Navigating sustainable packaging challenges in manufacturing
Manufacturing Matters Ep. 3
Sterre Van Empelen, Account Executive BeNeLux, Factbird
Release Date: April 1, 2024
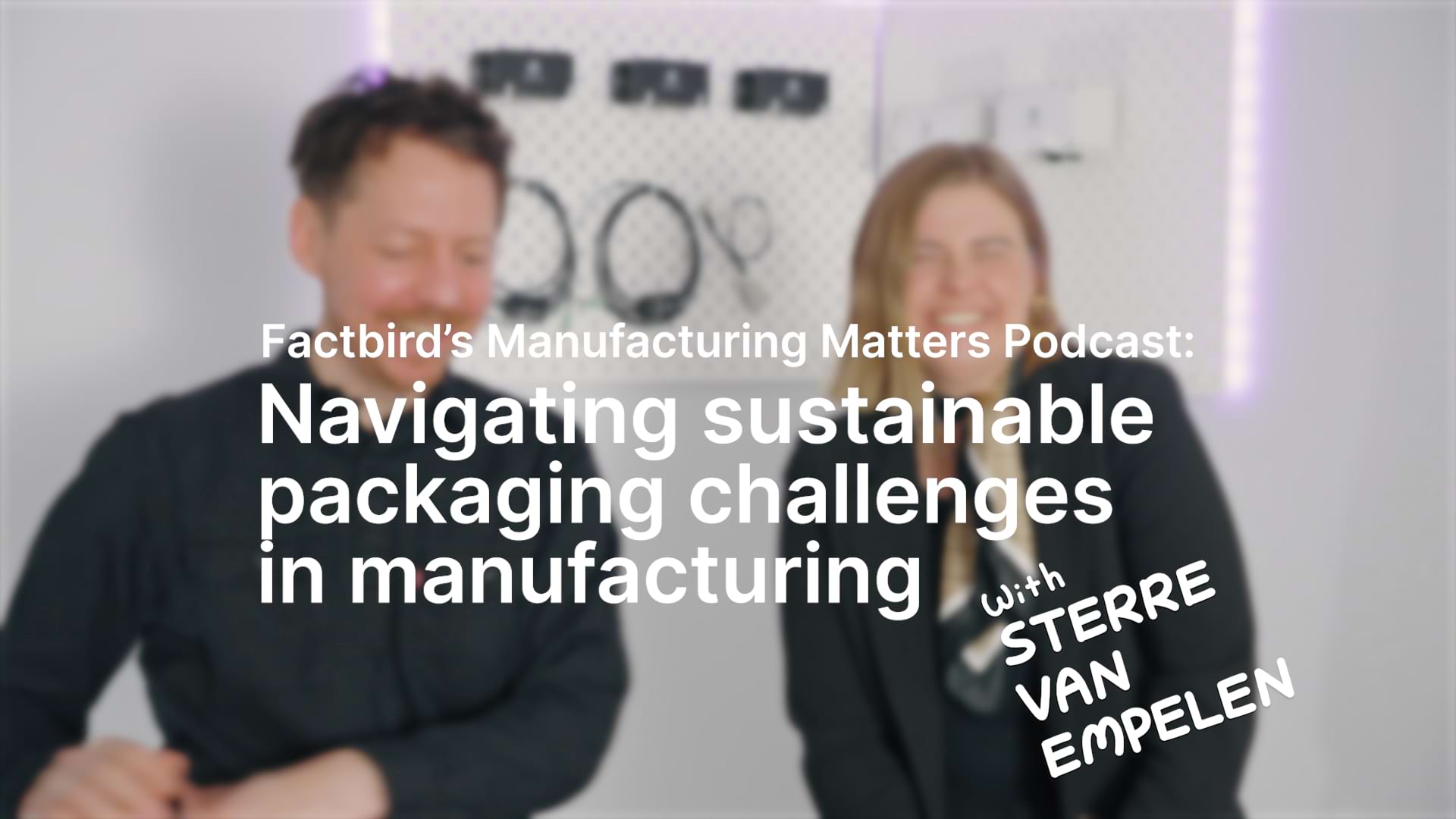
- The shift towards sustainable packaging is driven by demand, necessity, and regulations.
- Key challenges: machinery adaptation, cost management, material compatibility, and brand impact.
- Effective strategies include thorough testing of materials and real-time production tracking.
- Emphasis on innovation and getting ahead of regulatory compliance for successful sustainability transition.
In this episode of Manufacturing Matters, we talk about challenges around sustainable packaging in the manufacturing sector. Joining us is Sterre Van Empelen, Account Executive for BeNeLux at Factbird, an expert with significant lean manufacturing experience, particularly in the food and beverage sector. Sterre brings a wealth of knowledge from her time helping companies increase productivity and reduce costs while navigating the complex terrain of sustainable practices.
Defining sustainable packaging
The manufacturing industry, particularly the production of food and beverages as fast-moving consumer goods (FMCG), is currently facing a transformative shift towards sustainable packaging. Consumer demand, environmental necessity, and regulatory pressures all play a role in this switch to more sustainable packaging, making it a crucial issue for manufacturers.
Sustainable packaging in manufacturing involves using life cycle assessments to develop packaging solutions that reduce environmental impact and ecological footprint. Solutions can involve switching to materials with high recyclability and recycled content, reducing the use of single-use plastics, and reducing the complexity of materials used in packaging with mono-materials to improve recyclability and reduce waste.
Sterre explains that sustainable packaging involves more than just selecting environmentally friendly materials; it's about integrating practices that reduce waste, improve operational efficiency, and align with evolving consumer and regulatory expectations. Challenges arise from machinery limitations, material costs, and adapting to new standards without compromising product quality.
Manufacturing challenges with sustainable packaging
Manufacturers face challenges such as balancing recyclability with the carbon footprint, addressing scrap and rework, and navigating the complexities of packaging materials and design that can vary significantly by region and product type.
One of the primary challenges in transitioning to sustainable packaging is the balance between economic and operational feasibility and environmental responsibility. Sterre highlights that packaging issues such as material changes can lead to increased downtime and scrap rates, especially in the food and beverage industry.
Figuring out what works with existing machinery when changing materials is a big part of the transition process. During the podcast, Sterre offers examples where problems with new packaging have been detected with the help of Factbird:
- Bags falling apart during the sealing process because the new materials are not as robust as the original packaging materials.
- New paper or glass packaging being harder for existing machinery to grip and move than the original plastic packaging.
- There have been cases where using paper tape instead of plastic tape has resulted in production issues due to the new tape being less sticky.
- Labels and product identification not properly adhering to new packaging materials.
Additionally, sustainable options often come with higher costs. Companies in the food and beverage industry typically operate with low margins, especially those that produce cheaper, more commoditized goods. Balancing the need to improve sustainability with new packaging while staying competitive on costs represents a massive challenge for manufacturers.
Finally, Sterre mentions that packaging can impact the brand image. For example, thick glass bottles can give beverages a more premium feel, but switching to thinner glass bottles or even plastic can be less invasive for the environment.
Strategies for better implementation of sustainable packaging
Manufacturers looking to transition to more sustainable packaging must consider several factors. Here are some suggestions for what to look out for.
Don’t buy new packaging materials in bulk without very thorough testing across all product types. Incompatibility of new materials with existing equipment is quite common, and bulk purchases of packaging material that cannot be used will lead to a lot of waste and added costs.
Clearly tracking batches and monitoring equipment with manufacturing intelligence systems like Factbird helps manufacturers catch problems when they do occur. The digitised and automated collection of production data helps businesses quickly get to the root cause of problems, such as tape not sticking or packaging falling apart during a particular stage of the production process.
Understanding the full lifecycle of packaging materials, from production to disposal, is essential in making informed decisions that align with sustainability goals. Switching to glass might make sense in terms of long-term recyclability, but increased weight will increase the carbon cost of transport, and some supermarkets will not accept glass bottles any more.
Embrace innovation and change
As packaging sustainability regulations become more stringent and consumers demand more sustainable products, manufacturers need to change packaging materials and processes.
This transition is no easy feat. But by embracing innovation, optimizing processes, and getting ahead of regulatory changes, manufacturers can make significant strides in their sustainability and productivity efforts.
Show notes
Check out the links below for more content around sustainable packaging for manufacturers:
- For a comprehensive view of global regulatory changes, McKinsey's "Sustainability in Packaging: Global Regulatory Development Across 30 Countries" is a valuable resource.
- Raymundo’s is a producer of ready-to-eat products in the US. Find out how they improved their efficiency with Factbird in this case study: How Raymundos boosted their efficiency with real-time production data.
- Try Factbird's production monitoring and OEE solutions for yourself with no obligations: Get a free 30-day trial of Factbird.
- You can learn more about the sustainable pallet company I briefly mentioned during the podcast here: Pallet Earth.
Remember to subscribe to Manufacturing Matters to get notified when the next episode is available on Spotify, Apple Podcasts, YouTube, Amazon Music, or your favourite podcast directories.