How pretzel baker Ditsch digitized production monitoring with Factbird
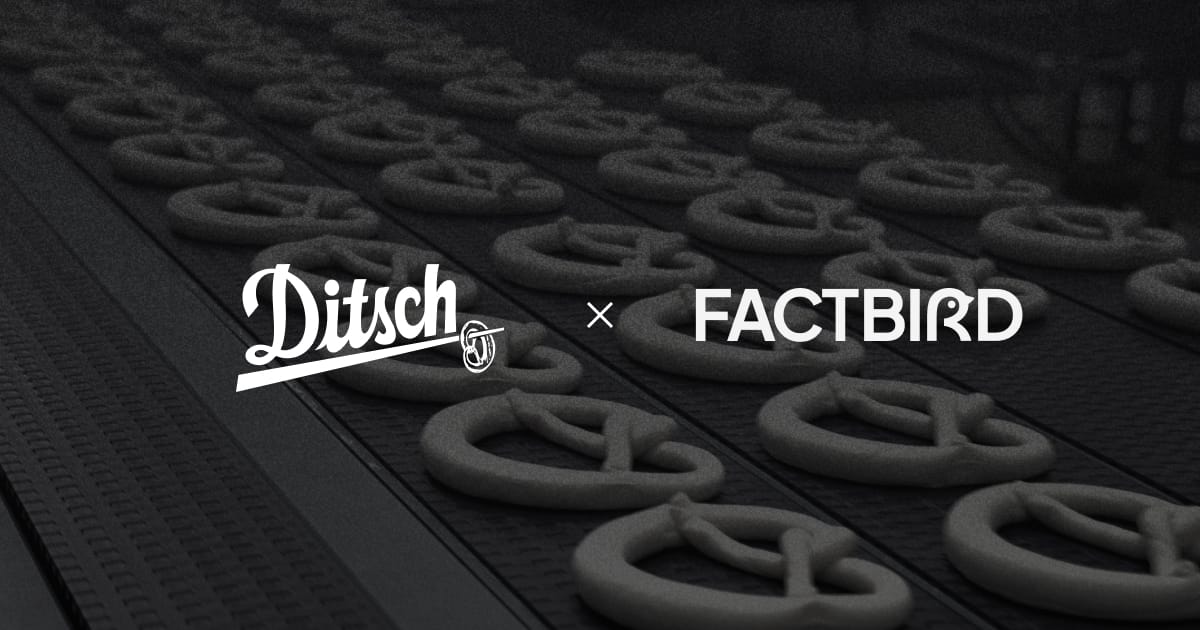
How pretzel baker Ditsch digitized production monitoring with Factbird
Ditsch has been dedicated to crafting authentic German-style pretzels since 1919. They ensure top-notch quality and safety by overseeing the entire production process, from selecting premium raw materials to the finished product. The company operates both in Germany and the USA, supplying Ditsch and Brezelkönig shops in the DACH region (Germany, Austria, and Switzerland), as well as international markets and the food retail sector, with frozen baked goods.
The Challenge
Ditsch has the common manufacturing challenge of optimizing efficiency, quality assurance, and cost management in a highly competitive market. The lack of real-time data availability and the cumbersome nature of manually recorded production data made timely and accurate decision-making difficult.
"Especially the constant, handwritten documentation... It was an enormous time-consuming task."
- Lucy Gerhold, Project Manager at Ditsch
To tackle these challenges, the digitalization initiative aimed to capture, visualize, and monitor the entire production process—from dough preparation to packaging—all from a single screen.
Implementing Factbird at Ditsch
Ditsch chose Factbird as a long-term partner to digitize their production lines. They started with Line 9 at their Oranienbaum-Wörlitz site in Germany as a pilot project. The goal was the integration of production data from existing PLC systems into Factbird using MQTT via Kepware to monitor over 180 performance and process parameters.
The implementation took eight months and involved setting up IT infrastructure, buying devices, installing Factbird software, and training employees.
The challenges were significant, especially when connecting the machine controls to Kepware, as some were delivered without the necessary data transfer interfaces. Then there were extra costs and supply chain problems, which delayed device procurement. Despite these issues, close collaboration led to major improvements in production efficiency and transparency. Ditsch has successfully established a new standard for digital production monitoring and control.
The Impact of Data-Based Decisions
The implementation of Factbird fundamentally transformed Ditsch's production processes and had a significant impact.
Digital Plant Monitoring and Documentation
The digitalization of production monitoring with Factbird has made the work of Ditsch's operators much easier. Instead of using time-consuming paper documentation, the system allows precise and efficient real-time data capture and monitoring. This is especially useful in the food industry, where continuous documentation of process parameters is necessary.
Employees can now respond faster to deviations, improving quality assurance and reducing errors. For instance, the "Control Recipes" function in Factbird automatically fills in the hourly check of important process parameters using existing sensor values, and employees only need to confirm in the app. Digitalization makes life easier for operators and ensures information for quality control and optimization is always accessible, greatly enhancing production efficiency. Georg Christoph, Plant Manager in Mainz, highlights that the system allows line workers to focus on their core tasks instead of spending time collecting and analyzing data.
Process Monitoring & Quality Assurance
The implementation of Factbird has significantly contributed to quality assurance at Ditsch. Continuous monitoring of critical process parameters and the introduction of alarms for deviations have greatly reduced response times to discrepancies.
"Previously, we had no alarms for deviations from target values, or we only noticed issues much later, like when the freezer was clogged because the pretzels had grown too large due to high temperatures in the proofing chamber," illustrates project manager Lucy Gerhold.
Precise monitoring and early detection of deviations are essential for food safety and meeting strict quality standards. Ditsch set lower and upper alarm levels for all analog process parameters. If a value goes outside the normal range, employees get a visual alarm notification. If the alarm continues, the shift supervisor gets an email notification. Digital documentation and access to historical data allow quick and reliable proof during complaints that production was within set tolerances.
"The greatest added value is that the process data is now consolidated digitally on a data platform based on PowerBI. This generates alarms that alert employees to problems or potential issues."
- Georg Christoph, Plant Manager at Ditsch
Data-Based Decision Making
With Factbird, Ditsch has significantly improved its data-driven approach to production. Real-time data and detailed analyses help management and employees make informed decisions and continuously improve production processes.
Digital documentation eliminates interpretation gaps and provides clear, objective data. This reduces quality fluctuations and process deviations, unifies workflows, and significantly increases production capacity.
Employee Engagement
The digital transformation has significantly eased the work of employees. Automated data collection and the intuitive cockpit interface (a clear dashboard showing the entire line status) allow them to work more efficiently and effectively.
"We wanted to provide our employees with continuous transparency about the status of the processes within production," emphasizes project manager Lucy Gerhold. This fostered a new level of engagement and responsibility among the employees.
Conclusion
The collaboration between Ditsch and Factbird demonstrates how digital transformation and the use of real-time production data enable companies to optimize their production processes and ensure product quality.
"The positive thing is that you can access all your machine data at any time from anywhere."
- Lucy Gerhold, Project Manager at Ditsch
Through Factbird, Ditsch has not only achieved its production goals but also made a significant step towards future viability and competitiveness.