Micro-stops and how you can track them
Manufacturing Matters Ep. 9
Tais Roden, Business Development Representative, UKI, Factbird
Release Date: June 24, 2024
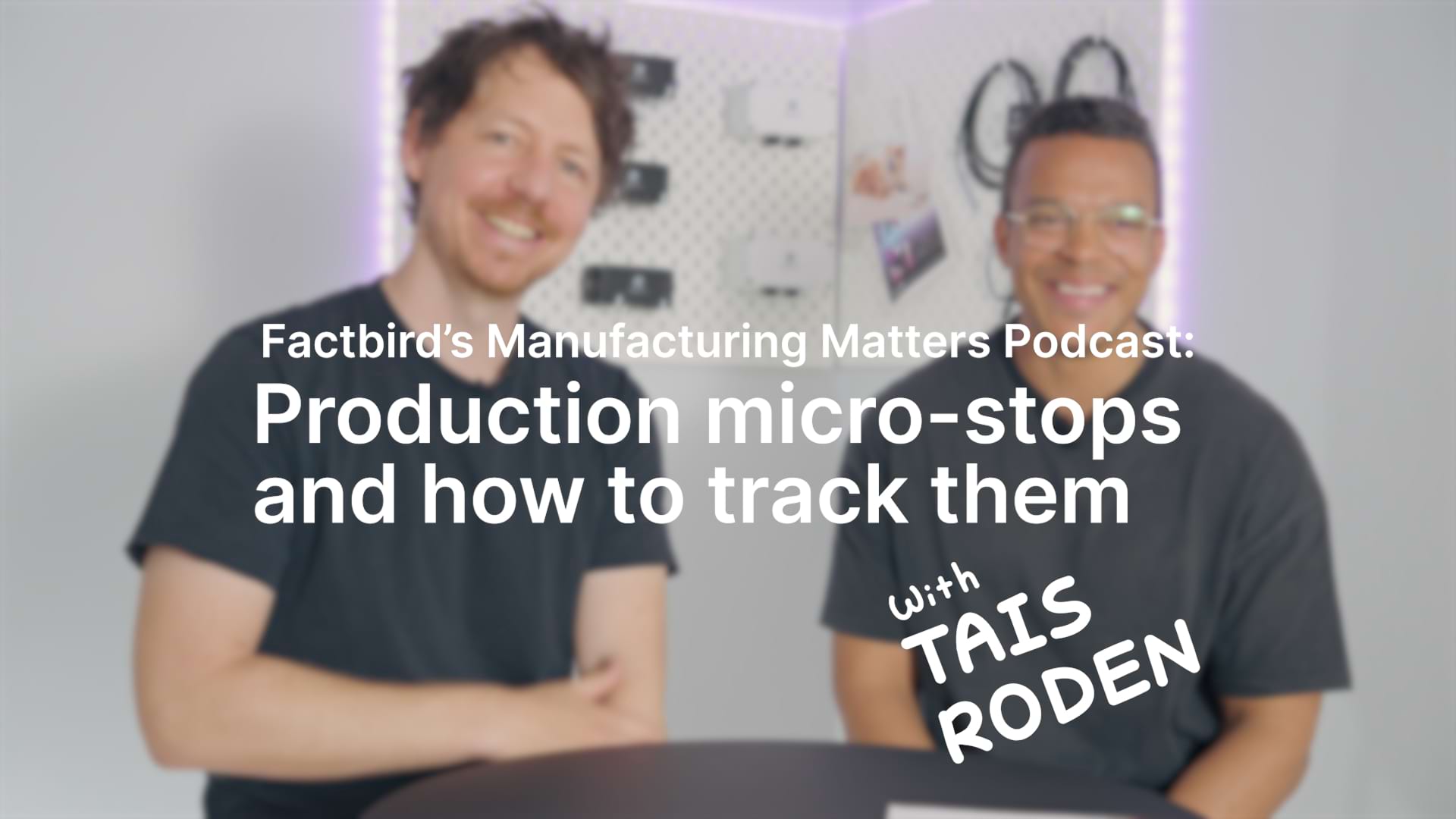
- Micro-stops are short, unplanned downtime that occur in manufacturing processes.
- Micro-stops are easy to overlook when recording stops manually.
- Failure to properly track micro-stops can lead to large productivity losses.
- Manufacturing intelligence solutions are an effective way to detect micro-stops and their root causes.
Micro-stops, the brief and often overlooked interruptions in manufacturing processes, are a prevalent issue in industries such as packaging and food and beverage production. Addressing these micro-stops is crucial, given the razor-thin profit margins that characterize these industries, making efficiency and minimal downtime essential for maintaining profitability.
In Episode 9 of the Manufacturing Matters podcast, I talked to Tais Roden to draw on his experience of helping manufacturers track micro-stops. Tais is the Business Development Representative for the UK and Ireland at Factbird and has recently been talking about manufacturing intelligence at the OMRON Roadshow in the UK.
Would you like to know how to get rid of micro-stops in your production? You can watch the full podcast in the video above or read on for an in-depth look at what micro-stops are and how to solve them.
What are micro-stops?
First up, let’s align on what we mean when talking about micro-stops.
Micro-stops, also known as minor stoppages or micro-downtime, are brief interruptions in the manufacturing process, typically lasting from a few seconds to a few minutes. Although the definition of “micro” varies by industry, these short interruptions are usually caused by minor issues that can be resolved quickly without much intervention.
Although each micro-stop is short, their cumulative effect can significantly reduce productivity. These interruptions can result from equipment malfunctions, operator errors, material handling issues, environmental factors, and process inefficiencies. Addressing micro-stops involves regular maintenance, proper training, efficient material handling, environmental control, and process optimization.
Why are micro-stops important?
When logging downtime manually with pen and paper, micro-stops can easily go unnoticed.
Frequent small stops can accumulate to cause significant downtime in manufacturing. So, it is crucial to log these micro-stops and address them when they become an issue. Failure to detect and fix micro-stops can lead to major problems in production and, therefore, for the company. For example:
- Unsatisfied customers and lost business due to production delays.
- Increased business costs due to idle equipment.
- Compromised employee safety due to risks during shutdown and start-up of operations.
- Inaccurate production KPIs lead to poor decision-making.
On the other hand, effective micro-stop analysis enables you to identify bottlenecks and implement strategies to reduce downtime caused by frequent minor stoppages. Overall Equipment Effectiveness (OEE) is a metric that is commonly used in manufacturing for this purpose, and Factbird can help provide an accurate overview of various stoppages on a production line.
As you can see in the example from the Factbird Cloud App below, micro-stops are classified as part of OEE1 together with quality losses, performance losses, and other unplanned availability losses.
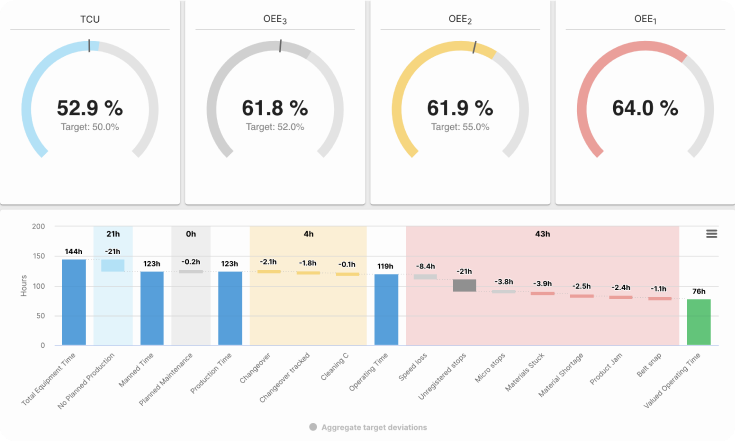
Causes of micro-stops
The increase in micro-stops is correlated with higher levels of automation. Common causes include:
- Suction clamp issues: Packages not picked up or dropped properly, halting production.
- Ventilation blockage: Blocked ventilation systems that require cleaning.
- Checkweigher jam: Checkweighers reject products that aren’t consistent with target weights but can become jammed when products get stuck.
- Sealing bar contamination: Sealing bars are used to cut and seal packaging, and it’s common for them to become contaminated and require cleaning from e.g. powder that escapes from packets during sealing.
- Cartoner misfeed: Improperly closed cartons needing removal.
- Glue gun misconfiguration: Incorrect glue gun settings needing adjustment.
- Tray conveyor and carton rail blockages: Trays or cartons falling or blocking the conveyor or supply rail.
- Full conveyors: Full conveyors or dirty sensors halting production.
- Palletizer overload: Overloaded palletizers halting production.
- Temporary power loss: A short power cut, whether caused by utility grid issues or internal electrical problems, can result in micro-stops.
- Human error: Misconfigurations, incorrect settings, and oversights can cause micro-stops.
How do you measure and reduce micro-stops?
Micro-stops can be measured in two ways: manually or automatically.
Manually tracking micro-stops
Manual tracking requires operators to track every stop, often with a pen and paper or whiteboard. However, if you aim to reduce micro-stops and improve efficiency, manual tracking is not recommended.
Micro-stops can be so short that they are hard to detect. Not detecting all micro-stops will lead to an incorrect calculation of how much downtime they actually cause.
On top of this, paper notes can get lost, data can be inputted into spreadsheets incorrectly, and whiteboards can get erased.
Additionally, manually tracking micro-stops is hard to standardize because employees might have different ways of defining stops. This subjectivity makes the data inconsistent; therefore, you can’t trust the analysis due to a poor foundation.
An experiment that Factbird employees did during a Six Sigma course provided a good example of the subjectivity of time perception. Pairs were provided with a stopwatch, and the challenge was to have the most accurate average guess of a 10-second period. The team member without the stop-watch had to say “stop” when they thought that 10 seconds had run out, and the results ranged from 7 to 16 seconds.
Automatic tracking of micro-stops
Switching to automatically tracking micro-stops can impact your business substantially by removing human error and offering better traceability to the root cause of stops.
Factbird offers multiple ways of capturing stop data. For plug-and-play production monitoring, you can retrofit Factbird DUOs to your production lines. Factbird DUOs are IIoT gateways that can take up to four digital or analog sensors per device and transmit data to the cloud using WiFi or cellular.
Alternatively, you can take advantage of existing sensors on your lines. There are multiple methods of doing this, such as sending data directly from OMRON PLCs or connecting Factbird to existing Kepware or OPC UA solutions.
Once your production data is in the Factbird Cloud App, micro-stops are automatically classified according to the thresholds or criteria that you set. Factbird’s manufacturing intelligence software will then offer analysis such as pareto charts, scatter plots over time, and OEE analysis. You now have accurate and valuable insights on how much downtime micro-stops create overall.
Micro-stop tracking case example
A good example of success tracking micro-stops comes from Broxburn Bottlers, a leading bottling service provider in the UK. As a company committed to offering on-time service delivery and quality products, they realized they were lacking production insights and reliable downtime data to act on and improve.
After implementing Factbird’s manufacturing intelligence solutions on their lines, the operators noticed that Line 3, the cork application line, had a lot of micro-stops. Each of them was as brief as a fraction of a second, but they added up to several hours a week of downtime.
Accurate production data helped them prioritize the resolution of the issue and identify the cause—the machine-change parts weren’t fit for purpose. Instead of having a standard part for all corks, they purchased multiple, dedicated parts. The result helped them improve OEE by 12%.
You can watch the full case study video here: Broxburn Bottlers Case Study.
Conclusion
Effective micro-stop tracking is essential for the effectiveness of production lines and the overall success of operations. Manual tracking of micro-stops is ineffective, and switching to automatic tracking of micro-stops, for example, by using Facbird’s manufacturing intelligence solutions, is highly recommended.
Remember to subscribe to Manufacturing Matters to get notified when the next episode is available on Spotify, Apple Podcasts, YouTube, Amazon Music, and other popular podcast directories.