Unleashing the power of production data in manufacturing
Manufacturing Matters Ep. 10
Salman Rehan, Senior Enterprise Account Manager, Factbird
Release Date: July 8, 2024
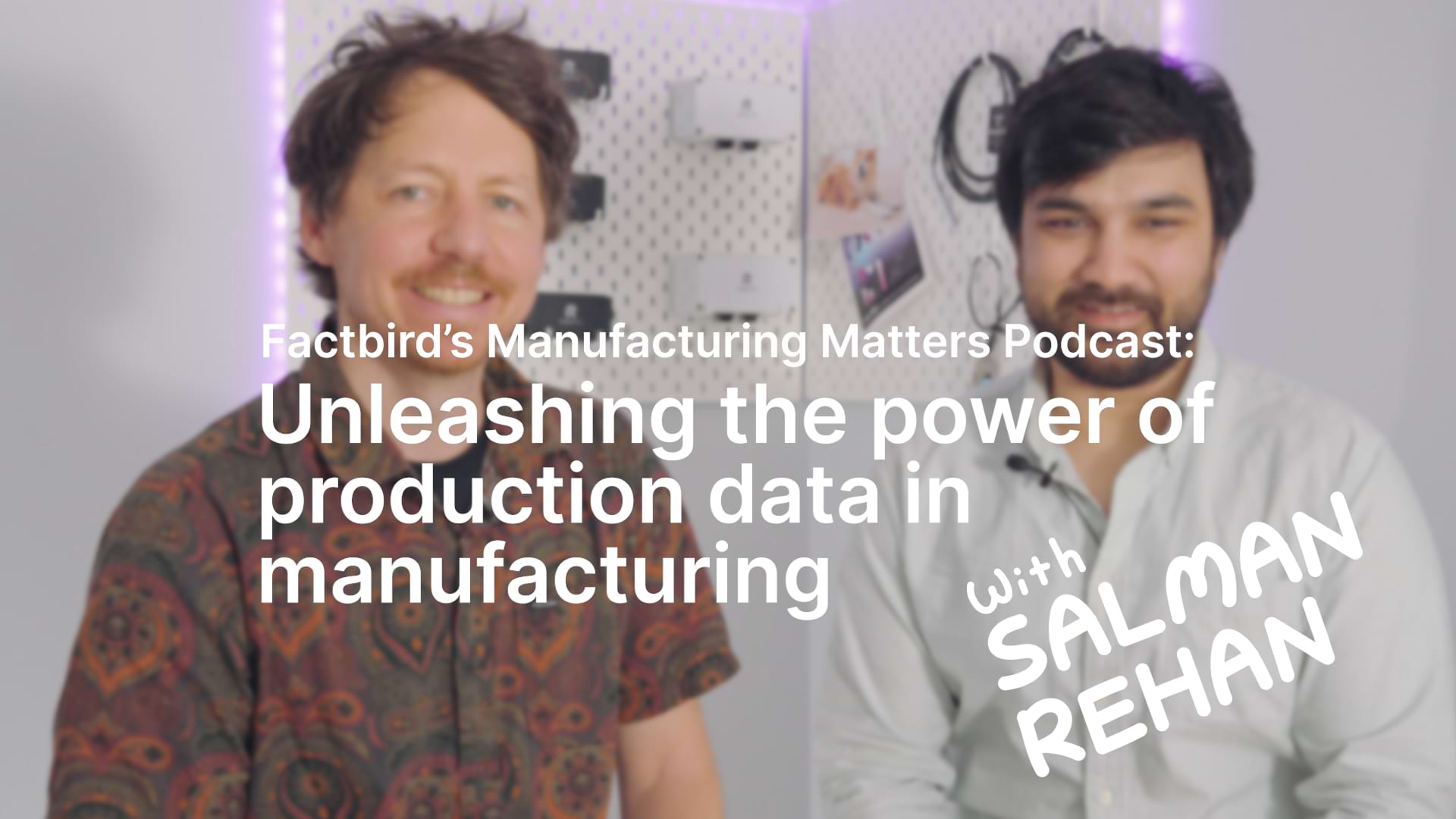
- Production data tracks machine performance, throughput, downtime, and quality.
- It offers manufacturers transparency and helps manage costs effectively.
- The shift from intuition to data-driven decisions is vital for success.
- Modern machines and plug-and-play solutions simplify data collection.
- Production data collection and digitalization helps bridge the skills gap in manufacturing.
With supply chain disruptions, cost management pressures, and the need to remain competitive, understanding what happens on the factory floor through production data has never been more important.
In Episode 10 of the Manufacturing Matters podcast, I had the pleasure of speaking with Salman, an industry veteran in the US and Factbird colleague. Salman shares invaluable insights on the evolution of production data tracking and analysis, its current significance, and the exciting future possibilities it holds.
Are you curious about how to harness the full potential of production data in your manufacturing processes? Read on for an in-depth exploration of production data and how it can help you improve your operations.
What is production data?
Production data encompasses the capture of information related to the manufacturing process, including machine performance, throughput, downtime, and quality metrics.
“Production data is basically the digitalization of your production.”
– Salman Rehan, Senior Enterprise Account Manager at Factbird
This data provides a comprehensive digital view of what is happening on the factory floor, enabling manufacturers to undertake deep analysis of performance and make more informed decisions.
As Salman puts it, "Production data is basically the digitalization of your production. It is real-time tracking of the performance of your machines. Compiling different types of data off of your machines."
It is one part of Industry 4.0, digitalization, digital transformation, and all of those buzzwords, but, in short, it’s about using data to make your manufacturing facility more efficient. Salman expands on the concept by explaining, “It comes in the operations space; so how can we make our operations more efficient and how can we do more with what we currently have?”
Why is production data important?
Salman emphasizes the critical role of production data in today's manufacturing landscape. Here are a few reasons why production data is indispensable:
- Transparency: Production data offers a clear picture of what is happening on the factory floor shift to shift, day to day, batch to batch, and so on, helping manufacturers identify inefficiencies and areas for improvement.
- Cost management: By understanding production data, companies can manage costs more effectively, saving money and reducing waste.
- Agility: Production data helps manufacturers navigate, for example, supply chain disruptions, raw material shortages, and customers’ wanting specific deals by providing real-time insights and enabling quick responses.
- Performance improvement: With data-driven decisions, you can set new production records through smart optimization of your lines and continuous improvement programmes.
- Staying competitive: The number one benefit of using production data is to stay competitive in a globally tough environment.
According to Salman, “To stay competitive, you need to pick up money off the floor, and production data is a big part of that. Collecting that data, analyzing it, and making data driven decisions.”
The evolution of production data usage
According to Salman, there have been big shifts in the mentality and requirements in the manufacturing space for Industry 4.0 digital solutions in recent years.
These shifts have come in areas such as real-time OEE and performance analytics, connected workers, quality management, predictive maintenance, and much more.
Salman notes significant changes in how production data is utilized over the past few years:
- Human intuition to data-driven decisions: While Gemba walks and intuition have traditionally guided decisions, there's a clear shift towards data-driven decision-making.
- Advanced machinery: Modern machines now come equipped with advanced data collection capabilities, making it easier to gather and analyze production data.
- Plug-and-play Solutions: Simple, scalable solutions like sensors and gateways allow manufacturers to start small and expand their data collection efforts quickly.
Practical steps for capturing production data
Here are some best practices for capturing production data:
1. Invest in advanced machinery: Modern machines are designed with built-in data collection capabilities, providing a solid foundation for production data tracking. The downside of this is, of course, the expense and lost production as you upgrade existing lines.
2. Utilize seamless solutions: Start with low-hanging fruits by adding sensors to lines or tapping into existing PLC signals with IIoT devices like the Factbird® DUO. This allows immediate data collection and analysis without interruption to production or large capital expenses.
3. Integrate with MES systems: While MES systems provide valuable insights, consider integrating them with manufacturing intelligence systems to get a more comprehensive understanding of your data.
4. Start slow, scale fast: Begin with small, manageable projects to demonstrate the value of production data, then rapidly scale your efforts as you see success. Factbird will always recommend focusing on the main bottleneck first, getting up and running quickly to provide maximum speed to value, before taking the learnings gained and scaling up production monitoring.
If you would like a more thorough guide, I'd recommend checking out this related article: Manufacturing Data Collection: How to Get Started in 5 Easy Steps.
Strong growth and a large skills gap
A big driver of this rapid shift to digitalization in manufacturing is strong growth coming out of the pandemic coupled with the brain drain.
Manufacturing has bounced back strongly from the turbulence of the pandemic, but many skilled workers are reaching retirement, and attracting new ones to fill the skill gap is proving tricky.
Emphasizing this need, a recent Deloitte analysis of manufacturing in the US predicts that between 2024 and 2033, “1.9 million jobs could remain unfilled if manufacturers are not able to address the skills and applicant gaps.”
According to Salman, “Digitalization is very important; we want to keep that knowledge in. So if there’s someone who has been at a company for 30, 40 years, when they exit the organization, there is a huge knowledge gap.”
"65% of respondents in the National Association of Manufacturers’ 2024 Q1 outlook pointed to attracting and retaining talent as their primary business challenge."
- US Manufacturing Could Need as Many as 3.8 Million New Employees by 2033, Deloitte and The Manufacturing Institute
Investments in capturing production data helps improve efficiency, train employees in best practice, and engage teams, and could be a pivotal part of future success in manufacturing.
Examples of success with capturing data
Salman explains that when starting discussions with a new site, his typical process is “I’ll ask the question, if you could have a million more units by the end of next week, what would that do for you guys?“
The answer is usually that that would be Christmas come early. We would hit our production quota much earlier, we’d get bonuses, shift leaders will be happy, operators, high fives everywhere.”
This demonstrates how marketing and sales aren’t typically the problem these days with manufacturing. Hitting quota and getting the most out of production lines is where the gains can be made.
A good example is Raymundos, which makes ready-to-eat authentic desserts in the US. Their products are popular, and everyone wants them. So they came to Factbird and said “we can’t keep up with demand, so what can we do about this?”
Prior to Factbird, they relied a lot on manual production monitoring. Writing stuff down on paper and after the fact, logging of downtime reasons and even losing data because of unreliable manual processes.
After installing Factbird, they had real-time data and are now immediately alerted to problems on the shop floor. They also have data-driven planning, helping them make better business cases for investment or pinpointing the biggest problems and appropriately applying resources to their resolution.
Now they are breaking production records by improving their use of existing equipment.
You can read the full case study here for more in-depth information on how they improved: How Raymundos boosted their efficiency with real-time production data.
Future trends in production data
Before you go, here are some thoughts on the future of production data:
- Increased automation: Expect a rise in automated data collection and analysis, reducing the need for manual intervention and helping operators focus on their core tasks.
- Enhanced analytics: More advanced analytics and machine learning (aka AI) will play a bigger role in interpreting production data, providing deeper insights and predictive capabilities.
- Real-time monitoring: Real-time monitoring and analysis will become standard, with more manufacturers being able to respond instantly to any issues or changes in the production process.
Data is gold
Production data is transforming the manufacturing industry, offering needed insights and opportunities for optimization. In this episode, Salman does a great job highlighting the importance of embracing data-driven decision-making and leveraging advanced technologies to stay competitive in today's dynamic market.
For more insights and practical tips on production data and other manufacturing topics, stay tuned to Manufacturing Matters. If you have any questions or topics you’d like us to cover, feel free to reach out.
Remember to subscribe to Manufacturing Matters to get notified when the next episode is available on Spotify, Apple Podcasts, YouTube, Amazon Music, and other popular podcast directories.