Der ultimative Leitfaden zur Produktionsüberwachung durch Software
Software zur Produktionsüberwachung hilft es Herstellern, mehr zu produzieren und Kosten zu senken. Erfahren Sie in diesem umfassenden Leitfaden, wie.
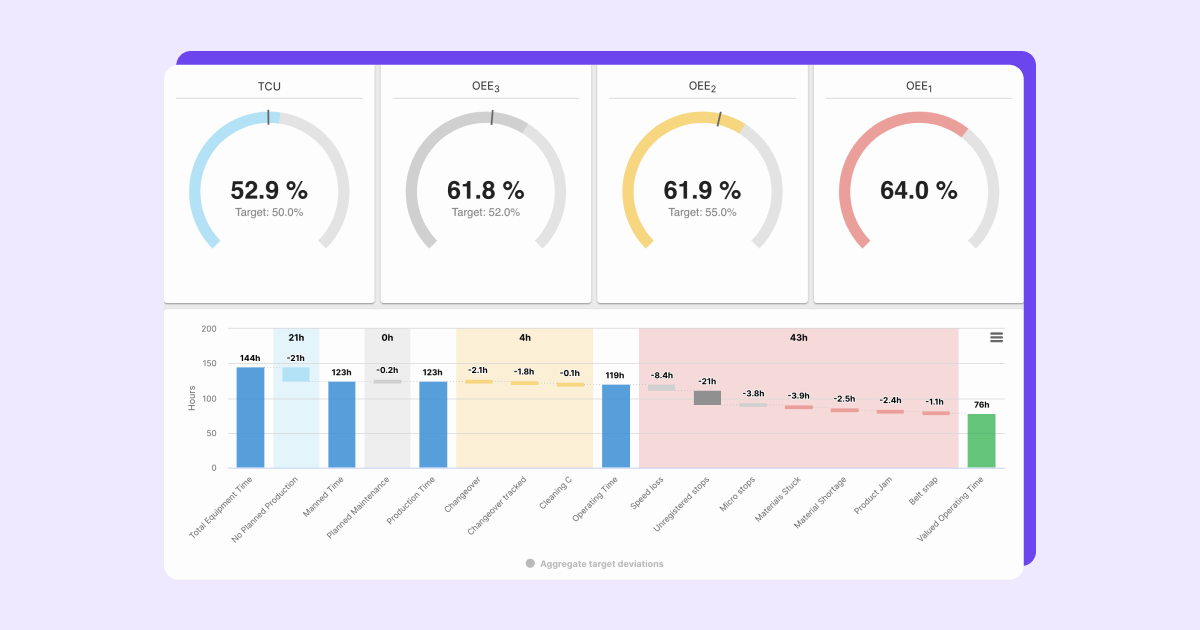
Hersteller haben oft Schwierigkeiten, ihre Produktionsziele zu erreichen, und geben alten Maschinen schnell die Schuld dafür. Tatsächlich können Maschinen, sofern wir nicht von abgenutzten Geräten sprechen, an neuere, intelligentere Arbeitsabläufe angepasst werden, die den Durchsatz erhöhen, Ausschuss reduzieren und energieeffizient werden können.
Wie können solche Ziele mit einem budgetorientierten Ansatz erreicht werden? Eine Software zur Produktionsverfolgung (manchmal auch Produktionsüberwachungssoftware genannt) ist eine wichtige Antwort auf Industrie 4.0.
In diesem Leitfaden erörtern wir den Wert der Implementierung von Software zur Produktionsverfolgung, die mit ihrer Anwendung verbundenen Kostensenkungen sowie die Art und Weise, wie Factbird in dieses Ökosystem passt.
Was ist eine Software zur Produktionsverfolgung?
Wir können Produktionsüberwachungssoftware als ein System definieren, das es Managern und Anlagenbedienern ermöglicht, die Produktion in der Werkshalle in Echtzeit zu analysieren. Die Produktionsdaten sind jederzeit abrufbar und zeigen wertvolle Daten wie produzierte Einheiten, Zykluszeit, Ausfallzeiten, Ausschuss, Energieverbrauch, Durchsatzvolumen usw.

Leistungsberichte, die auf der Produktionsüberwachung basieren, helfen Teams auf unterschiedliche Weise:
Wartung: Historische Daten sind eine überprüfbare Ressource, um die Ursachen für Maschinenstörungen zu lokalisieren.
Anlagenbediener: Der Fehlermeldeprozess wird automatisiert, wodurch das Risiko verringert wird, dass menschliche Fehler die Entscheidungsfindung beeinflussen. Stoppcodes können nachverfolgt und untersucht werden, um bessere Workflow-Lösungen zu finden.
Finanzen: Dank genauer Daten kann die Finanzabteilung jedes produzierenden Unternehmens effektive Strategien zur Senkung der Produktionskosten ausarbeiten.
Logistik: Die Datenerhebung wird in Echtzeit abgewickelt und ist für alle Teams zugänglich. Die Logistik kann ihren Arbeitsablauf verbessern und die Ressourcen gegebenenfalls an die Saisonalität anpassen. Unternehmen können ihre Logistikeinrichtungen verkleinern, indem sie nur die benötigten Rohstoffe und Fertigerzeugnisse lagern, die pro Monat berechnet werden.
Software zur Produktionsverfolgung dient nicht nur der Erfassung und Analyse von Daten, sondern kann auch dazu beitragen, alte Maschinen ohne hohe Investitionen in automatisierte Systeme umzuwandeln. Dies ist ein Punkt, auf den wir später noch eingehen werden.
Erfahren Sie mehr über die erstklassige Software zur Nachverfolgung der Fertigungsproduktion von Factbird >
Warum ist die Produktionsverfolgung wichtig?
Unternehmen mit einem Produktionsvolumen von über Tausenden von Einheiten pro Monat benötigen komplexe Prozesse zur Überwachung der Produktion, des Ressourcenverbrauchs, des Maschinenstatus, der Personalkosten usw. Wir können einige der Daten, die zur Analyse des Produktionspotenzials einer Fabrik erforderlich sind, wie folgt kategorisieren:
- Ziel der monatlichen Produktion
- Aktuelle monatliche Produktion
- Monatlicher Energieverbrauch
- Rohstoffverbrauch
- Verfügbarkeit/Schichten
- Ausfallzeiten (einzeln und akkumuliert) und ihre Ursachen
- Anzahl an Ausschuss und Nacharbeit pro Schicht oder Linie
Fertigungsteams profitieren in hohem Maße davon, dass sie diese Produktions-KPIs bei täglichen oder wöchentlichen Stand-Ups schnell überprüfen können. Sie profitieren vom Vergleich von Tagen und Wochen in regelmäßigen Besprechungen und Monaten und Jahren in Vorstandssitzungen.
Durch das Sammeln der erforderlichen Daten können Manager abschätzen, wie weit sie von ihren potenziell besten Produktionszahlen entfernt sind, welche Bereiche verbessert werden müssen und insbesondere, welche Bereiche sie kurzfristig mit minimalen Anpassungen beeinflussen können.
Die Auswirkungen der Produktionsverfolgung auf den Energieverbrauch
Die Reduzierung des CO2-Fußabdrucks ist eines der Hauptziele der Agenda 2030 im Hinblick auf den Umweltschutz. Die industrielle Fertigung wird als Hauptursache für Kohlendioxidemissionen bezeichnet, aber andere relevante Elemente, die Unternehmen berücksichtigen, sind:
- Energiepreise und die Auswirkungen auf den Produktpreis
- Umstellung auf nachhaltige Energiequellen
- Optimierung des Energieverbrauchs pro produziertem Stück
Ein Beispiel für diesen Trend sind Maschinenstillstände. Einige Hersteller entscheiden sich dafür, die Anlagen am Wochenende im Standby-Modus zu lassen, was im Vergleich zur Betriebszeit einen geringeren Energieverbrauch bedeutet. Diese Praxis minimiert die Ladezeiten der Maschinen während der Schichten, aber die im Leerlaufmodus angesammelte Energie sollte nicht übersehen werden.
Durch die Einführung eines Systems zur Überwachung der Produktion in der Fertigung können Manager den Gesamtenergieverbrauch pro Zeitraum ablesen und die Werte zwischen Betriebszeit und Bereitschaftszeit vergleichen. In unserem Case Study über Danfoss DK, die vom Factbird Performance Dashboard bereitgestellten Informationen ergaben, dass es kostengünstiger war, die Maschine während der Stillstandszeit vollständig abzuschalten. Danfoss DK konnte dank dieser Einsichten den Energieverbrauch senken und anderer energiebezogener Anpassungen vornehmen, die die Energiekosten um fast 77% reduzierten.
Das vollständige Interview mit Martin Ole Madsen, Manager — Operations Excellence SVS EUR bei Danfoss, können Sie sich hier ansehen.
Die Reduzierung des Energieverbrauchs führt sofort zu einem niedrigeren Endproduktpreis. Das Sammeln und Analysieren von Daten ist der erste Schritt zum Energiemanagement. Unternehmen können sich dann für ihre maßgeschneiderten Strategien entscheiden, um den Energiebedarf in der Produktion zu senken, oder sich für ISO 50001-2011 Richtlinien zur Energieeinsparung entscheiden.
Der Einfluss der Produktionsverfolgung auf den Durchsatz
Eine genaue Datenerfassung ist der erste Schritt zur Erhöhung des Durchsatzes. Manager unterschätzen oft die tatsächliche Produktionskapazität, obwohl kostengünstige Verbesserungen den Durchsatz erheblich erhöhen können.
Nachdem nun zuverlässige Datenquellen und den Workflow für jede Produktionslinie etabliert wurden, ist es an der Zeit, Engpässe zu identifizieren. Einige Gegenmaßnahmen zur Vermeidung von Produktionsverzögerungen hängen mit ungenauen Geschwindigkeits- oder Zufuhrraten für Rohmaterial zusammen; oft sind die Ursachen auf Missverständnisse der Anlagenbediener bezüglich der Maschinen zurückzuführen.
Die Anwendung der intelligenten Fertigungsmodelle des IoT hilft uns, Fehler zu beheben, Ausfallzeiten von Anlagen zu reduzieren, unnötigen Maschinenverschleiß zu verhindern und den idealen Zykluszeiten näher zu kommen. Infolgedessen können wir innerhalb weniger Wochen einen erheblichen Anstieg der Durchsatzzahlen verzeichnen, ohne auf umfangreiche Maschinenmodernisierungen zurückgreifen zu müssen.
Die Auswirkungen der Produktionsüberwachung auf Verschwendungen
Bei der Umsetzung eines Lean-Thinking-Ansatzes in der industriellen Fertigung geht es nicht nur darum, Produktionsverluste zu identifizieren. Berücksichtigen Sie sowohl Zeit als auch Verschwendungen als Elemente, die Sie so gering wie möglich halten sollten.
Ein Anlagenbediener, der aufgrund eines Produktionsstillstands untätig ist, stellt verlorenes Potenzial dar. Dies kann leicht behoben werden, indem die Ursachen für wiederkehrende Stopps angegangen und intelligentere Prozesse zur Überwachung und Beseitigung der Stopps eingerichtet werden. Genaue Daten lassen weniger Raum für Vermutungen, da Entscheidungen auf Fakten basieren. Dies führt dazu, dass Hersteller eine Steigerung der Produktion und eine höhere Motivation ihrer Belegschaft feststellen.
Der andere zu berücksichtigende Punkt ist Ausschuss. Aus dem OEE-Standard für Qualität, „Right First Time“, gibt uns die Fertigungsprozessanalytik Einblicke in die Menge des pro Schicht produzierten Ausschusses. Diese Aufgabe wurde früher von den Anlagenbedienern manuell erledigt (mit dem immensen Zeitaufwand, der damit verbunden war). So konnten Manager dann die Daten abgleichen, um die Ursachen von Unterbrechungen mit der Anzahl der Ausschüsse zu verknüpfen, oder ihre Chargenproduktion so anpassen, dass Aufwärmzyklen der Maschinen vermieden werden. In diesem Punkt besteht der Vorteil der Produktionsverfolgung darin, den Rohstoffverbrauch und das Ausschussvolumen in der Fertigung zu reduzieren.
Vorteile von Produktionsüberwachungssoftware
Vorteil #1 — Effektivere Anlagen
Es ist richtig anzunehmen, dass ältere Maschinen in anderen Zyklen arbeiten als die, die moderne Maschinen in die Werkstatt bringen; das macht sie jedoch nicht nutzlos. Alte Maschinen bergen ein verborgenes Potenzial, die heutigen Produktionsstandards zu erfüllen, und dank einer Überwachungssoftware können die erforderlichen Parameter eingestellt werden.
Stellen Sie sich vor, Ihr Unternehmen erwägt ein kostspieliges Upgrade für Ihre beiden Hauptproduktionslinien. Was ist, wenn Sie weniger als ein Drittel des benötigten Geldes in die Optimierung Ihrer aktuellen Produktionslinien investieren, anstatt sich neue Geräte anzuschaffen? In der Tat werden Sie überrascht sein, welche neuen Produktionskennzahlen aus zuverlässigen Datenquellen gewonnen werden können.
Vorteil #2 — Automatisierte Ausschusszählung
Dies wird traditionell von den Anlagenbedienern manuell durchgeführt, was bedeutet, dass eine Gruppe von Anlagenbedienern die alleinige Aufgabe hat, den von Maschinen erzeugten Ausschuss zu zählen, anstatt diese an anderer Stelle einzusetzen, wo ihre Fähigkeiten besser genutzt werden könnten. Softwarelösungen zur Produktionsüberwachung ermöglichen es uns, den Ausschuss automatisch zu zählen, was uns auch ein besseres Verständnis im Bezug auf OEE-Analysen gibt.
Wir können dann die Anzahl der Ausschüsse mit anderen Faktoren wie Ausfallursachen, Rohstoffchargen, Wartungsanforderungen usw. in Verbindung bringen.
Vorteil #3 — Prädiktive Wartung
Für Anlagenbediener und Wartungsteams ermöglicht die Produktionsüberwachungssoftware die Verfolgung und Analyse aller Ausfallursachen und Wartungsmaßnahmen. Anstatt immer wieder Brände zu löschen, können Wartungsteams Modelle für vorbeugende Wartung verwenden, um Ausfallzeiten langfristig zu reduzieren.
Was sollte eine gute Performance-Tracking-Software beinhalten?
Nachdem wir nun die Vorteile der Verwendung von Software zur Produktionsverfolgung/Überwachung aufgezeigt haben, fassen wir zusammen, was von einer Qualitätslösung erwartet wird:
- Datenzugriff rund um die Uhr: Denn je mehr Daten verfügbar sind, desto besser verstehen wir, was mit der Produktion passiert. Eine gute Lösung zur Leistungsüberwachung ermöglicht den Zugriff rund um die Uhr, unabhängig davon, welches Gerät zum Browsen der Daten verwendet wird.
- Übersichtliche Datenvisualisierung: Daten müssen von Anlagenbedienern und Managern gesammelt und interpretiert werden. Ein übersichtlicher Zugriff auf die Informationen hilft, Probleme in kürzerer Zeit zu lösen und für Mitarbeiter besser zu verstehen.
- Datenschutz: Da wir über sensible Daten sprechen, ist es am besten, den endgültigen Speicherort der gesammelten Informationen sicherzustellen. Erkundigen Sie sich nach der Methode des Softwareanbieters zur Verarbeitung Ihrer Daten, wo diese gespeichert werden und wer Zugriff darauf hat.
- Zugriff auf mehrere Plattformen: Rendern Sie die Software zur Leistungsüberwachung nicht nur für Monitore und Computer in der Werkshalle. Die Informationen sollten von Tablets, Mobilgeräten und Computern aus abgerufen werden können, ohne dass spezielle Hardwarelösungen erforderlich sind.
Arten von Dashboards zur Produktionsüberwachung
Es gibt verschiedene Modelle von Dashboards zur Produktionsüberwachung, die Anlagenbediener und Manager je nach den Erfordernissen ihrer Arbeit verwenden können.
OEE-Dashboards
OEE-Berechnungen müssen nicht mehr manuell erfolgen oder Softwarelösungen von Drittanbietern verwendet werden. Die meisten Softwarelösungen zur Produktionsüberwachung führen die OEE-Berechnung automatisch in Echtzeit durch, wobei Grafiken die OEE-Werte und jede einzelne Metrik segmentweise aufschlüsseln.
Aus diesen Dashboards können wir Informationen über die Qualität unserer Produkte auf der Grundlage des Prinzips “Right First Time”, über die gesamte Betriebszeit und die gesamte verfügbare Zeit für die Fertigung sowie über die Ausfallursachen oder geplanten Stopps abfragen.
Dashboards in der Werkshalle
Diese Leistungs-Dashboards zeigen einen vereinfachten Entwurf Ihrer Fertigungsstruktur und geben den Standort jeder relevanten Maschine im Produktionsprozess an. Dies wird zu einem wertvollen Vorteil, da Sie den genauen Standort der Rohstoffe und produzierten Teile verfolgen und die Logistikkapazität abschätzen können. Außerdem werden Informationen zur Gesamtanlageneffektivität (OEE) und zum Status der Maschinen angezeigt (auf welchen Maschinen gerade produziert wird und welche stillstehen).
Dashboards für die tägliche Produktion
Es wird wichtig, die Leistung von Produktionsressourcen zu verfolgen. Die Dashboards für die tägliche Produktion geben den Durchsatz pro Tag in Balkendiagrammen wieder. Manchmal ermöglichen sie kleinere Zeitintervalle. Die angestrebten Produktionsziele werden angezeigt, sodass Sie beurteilen können, wo Ihre Produktionsleistung steht.
Interaktive Stoppregistrierungsbildschirme
Schließlich hilft uns die Verwendung dieser Art von Dashboard dabei, die Ursachen für Stopps und hauptsächlich die kumulierten Auswirkungen wiederholter Stoppursachen zu analysieren. Anlgenbetreiber neigen dazu, kurze Stopps auf ein Minimum zu reduzieren. Dennoch zeigt uns die Erfahrung, dass Mikroausfälle oft zu einem hohen Maß an akkumulierter Ineffizienz führen. Daher enthalten diese Dashboards detaillierte Elemente, die Manager untersuchen sollten, um die Produktionsleistung zu verbessern.
Probleme, die durch Produktionsverfolgungssoftware gelöst wurden
Fehlender Überblick über die Produktionsleistung
Wie bereits erwähnt, unterschätzen Manager oft das tatsächliche Potenzial ihrer Maschinen für die Produktion. In Anbetracht der Methoden, mit denen die Produktion vor Industrie-4.0-Modellen verfolgt wurde, beginnen wir damit, Daten von den Sensoren an die SPS zu übertragen. Diese Daten werden in eine Excel-Tabelle verteilt, in der die Informationen nachverfolgt werden. Dieser alte Prozess beinhaltet eine ganze Reihe von Schritten, die menschlichen Fehlern zum Opfer fallen können, wie zum Beispiel:
- Falsche Datenzählung, insbesondere für Ausschuss und Teile, die überarbeitet werden müssen.
- Verzögerung bei der Dateneingabe, was die Fähigkeit beeinträchtigt, schnelle Maßnahmen zu ergreifen.
- Ungenaue Dateneingabe in Tabellenkalkulationen.
- Missverständnis der Daten.
- Vertriebsprobleme.
Die Verwendung von Excel-Tabellen beinhaltet auch komplexe Vorlagendesigns, um die Informationen zu verfolgen. Tools wie RSLinx sind erforderlich, um die Daten von PLC in das Excel-Dokument zu exportieren. Nur ein paar falsch platzierte Klicks und alle Datenberichte könnten durcheinander gebracht werden. Stattdessen vereinfacht eine Software zur Überwachung des Fertigungsprozesses den Prozess, synchronisiert ihn für einen einfachen Zugriff und schätzt das tatsächliche Produktionspotenzial auf der Grundlage der idealen Zyklusinformationen ab.
OEE-Analyse
Wenn die OEE-Berechnung manuell durchgeführt wird, kann sie zu einer Vielzahl von Fehlern führen. Von der Unterschätzung der Produktionskapazität (was bei optimierter Produktion zu OEE-Werten von über 100% führt) bis hin zur falschen Ausschusszählung kann der Prozess mühsam wirken, wenn er automatisiert werden kann. OEE-Softwarelösungen, die oftmals in Fertigungsüberwachungssoftware enthalten sind führt diese Berechnung in Echtzeit durch und gibt Aufschluss darüber, welche Stoppursachen die OEE-Werte senken.
Priorisierung
Dieser Punkt steht im Zusammenhang mit der OEE-Analyse, da die von der Softwarelösung zur Fertigungsüberwachung abgerufenen Informationen Hinweise darauf geben, welche Bereiche optimiert werden müssen. Anhand der abgerufenen Informationen sowohl zu den Stoppursachen als auch zur aktuellen Produktionsleistung kann das Management über folgende Punkte entscheiden:
- Agenda für die Wartung
- Aufrüstung der Werkshalle
- Workflow-Revisionen
- Qualität der Rohstoffe
- Taktiken zur Vermeidung von Verschwendung (Energie, Nacharbeit und Ausschuss).
Stoppursachen
Stoppursachen, insbesondere solche, die sich wiederholen, sind komplex, was die Lokalisierung ihres Ursprungs angeht. Stoppfehler, die zwischen 300 und 500 ms erkannt werden, scheinen nichts zu sein. Dennoch sind sie oftmals die Ursache für Verzögerungen bei der Produktlieferung.
Systeme zur Produktionsüberwachung geben präzise Rückmeldung darüber, welche und wann die Ursachen für den Stopp eingetreten sind. Die Anlagenbediener können dann mehrere von ihnen beeinflussen und das Problem an das Management weiterleiten, wenn die Lösung ihre Reichweite übersteigt. Darüber hinaus hilft das Zählen von Warnmeldungen bei Auslösen von Stopps dabei, die Lösung sofort zu beheben, anstatt das erst Problem zu erkennen, wenn sich die Produktion verzögert.
Entscheidungsfindung auf der Grundlage von Fakten
Wenn Informationen zugängloch werden, können die Fertigungsprozesse auf eine schlanke Fertigung umgestellt werden, bei der die Produktion optimiert und der Ausschuss minimiert wird. Manager können die aktuellen Produktionskennzahlen auf der Grundlage der von den Sensoren abgerufenen Daten bewerten und Strategien entwickeln, die ausschließlich auf Sachinformationen basieren. Bein einem eher eingeschränkten Budget wird dieser Punkt zu einem unschätzbaren Vorteil.
Wie kann Factbird Unternehmen dabei helfen, das Produktionsvolumen zu steigern?
Factbird ist eine umfassende Lösung für die Produktionsüberwachung, die über das OEE-Tracking hinausgeht. Sie erhalten eine genaue Ausfallzeitenanalyse zur Erhöhung der Verfügbarkeitsraten, Vorschläge zur vorausschauenden Wartung, die Überwachung der Chargenleistung und viele andere Tools, die Ihnen zur Verfügung stehen.
Benutzer können Live- und Langzeitdaten verfolgen und so viele verschiedene Stoppursachen wie erforderlich registrieren.
Factbird ist als Produktionsüberwachungslösung skalierbar. Das heißt, dass Unternehmen mit einem Pilotprojekt an einer begrenzten Anzahl von Maschinen/ Linien beginnen und dann neue Einheiten hinzufügen können, um letztendlich das benötigte Maschinenvolumen abzudecken.
Kompatibilität von Factbird (ERP/SAP-Integration und PowerBI)
Sie müssen nicht auf zuvor erworbene Tools verzichten, um Factbird verwenden zu können. Unsere Softwarelösung ermöglicht es , Daten aus der Factbird-App einfach nach PowerBI, Tableau usw. zu exportieren. Auf diese Weise können Unternehmen ihre bestehenden Analyse-Workflows beibehalten und diese Tools durch genaue Datenwerte und leichter zugängliche Informationen in der Werkshalle ergänzen.
Factbird® VIEW
Stellen Sie sich vor, Sie erhalten in Echtzeit Videoaufnahmen von den Vorgängen in den Produktionslinien. Mithilfe von Factbird® VIEW können Sie die Notwendigkeit, Fehlerursachen zu interpretieren reduzieren, indem einfach per Video gesucht wird, was zum Stoppen einer Linie geführt hat.
Durch das Sammeln von Videobildern in Echtzeit und deren Synchronisation mit Produktionsdaten in der Factbird Cloud-Anwendung, können Benutzer jederzeit überprüfen, welche Situation eine Stoppursache ausgelöst hat. Die Videos werden Minute für Minute mit den Produktionsdaten synchronisiert, sodass die Suche nach den Ursachen für einen Stopp an der Linie erleichtert wird.
Diese Videoinformationen können geteilt werden, sodass Wartungsteams detaillierte Berichte darüber erhalten, an welchen Problemen sie arbeiten sollten. Das Videomaterial wird standardmäßig einen Monat lang auf dem Server gespeichert, Sie können jedoch während der Installationsphase benutzerdefinierte Einstellungen anfordern.
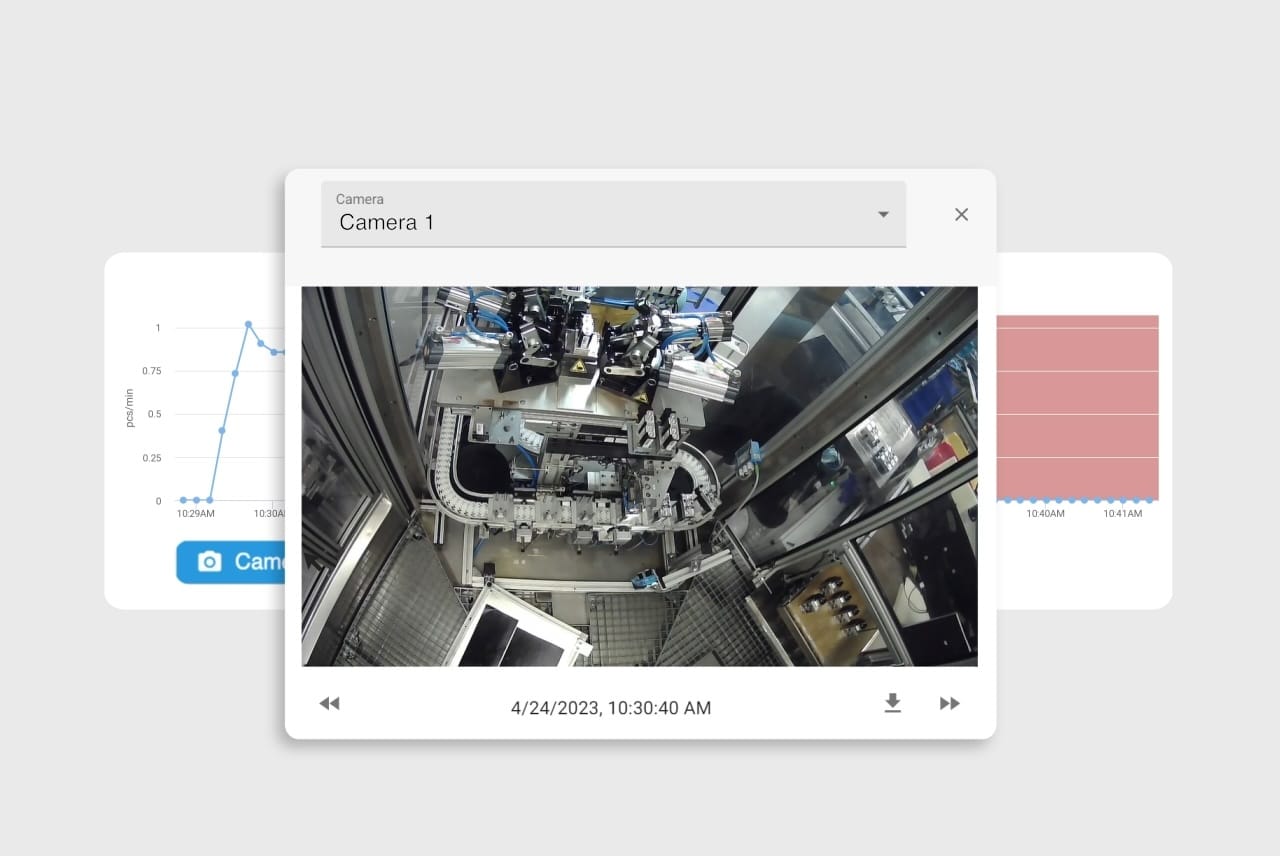
Datenschutz
Die Daten unserer Kunden werden bei uns mit höchster Sorgfalt behandelt. Die von den Factbird-Sensoren gesammelten Informationen werden in die Cloud hochgeladen, um über das Factbird-Dashboard abgerufen zu werden. Nur Benutzer mit Anmeldeinformationen können auf diese Informationen zugreifen. Wenn Ihr Passwort nicht funktioniert, können Sie unseren Kundensupport bitten, Ihnen bei der Wiederherstellung der Anmeldeinformationen zu helfen.
Datenausfälle können nicht mit mangelnder Konnektivität in Verbindung gebracht werden, da die Factbird-Lösung mit mobilen Daten, WLAN oder Ethernet funktioniert.
So installieren Sie die Factbird Software
Die Implementierung der Technologie von Factbird in Ihrer Werkshalle ist eine Aufgabe, für die nur ein paar Stunden Installation erforderlich sind. Für die Installation unserer Factbird-Lösungen sind keine zusätzlichen IT-Ressourcen erforderlich, und der Datenabruf erfolgt sofort. Dieser Abschnitt gibt Ihnen einen schnellen Überblick darüber, wie Sie das Factbird Manufacturing Metrics Dashboard installieren und verwenden, um Ihre Prozesse zu steuern.
Hier finden Sie hier einen Überblick darüber, wie die Manufacturing Intelligence-Lösungen von Factbird funktionieren.
Zugriff auf das Dashboard
Der erste Schritt besteht darin, Ihr Konto zu validieren. Sie erhalten von Factbird eine E-Mail mit einer temporären Anmeldeinformationen. Ändern Sie Ihr Passwort im Browser und Sie können sich in das Monitoring-Dashboard von Factbird einloggen.
In der Anfangsphase des Dashboards werden keine Daten abgerufen, da die Sensoren konfiguriert werden müssen. Suchen Sie nach der oberen linken Ecke des Factbird-Dashboards und rufen Sie das Sensormenü auf.
Einen Sensor konfigurieren
Um einen Sensor zu konfigurieren, sollten Sie zunächst seinen Typ angeben. Die Optionen lauten wie folgt:
Counter: Ein regulärer Zählsensor, der den Zählerstand seit der letzten Veröffentlichung überträgt.
Counter Speed: Ein Geschwindigkeitssensor, der in einen Zähler umgewandelt wurde.
Counter Accumulate: Ein akkumulativer Sensor, der in einen Zähler umgewandelt wurde.
Measurement: Ein Sensor, der den direkten Wert von Messungen wie Temperatur, Geschwindigkeit, Druck usw. verfolgt.
Event: Ein Ereignisensor, der bei einer Statusänderung ausgelöst wird.
Diskret: Ein Sensor, der einen von einer begrenzten Anzahl von Zuständen überträgt, in denen sich eine Linie befinden kann.
Als Nächstes müssen Sie die Werte für Validierte Geschwindigkeit und die Erwartete Geschwindigkeit einer Linie aktualisieren. Wechseln Sie zur Registerkarte Einheiten und wählen Sie zu Unit Data.
Definieren Sie Stopps, indem Sie das Minimale Stoppdauer (normalerweise Werte über 300 ms) und Schwellenwert für die Registrierung beenden. Es wird empfohlen, die Option „Stopps finden aktivieren“ einzuschalten, da dies die automatische Erkennung von Stoppursachen ermöglicht.
Die Stoppzuordnung funktioniert für Maschinen, die an PLC-Eingänge angeschlossen sind. Die Linienkonfiguration kann über dieses Sensor-Einstellungsmenü oder unabhängig davon vorgenommen werden.
Der letzte Schritt besteht darin, die Warnungen festzulegen und die Abonnenten zu verknüpfen. Die Teammitglieder werden benachrichtigt, sobald eine Stoppursache den minimalen Schwellenwert überschreitet. Wiederholen Sie alle diese Schritte nach Bedarf, um alle Sensoren zu konfigurieren.
Eine Linie erstellen
Wir starten den Linienerstellungsprozess, indem wir im Navigationsmenü auf Linien zugreifen. Sie müssen zuerst die Gruppe auswählen, in der sich der Sensor befindet. Sie können mit vordefinierten Gruppen arbeiten oder Ihre eigenen erstellen.
Der zweite Schritt besteht darin, den Engpass auszuwählen. Dies ist der primäre Sensor dieser Linie und sollte an kritischen Stellen der Produktionslinie platziert werden. Benennen Sie die Linie und weisen Sie die Verbindung zu (WLAN oder Ethernet, je nach Sensormodell). Wiederholen Sie diesen Vorgang, um so viele Linien wie nötig hinzuzufügen.
KPIs des Dashboards
Nachdem unser gesamtes Netzwerk von Sensoren und Linien erstellt wurde, verfolgt und analysiert das System von Facbird die Daten. Unser Dashboard enthält mehrere KPIs zur Überprüfung der Leistung der Geräte.
Die KPIs, die wir untersuchen können, sind:
- Anzahl der produzierten Produkte
- Längste Non-Stop
- Anzahl der Stopps
- Durchschnittliche Stopplänge
- Ausfallzeiten
- Zeit der Wertschöpfung (%)
- Zeit zur Wertschöpfung während der Besatzung (%)
- Durchschnittliche Zeit zwischen Ausfällen
- Durchschnittlich produziert
- Zykluszeit
- Produzierte Einheiten pro Stopp
- Geschwindigkeit bei bemannter Besatzung (Stk/min)
- Geschwindigkeit während Produktion (Stück/min)
- Hergestellt in der aktuellen Charge
- Voraussichtlicher Zeitpunkt der Fertigstellung
Es ist möglich, Daten anhand vorab festgelegter Zeitbereiche anzuzeigen und zu analysieren oder sogar Zeiträume aus den Grafiken hervorzuheben, um die Daten detaillierter zu untersuchen. Die in den KPI-Abschnitten enthaltenen Informationen können zum besseren Verständnis in Form von Grafiken visualisiert werden. Die Abbruchursachen werden unter den Grafiken aufgeführt.
Diese Informationen können zur Datenanalyse mit Tools von Drittanbietern im Diagramm- oder KPI-Format exportiert werden.
Stoppregistrierung
Die Registerkarte Stopps registrieren ist eine effiziente Methode, um die Ursachen für die reduzierte verfügbare Zeit zu beheben. Wir können mit beliebig vielen Kategorien oder Stoppursachen arbeiten. Aus diesem Grund stellen wir Benutzern eine Vorlage zur Verfügung, mit der sie die häufigsten Kategorien und Stoppursachen zusammenstellen können. Importieren Sie die XLSX-Datei in das Menü „Stopps registrieren“, das Sie ändern können, um zusätzliche Elemente hinzuzufügen. Dieses Verfahren ist benutzerfreundlich und einfach zu verstehen. Durch den Export der XLSX-Datei aus einer Linie können wir Kategorien und Stoppcodes mit anderen Produktionslinien synchronisieren.
Als zusätzliche Sicherheitsmaßnahme können Sie die Funktion Initialen erforderlich aktivieren. Diese erfordert, dass Anlagenbediener ihre Initialen eingeben, wenn sie Stoppcodes melden, und hilft bei der Erstellung historischer Daten.
Eine weitere interessante Option besteht darin, die Ursachen für Stopps manuell aufzuteilen, zusätzliche Informationen hinzuzufügen oder die Stoppursachen/ Kategorien für längere Stopps zu ändern.
Analytik und OEE
Die Registerkarte „Analytik“ ist ein leistungsstarkes Tool für Anlagenbediener, Wartungspersonal und Manager, mit dem sie in Echtzeit visualisieren können, was mit den Anlagen und der Produktionsqualität passiert. Die Kennzahlen zur Produktivität in der Fertigung werden detailliert verfolgt, sodass wir Daten in verschiedenen Formaten visualisieren können, die unseren Präferenzen entsprechen. Diese Grafiken können in andere Softwarelösungen exportiert werden, um Berichte zu erstellen.
Unser OEE-Berechnungstool arbeitet in Echtzeit und misst TCU, OEE3, OEE2 und OEE1 in Balkendiagrammen und Wasserfallvisualisierungen. Die gesammelten Daten geben genaue Einblicke in alle drei Teile der OEE-Formel und bieten Zugriff auf Abhilfemaßnahmen, um Faktoren, die unsere OEE-Werte behindern, schnell rückgängig zu machen.
Andon Anrufe
Eine weitere Premium-Funktion, die wir in der Softwarelösung von Factbird auflisten, sind Andon Anrufe. Dieses Tool hilft den Anlagenbedienern, Hilfe bei Fehlerursachen zu erhalten und das Problem sogar an spezialisierte Teammitglieder weiterzuleiten.
Die Registerkarte „Mitarbeiter“ hilft uns, die Kontaktdaten der Teammitglieder zu speichern. Dies erfordert die Telefonnummer, E-Mail-Adresse, Schicht und Rang des Mitarbeiters. Schichten können so konfiguriert werden, dass beliebig viele Schichten zugewiesen werden. Arbeiter können ihre Plätze in temporären, halbtemporären oder unbefristeten Anstellungen besetzen.
Zugriff auf Kalender ermöglicht es uns, die Gesamtzahl der Mitarbeiter zu visualisieren, die während einer Schicht arbeiten.
Serienfertigung
Die Software von Factbird bietet die Möglichkeit, bestimmte Produkte vollständig automatisiert im Chargen-Modus zu analysieren. Dazu müssen Sie zunächst ein Produkt erstellen, alle seine Parameter angeben und speichern. Wenn Ihre Maschine eine Serienproduktion ermöglicht, wird ein Sensor platziert und die Registerkarte Charge wird auf dem Dashboard von Factbird angezeigt.
Erstellen Sie als Nächstes eine Charge. Wählen Sie das Produkt, das chargenweise hergestellt werden soll, die Anzahl der Einheiten und den Starttyp aus. Nach dem Start des Vorgangs erhalten Sie eine geschätzte Fertigstellungszeit, und Sie können den Prozess auf der Registerkarte „Analytik“ in Echtzeit analysieren. Dies ist eine sehr nützliche Lösung für Branchen wie die Pharmaindustrie.
Abschließende Gedanken
Mit Systemen zur Produktionsverfolgung profitieren Hersteller von Kosteneinsparungen, einer Senkung des Energieverbrauchs und einer erhöhten Produktionsleistung.
Anlagenbediener, Produktionsleiter und Führungskräfte erhalten in Echtzeit ein besseres Verständnis dafür, was in der Produktionslinie vor sich geht. So können sie die Teams auf kontinuierliche Verbesserungen ausrichten und mehr aus ihren bestehenden Produktionslinien herausholen.
Datengestützte Entscheidungen dank Produktionsverfolgung sind für Fertigungsteams eine Selbstverständlichkeit.