Unlocking production efficiency with condition monitoring
Manufacturing Matters Ep. 16
Featuring Sterre Van Empelen, Account Manager at Factbird
Release Date: October 28, 2024
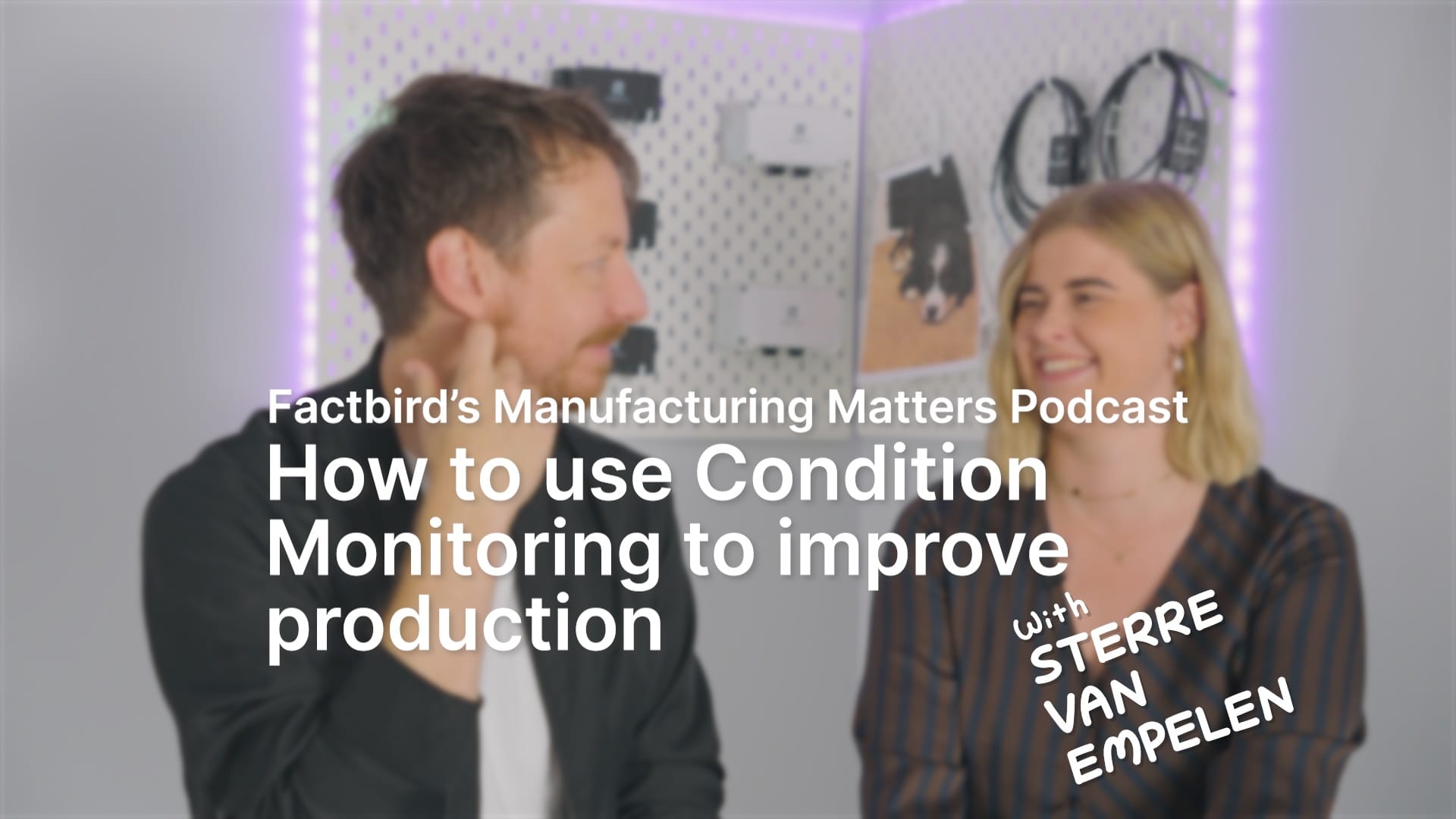
Summary:
- Condition monitoring tracks parameters like temperature, vibration, and humidity for optimal production quality.
- Monitoring upstream processes helps manufacturers address issues early, ensuring efficiency and minimizing waste.
- Benefits include predictive maintenance, quality control, process optimization, and energy savings across manufacturing.
- Retrofitting older equipment and breaking down data silos are key challenges to implementing condition monitoring.
In the latest episode of Factbird's Manufacturing Matters Podcast, we explore the increasingly crucial topic of condition monitoring and its potential for optimizing production processes. Joining us once again is Sterre Van Empelen, Factbird’s Account Manager for Benelux, who shares insights into how manufacturers can use condition monitoring to improve efficiency, reduce waste, and enhance product quality.
What is condition monitoring?
Condition monitoring is the practice of tracking key parameters—like temperature, vibration, and humidity—throughout the production process to ensure optimal conditions are maintained.
Sterre explains that condition monitoring is not only about checking on machinery for maintenance. She works with many food and beverage manufacturers that use condition monitoring to monitor product quality consistently from start to finish.
A great analogy she uses is baking, where constant checks are needed to make sure the dough rises perfectly and the oven stays at the right temperature.
By keeping a close eye on these parameters, manufacturers can ensure that their products meet high-quality standards, all while avoiding potential faults that could slow down production.
Why is condition monitoring more important than ever?
As Sterre highlights in the podcast, the role of condition monitoring has become increasingly essential in today’s manufacturing environment.
With a rising focus on sustainability and cost competitiveness, condition monitoring brings several key benefits to the table:
Predictive maintenance: By detecting signs of wear or malfunction early on, companies can avoid costly machine breakdowns and unplanned downtime. Predictive maintenance is perhaps the most well-known application of condition monitoring, allowing companies to detect early signs of wear or malfunction.
Quality control: Monitoring variables like temperature or humidity in real-time while producing food and beverage products helps you catch problems before they become critical while also assisting in assuring quality standards are met.
Process optimization: Consistent monitoring helps optimize machinery and processes. By monitoring machines and environmental conditions, you will have more valuable data for understanding inefficiencies to optimize your processes.
Waste reduction: Early detection of issues helps minimize waste, reducing both raw material waste, improving sustainability, and lowering operational costs.
Energy efficiency: Keeping track of energy consumption can lead to more efficient use of resources, a critical factor in reducing operational costs and improving sustainability.
Upstream vs. downstream condition monitoring
Sterre also emphasizes that many manufacturers do a great job of collecting data at the end of the production line but often struggle with monitoring conditions at the beginning.
At the end of the line, it is relatively simple to count units produced, be it the packages coming out or the pallets going into the truck. Before that, in upstream production, it’s more challenging to track inputs like liquids or powders, leading to many manufacturers lacking data in this area.
Understanding these upstream processes is critical to truly optimizing overall efficiency, and this is an area where condition monitoring techniques like setting alarms and ensuring certain parameters are met can help you increase efficiency by catching issues early.
Condition monitoring techniques
In the episode, Sterre walks us through common things that people measure when using condition monitoring, each offering data on valuable condition parameters.
Vibration analysis: Monitoring vibration levels to detect equipment wear or mechanical issues before they become critical. But vibrations are also used in some equipment to, for example, separate dough in baking, making it hard to get the parameters right.
Energy consumption monitoring: Tracking power usage to ensure machines are running efficiently and to identify areas for energy savings. Our customer Danfoss used energy monitoring to analyze the standby power drain of their machines, leading to a 33% reduction in equipment energy consumption.
Flow rate monitoring: Measuring the flow of liquids or gases to ensure that the correct quantities are being used in production; this can be oil going through pipes for food or a vital chemical agent being applied to a composite in the correct amount so that it forms as intended.
Temperature and humidity monitoring: Keeping conditions optimal for product quality, especially in industries where precise environmental conditions are critical, like baking or pharmaceuticals.
Challenges in implementing condition monitoring
While the benefits of condition monitoring are clear, implementing it isn’t without its challenges. As we discuss in the episode, one of the most common issues manufacturers face is integrating these systems into older machinery.
Many factories are equipped with a mix of old and new machines, and retrofitting older equipment with monitoring technology and integrating the data collected with data from newer machines can be difficult.
Sterre shares examples from factories that deal with frozen and wet environments, where even the physical installation of sensors can be a challenge. It is very important to make sure you choose the right sensor for the job (e.g., standard vs. waterproof sensors). If you go with a perhaps cheaper sensor that is prone to malfunctioning, you will end up spending more than getting the more expensive and robust sensor.
Another significant hurdle is the siloed nature of data and operations within many manufacturing companies. Teams across departments often collect data independently, making it challenging to compile a comprehensive view of the production process. As Sterre explains, breaking down these silos is essential for successful condition monitoring.
Measuring the ROI of condition monitoring
So, how can companies measure the success of condition monitoring? Sterre suggests that there are several key indicators that show the ROI of such systems. For one, companies can save significantly on maintenance costs by avoiding machine failures and reducing downtime. Additionally, improvements in product quality mean fewer customer complaints and returns, as well as less scrap and rework.
Condition monitoring also opens up opportunities for continuous improvement. By consistently collecting data on the production process, manufacturers can identify areas for optimization and make incremental changes that improve efficiency and reduce costs over time. This can be measured as improvements in overall equipment effectiveness (OEE), for example.
As we discuss, the results of implementing condition monitoring aren’t always immediate, but the long-term savings in terms of cost reduction, waste minimization, and higher product quality make it a valuable investment for any manufacturer.
Stay connected with the podcast
For more insights into how customer success can transform your manufacturing operations, subscribe to Factbird’s Manufacturing Matters podcast on Spotify, Apple Podcasts, YouTube, Amazon Music, or your favourite podcast platform.
If you have questions or topics you'd like us to cover, feel free to reach out via LinkedIn or email.