The strengths and weaknesses of overall equipment effectiveness (OEE)
Manufacturing Matters Ep. 1
Zoe Karasch, Sales Manager DACH, Factbird
Release Date: March 11, 2024
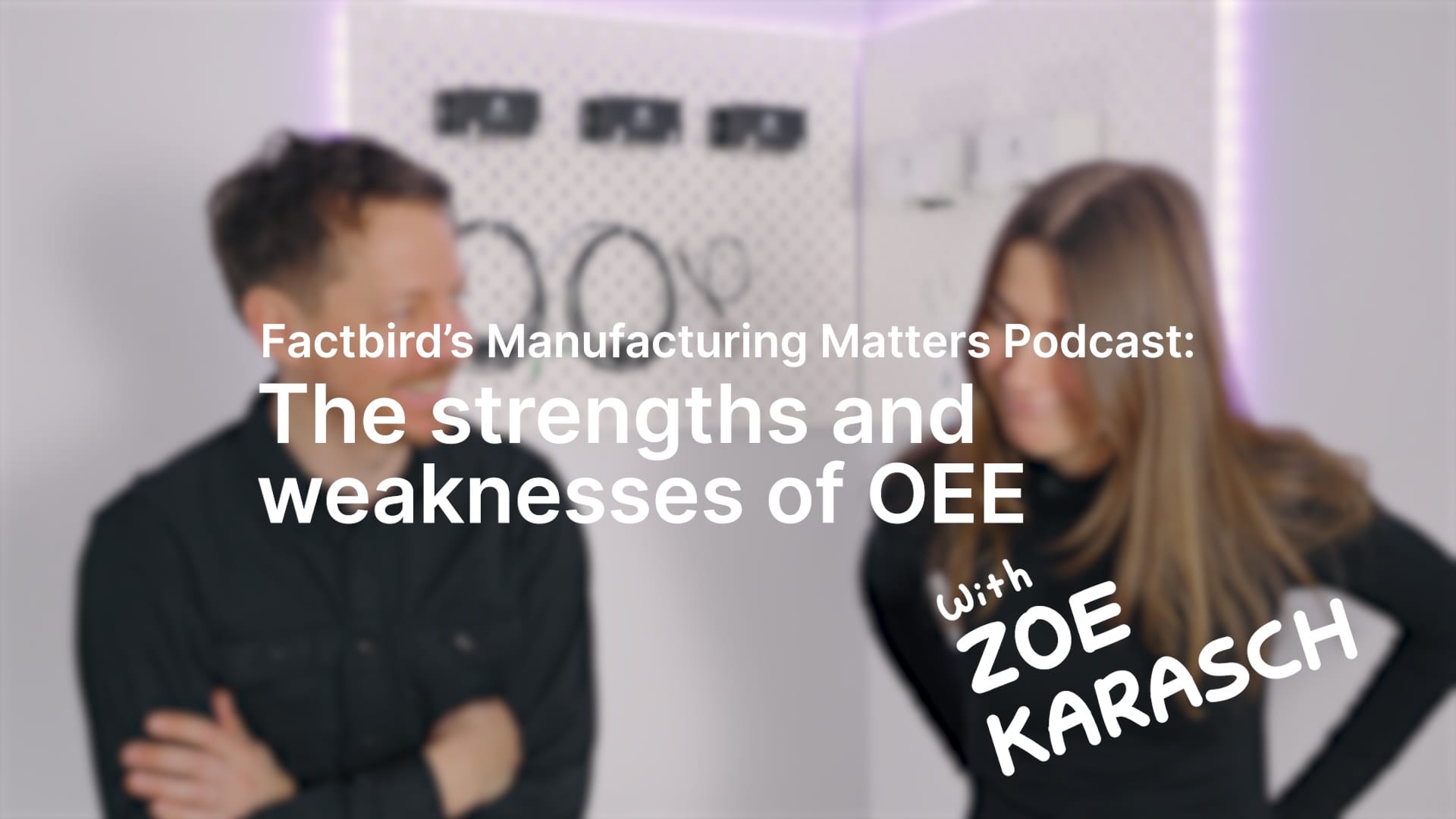
- OEE is a useful manufacturing metric for assessing and improving production efficiency.
- Factbird has four distinct OEE measurements to target different production weaknesses.
- Businesses use OEE to gain objective, comparative insights into efficiency to survive in competitive markets.
- Strengths of OEE include a comprehensive view of equipment effectiveness and areas for improvement.
- Weaknesses include its relative nature, its ill-fit for non-discrete production systems, and difficulty attributing improvements to specific actions.
Overall equipment effectiveness (OEE) is a powerful metric for analysing production, identifying weaknesses, and tracking progress. We spend a lot of time talking about how useful OEE is at Factbird, as it’s a much-valued part of our manufacturing intelligence solutions.
But is it the right tool for the job of increasing efficiency all of the time?
In this episode of the Manufacturing Matters Podcast, I talked to Zoe Karasch, the Sales Manager for the DACH region at Factbird, about her opinions on the strengths and weaknesses of OEE.
She has over three years of experience working with manufacturers, helping (very) large and small companies make their operations more efficient, saving them millions thanks to reducing waste and increasing efficiency. Here’s a summary of what she had to say.
What is OEE?
The textbook definition of OEE from Nakajima in TPM: Total Productive Maintenance is that it equals Availability x Performance x Quality and then you can read more into how each of those components is calculated.
But every company tends to have its own definition. This is often because manufacturers have different needs and move around certain downtime reasons between the three components of OEE.
At Factbird, the automated analysis performed by our OEE software departs from the original definition to suit modern manufacturing needs.
We have broken up OEE into four separate measurements that help bring to light specific weaknesses in production and have tweaked the categories certain downtime events fall under.
In OEE1, we essentially include quality losses, performance losses, and unplanned availability losses because all of these are avoidable.
In OEE2, we include availability losses from changeovers. This is meant to uncover improvements in planning and changeover processes.
In OEE3, we have planned availability losses that occur while operators are at work. This is used to discover “unused” staff capacities.
Finally, OEE4 (aka TCU, or Total Capacity Utilisation) includes all planned downtime, so weekends or night shifts where there is no planned production. This is separated to show the buffer capacity.
In the end, the most important thing is to have consistency in how OEE is calculated.
Why do businesses use OEE?
In today’s globalised environment, every business is fighting for survival. Manufacturers in particular need to be as efficient as possible to cope with drops in demand, more competition, struggles with finding talent, and supply shocks.
For manufacturing companies, a large portion of the necessary efficiency gains will be generated on the shop floor. There, time truly is money. So we need to know for a fact how effective each asset is and where there is potential for improvement.
OEE is a great way to measure that because it is objective. It is a tool that can be used for comparison with industry benchmarks, across production sites, between similar assets, between shifts, and more.
What are the strengths of OEE?
OEE is a tried-and-tested method for pinpointing downtime and increasing overall effectiveness.
A big strength of OEE is that it’s an objective number that contains a lot of the information that you want to know when figuring out the effectiveness of your equipment. For example, comparing the number of pieces produced between two machines won’t give you the full picture; you need to factor in what speed it could potentially run at, how many stops there were, whether they were planned or unplanned, etc.
So, on a micro level, it includes all factors and paints the full picture of your asset in one number. And then you can dig into the individual components of OEE to get a good idea of where to start to improve your assets.
What are the weaknesses of OEE?
OEE is a relative number. So, a weakness that it has is that it won’t tell you if your production is good or bad when used in isolation. Its value comes when comparing machines or sites, or looking at trends over time.
Another weakness is that, counterintuitively, it is possible that an OEE of 100% is not ideal for your business. This comes back to the LEAN concept of just-in-time production, meaning producing what is needed, when it is needed, and in the amount needed. So if your bottleneck is not running at 100%, there is no need for other machines to overproduce and waste time and resources. Ask questions like “are we measuring the bottleneck?” and “how much buffer capacity do we want?”
Additionally, if you see an improvement in OEE, it is very hard to determine which department or action is responsible. A factory is a complex place with many moving parts, so attribution and replication can be tricky.
Finally, OEE is made for discrete production as it comes out of Toyota, so production lines where you have a “one piece flow” happening. When you move into batch production, such as in the pharmaceutical industry, then OEE is not quite as strong.
Further reading
I hope you found this short exploration of the strengths and weaknesses of OEE interesting. I’d recommend checking out the following links if you would like to learn more about OEE:
- In-depth article: Find out how to calculate OEE (with examples)
- OEE Case Study: See how Wozniak drives operational excellence with data
- Factbird’s OEE software: Benefit from a live view of your OEE with Factbird
- OEE training services: OEE training
- Free trial: Try Factbird's production monitoring and OEE solutions for yourself
Remember to subscribe to Manufacturing Matters to get notified when the next episode is available on Spotify, Apple Podcasts, YouTube, Amazon Music, and other popular podcast directories.