fields, it's bad. You want your data to be reliable and things to operate when they're supposed to.”
Recognizing EMI can be a problem, testing for it, and proactively addressing EMI challenges through appropriate sensor selection will put you in a better position to avoid costly disruptions.
Beware of the hidden costs of choosing the wrong sensor
David highlights that the true cost of a sensor isn't just the purchase price but includes maintenance, downtime, and the potential impact on production quality.
For instance, in high-speed production lines, a malfunctioning sensor can cause mislabeling or improper packaging, leading to waste and rework.
He points out, "In high-volume production manufacturing facilities, the downtime is very costly. You have so many other moving parts happening on your line; you don't want to be worrying about sensors."
By investing in the appropriate sensors for each specific application and environment, manufacturers can avoid these hidden costs and improve overall efficiency.
Brand loyalty and standardization
Many manufacturers develop brand loyalty for sensors, standardizing on a particular manufacturer's products across their facilities. This practice simplifies maintenance, inventory management, and training. Maintenance teams become proficient with a specific sensor type, reducing the time required for replacements and adjustments.
However, David advises that while standardization has its benefits, it's crucial not to let brand loyalty overshadow the need for the right sensor for each application. Assess each use case individually to ensure the selected sensor meets all performance and environmental requirements.
Practical advice for manufacturers
Here is a summary of key recommendations when selecting manufacturing sensors:
Conduct thorough testing: Before fully integrating a new sensor type, perform extensive testing in the actual production environment to identify potential issues.
Consider the total cost of ownership: Evaluate the long-term costs associated with maintenance, downtime, and replacements, not just the initial purchase price. Investing in higher-quality sensors appropriate for your applications will prevent costly downtime and maintenance issues.
Stay informed on technological advances: Sensor technology continually evolves. Keeping informed about new developments can provide opportunities to enhance performance and efficiency.
Work with trusted suppliers: Engage with reputable sensor manufacturers or distributors who can provide expert guidance and support tailored to your needs.
Don’t be cheap
Selecting the right sensors is a critical decision that can significantly affect production efficiency, product quality, and operational costs.
By carefully considering both the detection requirements and the environmental conditions, manufacturers can choose sensors that offer the best balance of cost and performance.
As David succinctly puts it:
"Don't be cheap because it ends up being more expensive. Investing in the appropriate sensor technology is not just a purchase—it's a strategic decision that supports the long-term success and competitiveness of your manufacturing operations."
Stay connected with the podcast
For more insights into how customer success can transform your manufacturing operations, subscribe to Factbird’s Manufacturing Matters podcast on Spotify, Apple Podcasts, YouTube, Amazon Music, or your favourite podcast platform.
If you have questions or topics you'd like us to cover, feel free to reach out via LinkedIn or email.