How to make your manufacturing processes more resilient
Manufacturing Matters Ep. 11
Kenneth Ranzau, Key Account Manager, OMRON
Release Date: July 22, 2024
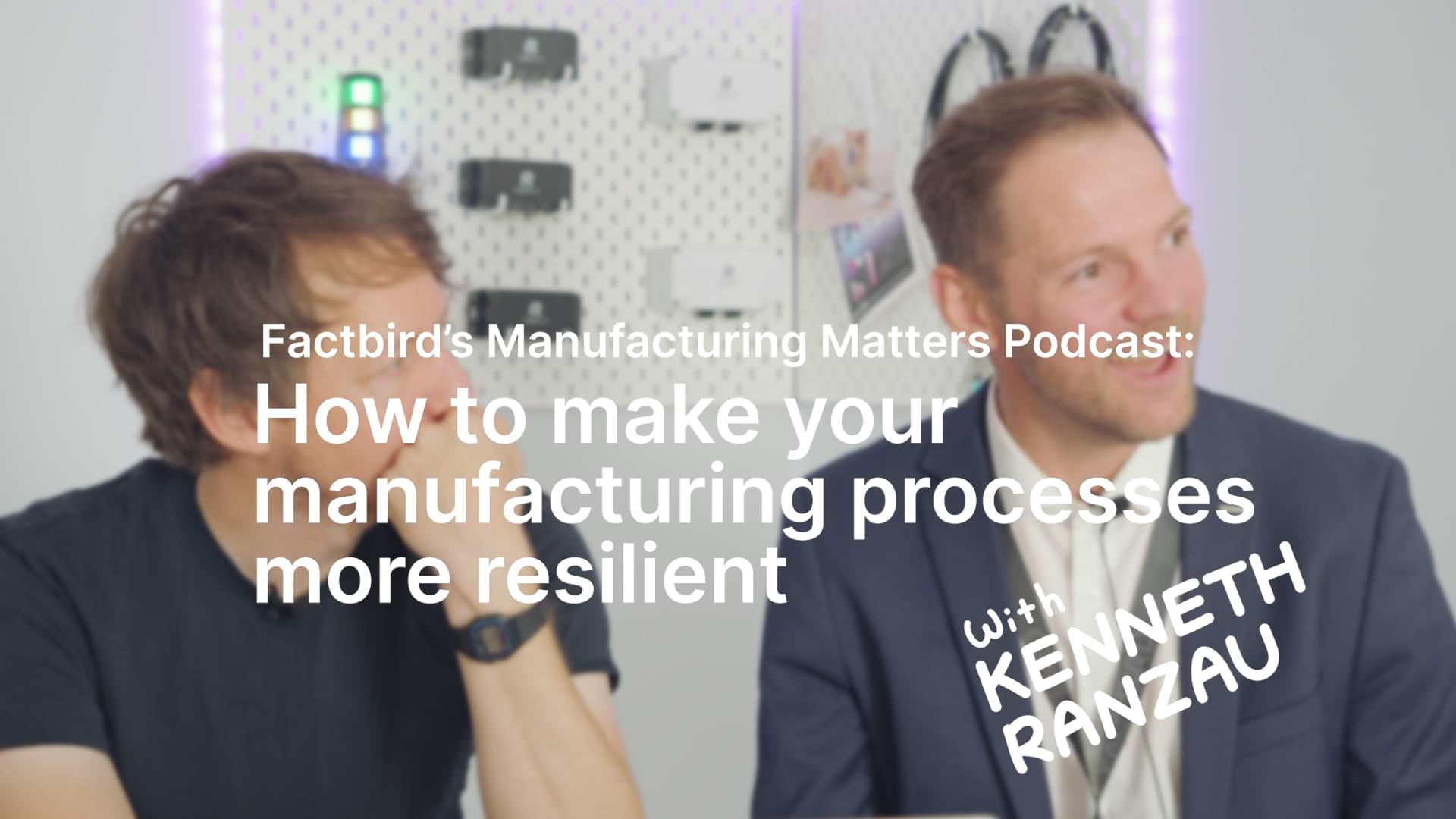
In the ever-evolving world of manufacturing, resilience has become a key factor in maintaining efficiency and ensuring consistent production.
In Episode 11 of the Manufacturing Matters podcast, I had the pleasure of speaking with Kenneth Ranzau from Omron Europe, a company dedicated to empowering people through automation and flexible manufacturing solutions. Omron is a major, global manufacturer of Programmable Logic Controllers (PLCs), sensors, and other components used for automation in manufacturing.
Read on as Kenneth shares his valuable insights on building resilient manufacturing processes and the importance of data in achieving this goal.
What is resilience in manufacturing?
Resilience in manufacturing is defined by reliability and awareness. It involves creating systems that can predict and prevent disruptions, ensuring that operations continue smoothly even in the face of challenges.
You can also describe resilience as the ability to withstand and quickly recover from disruptions, ensuring reliability and awareness across all processes.
As Kenneth puts it, resilience in manufacturing "means that you are aware of what is ongoing in your production and you are doing something about it, just in time. It’s also about reliability, and ensuring that you have production up and running all the time, and being flexible."
“To be able to have resilience, you need data.”
Kenneth Ranzau, Key Account Manager, OMRON
Why is resilience important?
Resilience in manufacturing was brought into sharp focus during the COVID pandemic. Global supply chain disruptions led to events like the 2020–2023 global chip shortage, which still reverberates through industries today.
According to the World Economic Forum in a 2022 paper, “Supply chain disruptions continue to destabilize global value chains and are undermining the prospects of long-term growth and prosperity. In a fast-changing world, manufacturing companies are now forced to design and roll out new strategies, and to develop the right set of capabilities, to build resilience across their entire value chains.”
On top of this, there are shortages of skilled workers, which is putting pressure on manufacturers around the world. In the US, for example, there are 622,000 manufacturing job openings yet to be filled as of January 2024, according to the U.S. Chamber of Commerce. Making manufacturing more resilient to labor shortages and the wave of retirements that the industry is now facing is something on the mind of most plant managers.
Capturing data
The first step of using data to build resilience into your production processes is capturing accurate, real-time data.
Here are some examples of how to capture data on production lines.
PLC data:
Using OMRON and Factbird, it is possible to collect data directly from programmable logic controllers (PLCs) to monitor machine performance and downtime. There are three options for doing this: Don’t touch, Read out, and Total control. The video below goes into the details of how these options work.
Plug-and-play edge devices:
When the wanted data isn’t already available, it’s possible to retrofit unobtrusive systems such as Factbird DUO that collect real-time insights for production processes.
Integration with OPC servers, such as Kepware:
It’s possible to read PLC tags with a Kepware setup and forward the tags of interest to cloud software for analysis, such as Factbird’s cloud app.
Capturing data is the first step, but using that data to make informed decisions is where the real value lies. Let’s take a look at that now.
Examples of using data to improve resilience
Here are some examples of how resilience comes into play when put into application in the manufacturing world.
Preventative and predictive maintenance:
By anticipating potential issues before they occur based on equipment time or usage, preventative maintenance helps manufacturers reduce unexpected downtime and maintain continuous production. Predictive maintenance takes this a step further by using real-time data such as condition monitoring and anomaly detection to accurately predict when maintenance is needed, helping to avoid breakdowns, extend the lifespan of equipment, and avoid unnecessary maintenance tasks. Read more: Preventive Maintenance for manufacturing explained.
Supply chain management:
Resilient manufacturing systems can effectively handle supply chain disruptions by utilizing alternative material sources and quickly reallocating capacity. This ensures continued value creation, even during unexpected challenges. Additionally, a resilient and transparent supply chain supports just-in-time (JIT) manufacturing by minimizing delays and ensuring timely production. This integration helps maintain efficiency, reduce inventory costs, and enhance overall production agility.
Production planning:
Effective production scheduling requires accurate data on machine availability, workforce capacity, and order requirements. By using historical and real-time production data, manufacturers can create optimized schedules that maximize resource utilization and meet delivery deadlines.
Overall Equipment Effectiveness (OEE):
Real-time production data is critical for calculating OEE, which measures the efficiency of manufacturing processes. By analyzing data on machine availability, performance, and quality, manufacturers can identify and prioritize areas for improvement and optimize their operations.
Batch Control:
Production data helps in managing batch processes by ensuring that each batch meets the required specifications. This includes tracking parameters such as temperature, pressure, and mixing times. By analyzing this data, manufacturers can ensure consistency and quality across batches, reduce waste, and improve overall process control.
Energy consumption management:
Analyzing production data related to energy usage helps manufacturers optimize energy consumption and reduce costs. By monitoring energy use across different machines and processes, companies can identify inefficient equipment, peak usage times, and opportunities for energy savings. This data can be used to implement energy-efficient practices and technologies, such as adjusting machine settings during low-demand periods or investing in more efficient machinery. You can read about how Danfoss improved their energy efficiency in this case study: How Danfoss achieved a 33% reduction in equipment energy consumption.
Conclusion
Building resilient manufacturing processes is essential for maintaining efficiency and staying competitive in today's market. Kenneth's insights from Omron highlight the importance of reliability, awareness, and the effective use of data in achieving resilience.
By implementing these strategies, you can enhance your operations, reduce downtime, and move towards a more automated future.
For more insights and practical tips on resilience in manufacturing and other industry topics, stay tuned to Manufacturing Matters. If you have any questions or topics you’d like us to cover, feel free to reach out to us via LinkedIn or email.
And please remember to subscribe to Manufacturing Matters to get notified when the next episode is available on Spotify, Apple Podcasts, YouTube, Amazon Music, and other popular podcast directories.