A quick guide to calculating Overall Equipment Effectiveness (OEE)
Master the OEE essentials in minutes with this quick guide to OEE. You'll learn how it is calculated and get practical advice on how to improve OEE.
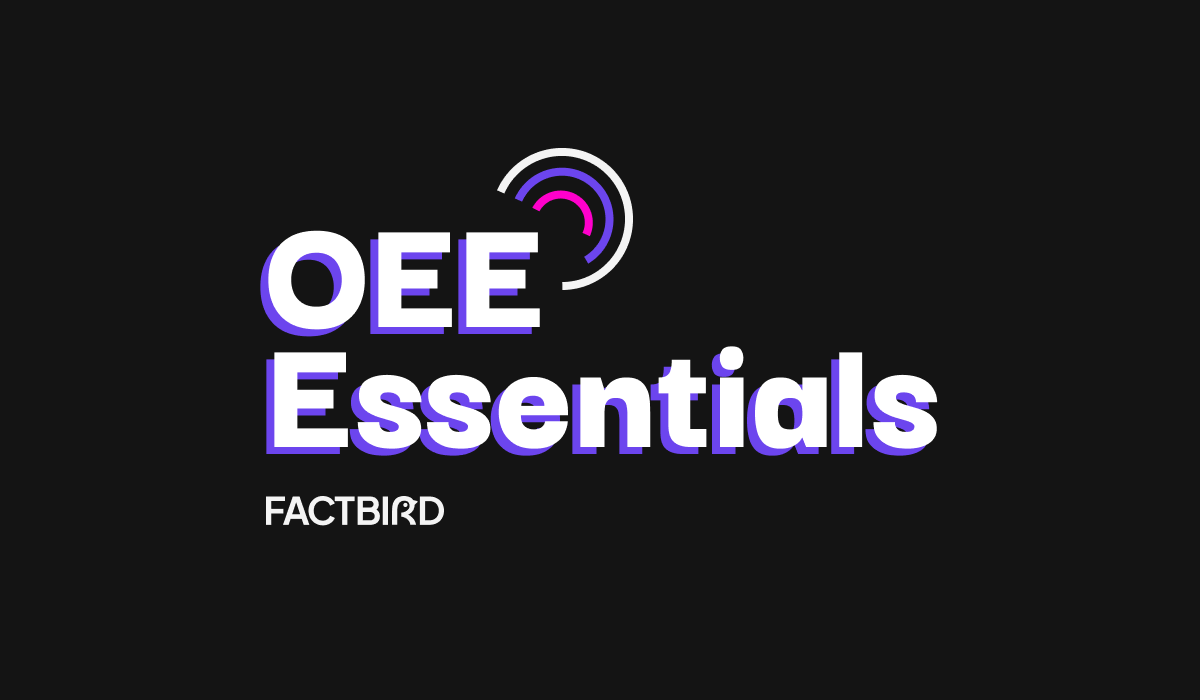
Manufacturers today face constant pressure to maximize efficiency, reduce waste, and improve productivity. One of the most effective ways to achieve these goals is by measuring and optimizing Overall Equipment Effectiveness (OEE).
OEE is a powerful metric that helps you understand how effectively your equipment is being utilized and where losses occur.
This guide breaks down everything you need to know about OEE calculation, from its components (availability x performance x quality) to strategies for improving OEE.
What is Overall Equipment Effectiveness (OEE)?
OEE is a metric used in manufacturing to evaluate the efficiency of equipment. In short, it measures the percentage of production time that is truly productive.
OEE is the product of three components: OEE = Availability x Performance x Quality.
A perfect OEE score of 100% means that only good parts are produced as fast as possible with zero downtime.
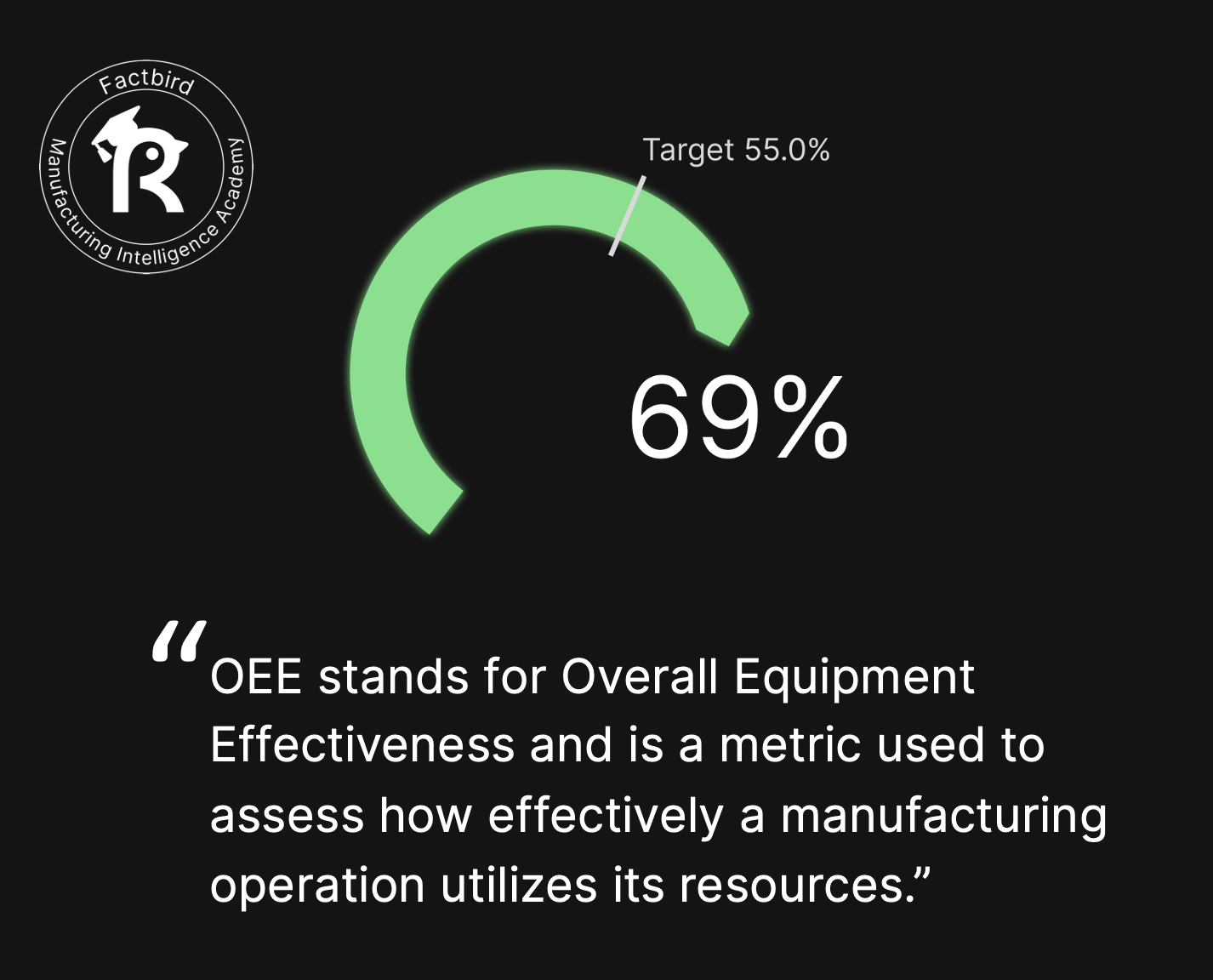
You can learn more about the basics of OEE here:
🔗 Understanding OEE - An Overview
Why is OEE Important?
OEE is widely used in manufacturing industries such as food and beverage, pharmaceuticals, packaging, and automotive manufacturing. It serves as a benchmark for identifying areas of improvement in production processes.
With OEE, you can:
- Identify inefficiencies in production and save costs.
- Compare machines, batches, shifts, lines, and sites with a standardized metric.
- Make better, data-driven decisions.
- Benchmark your efficiency against industry standards.
- Understand capacity and make better decisions on equipment investments.
- Drive continuous improvement by uncovering previously hidden losses.
The three components of OEE calculation
OEE is calculated based on three key factors:
Availability measures the percentage of planned production time that your equipment is actually running.
Performance evaluates how efficiently your equipment is operating compared to its maximum speed.
Quality assesses how many right-first-time parts are produced versus defective ones.
Each of these factors contributes to your overall OEE score.
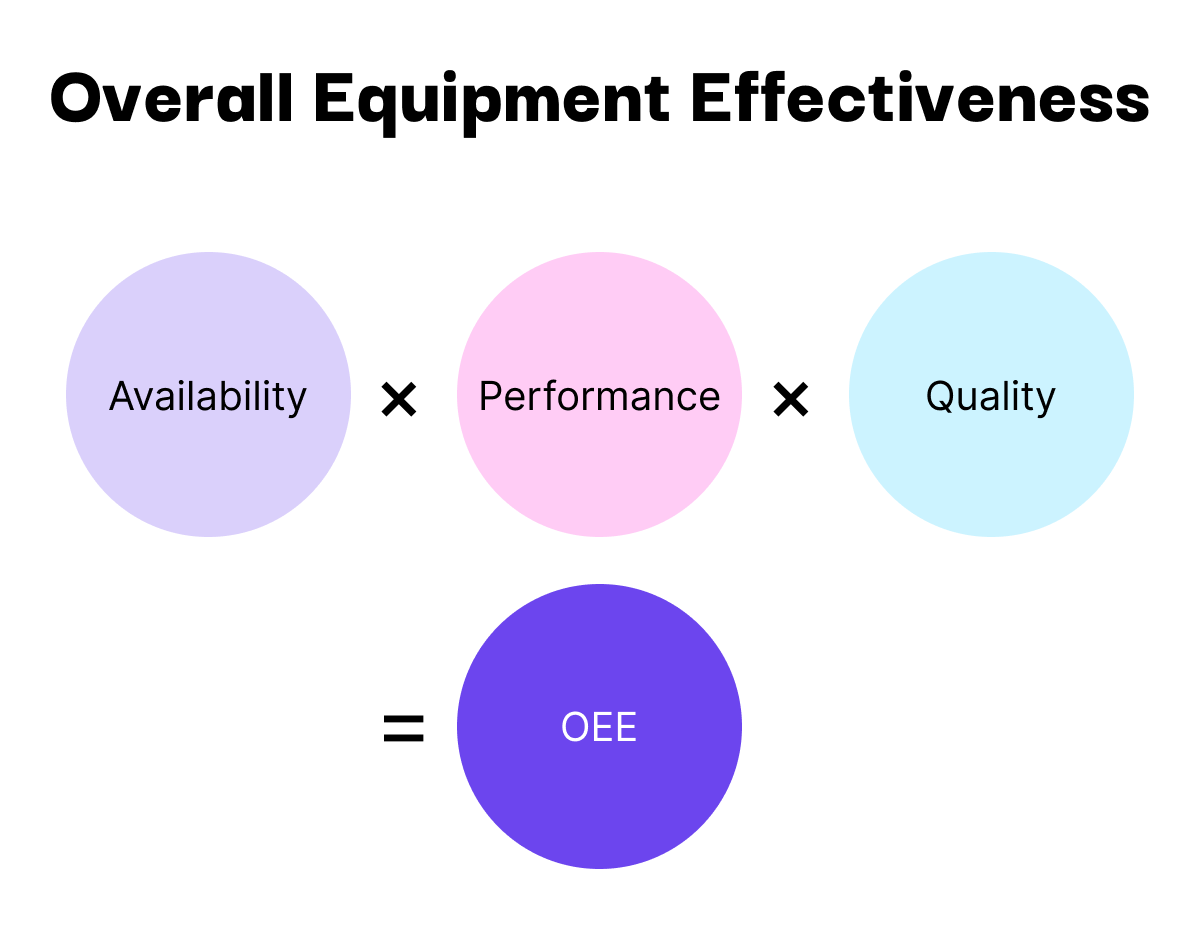
The OEE formula:
OEE = Availability x Performance x Quality
Now let's look at each component in a bit more depth.
1. Availability
Availability accounts for any events that stop production for a significant amount of time, such as breakdowns or setup changes.
Common Availability issues:
- Equipment failures and breakdowns.
- Long setup and changeover times.
- Operator unavailability.
- Lack of raw materials.
OEE availability formula:
Availability = (Actual Operating Time / Planned Production Time) x 100%
Learn more about Availability in OEE:
🔗 Free lesson on Availability in OEE
2. Performance
Performance measures the speed at which production runs relative to the maximum possible speed. Slow cycles, minor stops, and reduced machine speeds all affect this metric.
Common Performance issues:
- Suboptimal machine settings.
- Wear and tear on equipment reducing efficiency.
- Inconsistent raw material quality.
- Inefficient operator techniques.
- Poorly optimized production scheduling.
OEE performance formula:
Performance = (Ideal Cycle Time × Processe Amount) / Operating Time × 100%
Learn more about Performance in OEE:
🔗 Free lesson on Performance in OEE
3. Quality
Quality measures the percentage of good parts produced compared to total parts produced. It accounts for defects and rework.
Common Quality issues:
- Poor machine calibration.
- Inconsistent raw material quality.
- Operator errors.
- Process deviations.
- Lack of standardized operating procedures.
OEE quality formula:
Quality = (Good Units / Total Units Produced) x 100%
Learn more about Quality in OEE:
🔗 Free lesson on Quality in OEE
OEE waterfall charts
With OEE Waterfall charts, you get a more granular view of production inefficiencies compared to the typical availability x performance x quality OEE calculation.
This method provides a clear visualization of where time losses occur, helping you to pinpoint specific areas for improvement.
Key components of an OEE waterfall chart:
Total equipment time: The total time available for production, typically measured over a set period, such as a week or month.
Operating time: The time during which the equipment is scheduled for production. It accounts for planned downtime, such as scheduled maintenance or holidays.
Production time: The time when the equipment is actively producing, excluding both planned and unplanned stops.
Valued operating time: The effective production time during which only good-quality products are manufactured at optimal speed.
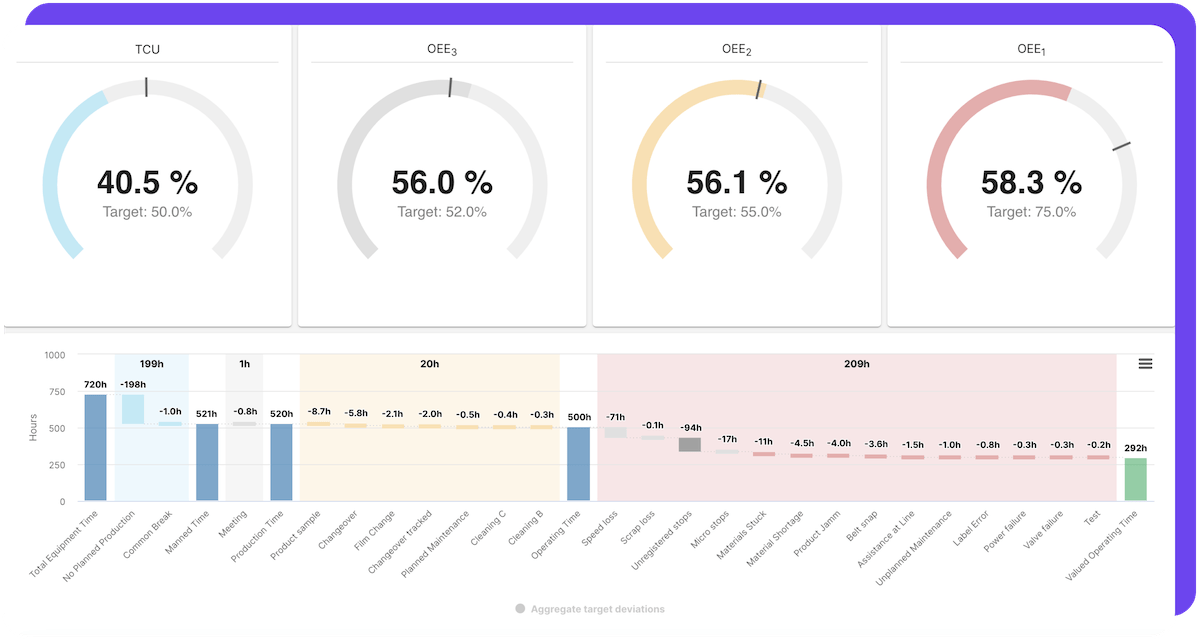
Factbird’s OEE Waterfall Chart introduces multiple ways to calculate OEE to help you and your teams identify areas for easier improvements:
OEE1: Calculated as the ratio of Valued Operating Time to Operating Time. It reflects losses during operation, such as equipment failures or minor stoppages.
OEE2: Determined by dividing Valued Operating Time by Production Time. This metric accounts for batch-specific non-operation losses, including changeovers and cleaning.
OEE3: The ratio of Valued Operating Time to Total Equipment Time, encompassing all potential losses, including unplanned downtime and lack of orders.
Total Capacity Utilization (TCU): Represents the overall utilization of the equipment's total available time, providing insight into the asset, line, or site's productivity.
🔗 Get a full overview of Factbird’s OEE Waterfall chart
A quick example of OEE calculation
First of all, here is the data we will use to calculate OEE:
- Total Equipment Time: 168 hours in a week.
- Operating Time: After accounting for various downtimes (e.g., maintenance, changeovers), the equipment ran for 74 hours.
- Ideal Production Rate: 240 units per minute.
- Actual Production Rate: 161 units per minute.
- Total Units Produced (week): 710,000 units.
- Defective Units (week): 35,500 units.
Based on that information, here is an example OEE calculation:
Availability: Operating Time / Total Equipment Time = 74 hours / 168 hours = 44%
Performance: Actual Production Rate / Ideal Production Rate = 161 / 240 = 67%
Quality: (Total Units Produced - Defective Units) / Total Units Produced = (710,000 - 35,500) / 710,000 = 95%
OEE: Availability × Performance × Quality = 44% × 67% × 95% = 28%
For a more detailed walkthrough and additional examples, including an example OEE calculation using the waterfall method, check out our comprehensive guide on OEE calculation:
🔗 How to calculate OEE (including free excel template)
Industry benchmarks for OEE
While a 100% OEE score is theoretically ideal, in reality, you’ll aim for more realistic OEE scores like these:
World-class OEE: 85% or higher
Typical OEE: 60-80%
Poor OEE: Below 50%
These benchmarks vary by industry. For example, pharmaceutical manufacturers often achieve high OEE numbers due to highly automated processes, strict quality controls, and minimal waste.
In contrast, food producers like bakeries may have lower OEE because of greater process variability, manual handling, and inherent production losses that are harder to eliminate.
🔗 An overview of OEE benchmarks and real-life examples
Step-by-step guide to implementing OEE calculation
Here’s a brief overview of how to implement OEE calculation in your organization.
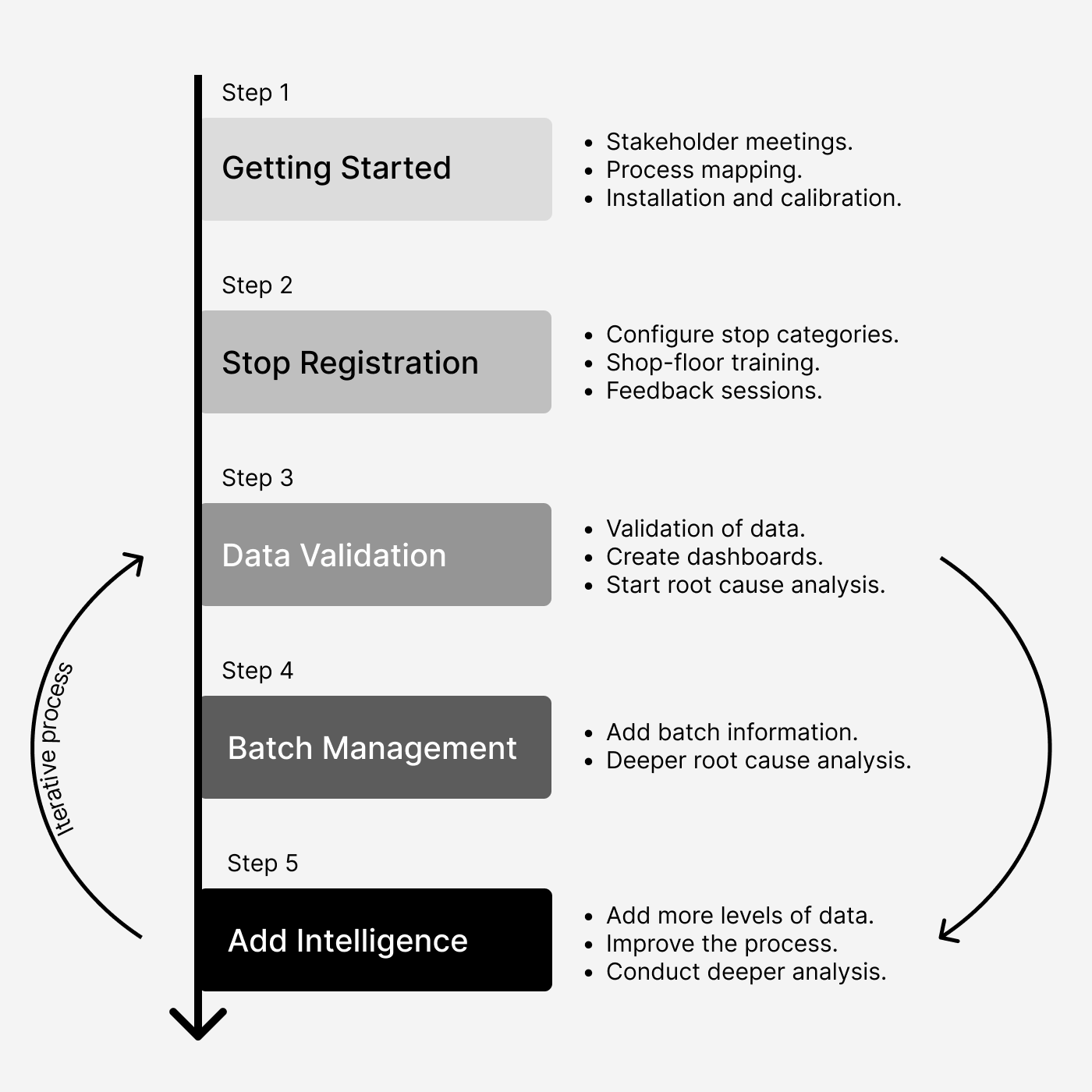
1. Getting Started
Get buy-in from stakeholders, install sensors, configure data collection protocols, and ensure all hardware and software components are correctly integrated.
2. Stop Registration
Define and categorize the reasons for production stoppages. Introduce a structure for operators to log stops, facilitating the identification of patterns and root causes of downtime.
3. Data Validation and Visualization
Regularly verify the accuracy of collected data. Develop dashboards and visual tools to represent this data clearly, enabling stakeholders to monitor performance and identify areas needing attention.
4. Batch Management
Organize production data by batches to analyze performance at a granular level. This approach helps in understanding variations between different production runs and optimizing processes accordingly.
5. Adding Intelligence
Now you have the base you can add complexity. You can start leveraging advanced analytics and machine learning to gain deeper insights from your OEE data. Implement predictive maintenance and other proactive strategies to enhance overall equipment effectiveness.
You can get a thorough overview of this OEE implementation framework here:
🔗 Best practices for implementing OEE calculation
Next steps and further learning
And there you have it. That is our quick guide to OEE. Would you like come more resources that help you become an expert in OEE? You can explore these:
🎙️ Podcast on the strengths and weaknesses of OEE
By mastering OEE, you can significantly improve productivity, reduce waste, and drive continuous improvement. I hope this article helps you on your operational excellence journey!