OEE Uplift: A structured approach for OEE improvement
Manufacturing Matters Ep. 8
Mikkel Rauff Simonsen, Senior Manager of Plant Optimization, Danish Crown
Release Date: June 10, 2024
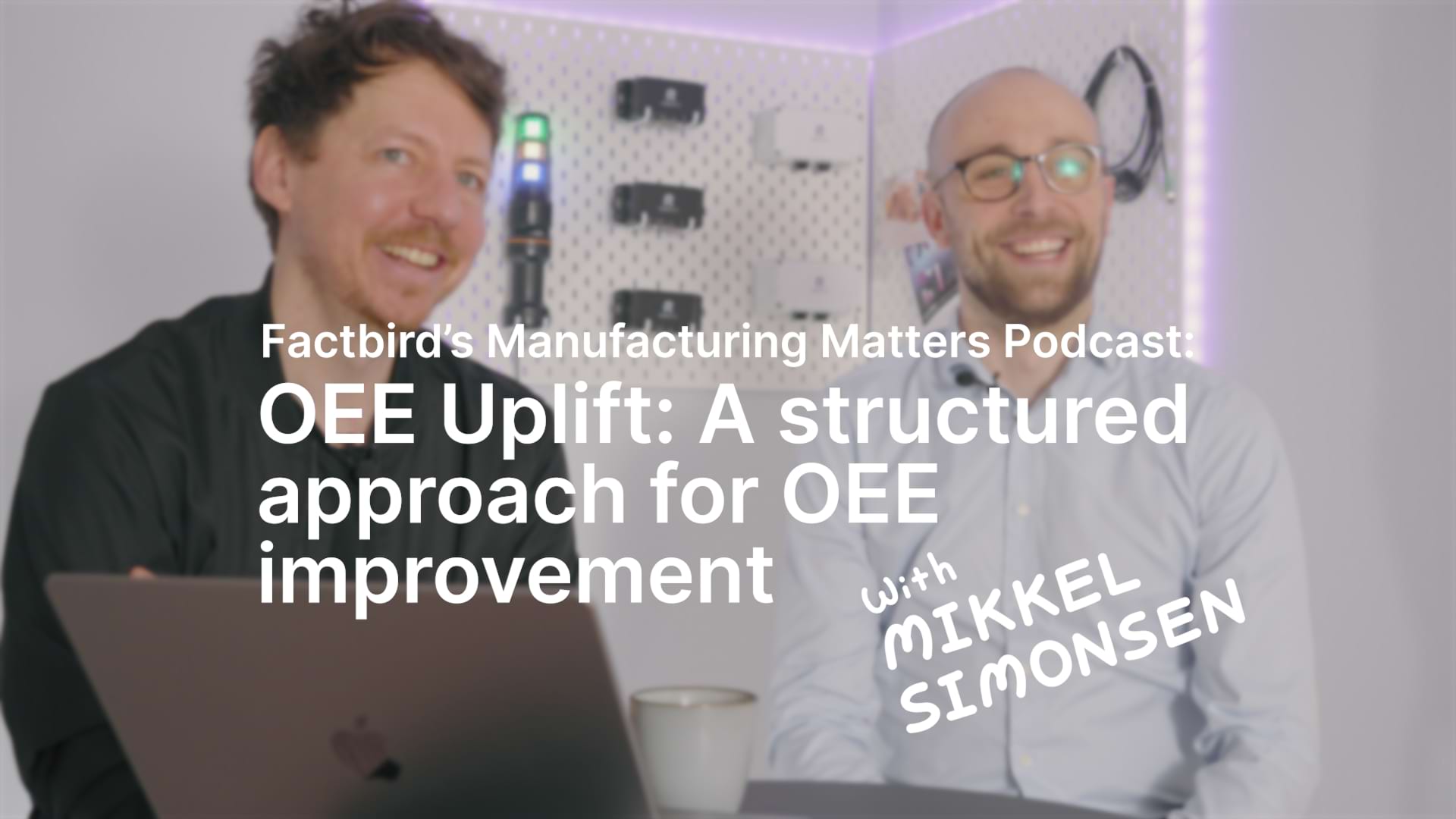
- Insights from OEE and digitization expert Mikkel Rauff Simonsen
- Improve OEE with the OEE Uplift Approach sprint model
- Cockpit: Centralize and visualize OEE data with dashboards to identify weaknesses
- Planning: Hold a kickoff meeting with stakeholders to agree on data-driven improvements
- Analysis: Conduct in-depth OEE analysis, set baselines and targets
- Implementation: Execute action log items as part of daily operations and track performance
- Standardize: Train operators, create SOPs, and distribute to similar lines
- Review: Reflect on performance changes and process improvements
Overall Equipment Effectiveness (OEE) is an important KPI for manufacturers who want to improve their operations using data. It sits alongside throughput, quality, batch, and shift performance analysis as one of the major reasons manufacturers implement Manufacturing Intelligence solutions like Factbird.
But OEE is just a number. To make gains, you need a structured approach to improvement.
In episode nine of the Manufacturing Matters podcast, Mikkel Rauff Simonsen, who has been working with performance optimization for over 15 years, generously shared his approach to OEE improvement: the OEE Uplift Approach.
Let’s dig in!
Understanding the OEE Uplift Approach
The OEE Uplift Approach is a structured improvement process designed to enhance Overall Equipment Effectiveness (OEE) that has been developed with the experience of a lot of operators, leaders, and lean experts from a broad range of companies.
It’s a sprint model that provides a systematic and organized framework for implementing OEE improvements. It helps teams focus on one issue at a time to solve and uplift OEE. Once you finish that sprint, you move on to the next challenge.
The OEE Uplift Approach is a tool that offers an agile response to challenges, provides a structured improvement process, fosters rapid iteration and experimentation, emphasizes continuous monitoring and adaptation, enhances collaboration and accountability, delivers rapid results and ROI, aligns with lean and continuous improvement principles, and offers flexibility and adaptability to changing circumstances.
Why the OEE Uplift Approach is important
Improving OEE is a common KPI for optimizing manufacturing operations and achieving a competitive advantage. OEE is just a number, but by enhancing it, you can realize real gains such as getting more out of your existing equipment, minimizing downtime, and increasing output. This leads to reduced costs, improved quality, and faster time-to-market, ultimately driving higher profitability and customer satisfaction.
But to realize improvements in OEE, you need to have a model for solving the challenges that you find when conducting an OEE analysis. Once you have data, you need to understand it and work with it. The OEE Uplift Approach offers a structured way of working with stakeholders and project leads to make improvements over and over again.
A common problem that manufacturers try to solve is reducing stops to have a more consistent flow of production. As an example, Mikkel brings up micro-stops, which is a stop category of many small stops of say 20 to 60 seconds, which can add up to a large chunk of your overall downtime. This is something many operations realize once they begin using tools like Factbird to automatically track stops. But in the data, you can only see that you have a problem with micro-stops. So, to understand it, you’ll want to use a structured approach such as the OEE Uplift Approach to understand the micro-stops and eliminate them.
Implementing the OEE Uplift Approach
The OEE Uplift approach comprises six essential steps, each designed to ensure a comprehensive and effective implementation.
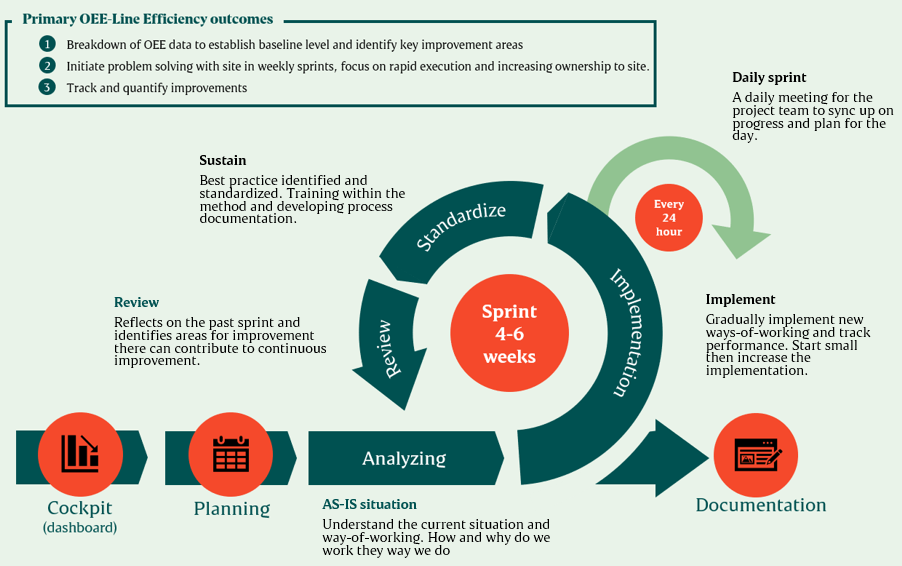
1. Cockpit
To start with, you will need a data hub or manufacturing intelligence system that brings together one or multiple data sources and visualizes OEE data in a dashboard. In the dashboard, you will be able to see granular information on the components that make up OEE and where there are weaknesses in your production.
2. Planning
Once you have the data and see there is room for improvement, you’ll have a kick-off meeting with your stakeholders. If you are in a lean improvement team, you’ll want to talk with people on the shop-floor and find out whether or not the analysis you have on micro-stops, for example, is the same as what they experience in their day.
Then you go into a dialogue about it with stakeholders and align on the improvement focus. This is important because you can't fix everything at once. If you want to improve micro-stops, for example, you can’t also focus on improving changeovers or improving unexpected technical breakdowns.
3. Analyzing
Now that you have defined what you want to improve, you go into a deep analysis of, for example, what’s causing the micro-stops. Here you can use frequency studies, Gemba, or other tools from Lean and Six Sigma to figure out what is happening.
Then you take your analysis back to the factory and create baselines. For example, in the last three months, you have seen that there are 50 minutes of micro-stops each day. Then you establish the target for the sprint, such as reducing the micro-stops from 50 minutes to 25 minutes per day. This should be something that is challenging but achievable. If you make it too hard, you will lose engagement in the process.
Importantly, before starting implementation, Mikkel focuses on workshops with teams and getting engagement. Get the team on the ground to provide their opinions and commit to solutions. This is so important as your team needs to own it and want to make the improvements themselves. If you just go in and tell people what to do, you will struggle to make changes.
Finally, you identify the actions you can take that will make the biggest impact while also being doable. This then goes into an action log.
4. Implementation
This phase is focused on taking the action log and making it part of day-to-day business.
Here, you gradually implement new ways of working and track performance via production data and with regular check-ins. In short, you want to take in information about the good days and focus on making them occur more regularly.
It’s also good to start small and then scale up to ensure manageable and sustainable changes.
5. Standardize
Now that you have made the change, you want to make it a standard operating procedure (SOP). You need to have this best practice that can be distributed to similar lines throughout your operations.
The SOPs require training, and they need to be visible for the operators and presented in a way that is easy for them to understand.
6. Review
Now you can reflect on your learning, not only on the performance changes, but also the uplift process—what went well and what went bad.
Then you write down your final review documentation and share it with all the relevant teams; include the focus of the uplift, the results, and the learnings from the process.
Success with the OEE Uplift Approach
The OEE Uplift approach is a powerful tool for optimizing manufacturing operations and fostering a culture of continuous improvement. I hope Mikkel’s insights and structured improvement processes help you achieve the improvement you want in your production environment.
For more insights and practical tips like the OEE Uplift approach and other operational improvement strategies, stay tuned to Manufacturing Matters. If you have any questions or topics you’d like us to cover, feel free to reach out to us via LinkedIn or email.
Remember to subscribe to Manufacturing Matters to get notified when the next episode is available on Spotify, Apple Podcasts, YouTube, Amazon Music, and other popular podcast directories.