The trends shaping manufacturing shop floors in 2025
Manufacturing Matters Ep. 17
Featuring Søren Schønnemann, CEO at Factbird
Release Date: November 25, 2024
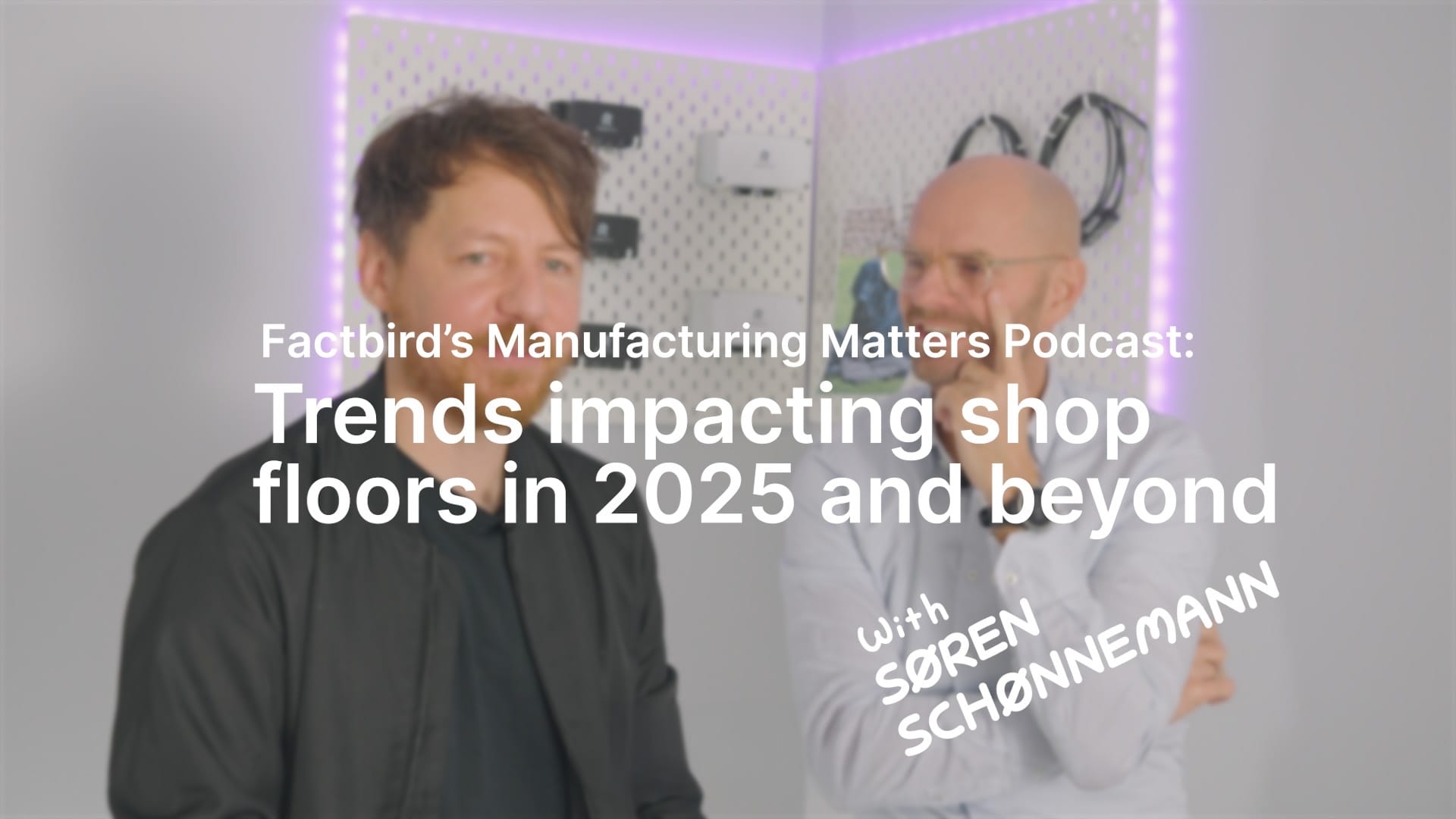
Summary:
- Geopolitical uncertainties, an aging workforce, cybersecurity threats, sustainability concerns, and competitiveness are major macro trends affecting manufacturing.
- On the shop floor, these translate into challenges like maintaining operational efficiency, integrating legacy equipment with new technologies, data silos, and skill gaps among workers.
- Manufacturers are focusing on holistic IT/OT integration, phased technology implementation, open systems for better integration, knowledge capture to mitigate skill gaps, and exploring AI and machine learning to stay competitive.
In episode 18, the season 1 finale of Factbird's Manufacturing Matters Podcast, we explore the key trends that will impact manufacturing shop floors in 2025 and beyond.
To do this, I sat down with Søren Schønnemann, CEO of Factbird, to discuss how macro-level risks and challenges are shaping the future of manufacturing and what that means for the most important part of a manufacturing operation: the shop floor.
Macro trends affecting manufacturing
In the podcast, Søren highlights several macro trends that are influencing the manufacturing industry:
1. Geopolitical and economic uncertainties
Global events such as conflicts in Europe and the Middle East, potential risks in Asia, and changing political landscapes in the US create uncertainties that impact supply chains, production costs, and market stability.
"There's certainly something about the geopolitical, economic challenges in the world that we live in today. Something that's on the mind of pretty much all of our enterprise customers and customers in general," Søren notes.
2. Aging workforce and skill gaps
The manufacturing sector is facing a significant shift as experienced workers retire. The new generation entering the workforce tends to have less loyalty to employers and changes jobs more frequently, leading to challenges in retaining institutional knowledge.
"Manufacturing traditionally has benefited from a high degree of skilled workers and a lot of tacit knowledge on the shop floor. That generation is slowly moving out of the job market, being replaced by a new generation that does not have the same loyalty to their employer as the former, and they're simply changing jobs more rapidly," Søren explains.
3. Cybersecurity threats
With the rapid deployment of Industry 4.0 technologies, manufacturers are increasingly vulnerable to cybersecurity risks. Open networks and interconnected systems can leave doors open for cyberattacks.
"By deploying technology really fast and maybe without, let's say, the master plan, you're opening doors that you should really not leave open. And that's, you know, we see a lot of conversation about, okay, how do we clean that up? Where should we be?" Søren warns.
4. Sustainability and ESG concerns
Environmental, Social, and Governance (ESG) considerations are becoming central to manufacturing strategies. Governments are imposing new regulations to combat climate change, and manufacturers are seeking ways to reduce their environmental footprint.
"I don't think anyone can shy away from the fact that sustainability and ESG is on everyone's mind. If you believe in climate change or not, something is happening," Søren says.
5. Competitiveness
Staying competitive is a constant concern. Manufacturers must deliver the right products at the right quality and price while being agile and responsive to market changes.
"Let's be honest, we all serve a shareholder of sorts somewhere. Even the biggest of companies serve a shareholder or a set of shareholders. And with the few exceptions, they're all in it to make money and make a profit," Søren emphasizes.
Translating macro trends to shop floor challenges
The macro trends described above manifest as specific challenges on the shop floor:
1. Maintaining operational efficiency
To stay competitive, manufacturers need to run smooth operations with healthy cost levels. However, identifying where to improve can be difficult due to fragmented data and unclear benchmarks.
"At the end of the day, if you want to stay relevant and solve all of the other challenges, you got to start with figuring out how you run a smooth operation. How do you have the healthy level of cost, and how are you as effective or efficient as an organization as possible?" Søren points out.
2. Integrating legacy equipment with new technologies
Many factories use equipment that is decades old, which doesn't always integrate well with modern IT systems. This leads to data silos and hinders the ability to have a holistic view of operations.
"Legacy equipment combined with overcomplicated new IT systems creates challenges because they don't speak well to each other," Søren explains. "How can you run from top down an efficient factory if you don't have a holistic overview of your facilities?"
3. Addressing skill gaps and workforce mobility
The high turnover of employees means less experienced workers are operating complex machinery, potentially leading to increased errors and downtime.
"It's quite remarkable, actually, to be on the shop floor, and you can tell on, let's say, maintenance or the operators, if something is about to go wrong before it happens. And you just, you could just go: how do you know?" Søren says.
Capturing that tacit knowledge becomes crucial as experienced workers leave and new ones take their place.
4. Overcoming employee resistance to new technologies
Introducing complex new systems can overwhelm operators who are already managing multiple tasks. Without proper training and intuitive interfaces, employee buy-in can be low.
"In order to get employee buy-in, in order to really make real changes on the shop floor, you need to have something that resonates with the operator on the level where the operator is at and does the trick, right? And slim it down," Søren notes.
Trends shaping the future of manufacturing
Looking ahead to 2025 and beyond, Søren identifies key trends that will shape manufacturing:
1. Holistic IT/OT integration
Manufacturers are moving towards integrating Information Technology (IT) and Operational Technology (OT) systems to create a more unified and efficient operation.
"I'm sensing a strong discussion and requirement around IT/OT integration to simplify things. It needs to be more holistic," Søren predicts. "There's going to be fewer systems that can do more, in order to mitigate some of the challenges that we talked about related to complexity, related to cybersecurity, related to costs, related to employee buy-in, and what have you."
2. Phased implementation of technology
Rather than deploying large, complex systems all at once, manufacturers are adopting a step-by-step approach to technology implementation. This allows for better employee adaptation and demonstrates noticeable outcomes at each stage.
"We're seeing this step-by-step approach in introducing new technologies. It's not just force-feeding new technology to the employees, but rather taking granular, phased approaches in the rollout where you're making sure that the adoption is high, the outcome is noticeable," Søren explains.
3. Open systems and better integration
There's a growing demand for systems that can easily integrate with others, breaking down data silos and enabling smoother operations across different departments and functions.
"Another thing we're seeing is a firm requirement from our customers, but also a trend in the market is more open systems. So rather than seeing that as a hierarchical setup, it needs to be more holistic or circular and integrated," Søren states.
4. Knowledge capture and employee retention
Manufacturers are focusing on ways to capture institutional knowledge and onboard new employees more effectively to mitigate the impact of high turnover rates.
"Another expectation slightly outside this, but then again related, is initiatives to capture knowledge, retain people, and make sure that we address the fact that people stay shorter," Søren says.
5. Exploration of AI and machine learning
While still in its early stages, the use of Artificial Intelligence (AI) and Machine Learning (ML) is a hot topic. Manufacturers are beginning to explore how these technologies can optimize operations and provide a competitive edge.
"Another trend that everyone's talking about is, what about artificial intelligence? What about machine learning? Hot topic. And it's there, right? I think it's definitely there. There's certainly a lot of talk about it," Søren acknowledges.
However, he cautions that it's important to approach AI realistically:
"If we're talking about the transition from industry 4.0 to industry 5.0, artificial intelligence can be the bridge. But where do you get started as an organization? That's the tricky thing. You have all the data. How do you set the data up for success?"
Practical steps for manufacturers
Here’s a quick summary of practical steps offered to you as you navigate the trends and risks discussed in this podcast:
- Simplify technology for operators: Choose user-friendly systems that enhance productivity without overwhelming employees.
- Invest in training and onboarding: Develop programs to quickly bring new employees up to speed and capture essential knowledge from experienced workers.
- Focus on data integration: Break down silos by adopting open systems that allow for seamless data flow across the organization.
- Adopt a phased approach to innovation: Implement new technologies in stages to ensure high adoption rates and measurable success.
- Stay informed on technological advances: Keep an eye on developments in AI and ML, but approach them with realistic expectations.
- Be pragmatic: Use manufacturing software that is easy to use and offers quick time to value rather than has every feature on the planet for your needs and more. Implementing overly complex systems is doomed to failure.
Conclusion
Manufacturing in 2025 and beyond will be shaped by a combination of macro trends and shop-floor realities. By understanding these forces and proactively adapting, manufacturers can position themselves for success.
Søren emphasizes the importance of focusing on the operators and making technology accessible:
"It's not good enough just to have the strategy and just to have the defined process; you've got to get the people into the equation. You've got to think about the operators that's going to do this every day."
By simplifying processes and focusing on what's essential, manufacturers can empower their workforce and navigate the challenges ahead.
Stay connected with the podcast
For more insights into the future of manufacturing, subscribe to Factbird’s Manufacturing Matters podcast on Spotify, Apple Podcasts, YouTube, Amazon Music, or your favorite podcast platform.
If you have questions or topics you'd like us to cover, feel free to reach out via LinkedIn or email.