Sustainable Change: Winning the long game in manufacturing
Manufacturing Matters Ep. 14
Benjamin Ravn, Plant Director for Albani / Royal Unibrew
Release Date: September 23, 2024
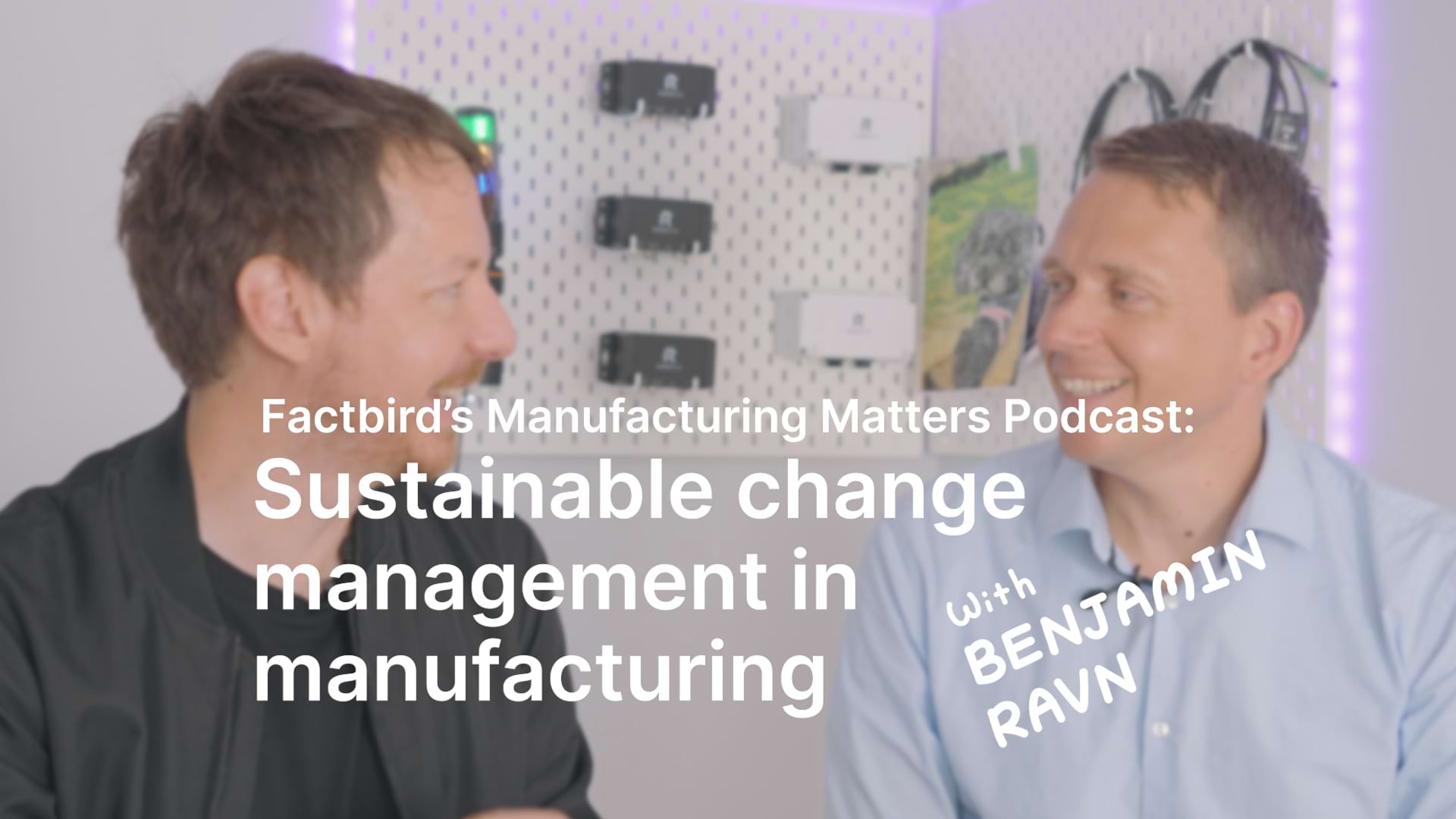
Summary:
- Sustainable change management involves implementing lasting transformations that endure beyond short-term goals.
- Benjamin Ravn, Plant Director at Albani/Royal Unibrew, emphasizes helping the whole person rather than just the employee.
- A structured framework with three enablers and three levers guides sustainable change.
- Leadership, behavior and engagement, and learning and development are enablers.
- Safety and quality, performance management, and strategic maintenance are levers.
In the latest episode of Factbird’s Manufacturing Matters podcast, we sit down with Benjamin Ravn, Plant Director at Albani/Royal Unibrew, to delve into the concept of sustainable change and its critical role in the long-term success of manufacturing companies.
Meet the expert: Benjamin Ravn
Benjamin Ravn is a manufacturing and management engineer who has dedicated more than 12 years to the fast-moving consumer goods (FMCG) industry.
For the past two years, he has served as the Plant Director at Albani, overseeing operations at Albani, Frem, and Nørrebro Brewhouse.
Albani’s parent company, Royal Unibrew, is a leading multi-beverage company with strong local brand portfolios, selling products in over 70 countries. Royal Unibrew has been a customer of Factbird since 2016.
Benjamin brings valuable insights into how organizations can build lasting transformations that not only improve profitability but also foster a culture of continuous improvement.
What is change management?
First, let's look at the stock standard definition of change management before digging into Albani / Royal Unibrew's approach to sustainable change.
In general, you can say change management is a systematic approach to guiding individuals and organizations through transitions, ensuring smooth adoption of changes. These changes can include cultural change, technological or infrastructure change, and changes to processes.
If you'd like to dig into change management so more, you can read the Harvard Business School's course on organizational change management and check out our previous podcast on change management advice for manufacturers.
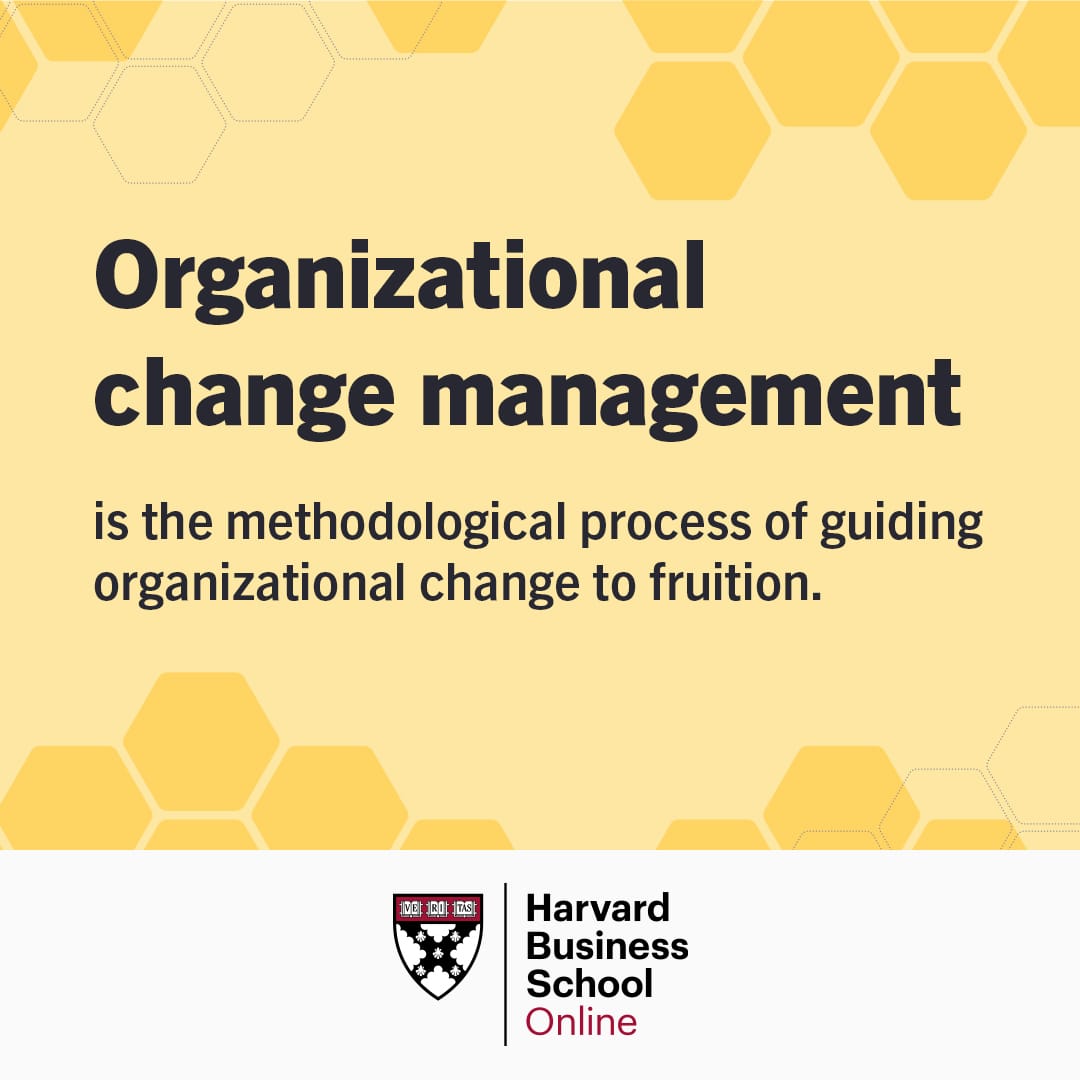
What is sustainable change management?
When Benjamin joined Albani, the leadership team was passionate about instilling a continuous improvement DNA within the organization. From talks about what they wanted to achieve with their time came the concept of sustainable change.
At Albani, sustainable change management refers to implementing transformations that are built to last, affecting all aspects of an organization—people, processes, and culture.
The goal was to create an organization where processes and improvements are not dependent on specific individuals but are ingrained in the company's fabric. This approach ensures that even if key personnel leave, the organization continues to thrive and improve.
"For us, sustainable change is a way to achieve success in the long run," Benjamin explains during the podcast. "Whenever we are deciding to run a transformation process, we do not look at only succeeding for a year or two years, but really building the organization and the competencies within the organization to achieve long-term success."
The human element
For Albani, sustainable change goes beyond transformation coming from technology and new processes but focuses on the people within the organization. As Benjamin says, “If we do not take care of them, then we do not achieve success in the long run.”
"We see the whole person," Benjamin says. "So, whatever you're dealing with at home or within your family, if you're sick or whatever, we try to deal with it all, making sure that we have a holistic view of that as well."
Why is sustainable change management important?
In short, it’s about building more profit, but you won’t engage people enough with simply that.
Typically, organizations will have a short-term goal of reducing waste, increasing OEE, or both. That makes more sense to drive change, but it doesn’t build the right focus for sustained change.
What Albani set out to do was to find a way to meet typical annual goals but also build success for the coming year as well. As Benjamin says, “So it’s not just a project or process we start and hire some consultants and do whatever, but we build it into the organization; that is key to us.”
To set up the success of Albani in the long run, they are aiming to set up each member of the organization for success. Sustainable change is crucial because it sets up both the organization and its members for long-term success.
By understanding employees' personal circumstances and supporting them holistically, leaders can better align expectations and foster a more committed workforce. This approach leads to higher engagement and lower turnover rates.
The sustainable change framework
To guide their efforts, Benjamin and the leadership team at Albani have developed a sustainable change management framework consisting of three enablers and three levers
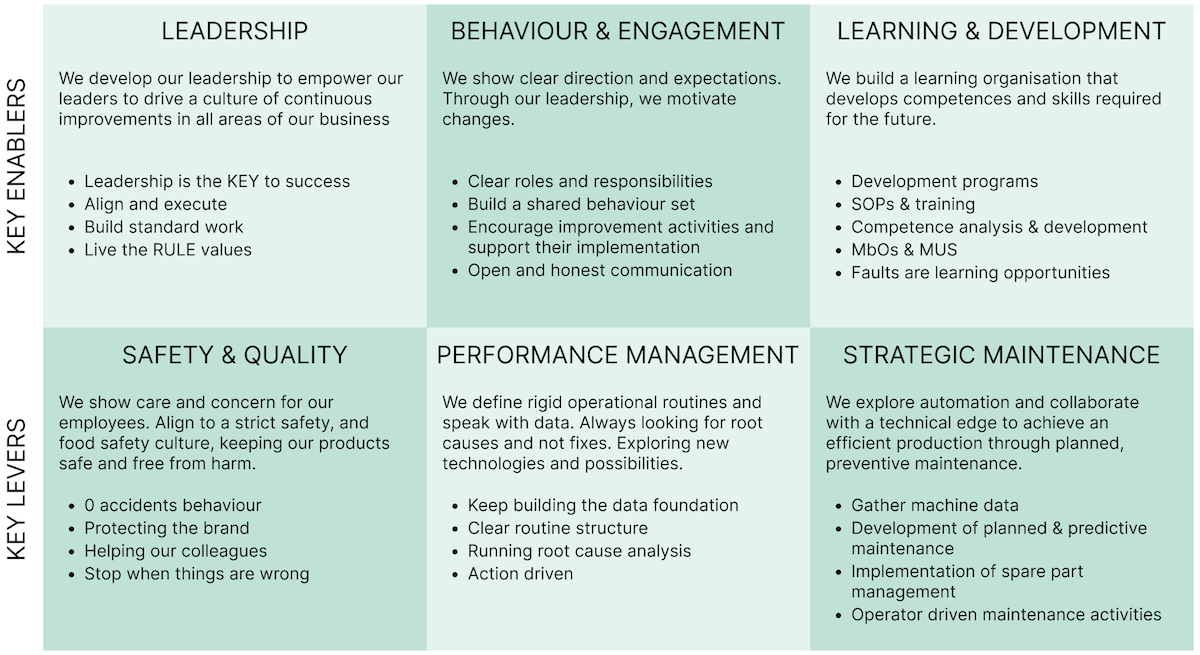
We’ll now explore in depth how this framework for sustainable change management works.
Enablers
The three enablers are:
- Leadership
- Behavior & Engagement
- Learning & Development
These are generic focal areas for sustainable change management . Whatever industry or company you are in, these three things should be a part of your organization.
Enabler 1: Leadership
The focus starts on leadership. Albani focuses on making sure that there is a shared understanding of the expectations, roles, and responsibilities of leaders.
It's both about performing daily tasks, such as registering hours, but also ensuring that the leadership has shared values.
A key part of good leadership at Albani is seeing the whole person. For example, Benjamin says, “It’s not just the employee or the eight hours that you are here. We see the whole person. Whatever you are dealing with at home, or within your family, or if you are sick, or whatever, we try to deal with it all and make sure that we have a holistic view.”
Key action examples:
- Leadership is the KEY to success: Sustainable change management starts with leadership.
- Royal Unibrew Leadership Expectations (RULE): Ensure all leaders share a common understanding of goals, values, and the desired organizational culture.
- Role modeling: Leaders must exemplify the behaviors they wish to see in their teams.
Enabler 2: Behavior & Engagement
According to Benjamin, “Whenever working with leadership, it’s natural also to look at behavior and engagement.”
Here, Albani focuses on how the organization works as a group. This involves addressing routines, communication styles, and cultural norms to build organizational commitment.
As Benjamin explains, it’s about “making sure that, not just within the leadership, we have a shared understanding of, you know, how we want to achieve zero accidents. What behavior do we need for that? What set of values do we need locally, but also at the group level?”
Key action examples:
- Clear roles & responsibilities: Understanding your role and others’ roles.
- Build a shared behavior set: Explicitly defining the desired culture and values.
- Open and honest communication: Not being afraid to speak up and communicate the good and the bad.
Enabler 3: Learning & Development
Learning and development are crucial for equipping employees with the skills needed for both current and future roles, fostering a culture of continuous improvement.
"We need to build a full learning mindset; eagerness to develop yourself," Benjamin explains. "And not just for the business purpose, but again, for the whole human being. If you want to learn pottery, that’s fine by me."
At Albani, the learning and development enabler consists of two main components:
- Standardized processes and training: Ensuring that there’s a clear understanding of their roles and the competencies required for each role, and a plan to build the competencies.
- Building a learning organization: Encouraging personal development beyond job-specific skills.
According to Benjamin, “If you have a learning mindset and a willingness to obtain new skills, that will slowly drip into your work as well. And you will start looking at, ok, now maybe we can do this differently, or this differently. We’ll change the way the organization works. So, it’s about how we as a company can help this process along.
An example for why this is important is that, for example, whatever you invest in safety, you get 2.5x back. It just makes sense for a company to invest in their employees.
Key action examples:
- Competency mapping: Identifying the skills and knowledge required for each role and assessing current capabilities.
- Personal development plans: Working with employees to create growth plans.
- Faults are learning opportunities: A culture of learning from mistakes rather than focusing on punishing them.
Levers
The three levers for sustainable change are:
- Safety, Quality & Food Safety
- Performance Management
- Strategic Maintenance
While the enablers set the foundation, the levers are the practical mechanisms that drive sustainable change within the organization.
Lever 1: Safety, Quality & Food Safety
In industries like beverage manufacturing, safety and quality are non-negotiable. This lever ensures that these critical areas are continuously improved and maintained.
"It's so easy to address. It makes sense for everyone that we want to take care of our people and we want to take care of the products we produce," Benjamin explains. “They are easy to exemplify behaviors. So saying, ok, if we all agree that whenever we walk around on the outside, that we want to follow the walkways, then we follow the walkways.”
Key actions:
- 0 accidents behavior
- Protecting the brand
- Helping our colleagues
- Stop when things are wrong
Lever 2: Performance Management
Performance management involves the systems, routines, meetings, and data structures needed to keep operations under control and drive improvement.
For Benjamin, part of this is "driving a stronger data foundation for meetings. We need more data present within our routines to make them more robust. And for making better decisions.”
But sustainable change is also about having clear structure, and as Benjamin puts it, “We build formal structures saying that the plant manager for this will be responsible for this and this, and the filling manager will be responsible for this. So it’s not bound to me being in the chair. So really standardized work.”
Key actions:
- Keep building the data foundation
- Clear routine structure
- Running root cause analysis
- Action-driven
Lever 3: Strategic Maintenance
Strategic maintenance shifts the focus from reactive to proactive maintenance, reducing downtime and extending equipment life.
"Being quite a conservative industry, we haven't worked on being proactive in the maintenance area," Benjamin admits. "There’s a lot of firefighting and a lot of breakdowns and things where we have no idea what's going on."
“So, for us, looking at that strategically as well, will benefit us on all the other (levers) as well.”
Here, Albani is looking at things like preventive and predictive maintenance and energy consumption monitoring, for example.
Key action examples:
- Gather machine data
- Development of planned and predictive maintenance
- Implementation of spare part management
- Operator-driven maintenance activities
Royal Unibrew is a leader in the industry
While talking about energy tracking, Benjamin highlights that Royal Unibrew is one of the best in the industry when it comes to meeting European sustainability regulations.
Royal Unibrew is on track to be CO2 neutral by 2025 in scope one and two emissions, showcasing their commitment to environmental responsibility.
This aligns with their efficiency goals and the drive to be a preferred place to work.
“We really want to be a place where people seek to work, you know, and that's not only Albani; that is Royal Unibrew,” Benjamin notes. “Our strategy is to be the preferred choice for both the customers, consumers, future shareholders, and employees.”
Actionable steps for manufacturing leaders
Here is a summary of helpful actions you can take to develop their own sustainable change framework.
- Assess your organization: Evaluate your current processes, culture, and leadership alignment.
- Develop a framework: Create your own set of enablers and levers that align with your organization's goals and industry.
- Engage your team: Involve employees at all levels in defining values and identifying areas for improvement.
- Invest in leadership development: Provide training and resources to develop effective leaders.
- Foster a learning culture: Encourage continuous learning and personal development.
- Prioritize safety and quality: Make safety and quality non-negotiable aspects of your operations.
- Leverage data: Use data analytics, including production data, to inform decisions and drive performance improvements.
- Implement strategic maintenance: Shift from reactive to proactive maintenance strategies.
- Monitor and adjust: Regularly review your strategies and make adjustments as needed to ensure long-term success.
Conclusion
Sustainable change is not a one-time initiative but an ongoing commitment to building an organization capable of long-term success.
By focusing on leadership, behavior, and engagement, and learning and development—and by leveraging safety, quality, performance management, and strategic maintenance—companies can create lasting transformations that benefit both the organization and its employees.
As Benjamin aptly puts it:
"You know, the old saying, if you want to go fast, go alone. If you want to go far, go together."
For more insights and practical tips on continuous improvement, lean manufacturing, and other industry topics, stay tuned to Manufacturing Matters. If you have any questions or topics you’d like us to cover, feel free to reach out to us via LinkedIn or email.
And remember to subscribe to Manufacturing Matters to get notified when the next episode is available on Spotify, Apple Podcasts, YouTube, Amazon Music, and other popular podcast directories.