How Broxburn Bottlers unlocked their production potential with real-time data
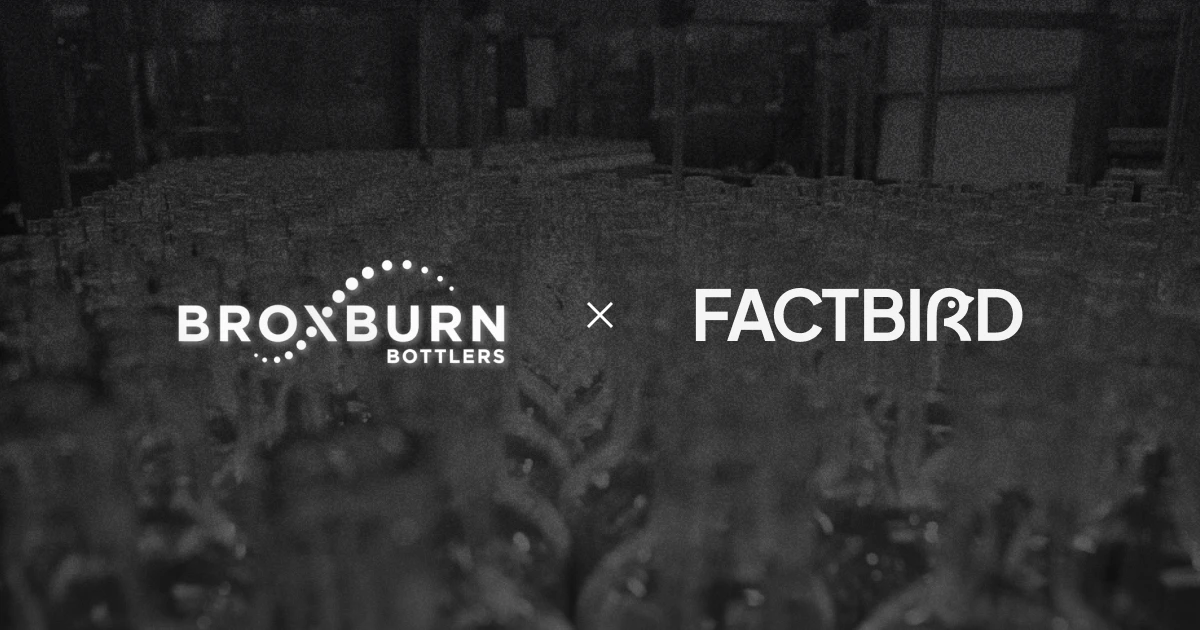
Broxburn Bottlers, a leading UK bottling services provider, had limited production insights and unreliable downtime data. Seeking to improve processes, they implemented Factbird in 2022, enabling real-time production tracking and problem-solving.
This case study explores the impacts across numerous roles within the company, highlighting the tangible benefits experienced since adopting Factbird.
Jonathan Bell, Operations Director
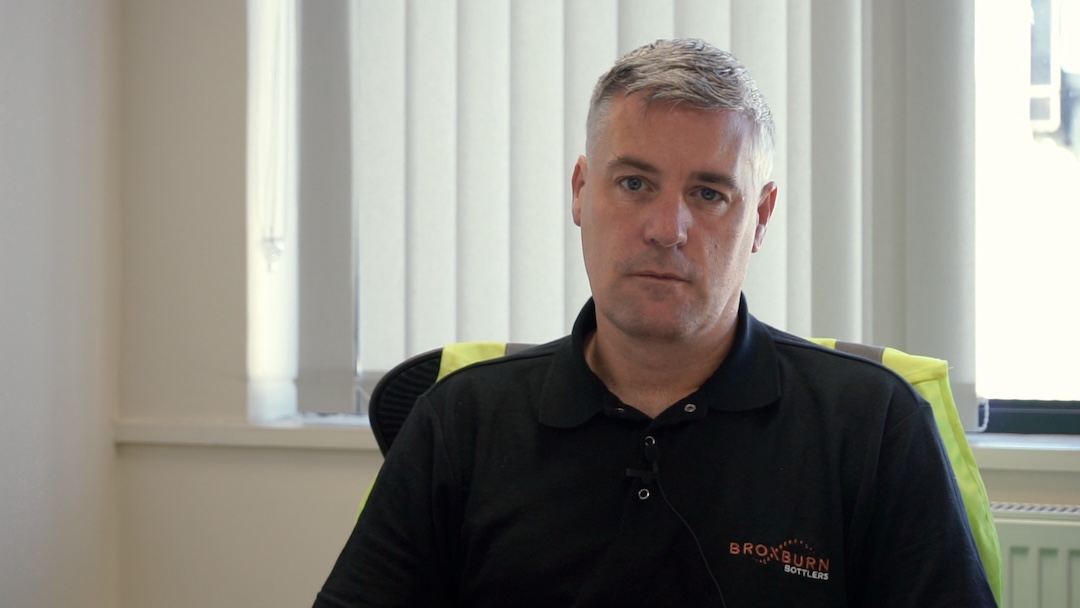
What were your biggest manufacturing process optimization challenges?
I came here about three years ago, and we had limited manufacturing data. All we had was the number of cases we produced against a target. So, we didn't know if that was good at the start. Was it a consistent performance? And we had a limited amount of downtime. So, it was always the big issues people could remember that we were capturing.
“It was always the big issues people could remember that we were capturing.”
If you've got a lot of micro-stops where a lot of corks are jamming, but that happened 40 or 50 times every couple of hours, you miss that data because people remember the big bang where a machine breaks, and they don't get the bigger issues, which accumulate over a day. So, we were missing some of the bigger issues.
What drove your solution search?
To capture actual performance efficiency on an hour-by-hour basis. Also, to have the ability to get the downtime, whether that be a micro-stop or a bigger stop.
And then we can analyze after the event and see what improvement work we wanted to do on each line and on each machine. So it gave us a lot more knowledge and data to make informed decisions.
Why did you choose Factbird?
The reason we chose Factbird was that we carry out an AMIS audit every year. An independent company, MCP, comes in, and they assess us for engineering and operator asset care. We asked them for advice on a system that they had seen previously, and they highly recommended Factbird.
We then started having discussions, and we carried out a trial. The trial obviously went really well, and we implemented it fully across the site. We chose Factbird to give us the manufacturing data that we required, which was both efficient and downtime-efficient. And it was simple to use.
So it wasn't scary for the operators to have to input the data on the line. It was very simplistic to use, but it gives you the in-depth data we needed for the improvement journey. And it ticked all boxes.
How was the implementation?
During the trial, a lot of people weren’t sure about the rationale for it and what we were using it for because they'd never seen a data capture system before. There was a lot of education and explaining to the people the rationale for it. It’s not Big Brother watching; we need the data to help us make decisions for improvement on each line and machine.
We carried out a trial, so we probably limited the timeline because it took us a while to get it installed. Once we got it installed, we started to use the system and “learn as you go.”
It probably took us two or three months, where we then said, ”Yes, we want the full system” because we tried it on one line—our busiest line first of all. And then we looked to implement it, after the successful trial, across all our other lines.
What areas did Factbird influence?
The system, although I said it was simplistic, the amount of data it can generate. If you're a data junkie, you can spend a lot of time going through the detail and improvement information that it can supply you.
It helped our understanding of each line and each machine's downtime and the key areas that we needed to focus our resources on for improvement.
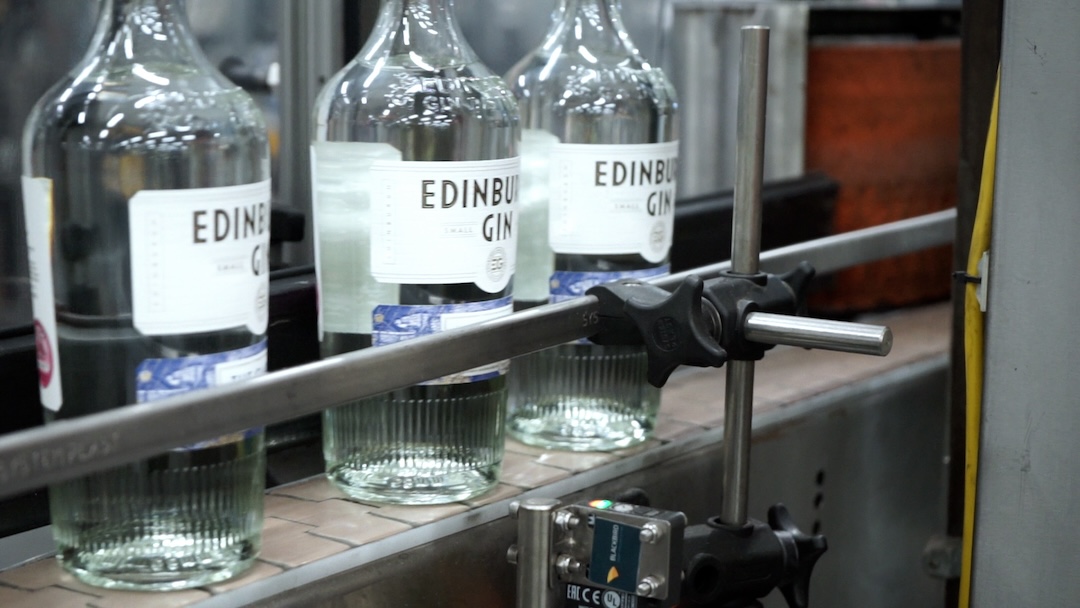
A good example was Line 3. We were getting a lot of micro-stops on the cork application. It would be a fraction of a second each time, but if you add up the operator unjamming the corks, it was a lot of time. Instead of a big bang where the machine stopped for an hour or two, this was an accumulation of numerous hours over a week and over a production run. So it helped us identify stuff like that—the micro-stops that all build up to the bigger issues.
That data allowed us to identify that the machine-change parts weren’t fit for purpose. So it allowed us to invest some CapEX in that area and buy dedicated change parts for all corks instead of having a common part used for two or three different variants.
“We're sitting at circa 77.8% year to date in 2023 up to the end of August. A step change in performance.”
For line 3 in 2022, we were sitting at an efficiency of 65.8%. After Factbird going in and us made the improvements that the system helped us identify, we've got a 12% increase. We're sitting at circa 77.8% year to date in 2023 up to the end of August. A step change in performance.
How do you use data now?
I think we use the data in numerous different areas. We have implemented a tiered meeting structure in which we use the efficiency and the downtime of Factbird. And if you go down the line, people are using it on a daily basis.
People on site are starting to dial in to the data who aren’t directly on the production line. And the guys on the production line use it on an hour-by-hour basis to make sure the performance is going on track. I think it would be a big miss now if we didn't have it.
How did you involve people on the factory floor?
When we first implemented it, we tried to explain to people the rationale for coming in that was going to help us make improvements and ultimately make their lives easier.
We've now gone from just a supervisor entering the downtime data to the machine operator entering the downtime data. They're starting to own the system and are starting to use it to their benefit.
“They're starting to own the system and are starting to use the system to their benefit.”
It’s involving them in the whole process and actually letting them see the benefits of the system by inputting the data and seeing the benefits coming out with improved efficiencies.
Part of our core values is about improvement, and the data enablers that Factbird gives us really align with that, because you can use the data to make decisions, whether it be for investment, resources, or anything else. So, it really does support the decision-making process on the improvement journey that we're on.
What were your biggest implementation lessons?
I think you need to put a project owner or a champion on the site, somebody where it’s their system when you're implementing it. So if there are questions, they can train people and challenge people about the integrity of the data, because the integrity of the data is the main thing. If you put rubbish in, you'll get rubbish out.
So, it's making sure that people put accurate data in and explaining to them the rationale for the system because people fear change, and if they don't know the reason for the change, they'll not input the correct data.
Lisa Napier, Production Senior Team Leader

What were your biggest production efficiency challenges?
The main challenge we had was a lack of data; there was nothing to really collate it. So, now having that, we are getting the information we need to improve on.
“We had a lot of minor stops, maybe 40 or 50. On a general day, we wouldn’t have captured that.”
With Factbird, we have the ability to find the root causes. As Jonathan mentioned, on Line 3, we had a lot of issues with corks, and so we had a lot of minor stops, maybe 40 or 50. On a general day, we wouldn’t have captured that. But now we are capturing that and seeing, “Yep, we are losing an actual lot of time with that.”
How was the experience implementing Factbird?
It was challenging. People don't like change. Initially, it was a little bit of a struggle, but now everybody has totally adopted it. Even for the normal operators on the line, who don't actually input the data, they are all buying into it. They go have a look and see what their efficiencies are like. So it's really good.
Scott (the champion) has been a big part of the implementation. Scott was down on the shop floor a lot, taking the guys through it. The supervisors were the first to get through it. Then we started taking operators through it. For me, the best part is the operators’ buy-in.
Where have you seen the most impact?
I am in production, so for me, it is fixing all the major problems in the bottling hall. Now, because we have that collection of data, we can look at a product and say, “Look, we ran that the last time and had these issues. We are now coming up to it; ”can we pre-empt?” And look at solving the problem before it hits the line.
How did Factbird improve troubleshooting?
For me, because we now have the data, I can check and see if the lines are at the correct speeds. If there are any issues in the line, I can just have a quick look, and tell the team. So, we're optimizing our time and not wasting it.
Has Factbird improved decision-making?
Yes, I look at this every day. I am on Factbird constantly, and I am radioing down the stairs. I am having a look; are they running at the right speeds? Why are they not running at the right speed? Have they asked for the engineers?
“I can see everything that I need to see with Factbird, which is great.”
On Line 7, this morning, we had an issue, and the engineers were on the line. The line wasn't running. For me, that's not productive, so then I asked the operators to jump on Line 5 while the engineers were working on Line 7.
I can see everything that I need to see with Factbird, which is great. I check registered stops, the line efficiency, and batches is also a handy one for me; it helps to see when they're going to finish. I look at the OEE as well as downtime.
It definitely increased efficiency across all lines. We are doing work with training as well, but the efficiency has definitely improved with Factbird.
What were your biggest implementation lessons?
I think having somebody that's going to be the champion for it, who can then train people, I think that's handy. And who has more knowledge that can then show somebody if they're not too sure, I think that's the best thing.
Chris McKeen, Electrical Engineer
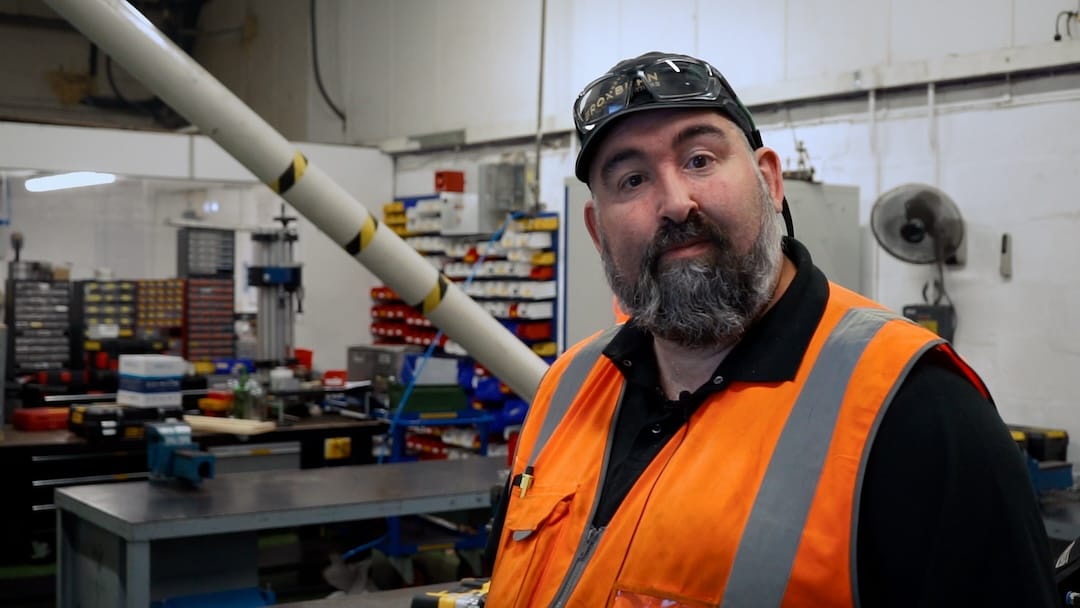
How do you use Factbird in your day-to-day work?
It allows us to see when we have machines and lines down. It allows us to see when they're planning to be down. So, we're able to react to any problems that we have on the line, whether it be a minor or a major issue.
“It helps us manage our time better, to be honest.”
We also use the system for changeovers, where we move from one product to another. Sometimes, they require engineering assistance. It helps us manage our time better, to be honest.
It allows us to get a task planned. So instead of just randomly running out and trying to find time, we know that we've got time coming up for a tea break, so we can plan our small jobs and large jobs around that.
We use the batch dashboard, estimated time of completion quite a lot, as well as the traffic light system (Andon), and the percentage of finished product.
Was the implementation hard?
Installing was a bit of a challenge, just due to the length of the lines. Then we needed to change to sensors that could pick up glass. Once that was set, it was a plug-and-play system. It works really well.
How has the support been?
Yeah, the support's been great. With a quick email, things are resolved; it's never an issue.
Do you have an example of how Factbird has helped?
Well, we have one line, which is an engineering-led changeover, and predominantly, we would need to wait or be told when this was coming up to get a change.
“It’s a faster change with less drag time.”
Now, with the system, by the time we get to 95%, we are all ready; we have got guys out and parts out. It’s a faster change with less drag time.
Seeing the OEE of a system. That allowed us to also see what we needed to do to improve our systems and our procedures to allow them to get better performance out of the machines.
What were your biggest implementation lessons?
Because it was sensors with no demarcations on them, people were playing about with them and moving them. So we contacted Factbird and got some stickers made. Now all our sensors are identified, so operators know that if they don’t get a reading, check that (the sensor) first before they get an engineer. Nine times out of ten, they just have to move a guide rail or something.
Otherwise, getting people used to using the computer and using the facilities that are within the software—how to read it and how to predict stuff with it—is just really a learning process for everybody.
Tony Lynch, Line Supervisor
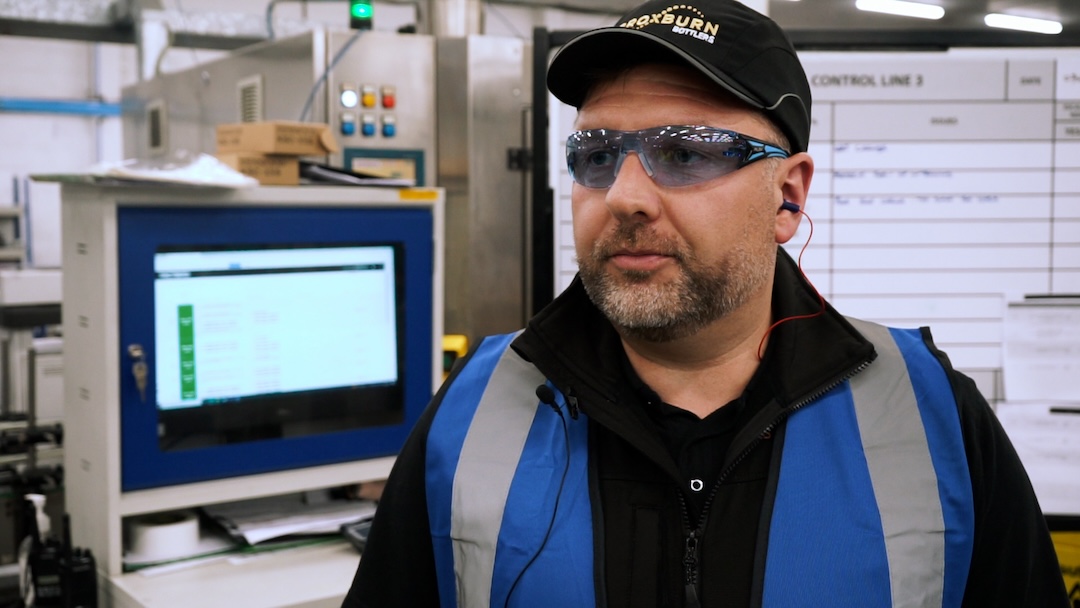
How do you use Factbird in your day-to-day work?
It’s good for the analytics. So, if you’ve been on a problem project before, you can look back at it and see what problems you’ve had. It gives the operators a heads-up.
The difference is night and day. We didn’t know how many cases per line we were doing, how many cases we were running through. So a lot of time we were taken away from the line dealing with that. Now Factbird does a lot of the work for us. So we can focus on the issues on the line now. We can collect that real-time data from Factbird. So that’s a big difference.
I use a lot (of features). Obviously, I use the live time (dashboard). We time when certain products are gonna finish, when they’re gonna start. We use analytics; we can pinpoint when we have issues and bring them up at team meetings. And I use the OEE (Overall Equipment Effectiveness Metrics) a lot, on an hour-to-hour basis.
How did the implementation go?
It was a bit alien to operators. Now, they are coming on board with it, they’re getting involved. Obviously, it helps drive the line’s efficiency for Broxburn Bottlers. They’re more involved; they’ve taken an interest. So, I think it's been a great value to the team.
Do you have any examples of efficiency savings?
Yeah, definitely. Before we had Factbird, we were manually counting how many cases we did. On an hourly basis, I was down the end of the line.
“It frees up time for myself; it frees up time for the guys.”
I can capture that now in seconds. So, it frees up time for myself; it frees up time for the guys. So we can target what the guys do on the line.
Kasia Liczenska, Operator
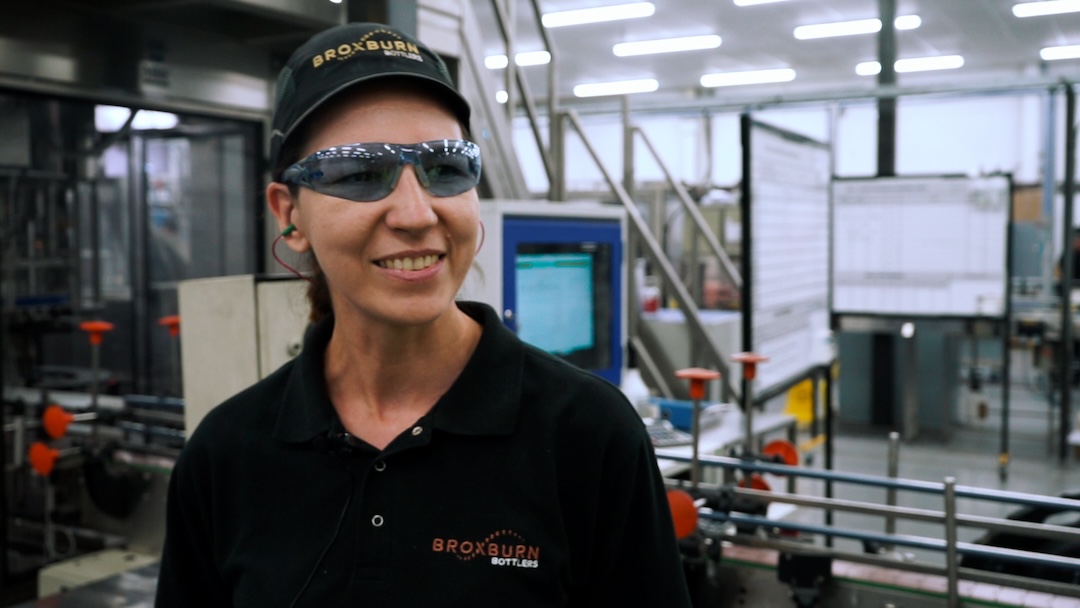
How has Factbird changed your daily work?
My work is much easier now because every day when I come to work, I can check how it was running one day before. So, I can know what problems there were with the batches.
So, I already know whatever it is—the fill level, the timing, the head, any problem—I am ready for that. I can even start fixing the problem before it comes. I know what to expect. Or I can know that it was an easy day, and that will be good for me.
How did you find the introduction of the system?
It’s quite easy. As long as someone shows you where everything is, it’s easy to find information.
It helps me fix problems before they come.
Before we start running an order, I can find out how it ran the last time. It helps me fix problems before they come. So I know what to expect with the system. It’s much easier for me.
Everything that I need as an operator, I get from the system. I would not change anything.