How Bisca is improving sustainability with more efficient production
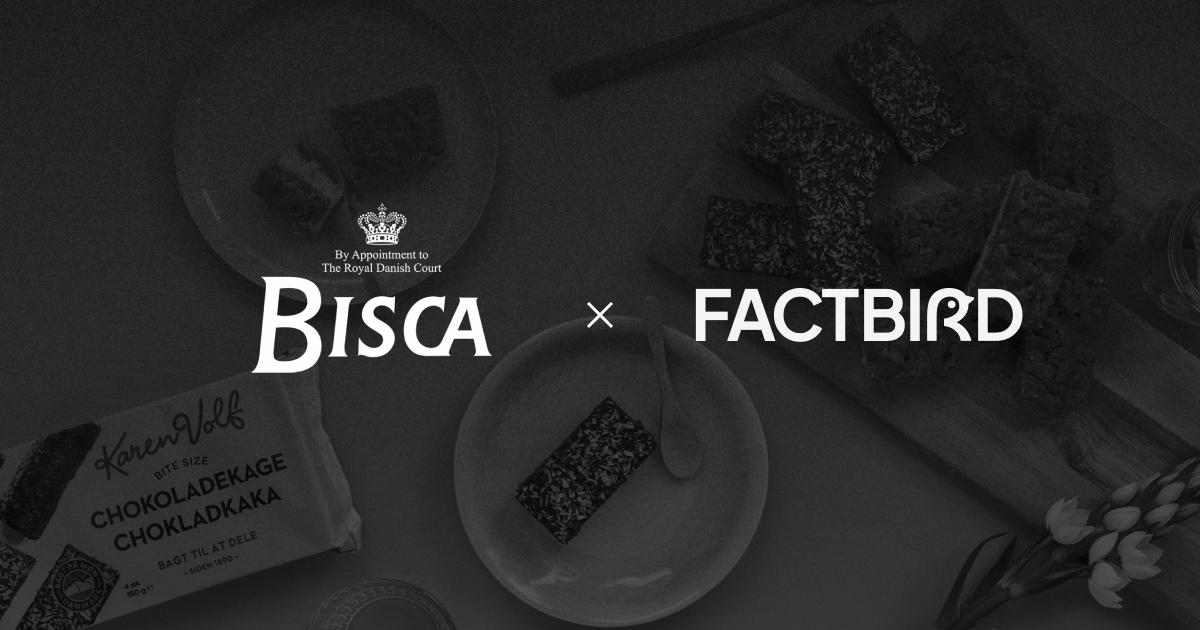
Bisca is a beloved food brand throughout Scandinavia and the globe. They were founded in 1890 and are behind well known brands like Bakkegaarden, All In One, Mønkiks, and Karen Volf, baking over 200 different types of cookies, cakes, crackers, and biscuits today.
Bisca has grown thanks to its focus on high-quality, craftsmanship, and sustainability. They are International Food Standard certified, British Retail Consortium certified, Roundtable on Sustainable Palm Oil certified, Rainforest Alliance certified, and hold the Royal Warrant as a Purveyor to the Royal Danish Court.

Factbird is proud to help one of Scandinavia’s best-known brands find new efficiencies, and we wanted to know more about how they are continuously improving their production (as well as sample some of their products). So we took the short drive south from Copenhagen to their 35,000 m2 production site in Stege on the island of Møn.
On site, we talked to Anders Holmström who is a Factory Manager and acts as head of production at Bisca, and Mads, a Production Operator at Bisca. Here’s what they had to say.
Why Bisca chose Factbird
Bisca has been using Factbird since 2022, and we wanted to know why they chose Factbird in the first place.
Anders explained that “we want to have the most bang for the buck on our resources. We did actually evaluate a couple of different systems. I’ve also seen other systems from earlier in my career. But we chose Factbird because of its ease-of-use, we liked the user interface. We wanted it to be in the cloud so we don’t want to maintain any servers here.
“And, I think, the largest benefit with Factbird was the plug-and-play installation. I mean, a couple of hours and you are up and running, actually up and running, on the same day.”
The implementation experience
Factbird lived up to it’s promise of easy installation for Bisca. According to Anders, “We did not have any difficulties. We chose Factbird because it’s so easy to install.”
Connectivity was a hurdle in the factory, however. Not for the Factbird IIoT devices, but for the screens showing the performance dashboards. Anders explained, “What we saw was that we didn’t have the infrastructure for the WiFi for the site. It was no problem for the sensors. But for the user interface, we have put some computers around. We didn’t have WiFi everywhere for them. So, the quick solution for us was to use some 4G routers to be able to have WiFi for the operator stations.”
Other than installation, user onboarding is a big hurdle when introducing new manufacturing software. Working together as a team on the implementation and getting buy-in from everyone, from operators on the machines to the board, has proven to be key to success time and time again.
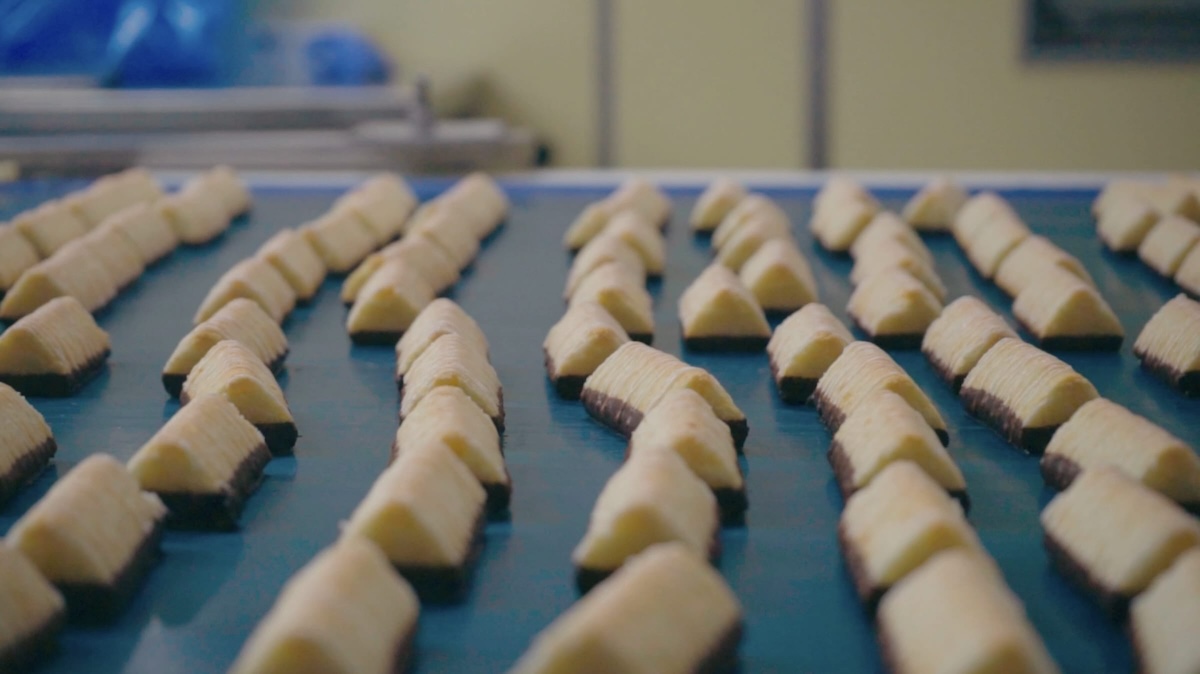
Anders says that for the implementation, “It’s very important that you have the production team on board. And I am very lucky to have a strong team with very good production leaders that have been dedicated in the process.
“They are also interested and dive into the system. (They) ask the operators if that is the correct categorisation of the stop. Should we have another stop category? So, I think we’ve been lucky that this has been quite easy for us based on the strong team that we have here.”
From the perspective of operator Mads, he felt that, “In the early days, you had to familiarize yourself with the system and learn it. But once you’ve found the different facets of the system, then I think it’s very simple and straightforward.”
Automatic aggregation and analysis of data
Factbird helped Bisca ramp up their data collection. Before using Factbird, they collected most of their production data manually. Now Bisca uses Factbird to solve all of their stops on the lines.
This means that they have Factbird on all of their baking lines, which is up to 14 lines. Eight lines have Factbird DUO IIoT gateways and sensors, while the rest are integrated via existing PLCs.
Most important for Anders is the aggregation of data so that they can figure out where the losses are and focus their resources on where they are needed the most.
“It’s much much easier to aggregate data; collect, combine, and analyse afterwards.”
- Anders Holmström, Factory Manager at Bisca
Mads also noted the consolidation of data as a big change. According to Mads, “We have consolidated all of our data. All of our stops in production and our documentation have been consolidated in one place. And it has made our daily work and tasks much easier. Specifically, how we identify our problems in our production line. The line has become much more traceable by using Factbird.
“Especially the communication with the technical staff (is easier). As we can see when there are repeated problems in our production. So we can go in and say, here we have a longer stop, and it gets fixed.”
“Now, we have one place for documenting data. And we do it on an ongoing basis. It makes it much easier during the day.”
- Mads, Production Operator at Bisca.
Mads went on to explain that “Before Factbird, we wrote down data by hand, for example, when we had downtime in production. And then, at the end of the day, we had to pick up all these downtime sheets and get them documented in our production report. Now, we have one place for documenting data. And we do it on an ongoing basis.”
Catching microstops
The root cause of stops can vary a lot. And sometimes large issues can be hidden in what are called microstops, or stops that are typically less than five minutes, depending on the industry. These short stops are normally untracked or very poorly tracked with manual collection of production data, but automated collection of data helps manufacturers see the bigger picture.
“What Factbird has enabled us to do is have full transparency and real-time data.”
- Anders Holmström, Factory Manager at Bisca
According to Anders, a big benefit of Factbird is that you can clearly see patterns and trends within a stop. He explains that “It’s a huge difference to see at the end of that day that, ok, we have a 40-minute stop on X. But if you see that 40 minutes split into, maybe, 80 30-second stops, that tells us a different story than one single large stop.
“We had, for example, one issue with paper baking molds for our butter cookies. We were surprised that we had so many small stops on that issue. So we dug deep into that and managed to solve that issue together with our supplier of this component. So that was a good case for us.”
Key KPIs for production
Bisca has seen positive productivity results in their factory with the use of Factbird. Performance doesn’t come from data alone, however. As Anders points out, “You don’t get any better off with just the data; it’s what actions you take.”
Their main KPI for Bisca’s operational excellence is overall equipment efficiency (OEE), a popular reference metric for the performance of equipment, lines, and factories over time. Bisca has seen a 7% improvement in OEE year over year, showing that they are getting more out of their resources and more bang for their buck.
According to Anders, this comes from “the stop registration that we use (in) day-to-day, week-to-week operations, to be able to focus on the biggest losses in the factory, and to focus our resources on that.”
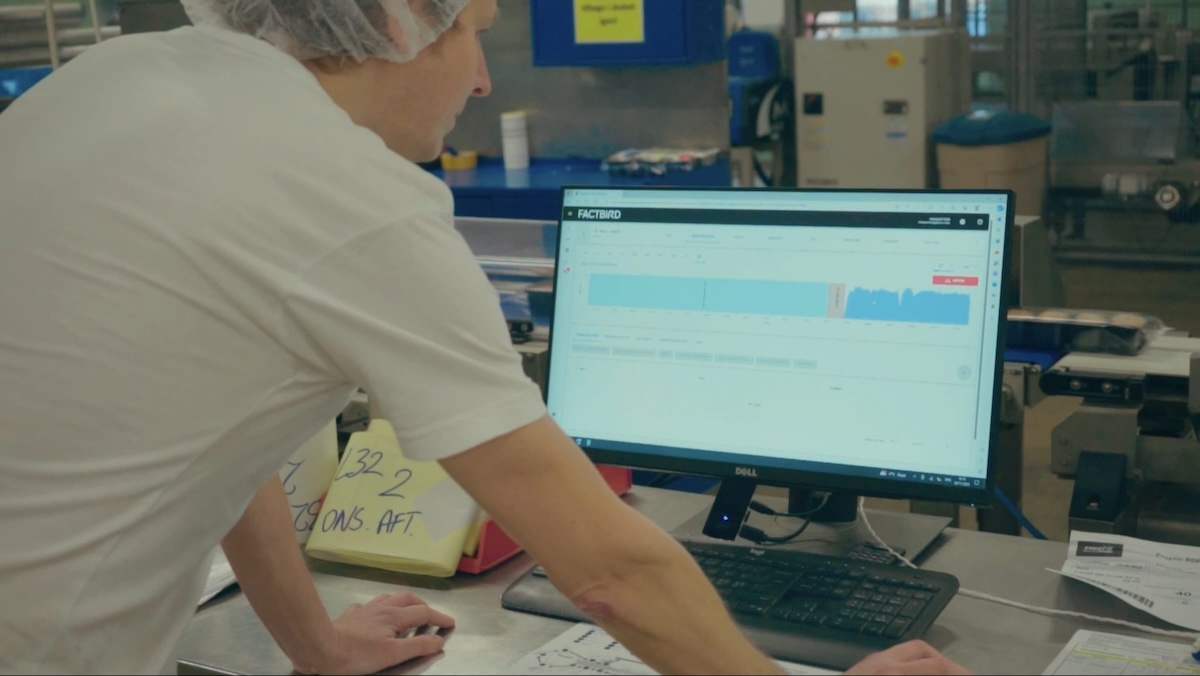
According to Mads, “It’s more simple now. You have one system where all of the data is collected. You can go in and have a look at the reports. We always record the stops, and here we clarify where the problems are on the production line. This makes it much faster and easier to identify where the stops are. And then you can set aside time to get it fixed.”
General advice for manufacturers
We asked Anders if he had any general lessons regarding the implementation of production monitoring systems like Factbird.
According to him, it’s “important that you have a plan for how you’re going to use the data. It’s not just installing a system and it’s there for you. You have to integrate it into your daily operations. You have to take action on it; otherwise, you are risking that it will fade away.”
For Mads, his advice is “keeping up-to-date throughout the day. That helps a lot. Especially if you have a busy day. If you don't note down data continuously during production, you end up having to try and remember what happened. The events of the day may well be forgotten. You have to stay ahead. And you can say this is where Factbird helps.”
What’s next for Bisca?
Ander’s like that evolving nature of Factbird. New features are continuously being added to Factbird’s suite of Manufacturing Intelligence solutions with the input of customers like Bisca.
One feature Anders would like to start using is Factbird VIEW. A camera system that will make it easier for Bisca to analyse root causes of stops and improve communication and understanding within their long production lines.
Otherwise, Anders shares that they are investigating ways to use Factbird to “look at our process parameters as well, like temperature and humidity in our baking process.”